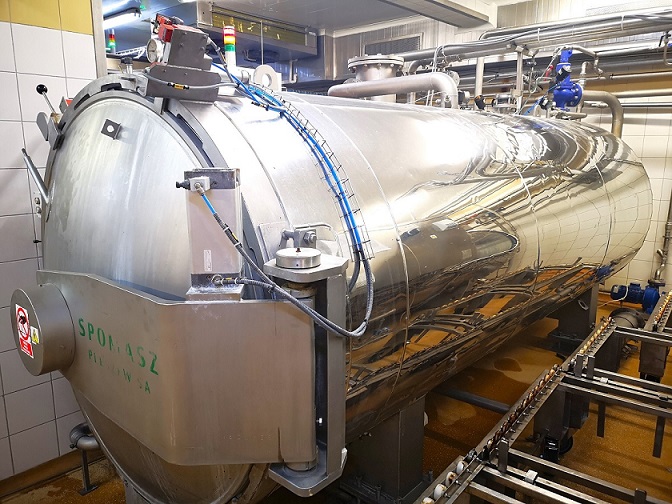
Qualifizierung von Autoklaven
Lebensmittelproduktion
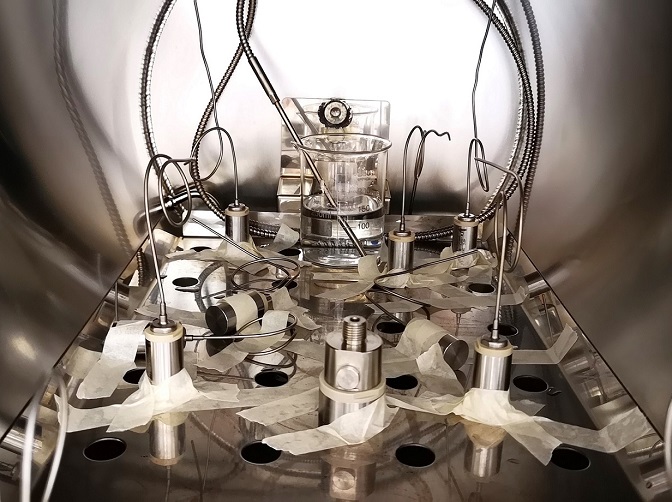
Qualifizierung von Autoklaven
LABORAUTOKLAVEN / Autoklaven der Klasse B
In der industriellen und medizinischen Welt ist die Qualifizierung von Autoklaven ein entscheidender Schritt, um sicherzustellen, dass Sterilisationsprozesse sowohl wirksam als auch reproduzierbar sind. Bevor ein Autoklav für solch kritische Aufgaben verwendet wird, muss er durch einen strukturierten Qualifizierungsprozess gehen. Dieser Prozess überprüft, ob die Maschine für die vorgesehene Aufgabe geeignet ist und einwandfrei arbeitet.
„Unterschiede und Zusammenhänge: Qualifizierung von Autoklaven vs. Prozessvalidierung“
In der pharmazeutischen und biotechnologischen Industrie spielen die Begriffe „Qualifizierung“ und „Validierung“ eine entscheidende Rolle. Beim Umgang mit solch kritischen Ausrüstungen wie Autoklaven sind diese Begriffe unerlässlich. Auch wenn sie oft gemeinsam oder sogar austauschbar verwendet werden, haben sie unterschiedliche Bedeutungen und Ansätze.
Qualifizierung von Autoklaven
Die Qualifizierung bezieht sich speziell auf den Nachweis, dass eine Anlage oder Ausrüstung – in diesem Fall der Autoklav – für ihre beabsichtigte Aufgabe geeignet ist. Es wird überprüft, ob der Autoklav mit der verwendeten Technologie korrekt funktioniert und ob er die erwarteten Ergebnisse gemäß den festgelegten Anforderungen liefert. In einfachen Worten konzentriert sich die Qualifizierung darauf zu bestätigen, dass der Autoklav tatsächlich das tut, was er soll und das auf konsistente und zuverlässige Weise. Das bedeutet, dass die Hauptaufmerksamkeit während der Qualifizierung dem Autoklav und seiner Funktionalität gilt.
Prozessvalidierung
Im Gegensatz dazu konzentriert sich die Prozessvalidierung auf den gesamten Prozess. Es geht darum, den Beweis zu erbringen, dass ein bestimmter Prozess – der möglicherweise unter Verwendung eines Autoklavs durchgeführt wird – effektiv und konsistent ein Produkt oder Ergebnis von vorgegebener Qualität produziert. Es wird also nicht nur die Ausrüstung betrachtet, sondern der gesamte Prozess und die Ergebnisse, die er liefert. Hier liegt der Fokus auf der Reproduzierbarkeit des Prozesses und der Sicherstellung, dass die festgelegten Qualitätsstandards eingehalten werden.
Da oft Prozesse in einer speziellen Ausrüstung wie einem Autoklav durchgeführt werden, erklärt dies die Verknüpfung und manchmal die Verwechslung der beiden Begriffe. Dennoch ist es wichtig, ihre Unterschiede zu erkennen und sicherzustellen, dass sowohl die „Qualifizierung von Autoklaven“ als auch die Prozessvalidierung korrekt durchgeführt werden, um optimale und sichere Ergebnisse zu gewährleisten.
Autoklaven-Qualifikationsstufen
Beim Prozess der „Qualifizierung von Autoklaven“ spielen verschiedene Qualifizierungsstufen eine zentrale Rolle. Jede dieser Stufen dient dazu, sicherzustellen, dass der Autoklav richtig designt, installiert, betrieben und letztlich performant arbeitet. Lassen Sie uns einen genaueren Blick auf diese entscheidenden Qualifizierungsstufen und ihre jeweiligen Anforderungen werfen:
DQ: Design-Qualifizierung – Die Basis der Qualifizierung von Autoklaven
Die Design-Qualifizierung, oft als DQ abgekürzt, ist der Startpunkt des Qualifizierungsprozesses. Sie beschäftigt sich mit den fundamentalen Merkmalen des Autoklavs. Ziel ist es sicherzustellen, dass sowohl die Konstruktion als auch die technischen Umsetzungen des Autoklavs den geforderten Parametern der Bestellung entsprechen. Dies ist von entscheidender Bedeutung, um sicherzustellen, dass Prozessgenauigkeit und -geschwindigkeit optimal erreicht werden.Die Design-Qualifizierung, kurz DQ, legt den Grundstein für die gesamte Qualifizierung von Autoklaven. Schon in dieser ersten Phase wird festgelegt, welche spezifischen Anforderungen an den Autoklav gestellt werden – dies wird als User Requirement Specification (URS) bezeichnet. Hierbei ist es wichtig zu betonen, dass Autoklaven von unterschiedlichen Herstellern individuell angepasst werden können, beispielsweise in Bezug auf Prozessgenauigkeit und Geschwindigkeit. Wenn während dieser Phase nicht alle erforderlichen Optionen berücksichtigt werden, kann dies den gesamten Qualifizierungs- und Validierungsprozess negativ beeinflussen. Es ist daher von größter Bedeutung, von Beginn an klar zu definieren, wofür der Autoklav genutzt werden soll und welche Richtlinien und Standards erfüllt werden müssen.
Nachdem die URS festgelegt wurde, erstellen die Anbieter von Autoklaven entsprechende Angebote, und es werden Lasten- und Pflichtenhefte zwischen Betreiber und Hersteller ausgearbeitet. Die Überprüfung dieser Dokumente auf Übereinstimmung bildet einen wesentlichen Bestandteil der Designqualifizierung. Nach Abschluss dieser Stufe wird der Autoklav gemäß den vereinbarten Spezifikationen produziert und parallel dazu beginnen die Vorbereitungen für die nachfolgenden Qualifizierungsstufen IQ, OQ und PQ.
IQ: Installationsqualifizierung – Der korrekte Aufbau des Autoklaven
Nachdem die Design-Qualifizierung abgeschlossen ist, folgt die Installationsqualifizierung, oder IQ. In dieser Phase der Qualifizierung von Autoklaven wird die gelieferte Maschine intensiv geprüft. Es wird sichergestellt, dass sie den technischen Spezifikationen des Herstellers entspricht und fachgerecht aufgebaut wurde. Auch die umfassende Dokumentation des Autoklavs wird in dieser Phase sorgfältig analysiert. Mit der Installationsqualifizierung (IQ) wird sichergestellt, dass der Autoklav richtig installiert wurde. Hierbei geht es um Aspekte wie den richtigen Aufstellort und die physischen Merkmale des Autoklavs, aber auch um die Vollständigkeit und Korrektheit der dazugehörigen Dokumentationen, einschließlich Betriebsanleitung, Wartungshinweise und Datenblätter.
OQ: Funktionsqualifizierung – Überprüfung der Betriebsfähigkeit des Autoklaven
Die Funktionsqualifizierung, bekannt als OQ (Operational Qualification), ist der nächste kritische Schritt. Hier wird die tatsächliche Funktion des Autoklavs gegenüber den Herstellerangaben geprüft. Dies stellt sicher, dass alle festgelegten Spezifikationen und Betriebsanforderungen erfüllt werden.In der Funktionsqualifizierung, oder OQ, steht der Betrieb des Autoklavs im Fokus. Hier wird überprüft, ob der Autoklav den im Rahmen der DQ festgelegten Anforderungen entspricht und korrekt funktioniert. Es werden diverse Tests durchgeführt, darunter auch Kalibrierungen und Simulationsversuche. Ebenso wird der Sterilisationsprozess ohne Produkt im Autoklav getestet.
PQ: Performance Qualifizierung – Realitätscheck für den Autoklaven
Der letzte und abschließende Schritt im Prozess der Qualifizierung von Autoklaven ist die Performance Qualifizierung, kurz PQ. Hier wird die tatsächliche Leistung des Autoklavs unter realen Bedingungen gegen die festgelegten Anforderungen überprüft. Für unterschiedliche Beladungskonfigurationen werden individuelle PQ-Tests durchgeführt. Die letzte Stufe, die Performance Qualifizierung (PQ), stellt sicher, dass der Autoklav unter realen Bedingungen optimal funktioniert. Hierbei wird der Sterilisationsprozess mit tatsächlichen Produkten getestet. Es ist essentiell, die Temperaturverteilung in verschiedenen Beladungskonfigurationen zu überprüfen, da diese von dem zu sterilisierenden Produkt abhängt. Ein zentraler Aspekt in der Qualifizierung von Autoklaven ist der sogenannte Sterility Assurance Level (SAL), der definiert, wann ein Produkt als steril betrachtet werden kann. Der SAL-Wert von 10^-6 stellt sicher, dass die Wahrscheinlichkeit eines nicht sterilisierten Produkts nach dem Sterilisationsprozess extrem gering ist.
Die Qualifizierung von Autoklaven ein rigoroser und mehrstufiger Prozess, der sicherstellt, dass die Autoklaven für ihre entscheidende Aufgabe in den Bereichen Industrie und Medizin optimal vorbereitet sind. Mit dem Abschluss dieses Prozesses und der Festlegung eines Re-Validierungsintervalls wird sichergestellt, dass der Autoklav auch in Zukunft effizient und sicher arbeitet.
Typischer Qualifikationsbereich für Dampfautoklaven
Installationsqualifizierung (IQ)
Identifizierung der Komponenten; Überprüfung der korrekten Installation
Die Prüfung zielt darauf ab, die Hauptkomponenten des Sterilisators korrekt zu identifizieren (u. a. Hersteller, Typ, Seriennummer) und zu überprüfen, ob der Geräteanschluss den vom Sterilisatorlieferanten und/oder -benutzer festgelegten Anforderungen entspricht.
Überprüfung des Kalibrierungszustands der Kontroll- und Messgeräte
Zweck der Überprüfung ist es, zu bestätigen, dass die Messgeräte, die zur Überwachung, Steuerung und Aufzeichnung kritischer Parameter des Sterilisationsprozesses (Temperatur, Druck) verwendet werden, kalibriert wurden und dass die Kalibrierungszertifikate den Sterilisatorunterlagen beigefügt wurden.
Vollständigkeit der mit dem Sterilisator gelieferten Dokumentation
Mit der Prüfung soll bestätigt werden, dass dem Sterilisator u. a. eine Betriebs- und Bedienungsanleitung sowie Vorschriften für den Betrieb und die Wartung des Sterilisators beigefügt wurden.
Vorgeschlagene/Beispieltests für die Anlagenqualifizierung:
– Überprüfung des FAT/SAT-Abschlusses
– Korrektheit, Vollständigkeit der Lieferung, Abwesenheit von Schäden
– Identifikation von Komponenten (Hersteller, Typ, Seriennummer, Material) und Software
– Abweichungen von der URS
– Überprüfung der Kennzeichnung der Hauptkomponenten des Autoklaven
– Vollständigkeit der technischen Dokumentation des Autoklaven (Beschreibungen, Anweisungen, Handbücher, Diagramme, Schaltpläne)
– Überprüfung der mechanischen Konstruktion des Autoklaven (Überprüfung der Bau- und Montagevorgänge)
– Überprüfung der elektrischen Auslegung des Autoklaven (Überprüfung der elektrischen Installationen)
– Korrektheit der Installation und des Anschlusses an die Versorgungseinrichtungen (Strom, Wasser usw.)
– Sicherheit der Ausrüstung
– Überprüfung der Arbeitsumgebung des Autoklaven
– Überprüfung der Ein- und Ausgänge des Autoklaven
– Liste der Messgeräte des Autoklaven (Kritikalitätsbewertung)
– Ersatzteilliste, Instandhaltung
– Einschalttest des Autoklaven
– Bericht über die Installation der Autoklaven-Software
– Kalibrierungszertifikate (und Übereinstimmung der Seriennummer der Elemente auf dem Zertifikat
und installiert)
– Angaben zu den Personen, die die Qualifizierung durchgeführt haben, und das Datum der IQ-Tests
Betriebliche Qualifizierung (OQ)
Temperaturverteilung in der Autoklaven-Kammer
Die Prüfung dient der Bestimmung der Temperaturverteilung in der Sterilisatorkammer, der Ermittlung des kältesten und des wärmsten Punktes in der Sterilisatorkammer.
Korrektheit der Sterilisationsprogramme
Diese Prüfung dient der Überprüfung der Korrektheit der Ausführung der einzelnen Schritte des Sterilisationszyklus durch den Sterilisator – Beurteilung des Verlaufs der Entlüftungsphase, Bestimmung der Äquilibrierungszeit, Bestätigung der Sterilisationszeit.
Test Bowie-Dick-Test
Dieser Test bestätigt die Wirksamkeit der Dampfdurchdringung und der Luftentfernung aus dem Inneren der porösen Chargen.
Leckage-Test
Mit diesem Test wird nachgewiesen, dass die Luftmenge, die während der Vakuumphasen in die Sterilisatorkammer eindringt, ein Niveau nicht überschreitet, das die Wirksamkeit der Dampfpenetration in die Ladung verringern und zu einer sekundären Kontamination der Ladung während der Trocknung beitragen könnte.
Geschwindigkeit der Druckänderung
Mit der Prüfung wird nachgewiesen, dass die Druckänderungsrate in der Sterilisatorkammer während des Betriebszyklus ein Niveau nicht überschreitet, das zu einer Beschädigung der Verpackung der sterilisierten Produkte führen kann.
Trockenheit der Charge
Diese Prüfung wird durchgeführt, um nachzuweisen, dass ein bestimmter Sterilisationszyklus nicht zu einem übermäßigen Anstieg des Feuchtigkeitsgehalts der sterilisierten Ladung führt.
Vorgeschlagener Umfang der OQ-Tests:
– Funktionstests (Erreichen und Stabilität von kritischen/extremen Systemparametern)
– Autoklaven-Alarme
– Sicherheitsverriegelungen, Funktion des Autoklaven-Sicherheitsschalters
– Prüfung bei Stromausfall
– Zugangskontrolle
– Berichtserstellung
– Grundsätze für Software-Updates, Datenarchivierung, Backup-Betrieb,
Datenwiederherstellung
– Identifizierung der bei der Qualifizierung verwendeten Materialien und Geräte (Gültigkeit der Zertifikate/Kalibrierungszertifikate)
Prozessqualifizierung (PQ)
Wärmeeindringung in die eigentliche Charge (Temperaturmessungen innerhalb der Charge)
Die Prüfung bestätigt, dass die Ladung die Sterilisationstemperatur erreicht und für die erforderliche Zeit aufrechterhält, dass die Ladung den erforderlichen Sterilisationswert (F0) erreicht und schließlich, dass der Gerätezyklus für die Sterilisation des gegebenen Ladungstyps geeignet ist.
Bewertung der Korrektheit des Sterilisationsprozesses mit Hilfe von chemischen Indikatoren des Typs 5 oder 6
Der Test bestätigt, dass die Beladung alle kritischen Sterilisationsparameter erreicht hat, die den korrekten Ablauf des Sterilisationsprozesses gewährleisten (Vorhandensein von Dampf, Temperatur und Dauer des Sterilisationsprozesses).
Bestätigung der Effizienz des Sterilisationsprozesses mit Hilfe von biologischen Indikatoren
Ein Test bestätigt direkt, dass ein biologischer Indikator, der in der sterilisierten Ladung platziert wurde, den erforderlichen Grad der mikrobiellen Reduktion erreicht hat und dass der Zyklus des Geräts letztendlich für die Sterilisation einer bestimmten Art von Ladung geeignet ist.
Typischer Umfang der Autoklavenqualifizierung und Sterilisationsvalidierung in der Lebensmittelindustrie
Temperaturverteilungstest: Auf der Suche nach dem „Cold Spot“
Der Temperaturverteilungstest hat ein primäres Ziel: Den Bereich oder Punkt innerhalb der Sterilisationskammer zu identifizieren, der während des standardisierten Sterilisationsprozesses die niedrigste, also kälteste, Temperatur aufweist. Dieser Bereich oder Punkt wird als „Cold Spot“ bezeichnet. Der Grund, warum dieser „Cold Spot“ von so großer Bedeutung ist, liegt darin, dass Produkte, die sich genau in diesem Bereich befinden, länger benötigen, um die für die Sterilisation erforderliche Temperatur zu erreichen. Somit stellt dieser Punkt das größte potenzielle Risiko für eine unzureichende Sterilisation dar. Nachdem dieser „Cold Spot“ einmal identifiziert wurde, sollte er in allen zukünftigen Tests und Verfahren als Referenzpunkt dienen. Hier sollte also ein Temperaturmessfühler platziert werden, um sicherzustellen, dass die gesamte Kammer die notwendige Sterilisationstemperatur erreicht hat.
Hitzedurchdringungstest: Optimierung und Sicherheit des Sterilisationsprozesses
Beim Hitzedurchdringungstest geht es in erster Linie darum, die Wärmeverhaltenseigenschaften einer spezifischen Kombination aus Produkt und Verpackung in einem gegebenen Autoklavensystem zu analysieren. Dies beinhaltet sowohl die Phase, in der das Produkt erhitzt wird, als auch die Phase, in der es wieder abkühlt. Ein fundiertes Verständnis dieses Verhaltens ist von entscheidender Bedeutung, um einen thermischen Prozess zu entwickeln, der nicht nur effizient, sondern auch sicher ist, und um sicherzustellen, dass jedes Produkt korrekt und gleichmäßig erhitzt wird.
Ein weiterer Aspekt dieses Tests ist die Identifizierung und Analyse von möglichen Abweichungen im Prozess. Das heißt, es wird gesucht, wo sich im Produkt oder im Behältnis der „kälteste Punkt“ befindet – dieser Punkt ist analog zum „Cold Spot“ im Temperaturverteilungstest, jedoch spezifisch für das Produkt oder den Behälter. Das Auffinden dieses Punktes ist entscheidend, um sicherzustellen, dass wirklich das gesamte Produkt die erforderliche Sterilisationstemperatur erreicht hat und somit das Risiko einer unvollständigen Sterilisation minimiert wird.
Die Gesetzesgrundlagen für die Validierung von Autoklaven: Ein umfassender Überblick
In der Medizin- und Industriewelt spielt die Qualifizierung von Autoklaven eine entscheidende Rolle, und die Gesetzeslage hierzu wird durch verschiedene Richtlinien und Normen geregelt. Eine der prominentesten unter diesen ist die DIN EN 554. Doch es ist essentiell, auch die anderen relevanten Normen und Richtlinien im Auge zu behalten. In diesem Leitfaden gehen wir auf die wichtigsten Gesetzesbestimmungen für Sterilisationsprozesse ein.
Ist die Autoklav-Validierung gesetzlich vorgeschrieben?
Ja, und das aus gutem Grund. Die Validierung von Autoklaven ist unerlässlich, da diese Geräte für die Sterilisation verschiedener Gegenstände verwendet werden, bei denen Sterilität von höchster Priorität ist. Einige typische Anwendungen beinhalten:
– Krankenhäuser
– Labore
– Lebensmittel
Es ist daher nicht nur vorgeschrieben, dass Autoklaven validiert werden müssen, sondern es gibt auch klare Richtlinien, wie dieser Prozess durchzuführen ist.
Anforderungen an die Dampfsterilisation gemäß DIN EN 554
Die DIN EN 554 ist heute die zentrale Norm für die Anforderungen an die Dampfsterilisation. Sie wurde in den Arbeitsgremien des Europäischen Normungskomitees (CEN) erarbeitet und definiert klar, wann ein Artikel als steril angesehen werden kann: Ein Artikel gilt dann als steril, wenn theoretisch nicht mehr als ein lebender Mikroorganismus in 1 Million (1×106) sterilisierten Einheiten des Endprodukts vorhanden ist. Dies gibt das Sterilisationsziel von SAL 10-6 (Sterility Assurance Level) vor, welches auch für Autoklaviervorrichtungen maßgeblich ist.
Weitere wichtige Richtlinien und Normen bei der Validierung von Autoklaven
Während die DIN EN 554 eine zentrale Rolle spielt, sind auch andere Normen und Richtlinien im Kontext der Qualifizierung von Autoklaven von Bedeutung:
DIN EN 554: Stellt die Grundlage für die Sterilisation von Medizinprodukten sowie die dazugehörige Validierung und Routineüberwachung dar.
DIN 58946: Legt die baulichen und betrieblichen Anforderungen an Dampfsterilisatoren im Gesundheitswesen fest.
DIN EN 285: Bietet Vorschriften für Großsterilisatoren und ist eine länderübergreifende Norm für diese Geräte.
EN ISO 17665: Legt im „Teil 1“ die Anforderungen an die Entwicklung, Validierung und Überwachung von Sterilisationsverfahren für Medizinprodukte fest.
EN ISO 15883: Diese Normserie behandelt Reinigungs- und Desinfektionsgeräte, insbesondere deren Geräteanforderungen und die Validierung von Abläufen.
Zusätzlich zu diesen Normen gibt es auch Leitlinien von Organisationen wie DGSV, DGKH und AKI, die sich mit der Validierung und Überwachung maschineller Reinigungs- und thermischer Desinfektionsprozesse für Medizinprodukte auseinandersetzen.
„Qualifizierung von Autoklaven für GMP, GLP und GCP Konformität“
Autoklaven spielen eine kritische Rolle im Kontext der Arzneimittelherstellung, Medizinprodukteherstellung und in Laboren, die sich mit sensiblen Stoffen wie Arzneimitteln, Pflanzenschutzmitteln oder Kosmetika befassen. Die EU-GxP-Leitfäden, einschließlich GMP (Gute Herstellungspraxis), GLP (Gute Laborpraxis) und GCP (Gute klinische Praxis), legen klare Richtlinien für die Qualifizierung und Validierung von Autoklaven fest, die direkt in diese Prozesse eingebunden sind.
Durch gesetzliche Regelungen wie das Arzneimittelgesetz, das Medizinproduktegesetz oder die Biostoff- und Gentechnikschutzverordnung, werden Anforderungen an die Sterilisation und die Autoklavenqualifizierung gestellt. Diese Gesetze verweisen oft auf EU-Richtlinien, Normen und andere Leitlinien, wodurch diese einen rechtlichen Rahmen bekommen.
Ein zentraler Punkt der EU-GxP-Leitfäden ist die Sicherstellung eines hohen und einheitlichen Qualitätsstandards. Das bedeutet, dass Autoklaven, die in den Herstellungsprozess für kritische Produktgruppen eingebunden sind, eine bestimmte Leistung und Konstruktion aufweisen müssen. Das gilt insbesondere, wenn sie für die Inaktivierung von sensiblen Materialien wie Mikroorganismen oder gentechnisch veränderten Organismen verwendet werden.
Wenn Ihr Autoklav direkt in diese Prozesse eingebunden ist, müssen Sie sicherstellen, dass er den Qualitätsstandards entspricht und regelmäßig geprüft wird. Die genauen Anforderungen an die Qualifizierung und Validierung können von den zuständigen Behörden definiert oder an bestehende Normen angepasst werden.
Ausführlicher Überblick über verschiedene Autoklaven-Systeme und ihre Anwendungen
Dampf-Luft-Autoklaven: Unterschied zwischen horizontalen und vertikalen Systemen
Der Dampf-Luft-Autoklav stellte eines der ersten Systeme in der Geschichte der Autoklaven dar und war insbesondere für die Verarbeitung von schwach säurehaltigen, konservierten Lebensmitteln geeignet. Der Grund dafür liegt in der hervorragenden Eignung von Dampf als Medium für die Wärmeübertragung. Eine zentrale Herausforderung beim Betrieb eines solchen Systems ist das Vorhandensein von Luft, die vor Beginn des Sterilisationsprozesses entfernt werden muss. Nicht entfernte Lufteinschlüsse könnten nämlich so genannte „kalte Stellen“ verursachen.
Horizontale Dampf-/Luft-Autoklaven: Statische und rotierende Systeme
Für Produkte, die in flexiblen Verpackungen wie Aluminium- oder Kunststoffschalen sowie Pouchbeuteln geliefert werden, ist es erforderlich, einen Überdruck zu erzeugen. Dieser Überdruck sollte den Sättigungsdampfdruck bei der Sterilisationstemperatur übersteigen. Der Hauptzweck hierbei ist die Verhinderung einer Ausdehnung der flexiblen Verpackung während des Sterilisationsprozesses. Um diesen Überdruck aufrechtzuerhalten, kann entweder das Entlüftungsventil geöffnet oder Druckluft zugeführt werden. Ein großer Ventilator am Ende des Autoklaven sorgt dann dafür, dass die zugeführte Druckluft gründlich mit dem Dampf gemischt wird, wodurch „kalte Stellen“ vermieden werden.
Vollwasser-Stand-Autoklaven: Horizontale und vertikale Systeme
Hier handelt es sich um eine spezielle Überdruck-Sterilisationsanlage, bei der das Prozessmedium überhitztes Wasser ist. Es ist von entscheidender Bedeutung, dass der Wasserstand im Autoklav immer über der höchsten Verpackung bleibt. Wenn dies nicht gewährleistet wird, könnten die oben liegenden Behälter nicht ausreichend sterilisiert werden.
Berieselungs- & Wasser-Sprüh-Autoklaven: Ein Unterschied in der Verteilung
Ein Berieselungsautoklav zeichnet sich dadurch aus, dass eine geringe Menge Prozesswasser vom Boden des Autoklaven durch eine Hochleistungspumpe aufgesaugt und dann über eine spezielle Metallplatte oder einen Verteiler im oberen Bereich des Geräts verteilt wird. Beim Wasser-Sprüh-Autoklav hingegen wird das aufgesaugte Prozesswasser mittels Zerstäubern verteilt, die sowohl oben als auch an den Seiten des Autoklaven angebracht sind.
Vertikale gegenüber horizontalen Autoklaven
Vertikale Autoklaven sind Systeme, bei denen die zu sterilisierenden Körbe entweder manuell oder mittels einer Hebevorrichtung in den Autoklav abgesenkt werden. Ihre Größe kann variieren, von kleinen Autoklaven, die nur einen Käfig beherbergen, bis hin zu größeren Systemen, die 3-4 Körbe aufnehmen können.
Horizontale Autoklaven dagegen sind so konzipiert, dass die Käfige in das Gerät geschoben oder transportiert werden. Sie reichen von kleinen Modellen, die nur einen Käfig beherbergen, bis hin zu umfangreichen Anlagen, die bis zu 12 oder mehr Käfige aufnehmen können.
Rotierende Batch-Autoklaven und ihre Eigenschaften
Bei rotierenden Batch-Autoklaven handelt es sich um horizontale Systeme, bei denen die Käfige in die so genannte Retorte geschoben oder befördert werden. Ein einzigartiges Merkmal dieser Systeme ist die Fähigkeit, die Käfige während des Sterilisationsprozesses zu drehen, um eine optimale Hitzedurchdringung zu gewährleisten.
GMP-Anforderungen: Qualifizierung von Geräten und Anlagen
- Qualifizierungs- und Validierungsaktivitäten sollten von entsprechend geschultem Personal
- Alle Dokumente, die während der Qualifizierung und Validierung erstellt werden, solltenvon den zuständigen Mitarbeitern in Übereinstimmung mit dem pharmazeutischen Qualitätssystem genehmigt und autorisiert werden.
- Qualifizierungsdokumente können gegebenenfalls gemeinsam genutzt werden, z. B. Qualifizierung Installationsqualifizierung und Betriebsqualifizierung.
- Werden Validierungsprotokolle oder andere Unterlagen von einer dritten Partei bereitgestellt, dieDienstleistungen zur Verfügung gestellt werden, sollten die zuständigen Mitarbeiter des Herstellers vor deren Validierungderen Angemessenheit und Übereinstimmung mit den internen Verfahren des Herstellers bestätigen.
- Protokolledes Dienstleisters können vor ihrer Verwendung durch zusätzliche Dokumente oder Prüfprotokolle ergänzt werden.
- Ergebnisse, die nicht den vordefinierten Akzeptanzkriterien entsprechen, solltenals Abweichungen aufgezeichnet und in Übereinstimmung mit den standortspezifischen Verfahren vollständig erklärt werden.
- Ihre Auswirkungen auf das Validierungsergebnis sollten im Bericht erläutert werden.
- Die Überprüfung und die Schlussfolgerungen der Validierung sollten aufgezeichnet und die erzielten Ergebnisse zusammengefasst werden, wobei auf die auf die Akzeptanzkriterien. Jede spätere Änderung der Akzeptanzkriterien sollte wissenschaftlich begründet werden. begründet werden, und aus der Validierung sollten endgültige Empfehlungen abgeleitet werden. Die formale Zulassung zur nächsten Qualifizierungs- und Validierungsstufe sollte von den entweder in der Phase der Genehmigung des Validierungsberichts oder in einem separaten zusammenfassenden Dokument. Eine bedingte Zulassung zur nächsten Qualifikationsstufe kann erfolgen kann erfolgen, wenn bestimmte Abnahmekriterien nicht erfüllt wurden oder Abweichungen nicht vollständig erklärt wurden, aber eine dokumentierte Bewertung durchgeführt wurde, die bestätigt, dass dies keine wesentlichen Auswirkungen auf das weitere Vorgehen hat.
- Die Anforderungen an Geräte, Bereiche, unterstützende Einrichtungen und Systeme sollten in der URS oder der funktionalen Spezifikation definiert werden. Die wesentlichen Qualitätsanforderungen sollten in dieser Phase definiert werden. Die wesentlichen Qualitätsanforderungen sollten in dieser Phase definiert werden, und jedes Risiko für die Anforderungen der Guten Herstellungspraxis sollte auf ein akzeptables Niveau reduziert werden. Die URS sollte während des gesamten Lebenszyklus der Validierung sein.
- Der nächste Schritt bei der Qualifizierung von Ausrüstung, Bereichen, unterstützenden Anlagen und Systemen ist die DQ, bei der die Übereinstimmung des Projekts mit den Anforderungen der Guten Herstellungspraxis nachgewiesen und dokumentiert wird. Herstellung. Die URS-Anforderungen sollten während der Projektqualifizierung überprüft werden.
- Falls angemessen und gerechtfertigt, können die Überprüfung der Dokumentation und die Durchführung einiger Tests in der FAT-Phase oder in anderen Phasen durchgeführt werden, ohne dass sie in der IQ und OQ am Herstellungsort zu wiederholen, wenn nachgewiesen werden kann, dass Transport und Montage die geprüfte Funktionalität nicht beeinträchtigen. geprüfte Funktionalität nicht beeinträchtigen.
FAQ
Q: Was ist die Qualifizierung von Autoklaven?
A: Die Qualifizierung von Autoklaven bezieht sich auf den Prozess, bei dem die Sterilisationsfähigkeit eines Autoklavs überprüft und dokumentiert wird. Dies umfasst die Prüfung der Temperaturverteilung, Messung der Sterilisationsparameter und Validierung des gesamten Sterilisationsprozesses.
Q: Warum ist die Qualifizierung von Autoklaven wichtig?
A: Die Qualifizierung von Autoklaven ist wichtig, um sicherzustellen, dass der Autoklav korrekt funktioniert und die erforderlichen Sterilisationsbedingungen erfüllt. Dies ist entscheidend, um eine zuverlässige Sterilisation von medizinischen Instrumenten und Materialien zu gewährleisten und die Sicherheit der Patienten zu gewährleisten.
Q: Welche Rolle spielt die Messung bei der Qualifizierung von Autoklaven?
A: Die Messung spielt eine entscheidende Rolle bei der Qualifizierung von Autoklaven. Es werden Temperatursensoren verwendet, um die Temperaturverteilung im Autoklav zu messen und sicherzustellen, dass sie innerhalb der vorgegebenen Grenzwerte liegt. Diese Messungen sind wichtig, um die Effektivität der Sterilisation zu überprüfen.
Q: Welche Kalibrierung wird für die Messung in Autoklaven benötigt?
A: Die Kalibrierung der Temperatursensoren ist wichtig, um sicherzustellen, dass die Messungen genau und zuverlässig sind. Die Sensoren sollten regelmäßig kalibriert werden, um sicherzustellen, dass sie korrekt arbeiten und genaue Messergebnisse liefern.
Q: Was sind bioindikatoren für Autoklaven?
A: Bioindikatoren sind biologische Proben, die zur Überwachung der Wirksamkeit der Sterilisation in Autoklaven verwendet werden. Sie enthalten spezifische Mikroorganismen wie Bacillus stearothermophilus, die empfindlich auf Sterilisationsprozesse reagieren. Durch die Messung der Überlebensrate dieser Mikroorganismen kann die Wirksamkeit der Sterilisation bewertet werden.
Q: Wie wird die Leistungsqualifizierung von Autoklaven durchgeführt?
A: Die Leistungsqualifizierung von Autoklaven beinhaltet eine Reihe von Tests und Messungen, um sicherzustellen, dass der Autoklav die erforderlichen Sterilisationsparameter erfüllt. Dies umfasst die Überprüfung der Temperaturverteilung, die Validierung des Sterilisationsprozesses und die Bewertung der Wirksamkeit der Sterilisation durch bioindikatorbasierte Tests.
Q: Welche Standards und Richtlinien sind bei der Qualifizierung von Autoklaven zu beachten?
A: Bei der Qualifizierung von Autoklaven sollten mindestens die Anforderungen der Normen EN 285 und ISO 17665 erfüllt werden. Diese Normen legen die Anforderungen an die Sterilisationsprozesse fest und stellen sicher, dass die Sterilisation mit feuchter Hitze zuverlässig und wirksam ist.
Q: Wann sollte die Qualifizierung von Autoklaven durchgeführt werden?
A: Die Qualifizierung von Autoklaven sollte vor der erstmaligen Inbetriebnahme und regelmäßig gemäß den Vorgaben eines validierten Plans durchgeführt werden. Darüber hinaus sollte die Qualifizierung nach wesentlichen Änderungen am Autoklav oder nach schwerwiegenden Störungen durchgeführt werden, um sicherzustellen, dass der Autoklav weiterhin wirksam funktioniert.
Q: Wer bietet Unterstützung bei der Qualifizierung von Autoklaven an?
A: Es gibt verschiedene Unternehmen, die Unterstützung bei der Qualifizierung von Autoklaven anbieten. Zu den namhaften Anbietern gehören Ellab, die innovative Lösungen zur Überwachung und Validierung von Sterilisationsprozessen anbieten. Darüber hinaus bieten viele Unternehmen Schulungen, Support und Beratungsdienste im Bereich der Autoklavenqualifizierung an.
Q: Wie kann ich die Messstellen in meinem Autoklav sichern?
A: Um die Messstellen in Ihrem Autoklav zu sichern, können Sie Logger und Sensoren verwenden, die speziell für die Überwachung von Sterilisationsprozessen entwickelt wurden. Diese Geräte können an den relevanten Messpunkten angebracht werden und kontinuierlich Temperaturwerte und andere relevante Daten liefern.
Q: Welche Rolle spielt die Messung im Autoklav Prozess?
A: Die Messung hat eine wichtige Rolle im Autoklav-Prozess. Sensoren und Logger messen kontinuierlich den Druck und die Temperatur im Inneren des sterilisators, um sicherzustellen, dass die Bedingungen für die Dampfsterilisation geeignet sind. Diese Messwerte können mit der ellab-valsuite® Software abgerufen und analysiert werden.
Q: Was ist die Zielsetzung der Qualifizierung von Autoklaven?
A: Die Zielsetzung der Qualifizierung von Autoklaven ist es, nachzuweisen, dass das Gerät konsequent und reproduzierbar die gewünschten Temperaturen und Druckbedingungen für die Sterilisation erreichen kann. Dabei ist es erforderlich, dass die Temperaturverteilung innerhalb des Autoklavs in den vereinbarten Toleranzen liegt.
Q: Wie wird die Kalibrierung der Autoklaven und sterilisatoren durchgeführt?
A: Die Kalibrierung von Autoklaven und Sterilisatoren wird meist vor Ort durchgeführt. Temperatursensoren und Druckmessgeräte werden mit geeigneten Kalibrationsgeräten verglichen. Die Kalibrierung sollte mindestens einmal jährlich oder nach Reparaturen und Modifikationen des Gerätes durchgeführt werden.
Q: Was sind Bioindikatoren und wofür werden sie im Autoklav Prozess verwendet?
A: Bioindikatoren sind spezielle Mikroorganismen, z.B. Bacillus stearothermophilus, die eine hohe Beständigkeit gegenüber Sterilisationsverfahren aufweisen. Sie werden in den Autoklav eingebracht und nach dem Prozess ausgewertet. Wenn sie abgetötet wurden, kann davon ausgegangen werden, dass der Prozess erfolgreich war.
Q: Was ist die Temperaturverteilung und warum ist sie wichtig für den Autoklav Prozess?
A: Die Temperaturverteilung bezeichnet die Gleichmäßigkeit, mit der die Hitze im Inneren des Autoklavs verteilt wird. Eine ungleichmäßige Temperaturverteilung kann zu unsachgemäßer Sterilisation führen, da nicht alle Bereiche des Autoklavs die notwendige Temperatur erreichen. Für die Verifizierung der Temperaturverteilung werden an verschiedenen Messstellen innerhalb des Autoklavs Temperatursensoren platziert.
Q: Was beinhaltet der Validierungsplan für Autoklaven?
A: Der Validierungsplan für Autoklaven umfasst verschiedene Aspekte, wie die Identifizierung der kritischen Parameter (Temperatur, Druck), Zielsetzung, Verantwortlichkeiten, Anforderungen an die Dokumentation, Verfahren für Messung, Kalibrierung und Wartung, sowie Prüfverfahren zum Nachweis der Leistungsqualifizierung und den Umgang mit Abweichungen und Fehlern.
Q: Wie wird die Leistungsqualifizierung von Autoklaven durchgeführt?
A: Die Leistungsqualifizierung von Autoklaven beinhaltet die Überprüfung, dass das Gerät unter den festgelegten Bedingungen funktioniert. Dies umfasst Tests mit den maximalen und minimalen Beladungen, sowie Tests mit Bioindikatoren. Dabei wird besonders auf die Einhaltung der DIN EN ISO und EN 285 Standards geachtet.
Q: Wie wird die Sterilisation mit feuchter Hitze durchgeführt?
A: Bei der Sterilisation mit feuchter Hitze werden Gegenstände durch Dampf bei hohen Temperaturen (meistens 121°C oder 134°C) sterilisiert. Der Dampf wird in den Autoklav geleitet, und seine Wärme tötet Mikroorganismen ab. Bioindikatoren dienen zur Sicherstellung der Wirksamkeit der Sterilisation.
Q: Wie verläuft die Qualifizierung von Autoklaven?
A: Die Qualifizierung von Autoklaven beinhaltet mehrere Schritte. Zunächst wird eine Risikoanalyse durchgeführt. Anschließend werden die kritischen Prozessparameter wie Temperatur und Druck definiert. Im nächsten Schritt werden Messungen zur Validierung dieser Parameter durchgeführt. Am Ende steht die Leistungsqualifizierung, bei der das korrekte Funktionieren des Autoklavs unter realen Bedingungen überprüft wird.
Q: Was ist ein Autoklav und wofür wird er verwendet?
A: Ein Autoklav ist ein Gerät, das zur Sterilisation von medizinischen Instrumenten, Laborgeräten und anderen Materialien verwendet wird. Durch die Kombination von hohem Druck und Hitze können Mikroorganismen und Sporen zuverlässig abgetötet werden.
Q: Was ist eine Qualifizierung von Autoklaven?
A: Die Qualifizierung von Autoklaven ist ein Prozess, bei dem nachgewiesen wird, dass ein Autoklav die spezifizierten Anforderungen erfüllt. Es ist wichtig für die Sicherstellung der Produktqualität und die Grundlage für die Durchführung von Validierungen.
Q: Welche Rolle spielt die Dampfsterilisation bei der Qualifizierung von Autoklaven?
A: Die Dampfsterilisation ist ein wesentlicher Bestandteil der thermischen Verfahren in Autoklaven. Sie muss validiert werden, um eine gleichmäßige Druck und Temperatur innerhalb der Kammer zu gewährleisten und die Sicherheit und Effektivität der gesamten Prozedur zu sichern.
Q: Was bedeutet „Sichern Sie Ihre Messstellen ganz einfach“ im Kontext von Autoklaven?
A: „Sichern Sie Ihre Messstellen ganz einfach“ bezieht sich auf die Verwendung von validierten Systemen wie Temperatursensoren und ein Drucksensor, die an verschiedenen Messstellen im Autoklav platziert werden. Diese gewährleisten, dass die Bedingungen im Autoklav unabhängig von der Steuerung korrekt sind.
Q: Wie viele Messstellen sollten mindestens in einem Autoklav platziert werden?
A: Es ist empfohlen, mindestens 10 Messstellen in einem Autoklav zu platzieren. Dies stellt sicher, dass Temperatur- und Druckverteilungen genau verfolgt und kontrolliert werden können.
Q: Wie wirken sich Validierungen auf die Qualifizierung von Autoklaven aus?
A: Validierungen spielen eine entscheidende Rolle im Prozess der Autoklaven-Qualifizierung. Sie helfen nachzuweisen, dass der Autoklav die gewünschten Ergebnisse liefert und dass die Temperatur- und Druckbedingungen im Inneren des Autoklavs vor, während und nach jedem Sterilisationszyklus korrekt sind.
Q: Was ist die software reports?
A: Die software reports ist ein Berichtstool, das bei der stetigen Überwachung und Kontrolle von Autoklaven-Prozessen hilft. Es ermöglicht das Nachverfolgen und Aufzeichnen von Temperatur- und Druckdaten, um die Qualität und Konsistenz von Sterilisationsprozessen zu gewährleisten.
Q: Worauf sollte man bei der Beladungskonfiguration und dem Beladungsmuster achten?
A: Die Beladungskonfiguration und das Beladungsmuster sind entscheidend für die Effizienz eines Autoklavs. Es ist wichtig, die worst-case-Beladung zu betrachten, d.h. die maximale Menge und Verteilung von Material, die in einem Zyklus behandelt wird, um sicherzustellen, dass alle Teile gleichmäßig sterilisiert werden.
Q: Was bedeutet „Qualifizierten gelieferten Autoklaven“?
A: Ein „qualifizierter gelieferter Autoklav“ bezieht sich auf einen Autoklav, der bereits bei der Lieferung und Installation eine Qualifizierung durchlaufen hat und deren korrekte Funktion überprüft und durch Tests bestätigt wurde.
Q: Was ist der Beweis für einen qualifizierten Autoklav?
A: Der Beweis für einen qualifizierten Autoklav ist in der Regel eine Reihe von Dokumenten und Berichten, darunter die software reports, die die korrekte Funktion und Effizienz des Autoklavs nachweisen. Jederzeit und egal kann daher nachvollzogen werden, ob und wie der Autoklav korrekt funktioniert.
Q: Benötigen Sie Hilfe bei der Qualifizierung Ihrer Anlagen?
A: Sollten Sie Hilfe bei der Qualifizierung Ihrer Anlagen benötigen, empfiehlt es sich, einen Experten zu konsultieren. Ein Spezialist kann Sie unterstützen, den Prozess der Autoklaven-Qualifizierung korrekt und effizient durchzuführen und dabei alle Relevanten Faktoren und Anforderungen zu beachten.
Q: Was ist die Qualifizierung eines Autoklavs?
A: Die Qualifizierung eines Autoklavs ist ein Prozess, der sicherstellt, dass der Autoklav korrekt funktioniert und den gewünschten Anforderungen und Standards entspricht. Sie umfasst verschiedene Testphasen, darunter Installation Qualifizierung (IQ), operationelle Qualifizierung (OQ) und Leistungsqualifizierung (PQ).
Q: Was ist die Validierung von Autoklaven?
A: Die Validierung von Autoklaven ist der dokumentierte Nachweis, dass das Gerät bei definierten Bedingungen konsequent und zuverlässig sterilisiert. Dies geschieht durch Methoden wie die Dampfdurchdringungsprüfung und den Bowie-Dick-Test.
Q: Wie läuft die Qualifizierung von Autoklaven ab?
A: Die Qualifizierung von Autoklaven beinhaltet Installation Qualifizierung (IQ), operationelle Qualifizierung (OQ) und Leistungsqualifizierung (PQ). IQ bestätigt, dass das Gerät richtig installiert wurde. OQ überprüft, dass das Gerät unter allen Betriebsbedingungen korrekt funktioniert. PQ demonstriert schließlich, dass das Gerät die erforderlichen Ergebnisse konsequent liefert.
Q: Was ist die Qualifizierung und Validierung von Autoklaven?
A: Die Qualifizierung und Validierung von Autoklaven ist ein Prozess, der sicherstellt, dass der Autoklav konsequent und effektiv sterilisiert. Die Qualifizierung stellt sicher, dass das Gerät gemäß den Installationsanforderungen ordnungsgemäß funktioniert, während die Validierung den Nachweis erbringt, dass das Gerät unter den vorgeschriebenen Bedingungen beständig sterilisiert.
Q: Was sind die Kosten der Validierung eines Autoklavs?
A: Die Kosten für die Validierung eines Autoklavs variieren je nach Anforderungen, Komplexität der Maschine und Größe der Produktion. Ein Fachspezialist oder eine zertifizierte Firma führt in der Regel diese Validierung durch, so dass die Kosten auch ihre Servicegebühren umfassen.
Q: Was ist die Rolle von Autoklaven in der Lebensmittelindustrie?
A: Autoklaven spielen in der Lebensmittelindustrie eine wichtige Rolle bei der Sterilisation von Lebensmitteln und Verpackungsmaterialien, um das Wachstum von Mikroorganismen zu verhindern und die Haltbarkeit zu verlängern.
Q: Wie wirkt sich die Qualifizierung und Validierung von Autoklaven auf die Lebensmittelindustrie aus?
A: Die Qualifizierung und Validierung von Autoklaven gewährleistet, dass die Maschinen in der Lebensmittelindustrie effektiv sterilisieren und die Sicherheit und Qualität der Lebensmittel beibehalten wird. So wird das Wachstum von Mikroorganismen verhindert und die Haltbarkeit der Lebensmittel verlängert.
Q: Was versteht man unter „Qualifizierung und Validierung von thermischen Prozessen“?
A: Unter „Qualifizierung und Validierung von thermischen Prozessen“ versteht man die Tätigkeiten, die sicherstellen, dass thermische Prozesse wie die Sterilisation in einem Autoklav konsequent und wirksam durchgeführt werden und gewünschte Ergebnisse liefern.
Q: Wie wird die Dampfsterilisation validiert?
A: Die Dampfsterilisation wird durch verschiedene Tests validiert, darunter die Dampfdurchdringungsprüfung und der Bowie-Dick-Test. Diese Tests stellen sicher, dass der Dampf alle Bereiche im Autoklav erreicht und effektiv sterilisiert.
Q: Wie funktioniert die Sterilisation von Lebensmitteln in einem Autoklav?
A: Bei der Sterilisation von Lebensmitteln in einem Autoklav werden die Lebensmittel hohen Temperaturen und Druck ausgesetzt. Dies tötet Mikroorganismen ab und verlängert die Haltbarkeit der Lebensmittel. Durch die Validierung und Qualifizierung des Autoklavs wird sichergestellt, dass dieser Prozess konsequent und effektiv durchgeführt wird.
IQ OQ PQ KWALIFIKACJA WALIDACJA, Brzozowa-Str. 1, 64500 Szamotuly, Polen.
REGON: 385660270, Ust.-IdNr.: PL6661952686
Kontakt
-
Email: info@qualifizierung-validierung.de
Telefon:
+48 61 624 36 40
[Sprachen: Deutsch]
+48 506 676 138 [Sprachen: Englisch, Polnisch]