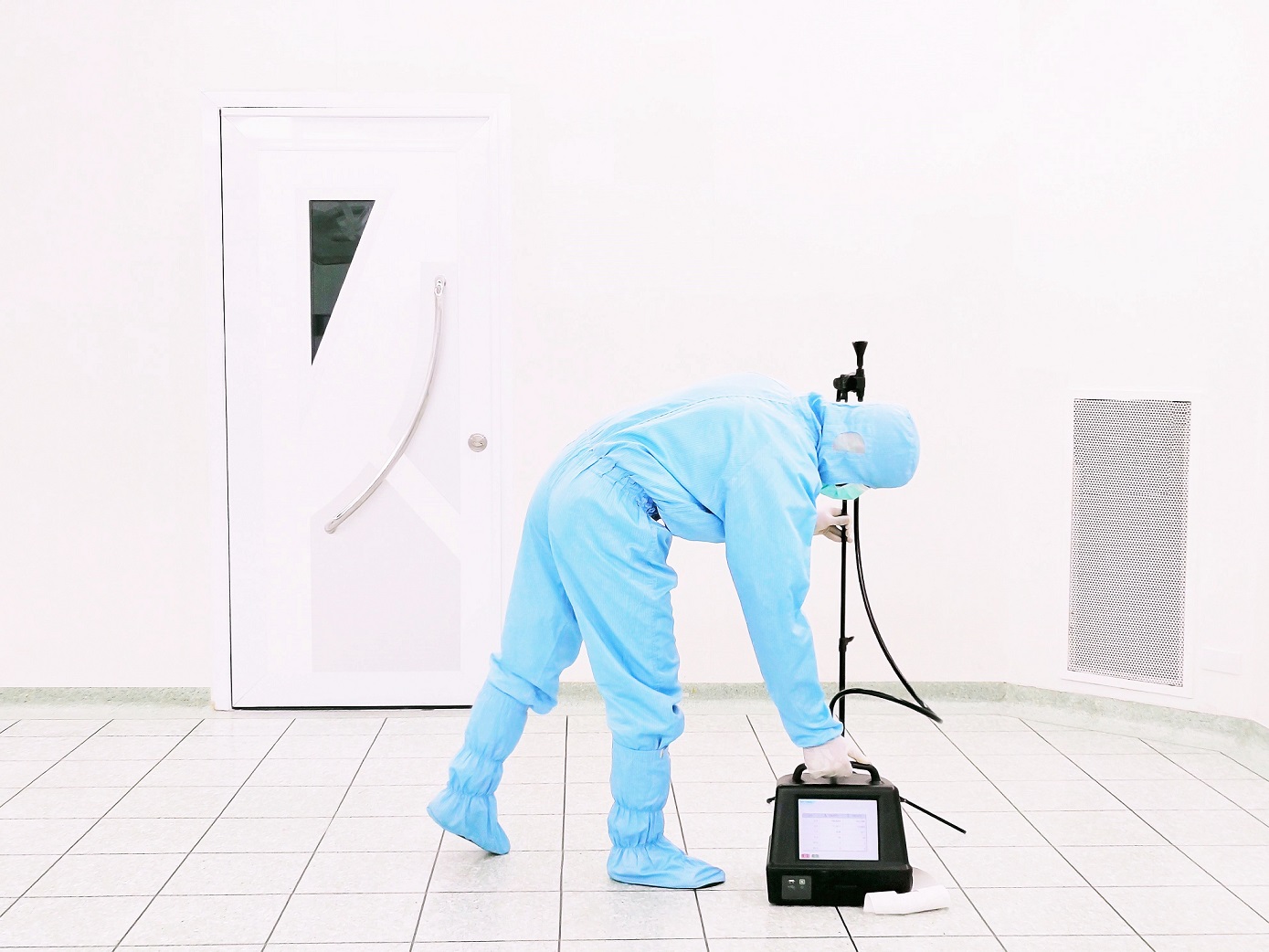
MESSUNG UND QUALIFIZIERUNG VON REINRÄUMEN [DIN 14644-1, DIN 14644-3]
Wir führen IQ/OQ/PQ-Qualifizierungen von Reinräumen und Reinbereichen sowie Laminar Flow Hauben durch. Folgende Tests können wir für Ihr Unternehmen durchführen:
- Lüftungsleistung / Anzahl der Luftwechsel im Raum
- Luftgeschwindigkeit unter dem Filter (Laminar Flow Hauben)
- Integrität der HEPA-Filter
- Partikelanzahl nach DIN EN ISO 14644-1
- Regenerationszeit des Raumes
- Druckunterschied zwischen den Räumen
- Rauchtest
- Lufttemperatur und relative Luftfeuchtigkeit
- Kohlendioxidgehalt in der Luft
DIN EN ISO ISO 14644-1 (Beschreibung der Methodik zur Messung der Partikelmenge in der Luft) und DIN EN ISO 14644-3 (Beschreibung der anderen Messmethoden, die bei der Validierung von Reinräumen verwendet werden) sind Normen, die in vielen Branchen – Pharmazeutik, Medizin, Labor, Automobil – in Cleanroom verwendet werden. Bei den von uns durchgeführten Qualifizierungen verwenden wir die aktuellen Ausgaben von DIN EN ISO 14644-1 und DIN EN ISO 14644-3. Wir vergleichen die Messergebnisse mit den in der DIN EN ISO 14644-Normenreihe, den EU-GMP-Anforderungen oder den Kundenrichtlinien festgelegten Akzeptanzkriterien. Nehmen Sie unsere Messdienstleistungen in Anspruch!
Die Klassifizierung von Reinräumen kann für eine oder mehrere der drei Phasen der Raumnutzung durchgeführt werden, d. h.
- „nach dem Bau“,
- „im Ruhezustand“,
- „im Einsatz“.
Unter dem Zustand „nach dem Bau“ ist zu verstehen, dass der Reinraum komplett mit allen Hilfssystemen/Medien, aber ohne Maschinen, Möbel, Materialien oder Personal ist. Vor den Messungen sollte der Raum gereinigt werden, da die Bau- und Installationsarbeiten oft nicht in einem „sauberen Standard“ durchgeführt werden. Es empfiehlt sich auch, die Lüftungsanlage vor den Messungen mindestens einige Tage lang laufen zu lassen.
Der „Ruhezustand“ ist dann gegeben, wenn alle Produktionsanlagen installiert sind und keine Produktionsvorgänge stattfinden. Messungen der Partikelanzahl „im Ruhezustand“ werden nach einer kurzen Zeit der Luftreinigung vorgenommen, die in der Regel mindestens 15-20 Minuten nach Ende des Produktionsbetriebs und nachdem das Personal den klassifizierten Raum verlassen hat, angenommen wird.
Der Zustand „im Einsatz“ ist dann gegeben, wenn alle Geräte in einem bestimmten Modus mit einer bestimmten Anzahl von Mitarbeitern in Betrieb sind.
Die Messung der Partikelanzahl erfolgt nach DIN EN ISO 14644-1. Basierend auf der Norm wird Folgendes festgelegt:
- Anzahl der Messpunkte (abhängig von der Fläche des Reinraums),
- das Volumen und die Zeit der an jedem Messpunkt entnommenen Luftprobe (abhängig von der erwarteten Reinheitsklasse des Reinraums).
Für Räume der Klassen A-D nach EUGMP werden Partikel mit einer Größe von mehr als 0,5µm und 5µm berücksichtigt. Für die Reinraumklassen ISO 7 – ISO 9 nach DIN EN ISO 14644-1 werden Partikel mit einer Größe von mehr als 0,5µm, 1µm und 5µm berücksichtigt. Für Reinräume ISO 1 – ISO 6 werden zusätzlich Partikel mit einer Größe von mehr als 0,1µm, 0,2µm, 0,3µm berücksichtigt, was den Einsatz eines Laser-Partikelzählers höherer Klasse erfordert.
Bevor die Messungen vorgenommen werden, muss für jeden Raum Folgendes festgelegt werden:
- der Zustand des Raumes, in dem die Messung durchgeführt werden soll („nach dem Bauen“, „im Ruhestand“, „im Einsatz“),
- die Raumfläche,
- die erwartete Sauberkeitsklasse im Raum.
Die Messung der Regenerationszeit (Eng. recovery test) wird durchgeführt, um die Fähigkeit eines Raumes zu beurteilen, sein ursprüngliches Reinheitsniveau oder das für eine bestimmte Reinheitsklasse erforderliche Reinheitsniveau wieder zu erreichen, nachdem eine erhebliche Menge an Partikeln (DEHS-Stoff) in die Luft eingeführt wurde. Für die Zwecke des Tests werden in der Regel so viele Partikel eingeführt, dass ein Verschmutzungsgrad erreicht wird, der das 100-fache (möglicherweise das 10-fache) der Reinheitsklassengrenze des Raums übersteigt.
Die Kenntnis der Regenerationszeit des Raumes ist ein sehr gutes Maß für die Beurteilung der Leistung eines Reinraumes, weil die erreichte Regenerationszeit des Raumes – im Gegensatz zu Informationen über die Anzahl der Luftwechsel allein – auch von der Form des Raumes, der Anzahl und dem Ort der Luftzufuhr- und -abfuhrpunkte sowie der Anzahl und dem Ort von „Hindernissen“ innerhalb des Raumes (Maschinen, Wände usw.) beeinflusst wird.
Die Regenerationszeit wird bei der Qualifizierung von neuen oder modernisierten Reinräumen (im „nach dem Bau“- oder „im Ruhezustand”) oder im Rahmen der periodischen Leistungsbewertung des Reinraumes bestimmt. Die Messung der Regenerationszeit ist nicht erforderlich für Räume oder Zonen, die von der Luft in einer Richtung durchströmt werden (z. B. laminare Kammern).
Die Raumregenerationszeit wird nach DIN EN ISO 14644-3 Punkt B.4 gemessen.
Bevor die Messungen vorgenommen werden, muss für jeden Raum Folgendes festgelegt werden:
- Verschmutzungsgrad der Luft: 100x (Standard) oder 10x
- Berücksichtigte Partikelgröße: >0,3µm (Standard), oder >0,5µm
- Ort der Messstelle: an der Stelle in der Nähe des Auslasses (Standard) oder an der Stelle im Raum mit der höchsten gemessenen Partikelzahl
Die Messungen werden mit einem genauen Differenzdrucksensor (Mikromanometer) durchgeführt, der im Bereich von -500 Pa ÷ +500 Pa kalibriert ist. Das Mikromanometer ist mit zwei Messstutzen ausgestattet, von denen einer über eine Leitung (flexibles Rohr mit einem Außendurchmesser von 8 mm) mit dem Raum mit dem höheren Druck verbunden ist. Der andere Stutzen (einschließlich des Geräts) befindet sich in einem Raum mit einem niedrigeren Druck (Referenzraum mit einem Überdruck von 0 Pa). Die Messung des Differenzdrucks in den Räumen wird gleichzeitig dreimal durchgeführt und der Durchschnittswert von den drei Messungen wird als Messergebnis angegeben.
Zur Durchführung der Messung werden in erster Linie Anschlüsse verwendet, die zu diesem Zweck in den Räumen fest installiert sind. Dies gewährleistet die Stabilität der Messbedingungen und bietet die beste Gelegenheit, die gesammelten Daten mit historischen Daten zu vergleichen. Wenn der Raum nicht mit einem geeigneten Anschluss ausgestattet ist, ist es manchmal möglich, das Kabel an der Türdichtung (oder unter der Tür) einzuführen.
Der Rauchtest (Eng. smoke test) wird in Reinräumen und in solchen Anlagen wie laminare Kammern durchgeführt, um die Richtung des Luftstroms zu erweisen, tote Zonen sichtbar zu machen und die Laminarität des Luftstroms zu bestätigen.
Die Rauchprüfung wird nach DIN EN ISO 14644-3 Punkt B3 durchgeführt.
Der Rauchtest kann für den gesamten Raum oder in mit dem Kunden vereinbarten Bereichen durchgeführt werden, die aufgrund der dort stattfindenden Vorgänge kritisch sind. Der Test liefert den Nachweis, dass die Raumluft ausreichend ausgetauscht wird und dass es keine „toten Zonen“ im Raum gibt, in denen es lokal zu einer höheren Ansammlung von Schadstoffen kommen könnte. Die Prüfung bestätigt auch direkt, ob die erforderliche Luftbewegungsrichtung an Türen oder technischen Öffnungen eingehalten wird, denn von der Luftbewegungsrichtung hängt der Schutz des betreffenden Bereichs vor Verunreinigungen/Kontaminationen ab. Während des Tests wird in der Nähe von Türen, die Räume mit unterschiedlichem statischen Druck trennen, Rauch erzeugt. Der Rauchstrom sollte auf den Raum mit dem niedrigeren Druck gerichtet sein. Der Rauch wird auch in andere Teile des Raumes eingeleitet, um das Vorhandensein von „toten Zonen“ im Raum zu beurteilen. Wenn im Raum ein guter Luftaustausch herrscht, verbleibt der Rauch nicht im Raum, sondern wird effizient zu den Abzugsgittern abgeleitet.
Bei Geräten mit unidirektionaler Luftbewegung (laminare Lüftungsöffnungen) dient der Rauchtest vor allem dazu, die Laminarität der Luftzufuhr zu überprüfen. Bei der Prüfung wird erwartet, dass der Rauchstrom parallel und ohne Turbulenzen über den geschützten Bereich verläuft. Der Test lohnt sich besonders für einen Arbeitsplatz, der mit den dort typischerweise verwendeten Geräten ausgestattet ist, um zu überprüfen, ob die Menge und Verteilungsweise der Geräte die Luftbewegung unter der laminaren Zufuhr nicht beeinträchtigt.
Die Lüftungseffizienz (und die Anzahl der Luftwechsel im Raum) wird nach DIN EN ISO 14644-3 Punkt B.2.2. gemessen.
Die dem Raum zugeführte Luftmenge wird mit einem Bolometer (an jedem Auslass separat) bestimmt, d. h. nach der in DIN EN ISO 14644-3 empfohlenen Methode. Die Anzahl der Luftwechsel im Raum pro Stunde wird dann berechnet, indem die gemessene Gesamtmenge der Zuluft durch das gemessene Raumvolumen (den Kubatur) dividiert wird.
Die Messung mit einem Bolometer setzt voraus, dass das Bolometer die Oberfläche des Lüfters genau abdeckt. Daher ist es notwendig, dass der Kunde die Abmessungen der Lüfter bestätigt, damit das Bolometer vor der Ankunft mit den entsprechenden Messhülsen ausgestattet ist.
Bevor die Messungen vorgenommen werden, muss für jeden Raum Folgendes festgelegt werden:
- Abmessungen der einzelnen Lüfter
- Installationshöhe der Lüfter/Deckenhöhe (wir messen nicht bei Deckenhöhen über 3,5 m).
Wir führen Qualifizierungen in Reinräumen (Cleanroom) gemäß den Anforderungen der GMP, der Norm ISO 14644-1 und der Norm ISO 14644-3 durch. Im Rahmen der Reinraumqualifizierung führen wir am häufigsten folgende Arten von Messungen durch: Messung der Anzahl fester Partikel in der Luft, Messung der Integrität von HEPA-Filtern, Messung der Regenerationszeit des Reinraums, Messung der linearen Luftgeschwindigkeit, Volumenstrom der Luftströmung, Messung der Anzahl der Luftwechsel im Raum, Test zur Visualisierung der Luftströmungsrichtung, Messung des Überdrucks des Reinraums im Vergleich zur angrenzenden Zone, Messung von Temperatur und Luftfeuchtigkeit im Raum, CO2-Konzentration in der Luft. Messungen in Reinräumen können als unabhängige Untersuchungen oder als Gruppe von Tests durchgeführt werden, die eine IQ OQ PQ Qualifizierung des Cleanrooms bilden (sog. Validierung von Reinräumen).
Installationsqualifizierung (IQ) ist ein Teil der Qualifizierung von Geräten/Installationen und Räumlichkeiten (u.a. Reinräume), bei der bestätigt wird, dass die zu qualifizierende Installation oder der Raum gemäß dem genehmigten Entwurf und den Empfehlungen des Herstellers gebaut und installiert wurde, der Lieferumfang der Bestellung entspricht (einschließlich der Dokumentation in diesem Bereich – Bedienungsanleitung, Betriebsanleitung) und die Schlüsselelemente des qualifizierten Systems oder des Reinraums korrekt identifiziert sind. Die Qualifizierung von Reinräumen (Cleanroom) wird hauptsächlich in Unternehmen der pharmazeutischen und kosmetischen Industrie durchgeführt, aber auch Labore erfordern manchmal eine IQOQPQ-Qualifizierung. Im Gegensatz zur Betriebsqualifizierung ist die Art der Tests, die im Rahmen der Installationsqualifizierung durchgeführt werden, oft ähnlich zwischen verschiedenen Gruppen von Geräten, Installationen und Systemen. Die Installationsqualifizierung IQ (einschließlich der IQ-Qualifizierung des Reinraums Cleanroom) umfasst oft: die Verifizierung des Abschlusses von FAT/SAT, die Überprüfung der Richtigkeit/Vollständigkeit der Lieferung sowie die Verifizierung der Unversehrtheit der gelieferten Elemente, die Identifizierung der Bestandteile des Geräts (Hersteller, Typ, Seriennummer, Material), die Verifizierung der Software, die Überprüfung der Kennzeichnung der Hauptelemente des Geräts/System/Raums, die Überprüfung der Vollständigkeit der technischen Dokumentation (Beschreibungen, Anleitungen, Schemata, Diagramme, Ergebnisse der Partikelemissionstests für Materialien und Geräte, die für den Cleanroom bestimmt sind). Die Installationsqualifizierung kann auch eine Überprüfung der mechanischen Konstruktion, eine Überprüfung der elektrischen Konstruktion, die Überprüfung der Richtigkeit der Installation und des Anschlusses an Medien (Strom, Wasser, Druckluft) umfassen. Im Rahmen der IQ-Tests können auch Messungen der Umgebungsbedingungen – meist Temperatur und relative Luftfeuchtigkeit – durchgeführt werden. Im Falle der Qualifizierung von Reinräumen (Cleanroom) kann auch die Konzentration von Kohlendioxid (CO2) im Raum untersucht werden. Die IQ-Qualifizierung kann auch eine Überprüfung der Liste der Messgeräte und der Liste der Ersatzteile, einen Bericht über die Softwareinstallation, Kalibrierungszertifikate für Mess- und Prüfgeräte umfassen. Wie bei jeder Qualifizierung werden auch bei der Installationsqualifizierung (IQ) die Daten der Personen, die die Qualifizierung durchführen, die Bedingungen und das Datum der Tests, die Identifikation der zur Durchführung der IQ-Qualifizierung verwendeten Messgeräte (falls zutreffend) berichtet. Die Anzahl der Überprüfungen während der Installationsqualifizierung kann unter der Bedingung eingeschränkt werden, dass bestimmte Tests während FAT/SAT durchgeführt wurden. Um einen Qualifizierungsplan für den Reinraum zu erstellen, ist in der Regel die entsprechende Dokumentation erforderlich (URS, Bestellung, P&ID-Schemata, Materiallisten, Produktdatenblätter, DTR des Geräts, Beschreibung des qualifizierten Systems). GMP weist darauf hin, dass die Installationsqualifizierung (minimale Anforderungen) umfassen soll: die Überprüfung der Korrektheit der Montage von Ausrüstungsteilen, Instrumenten, Geräten, Rohrleitungen und technischen Installationen im Hinblick auf ihre Übereinstimmung mit den technischen Zeichnungen und Spezifikationen; die Überprüfung der Korrektheit der Montage in Bezug auf zuvor festgelegte Kriterien; die Zusammenstellung und Verifizierung der vom Lieferanten übergebenen Bedienungs- und Wartungsanleitungen sowie der Wartungsanforderungen; die Kalibrierung der Instrumente; die Verifizierung von Baustoffen.
Die Operationelle Qualifizierung (OQ) zielt darauf ab, objektiven Beweis zu liefern, dass die einzelnen Funktionen des getesteten Reinraums/Cleanrooms, Geräts oder der Anlage korrekt funktionieren – entsprechend der funktionalen Spezifikation FS oder im Rahmen der geplanten Nutzung des Geräts durch den Benutzer. Die operationelle Qualifizierung wird nach dem erfolgreichen Abschluss der Installationsqualifizierung (IQ) durchgeführt und kann auch (ganz oder teilweise des ursprünglichen Umfangs der operationellen Qualifizierung) nach der Reparatur des Geräts oder Raums durchgeführt werden. Die während der operationellen Qualifizierung durchgeführten Tests unterscheiden sich je nach Art des qualifizierten Geräts, jedoch ist es möglich, bestimmte Testgruppen anzugeben, die häufig während dieses Teils der Qualifizierung durchgeführt werden. Ein beispielhafter Bereich der OQ-Tests für die Qualifizierung eines Reinraums: Funktionstests – Erreichung und Stabilität kritischer/extremer Systemparameter (z.B. Luftstromgeschwindigkeit unter laminarer Strömung, Anzahl der Luftwechsel im Raum, Raumregenerierungszeit), Alarmtests (Bestätigung der korrekten Aktivierung und Kommunikation von Alarmen), Erstellung von Berichten, Zugriffskontrolle auf einzelne Funktionen durch verschiedene Benutzergruppen des Reinraums; Identifizierung von Materialien und Messgeräten, die während der Qualifizierung des Reinraums verwendet wurden (Gültigkeit der Zertifikate/Kalibrierungsbescheinigungen); Tatsache der Durchführung von Schulungen für Benutzer der Anlage/des Reinraums; Vorhandensein genehmigter Anweisungen und Verfahren (Reinigungs-, Wartungs-, Kalibrierungsanweisungen). Der Qualifizierungsbericht sollte auch die Personen, die die operationelle Qualifizierung durchführen, und das Datum der Durchführung der einzelnen Tests angeben. Um einen Plan für die operationelle Qualifizierung eines Reinraums zu entwickeln, muss man über die entsprechende Dokumentation verfügen: funktionale Spezifikation (Arbeitsbereich des Geräts/Elements, Zielwerte der Arbeitsparameter), Charakteristikkarten und Systembeschreibung, DTR. GMP weist darauf hin, dass die im Rahmen der operationellen Qualifizierung durchgeführten Tests: auf der Grundlage der Kenntnis der Prozesse, Systeme und Geräte entwickelt werden sollten, um zu bestätigen, dass das System so funktioniert, wie es entworfen wurde; die unteren und oberen Grenzen der Betriebsparameter oder die Bedingungen des Worst-Case-Szenarios bestätigen sollten.
Die Ergebnisse der Messungen, die im Rahmen der Qualifizierung eines Reinraums durchgeführt werden, werden in Form von separaten Testkarten dokumentiert. Der Bericht über die Qualifizierung eines Reinraums umfasst auch: eine Beschreibung des Ziels der Qualifizierungsarbeiten, eine Beschreibung des qualifizierten Systems – die Systemgrenzen, eine grundlegende Beschreibung des Aufbaus und der Funktion, kritische Elemente, ein vereinfachtes Schema des Aufbaus, das die Anordnung der Hauptkomponenten zeigt (für komplexe Geräte und Systeme), eine Liste der Testkarten, die Karten der einzelnen IQ OQ PQ-Tests mit den Ergebnissen der Überprüfungen und Messungen, während der Qualifizierung festgestellte Abweichungen, eine Zusammenfassung der Qualifizierung mit Bezug auf die akzeptierten Kriterien, Kopien der aktuellen Kalibrierzertifikate der Messgeräte, die während der Qualifizierung des Geräts verwendet wurden, eine Liste der Personen, die an der Qualifizierung des Geräts teilgenommen haben.
Unser Unternehmen führt Qualifizierungen von Reinräumen in Unternehmen der pharmazeutischen, kosmetischen Industrie und in Laboren durch. Wir führen auch Qualifizierungen von Autoklaven, IQOQPQ-Qualifizierungen von Laborgeräten, Qualifizierungen von Druckluft (ISO 8573) durch. Wir arbeiten auch mit Lieferanten von Produktionsgeräten, Ausführern von Reinräumen und Lieferanten von Laborausrüstung zusammen, die aufgrund der Notwendigkeit, die Gültigkeit der Kalibrierung der bei der Qualifizierung verwendeten Messgeräte zu wahren, bevorzugen, die Durchführung eines Teils oder der gesamten Messungen zu unterbeauftragen.
Gemessen wird die Geschwindigkeit und Homogenität des Luftstroms unter dem Schwebstofffilter nach DIN EN ISO 14644-3 Punkt B.2. Die Messung dient zur Beurteilung der ordnungsgemäßen Funktion der Laminarströmung und des Filterverschleißgrades. Ein zu niedriger Wert der Luftgeschwindigkeit kann auf eine starke Verschmutzung (Verschleiß) des Filters hinweisen und macht einen Filterwechsel erforderlich. Das allgemein anerkannte Akzeptanzkriterium (EUGMP) für die Bewertung der Gleichmäßigkeit der Luftgeschwindigkeit unter einem HEPA-Filter beträgt 0,45 m/s +-20%.
Unser Unternehmen führt Luftgeschwindigkeitsmessungen durch, bietet jedoch keine Dienstleistungen für den Austausch und die Entsorgung von gebrauchten HEPA-Filtern an.
Die Integritätsprüfung der HEPA-Filter wird durchgeführt, um zu bestätigen, dass der Filter fest im Gehäuse installiert und frei von Schäden und Leckagen ist. Die Integritätsprüfung des HEPA-Filters erkennt die Leckage der unzureichend gereinigten Luft, was auf folgende zurückzuführen sein kann:
- mangelnde Dichtheit der Verbindung zwischen Filter und Lüfter (z. B. durch ungleichmäßigen Druck zwischen Filter und Lüftergehäuse, beschädigte oder abgenutzte Dichtung),
- Beschädigung des Filters während des Transports oder der Installation,
- falscher Einbau des Filters,
- übermäßiger Gebrauch des Filters.
Die Prüfung der Integrität der HEPA-Filter wird in erster Linie für kritische Räume in Bezug auf ihre Qualität und reine Zonen durchgeführt, z. B. in Reinräumen der ISO-Klassen 5 oder 6, laminaren Lüftern in mikrobiologischen Laboratorien. Viele Reinraumbenutzer führen keine der Integrität der HEPA-Filter in Räumen der ISO-Klassen 7 und 8 durch, wenn diese Räume die Anforderungen an die Partikelanzahl in der Luft erfüllen.
Wir führen die Prüfung der Integrität der HEPA-Filter nach DIN EN ISO 14644-3, Punkt B.7 durch.
Die Messung besteht darin, ein Prüfaerosol vor den zu prüfenden HEPA-Filter einzuführen, die Anzahl der Partikel vor dem Filter zu messen und anschließend die Anzahl der Partikel hinter dem Filter zu messen, während die Oberfläche des Filterrahmens, der Raum zwischen dem Rahmen und den Filterbefestigungswänden, der Bereich um die Dichtung und die gesamte Filteroberfläche mit einer speziellen Sonde abgetastet werden, die an einen Laserpartikelzähler angeschlossen ist.
ISO 14644-3 besagt, dass bei der Prüfung der Integrität von Filtern mit einem Wirkungsgrad ≥99,995% (HEPA-14-Filter und höher) eine Durchdringung von >0,01% als „Leckage“ betrachtet werden sollte, während bei Filtern mit einem Wirkungsgrad ≥99,95%, aber weniger als 99,995% (u.a. HEPA-13-Filter) eine Durchdringung von >0,1% als „Leckage“ betrachtet werden sollte.
Um das Prüfaerosol in die Anlage einzubringen, wird der Schlauch mit dem erzeugten Aerosol an das Lüfterkanal vor dem zu prüfenden Filter angeschlossen (eine Öffnung mit einem Durchmesser von 10 mm oder ein Stutzen mit einem Außendurchmesser von 7 mm ist erforderlich). Zur Messung der Aerosolkonzentration vor dem Filter ist in der Anlage eine Öffnung mit 13 mm Durchmesser oder ein Stutzen mit 10 mm Außendurchmesser erforderlich.
Technische Anforderungen an die Anlage:
- Erforderliches Loch zum Einführen des Prüfaerosols (vor dem Filter): Durchmesser von 13 mm.
- Erforderliche 230 V-Steckdose (vor dem Filter): in einer maximalen Entfernung von 25 m.
- Erforderliches Loch für die Messung der Konzentration des Testaerosols (vor dem Filter): Durchmesser von 10 mm.
- Erforderliche Ausbau und Einbau des Filterdeckels durch den Kunden (reinseitig).
- Bei Filterhöhen > 2,5 m ist von dem Kunden eine Plattform bereitzustellen.
In Reinräumen der ISO-Klasse 8 werden in der Regel mehrere Luftfilterungsstufen verwendet (z. B. G4-Vorfilter, F9-Filter, H13-Endfilter). Die Luftbewegung im Raum ist nicht unidirektional (es kommt zu einer Vermischung der dem Raum zugeführten „sauberen“ Luft mit der im Raum vorhandenen „schmutzigen“ Luft). Die Lüfter in einem ISO-8-Reinraum befinden sich normalerweise an der Decke. Die Luft wird durch einen HEPA-Filter im Lüfter (in der Decke) oder durch einen HEPA-Filter in der HVAC-Zentrale gereinigt. Die Lüftungsöffnungen befinden sich in der Regel an den Wänden in Bodennähe (z. B. in den Ecken des Raums). Die erforderliche Anzahl von Luftwechseln pro Stunde hängt von der Art der im Reinraum durchgeführten Tätigkeiten und der Anzahl des anwesenden Personals ab, aber das Ziel könnte sein, 10-40 Luftwechsel pro Stunde zu gewährleisten. In Reinräumen der ISO-Klasse 8 ist das Personal oft ständig anwesend. Das Personal kann in normaler Arbeitskleidung (lange Hosen, lange Ärmel, Kappe) und die Besucher mit einer Einwegschürze bekleidet sein. Es wird empfohlen, im Raum einen Mindestüberdruck von 5-10 Pa gegenüber der angrenzenden Zone aufrechtzuerhalten.
Bei der Qualifizierung eines Reinraums der ISO-Klasse 8 werden in der Regel folgende Tests durchgeführt: Messung der Partikelanzahl in der Luft, Messung der Regenerationszeit des Raums, Messung des Differenzdrucks, Messung der Temperatur und der relativen Luftfeuchtigkeit. Optionale Tests: Messung der Anzahl der Luftwechsel, Prüfungen der Integrität der HEPA-Filter, Rauchtest.
In Reinräumen der ISO-Klasse 7 wird die Luft in mehreren Stufen gefiltert (z. B. G4-Vorfilter, F9-Filter, H13 oder H14-Endfilter). Die Luftbewegung im Raum ist nicht unidirektional. Die Lufteinlässe im ISO-7-Reinraum befinden sich in der Regel an der Decke (der HEPA 13/14-Endfilter befindet sich im Deckenauslass). Die Luftauslässe befinden sich in der Regel an den Wänden in Bodennähe. Die erforderliche Anzahl von Luftwechseln pro Stunde liegt oft im Bereich von 20-60n/h. In Reinräumen der ISO-Klasse 7 ist das Personal normalerweise ständig anwesend. Das Personal kann in normaler Arbeitskleidung (lange Hosen, lange Ärmel, Kappe) und die Besucher mit einer Einwegschürze bekleidet sein. Es wird empfohlen, im Raum einen Mindestüberdruck von 10 Pa gegenüber der angrenzenden Zone aufrechtzuerhalten.
Bei der Qualifizierung eines Reinraumes der ISO-Klasse 7 werden in der Regel folgende Tests durchgeführt: Messung der Partikelanzahl in der Luft, Messung der Regenerationszeit des Raums, Messung des Differenzdrucks, Messung der Temperatur und der relativen Luftfeuchtigkeit. Optionale Tests: Messung der Anzahl der Luftwechsel, Prüfungen der Integrität der HEPA-Filter, Rauchtest.
In Reinräumen der ISO-Klasse 6 wird die Luft in mehreren Stufen gefiltert (z. B. Vorfilter F7, dann Filter H10, Endfilter H14). Die Luftbewegung im Raum ist nicht-unidirektional, unidirektional (laminar) oder gemischt. Die Luftauslässe in einem ISO-6-Reinraum befinden sich in der Regel an der Decke (das HEPA 13/14-Endfilter befindet sich im Deckenauslass). Die Lüfter in einem ISO 6-Reinraum sind an mehreren Stellen im Raum an der Unterseite der Wände angebracht. Die erforderliche Anzahl von Luftwechseln pro Stunde liegt oft im Bereich von 40-150 Luftwechseln /1h. Die Anwesenheit von Personal in Reinräumen der ISO-Klasse 6 sollte eingeschränkt werden. Personen, die Räume der ISO-Klasse 6 betreten, müssen einen speziellen Reinraumanzug oder eine mehrteilige Kleidung tragen (staubfrei, z. B. aus Polyester – lange Hose, lange Ärmel, Handschuhe, Kapuze mit Nackenschutz, Maske, spezielles Schuhwerk). Es wird empfohlen, unter der Oberbekleidung spezielle Reinraumunterwäsche zu tragen. Der Überdruck des Raumes gegenüber der angrenzenden Zone beträgt mindestens 10 Pa.
Bei der Qualifizierung eines Reinraumes der ISO-Klasse 6 werden in der Regel folgende Prüfungen durchgeführt: Messung der Anzahl der Luftwechsel, Prüfungen der Integrität der HEPA-Filter, Messung der Anzahl der Partikel in der Luft, Messung der Regenerationszeit des Raumes oder der Luftgeschwindigkeit unter dem Filter, Messung des Differenzdrucks, Messung der Temperatur und der relativen Luftfeuchtigkeit, Rauchtest.
In Reinräumen der ISO-Klasse 5 wird die Luft in mehreren Stufen gefiltert (z. B. Vorfilter F7, dann Filter H10, Endfilter H14). Die Luftbewegung im Raum ist normalerweise unidirektional (laminar). Die Luftzufuhr erfolgt über Auslässe, die sich an der Decke (seltener an der Wand) befinden. Zahlreiche Lüfter in einem ISO-5-Reinraum befinden sich in der Regel an der Unterseite der Wände oder im Boden (oder an der gegenüberliegenden Wand, wenn horizontale Lüfter verwendet werden). Bei Reinräumen mit laminarer Luftströmung kommt es nicht auf die Anzahl der Luftwechsel pro Stunde an, sondern auf den Wert der linearen Luftgeschwindigkeit unter dem Filter. Das Ziel ist in der Regel eine Strömungsgeschwindigkeit von 0,45 m/s +/- 20 %. Die Anwesenheit des Personals in einem Reinraum der ISO-Klasse 5 sollte nur in Ausnahmefällen zulässig sein. Personen, die einen Reinraum der ISO-Klasse 5 betreten, müssen einen speziellen Reinraumanzug oder mehrteilige Kleidung tragen (staubfrei, z. B. Polyester – lange Hose, lange Ärmel, Handschuhe, Kapuze mit Nackenschutz, Maske, spezielles Schuhwerk). Es wird empfohlen, unter der Oberbekleidung spezielle Reinraumunterwäsche zu tragen. Der Überdruck des Raumes gegenüber der angrenzenden Zone beträgt mindestens 10 Pa.
Bei der Qualifizierung eines Reinraums der ISO-Klasse 5 werden in der Regel folgende Tests durchgeführt: Messung der Anzahl der Luftwechsel, Prüfungen der Integrität der HEPA-Filter, Messung der Anzahl der Partikel in der Luft, Messung der Regenerationszeit des Raums oder der Luftgeschwindigkeit unter dem Filter, Messung des Differenzdrucks, Messung der Temperatur und der relativen Luftfeuchtigkeit, Rauchtest.
VORGESCHLAGENES PRÜFSPEKTRUM
REINRÄUME:
ISO-KLASSE 7-9 [GEM DIN EN ISO 14644-1]
GMP-KLASSE C-D [GEM EUGMP]
Partikelanzahl (Volumen jeder Probe: 28,3 l)
Regenerationszeit des Raumes
Druckunterschied zwischen den Räumen
Lufttemperatur und relative Luftfeuchtigkeit
REINRÄUME:
ISO-KLASSE 5-6 [GEM DIN EN ISO 14644-1]
GMP-KLASSE A-B [GEM EUGMP]
Partikelanzahl (Volumen jeder Probe: 1m3)
Regenerationszeit des Raumes
Druckunterschied zwischen den Räumen
Lufttemperatur und relative Luftfeuchtigkeit
LAMINAR FLOW HAUBEN
(LABOR-/INDUSTRIEMAßSTAB)
Integrität der HEPA-Filter
Luftgeschwindigkeit unter dem Filter
Partikelanzahl (Volumen jeder Probe: 28,3l oder 1m3)
Rauchtest
FAKULTATIVE PRÜFUNGEN
FÜR REINRÄUME
Lüftungsleistung / Anzahl der Luftwechsel im Raum
Integrität der HEPA-Filter
Rauchtest
Kohlendioxidgehalt in der Luft
TECHNISCHE ANFORDERUNGEN
FÜR AUSGEWÄHLTE PRÜFUNGEN
ÜBERPRÜFEN SIE, BEVOR SIE EINE BESTELLUNG AUFGEBEN
Lüftungsleistung / Anzahl der Luftwechsel im Raum:
Bei der Messungen verwenden wir Balometer.
Lüftergröße: 610 mm x 610 mm (Standard)
Bei anderen Lüftergrößen, setzen Sie sich bitte mit uns in Kontakt.
Lüfterleistung: 80 – 3500 m3/h.
Deckenhöhe: maximal 3,5 m.
Integrität der HEPA-Filter:
Erforderliches Loch zum Einführen des Prüfaerosols (vor dem Filter): Durchmesser von 13 mm.
Erforderliche 230 V-Steckdose (vor dem Filter): in einer maximalen Entfernung von 25 m.
Erforderliches Loch für die Messung der Konzentration des Testaerosols (vor dem Filter): Durchmesser von 10 mm.
Erforderliche Ausbau und Einbau des Filterdeckels durch den Kunden (reinseitig).
Bei Filterhöhen > 2,5 m ist von dem Kunden eine Plattform bereitzustellen.
BERICHTERSTATTUNG
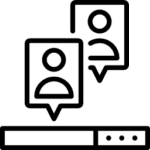
AUF DEUTSCH
UND ENGLISCH
Standardmäßig erstellen wir den Bericht in einer zweisprachigen Version: Deutsch-Englisch.
Auf Wunsch können wir den Bericht auch
in polnischer Sprache erstellen.
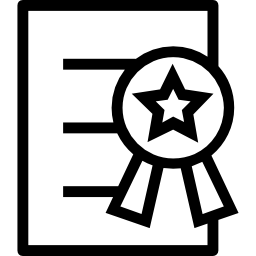
IM EINKLANG MIT DEN
GMP-GRUNDSÄTZEN
Die Ergebnisse werden auf separaten Prüfbögen (IQ/OQ/PQ) festgehalten. Der Bericht enthält u. a. die Angaben zu den verwendeten Geräten und der an den Prüfungen beteiligten Personen.
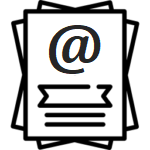
ELEKTRONISCHE
ÜBERMITTLUNG
Der Bericht wird in elektronischer Form (PDF-Dokument) übermittelt.
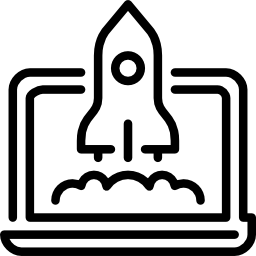
IN DER REGEL INNERHALB
VON 14-30 TAGEN FERTIG
In der Regel wird der Bericht innerhalb von 14 Tagen
(maximal 30 Tagen) nach der Messung übermittelt.
DIESE KUNDEN HABEN UNS BEREITS VERTRAUT
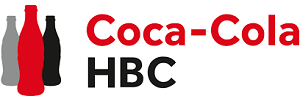
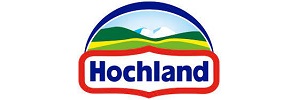
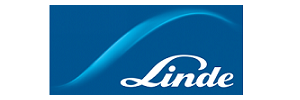
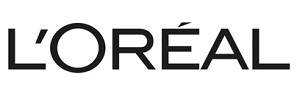
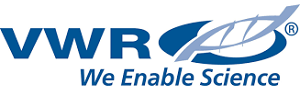
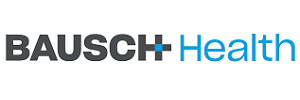
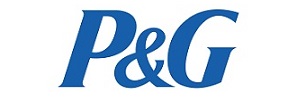
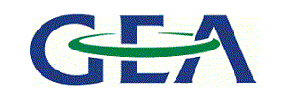
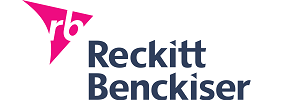
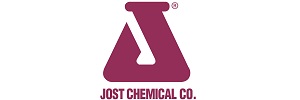
PREISLISTE
Möchten Sie schnell die Kosten für die Durchführung von Messungen abschätzen?
In der Preisliste finden Sie:
– Informationen über die von uns durchgeführten Messungen
– Preise der Untersuchungen
EIN GENAUES ANGEBOT ANFORDERN
Beim Bau von Reinräumen, die nach ISO 14644-1 errichtet wurden, ist ein korrektes Designverfahren unerlässlich, zusammen mit technisch-organisatorischen Absprachen (welche die Leitlinien für die Realisierung des Reinraums darstellen), der Ausführung von Bau- und Installationsarbeiten basierend auf einem genehmigten und geprüften Reinraum-Design, der Durchführung sorgfältiger Abnahmeverfahren gemäß DIN 14644, der Festlegung und Einhaltung der Betriebsregeln für den Reinraum sowie der Aufrechterhaltung eines Servicelevels, das ein funktionales Sicherheitsniveau gewährleistet (basierend auf Funktionalitätsmessungen, die je nach Zweck des Reinraums definiert sind). Besonders wichtig ist die Zusammenarbeit zwischen dem Designer, dem Investor und einem Fachexperten für DIN 14644-1 sowie die Qualitätssicherung (QA) während des gesamten Planungs-, Bau-, Abnahme- und Nutzungsprozesses des Reinraums.
Das Design der Lüftungs- und Klimaanlagensysteme für Reinräume muss den Anforderungen entsprechen, die mit seiner Architektur, den im Raum verwendeten Technologien, dem Raumlayout, der Aufteilung des Gebäudes in einen sauberen und einen unsauberen Bereich sowie der Verkehrsführung zusammenhängen.
Lüftungs- und Klimaanlagensysteme in Einrichtungen, die als Reinräume dienen, müssen:
– Luftreinheit auf einem erforderlichen Niveau gewährleisten, das durch die zulässige Konzentration der folgenden Verunreinigungen definiert ist: feste Partikel, Mikroorganismen, abhängig vom Typ der Räume und ihrer Funktion, mit besonderer Berücksichtigung der Anforderungen für den Reinraumbereich,
– die Übertragung von Verunreinigungen durch die Luft verhindern, indem ein erforderlicher Luftströmungsrichtung zwischen den Räumen (kaskadierte Luftdruckanordnung) sichergestellt wird, wobei die Richtung der Luftbewegung von Räumen mit höheren Anforderungen an die Luftreinheit zu Räumen mit niedrigeren Anforderungen beibehalten wird, die Aufrechterhaltung einer angemessenen Geschwindigkeit der zugeführten Luft, die Abführung interner Wärmegewinne und Feuchtigkeitsgewinne durch die Zuführung einer ausreichenden Menge an aufbereiteter Luft aus der Klimazentrale (Lüftungsanlage), das Sicherstellen komfortabler Bedingungen für das Personal durch Aufrechterhaltung der erforderlichen thermischen und Feuchtigkeitsbedingungen in den Räumen.
Grundlagen für das Design von Lüftungs- und Klimaanlagensystemen in Reinräumen
Klassifizierung der Räume
Abhängig von ihrem Zweck und den Anforderungen an die Luftreinheit (partikulär und mikrobiologisch) werden Reinräume gemäß ihrer Reinheit nach dem internationalen Standard DIN 14644-1 klassifiziert. Dieses Dokument enthält Anforderungen für Räume in Einrichtungen, in denen produktive Tätigkeiten ausgeführt werden, unter Berücksichtigung ihrer Bestimmung, der grundlegenden Arten von durchgeführten Aktivitäten sowie der Lösungen für Lüftungs- und Klimaanlagensysteme.
Grundlegende Anforderungen an das Zuluft- und Abluftsystem eines Reinraums ISO 8:
– Empfohlene Luftdruckanordnung: Überdruck von mindestens 10Pa
– Hochwirksame Filter der Klasse mindestens H12
– Geschwindigkeit des Luftstrahls in einer Entfernung von 0,30 m unterhalb der Abluftöffnung: 0,20 – 0,45 m/s
– Der Abluftstrom (entfernte Luft) muss ausreichen, um die Wärme- und Feuchtigkeitsgewinne auszugleichen; er sollte nicht weniger als 50% des zugeführten Außenluftstroms betragen
– Minimale Luftwechselrate: 15 Wechsel pro Stunde
In besonderen Fällen, die sich aus dem Nutzungskonzept, den ausgeführten Funktionen ergeben, und in Ermangelung spezifischer gesetzlicher Anforderungen, sollte die Zuordnung von Reinräumen zu einer bestimmten Klasse der Partikelreinheit gemäß DIN 14644-1 zwischen dem Investor, der Qualitätssicherung, dem Auftragnehmer und gegebenenfalls dem Bauingenieur vereinbart und durch ein schriftliches Dokument bestätigt werden, das der Planungsdokumentation beigefügt ist.
Der Luftstrom des Lüftungssystems sollte auf der Grundlage eines Bilanzs der Wärme-, Feuchtigkeitsgewinne oder der Schadstoffkonzentration bestimmt werden. Die angegebenen minimalen Luftwechselraten dienen nur als Hilfswerte und sollten nicht die Grundlage für das Design von Lüftungs- und Klimaanlagensystemen in Reinräumen sein, sondern lediglich dazu dienen, das erforderliche Minimum für die betrachtete Reinraumklasse zu bestimmen.
Sofern nicht anders festgelegt, sollte die Klasse der Partikelreinheit nach DIN 14644-1 auf der Grundlage von Produktionsoperationen festgelegt werden, die von anderen Einheiten mit einem ähnlichen Produktionsprofil durchgeführt werden, und die Zustimmung des Investors zu dieser Lösung eingeholt werden.
Vor Beginn des Designprozesses des Lüftungs- und Klimaanlagensystems (insbesondere für Räume der Klasse ISO 5 und sauberer) sollte der Investor in schriftlicher Form die geplanten Operationstypen in Reinräumen sowie die geplante Cleanroom-Ausrüstung spezifizieren. Die technologischen Anforderungen an den Reinraum ISO 5 und sauberer sollten endgültig festgelegt werden, nachdem sie mit dem Personal des Investors und der Qualitätssicherung besprochen wurden.
Räume und Bereiche, die den ISO 5-9 Klassen zugeordnet sind, müssen mit Lüftungs- und Klimaanlagensystemen ausgestattet sein, die mindestens die erforderliche Luftwechselrate, die geforderte Luftreinheit sowie thermischen Komfort gewährleisten, ohne dass eine Anpassung der relativen Luftfeuchtigkeit erforderlich ist. Die Hauptaufgabe des Lüftungs- und Klimaanlagensystems in einem Reinraum ist die Aufrechterhaltung der Luftreinheit. Dies wird erreicht durch:
– Aufrechterhaltung eines Überdrucks im Verhältnis zu angrenzenden Räumen,
– Zufuhr von sauberer Luft mit einer bestimmten, konstanten Geschwindigkeit und einer bestimmten Temperaturdifferenz zwischen der Zulufttemperatur und der tatsächlichen Raumtemperatur im Bereich von 1-3 K,
– Verdünnung von Verunreinigungen durch Zufuhr einer angemessenen Menge an Außenluft mit der erforderlichen Reinheit.
Für viele Reinräume wird die Verwendung eines Zuluftsystems mit Deckenlüftungsöffnungen oder einem vollständigen Laminar-Flow-Deckensystem mit geringer Turbulenz empfohlen, wobei die erforderliche Absinkgeschwindigkeit der Luftströmung beibehalten wird. Im geschützten Bereich von Reinräumen sollte eine angemessene Luftwechselrate sichergestellt werden, um thermischen Komfort, den erforderlichen Überdruck und einen einseitigen Luftstrom aus dem betreffenden Raum in angrenzende Räume durch Türen oder andere technische Elemente zu gewährleisten.
Es wird empfohlen, die Möglichkeit zu berücksichtigen, den Zuluftstrom (mindestens auf 50% des nominalen Zuluftstroms) zu reduzieren, wenn der Reinraum nicht genutzt wird. Es wird nicht empfohlen, das Lüftungs- und Klimaanlagensystem während Pausen in der Nutzung von Reinräumen, insbesondere der ISO 7 und niedriger, auszuschalten. Unter keinen Umständen darf ein Umkehren der Luftströmungsrichtung zwischen den Räumen zugelassen werden, indem der Überdruck im Verhältnis zu angrenzenden Räumen verloren geht. Nach dem Ausschalten des Lüftungs- und Klimaanlagensystems, das Reinräume bedient, ist es notwendig, es rechtzeitig (mindestens 60 Minuten) vor Beginn weiterer Produktionsaktivitäten wieder einzuschalten oder sicherzustellen, dass mindestens 30 Luftwechsel (bezogen auf Frischluft) im Raum stattgefunden haben, bevor er genutzt wird.
Um Ausfallzeiten in den Systemen, die Reinräume bedienen und die Produktionsoperationen im Reinraum gefährden könnten, zu vermeiden, wird die Verwendung redundanter Geräte (oder zumindest ein redundantes Lüfter-Setup) empfohlen, die mit einem Steuerungs- und Automatisierungssystem ausgestattet sind, das ihren automatischen Betrieb im Falle eines Ausfalls der Primärgeräte ermöglicht, gesteuert vom Reinraum aus. Für die Beheizung von Reinräumen wird die Verwendung von Flächenheizsystemen empfohlen. Es ist zulässig, Heizgeräte mit glatten, nicht gerippten, leicht zu reinigenden und zu desinfizierenden Heizflächen (z.B. Heizkörper in hygienischer Ausführung) zu verwenden. Die Luftbewegung, die zur Gewährleistung des thermischen Komforts im Bereich des Reinraums erforderlich ist, darf den Laminar-Flow nicht stören (in Reinräumen mit einseitiger Luftströmung). Bei Zweifeln wird empfohlen, eine Visualisierung des Luftstroms (Rauchtest) durchzuführen, z.B. gemäß DIN 14644-3.
Vor Beginn der Endarbeiten im Reinraum (Wände, Decken, Böden, Türöffnungen usw.) sollte eine gründliche, kommissionelle Überprüfung der gesamten Bau- und Installationsstruktur durchgeführt und alle Öffnungen und andere Elemente, die zum Verlust der Dichtheit des Raumes führen, mit für Reinräume zugelassenen und geeigneten Materialien abgedichtet werden (gemäß DIN 14644-14). Die Kommission sollte aus dem Investor und/oder Nutzer, dem Auftragnehmer und einem Bauaufsichtsinspektor bestehen. Die Dichtheit des Raumes sollte durch ein entsprechendes Protokoll bestätigt werden, das von allen Kommissionsmitgliedern unterschrieben wird. Vor der Montage der endgültigen Elemente der Lüftungsinstallation (z. B. Laminar-Flow-Decke, Mischlüftungsauslässe, Abluftöffnungen, Drosselklappen, Durchflussregler) sollten endgültige Dichtheitsprüfungen der Zuluft- und Umluftinstallationen in Anwesenheit eines Vertreters des Investors und/oder Nutzers sowie eines Bauaufsichtsinspektors im Sanitärbereich durchgeführt werden. In besonderen Fällen wird empfohlen, dass ein Validierungs- oder HVAC-Spezialist zusätzliches Mitglied der Kommission ist.
Die Überdruckmessung zwischen den Räumen sollte unterhalb der abgehängten Decke durchgeführt werden. Gleichzeitig sollte in allen Reinräumen, die durch Überdruck geschützt sind, zusätzlich ein Überdruck zwischen dem Raum und dem Raum über der abgehängten Decke sichergestellt werden. In Reinräumen mit den höchsten hygienischen Anforderungen (ISO 5 und sauberer) wird in der Regel ein laminarer Luftstrom eingesetzt. Der Zuluftstrom muss, neben der Gewährleistung einer angemessenen Geschwindigkeit der Zuluft und einer angemessenen Zulufttemperatur, die Wärmegewinne und Feuchtigkeitsgewinne entfernen und dabei den erforderlichen Überdruck im Verhältnis zu angrenzenden Räumen aufrechterhalten.
Reinräume der Klasse ISO 5 erfordern in der Regel eine dreistufige Filtration der Zuluft und eine einstufige Filtration der Abluft. Die minimalen Anforderungen an die Luftfilterklassen der Zuluft sind wie folgt:
– 1. Stufe: Filter der Klasse F7
– 2. Stufe: Filter der Klasse F9
– 3. Stufe: Filter der Klasse H13
In Gebieten mit hoher Staubbelastung der Außenluft, in industrialisierten und großen Städten, sollte dem Filter F7 ein Grobfilter vorgeschaltet werden. Für die Filtration der Abluft sollten Filter der Klasse mindestens M5 und Partikelseparatoren an den Abluftgittern mit Maschenweiten von nicht mehr als 0,8 mm verwendet werden. Wandabluftgitter sollten im Raum möglichst gleichmäßig verteilt angeordnet werden, um die Stabilität des Laminar-Flows zu gewährleisten, indem sie beispielsweise in den vier Ecken des Raumes oder in deren Nähe platziert werden, mit zwei Gittern an einem Standort – eines unter der Decke und das andere über dem Boden. Es sollte 20% des Luftvolumenstroms aus dem Deckenbereich (durch Gitter in einem Abstand von bis zu 0,30 m unterhalb der Deckenoberfläche) und 80% des Luftstroms aus dem Bodenbereich (in einer Höhe von bis zu 0,30 m über dem Bodenniveau) entfernt werden. Die Position der oberen Abluftgitter sollte nicht das Phänomen des direkten Ansaugens der Zuluft verursachen (sog. Kurzschlussphänomen). Es wird empfohlen, eine Lösung zu verwenden, die eine individuelle Einstellung des Luftstroms für obere und untere Abluftgitter ermöglicht, z. B. durch den Einsatz von Regelklappen oder Gittern mit eingebauten Regelklappen. Der direkt abgeführte Luftstrom während des Betriebs des Systems darf nicht weniger als 50% des zugeführten Außenluftstroms betragen, wobei der für die Auswahl der Abluftgitter zugrunde gelegte Abluftstrom nicht weniger als 90% des Zuluftstroms betragen sollte.
Um die erforderliche Luftreinheit in Reinräumen der Klasse ISO 5 bis ISO 8 zu gewährleisten, ist der Einsatz von Schleusen erforderlich. In der Schleuse muss ein Unterdruck im Vergleich zum Reinraum und ein Überdruck im Vergleich zu den angrenzenden Räumen sichergestellt werden. Der Abfluss überschüssiger Ausgleichsluft sollte systematisch erfolgen (z.B. durch Entlüftungsklappen) oder durch einen Spalt unter der Tür. Die Zuluft zur Schleuse muss durch Hygiene-Luftauslässe mit einem hochwirksamen Filter der Klasse mindestens H13 erfolgen, wobei eine angemessene Luftwechselrate gewährleistet wird.
Bei der Verwendung eines Luftbefeuchters in der Zuluftanlage ist es notwendig, einen Filter der Klasse F7 vor dem Befeuchter zu platzieren. Während der Nichtnutzung von Räumen der Klassen ISO 8 oder ISO 9 kann das mechanische Lüftungssystem abgeschaltet werden, jedoch sollte es 60 Minuten nach Verlassen des Raums durch das Produktionspersonal noch in Betrieb sein und 30 Minuten vor Produktionsbeginn wieder eingeschaltet werden. Im Kühlleistungsbilanz der Klimaanlagen müssen die Empfehlungen der Hersteller für die im Reinraum installierten Geräte bezüglich der Grenzparameter für den Betrieb der Geräte berücksichtigt werden. Diese Richtlinien bieten eine umfassende Grundlage für die Gestaltung, den Betrieb und die Wartung von Lüftungs- und Klimaanlagensystemen in Reinräumen, um die Einhaltung der erforderlichen Standards für Luftreinheit, Temperatur und Druckverhältnisse sicherzustellen. Durch die Anwendung dieser Praktiken können Unternehmen die Produktqualität verbessern, das Risiko von Kontaminationen minimieren und die Einhaltung relevanter Vorschriften und Normen gewährleisten.
Um eine ordnungsgemäße Druckkaskade in Reinräumen aufrechtzuerhalten, müssen folgende Anforderungen erfüllt sein:
– Der Luftdruckunterschied zwischen dem Reinraum und allen angrenzenden Räumen sollte nicht weniger als 10 Pa betragen,
– Der Luftdruckunterschied zwischen dem Hilfsraum und dem Korridor sollte nicht weniger als 5 Pa betragen,
– Der Luftdruckunterschied zwischen dem sauberen Korridor und dem schmutzigen Korridor sollte nicht weniger als 5 Pa betragen.
Für alle Reinräume wird empfohlen, einen Über-/Unterdruck von nicht weniger als 10 Pa im Vergleich zur Schleuse aufrechtzuerhalten.
Im Falle eines besonderen Risikos sollte im Reinraum eine Druckkaskade von mindestens 15 Pa Überdruck zwischen dem Raum und der Schleuse sowie mindestens 5 Pa zwischen der Schleuse und dem Korridor gewährleistet sein. In allen Räumen wird empfohlen, einen größeren Luftdruckunterschied als die minimalen Werte aufrechtzuerhalten, jedoch unter Einhaltung der Anforderungen, ohne den maximal zulässigen Schallpegel A in den untersuchten Räumen zu überschreiten.
Es ist nicht zulässig, Räume mit unterschiedlicher Funktion und verschiedenem Druckniveau innerhalb eines Raumes zu kombinieren.
Das erforderliche Über-/Unterdruckniveau muss unbedingt während jeder Betriebsphase der Anlage aufrechterhalten werden, unabhängig von der Filterverschmutzung, dem Betriebsmodus (Voll- oder reduzierte Leistung) und anderen Betriebsstörungen des Lüftungs- und Klimaanlagensystems. Das Steuerungs- und Automatisierungssystem, das die korrekte Funktion der Lüftungs- und Klimaanlagensysteme überwacht, muss die genannten Anforderungen berücksichtigen.
Diese Richtlinien sind entscheidend, um die Kontaminationskontrolle in Reinräumen zu gewährleisten und einen sicheren Betrieb unter Berücksichtigung des Schutzes von Produkten, Personal und Umgebung zu ermöglichen. Die Einhaltung einer korrekten Druckkaskade hilft, die Einschleppung von Verunreinigungen zu verhindern und die Integrität der Prozesse in kritischen Umgebungen zu wahren.
Luftauslässe für Reinräume müssen den erhöhten hygienischen Anforderungen entsprechen und leicht zugänglich sein, um eine regelmäßige Reinigung zu ermöglichen. Sie sollten aus glatten, abrieb- und korrosionsbeständigen Materialien hergestellt sein (z.B. aus Edelstahl 1.4301) und sich für eine effektive manuelle Reinigung und Desinfektion eignen.
Laminar-Luftauslässe sind ein zentrales Element des Lüftungs- und Klimatisierungssystems, das einen Reinraum versorgt. Die zugeführte Luft sollte in einer niedrig-turbulenten Weise von oben nach unten über den gesamten streng geschützten Bereich strömen, wobei Geschwindigkeit und Temperatur der Luft unabhängig von den Umgebungsbedingungen beibehalten werden.
Es wird gefordert, dass:
– die Außenluft nur durch einen Laminar-Flow-Deckenbereich in den Raum eingeführt wird,
– die erforderliche Absinkgeschwindigkeit zur Aufrechterhaltung eines stabilen laminaren Flusses im Bereich von 0,18-0,25 m/s liegt (gemessen in einer Höhe von 1,20 m über dem Boden),
– als Endfilter direkt in der Auslassfläche der Decke ein hochwirksamer Filter der Klasse mindestens H13 (nach EN 1822-1) installiert ist; in besonderen, im Projekt begründeten Fällen (z.B. wenn die Technologie den Wechsel der Filter von der schmutzigen Seite her ermöglicht), ist es zulässig, den hochwirksamen Filter am Lufteinlass zur Expansionskammer des Laminar-Auslasses zu positionieren,
– im Laminar-Flow-Deckenbereich ein Strahlstabilisator (Laminarisator) installiert ist, der aus einem hygienisch geeigneten Gewebe besteht,
– die Ausstattungselemente und die Deckenkonstruktion des Laminar-Flow-Deckenbereichs dicht sind und so konstruiert wurden, dass keine Luftlecks innerhalb ihres Bereichs vorhanden sind (Leck am Filter, Leck an der Verbindung des Filterrahmens mit dem strukturellen Element, das den Filter in der Laminar-Flow-Decke hält, Leck zwischen dem Filterrahmen und dem Filtermaterial, Leck zwischen dem strukturellen Element und dem Lüftungskanal),
– Messanschlüsse leicht zugänglich sind.
Schräge Luftauslässe
Schräge Luftauslässe dürfen nur in Reinräumen mit geringeren hygienischen Anforderungen verwendet werden. Direkt im Auslass muss ein hochwirksamer Filter der Klasse mindestens H13 installiert sein. Schräge Luftauslässe sollten in der Ecke von Wand und Decke platziert werden, um einen linearen Auslass zu bilden (nur auf einer Seite des Raumes), so dass die zugeführte Luft in Richtung des geschützten Bereichs strömt. Die Einblasgeschwindigkeit des Auslasses wird vom Hersteller festgelegt, sollte jedoch nicht höher als 2 m/s sein und eine Luftstromgeschwindigkeit im Bereich des geschützten Bereichs von 0,15 m/s – 0,25 m/s gewährleisten.
Luftauslässe mit turbulenter Strömung
In besonderen Fällen, abhängig von der Bestimmung der Reinräume, ist es erforderlich, direkt im Auslass hochwirksame Filter der Klasse mindestens H11 zu installieren, unter Beibehaltung der Dichtigkeit der Montage. Die Einblasgeschwindigkeit des Auslasses wird vom Hersteller festgelegt, sollte jedoch nicht höher als 2 m/s sein und die empfohlenen Luftgeschwindigkeitsparameter im Aufenthaltsbereich der Personen gewährleisten.
Abluftöffnungen in Reinräumen müssen den erhöhten hygienischen Anforderungen dieser Räume entsprechen und leicht zugänglich sein, um eine regelmäßige Reinigung zu ermöglichen. Sie sollten aus glatten, abrieb- und korrosionsbeständigen Materialien gefertigt und leicht zu reinigen sowie zu desinfizieren sein.
Die Anordnung der Abluftöffnungen in einem Reinraum sollte einen sicheren, stabilen und gerichteten Luftstrom durch den Reinraum gewährleisten, der die Überschreitung der Grenzwerte für schädliche Kontaminationen an jedem Punkt des Raumes verhindert. Dies soll so erfolgen, dass Störungen durch die Vermischung von sauberer Luft mit Abluft minimiert werden.
Abluftgitter in Reinräumen der Klasse ISO 8 und ISO 5:
Die Abluft aus Reinräumen sollte über hygienische Wandgitter erfolgen, die nahe dem Boden und der Decke platziert sind, nicht weiter als 0,30 m von der Boden- und Deckenoberfläche entfernt und gleichmäßig im Reinraum verteilt.
Abluftgitter in Reinräumen der Klasse ISO 5 und ISO 8 sollten mit Flockenabscheidern ausgestattet sein, deren Maschenweite <0,8 mm beträgt. Es sollte möglich sein, das Abluftgitter leicht zu demontieren, um den Flockenabscheider auszutauschen und zu reinigen.
Abluftkomponenten in anderen Räumen:
In Räumen der Klasse ISO 9 sollten Abluftkomponenten gemäß den Grundsätzen der Ingenieurskunst und den geltenden Vorschriften angeordnet werden, wobei deren Zugänglichkeit für das technische Personal zu berücksichtigen ist. In Räumen mit erhöhten hygienischen Anforderungen sollten hygienische Abluftöffnungen verwendet werden, die für regelmäßige Reinigung und Desinfektion geeignet sind.
Durch die Einhaltung dieser Richtlinien wird sichergestellt, dass die Luftqualität in Reinräumen aufrecht erhalten bleibt, indem verhindert wird, dass schädliche Partikel und Mikroorganismen im Raum verbleiben oder sich verteilen. Die regelmäßige Wartung und Reinigung der Abluftsysteme ist entscheidend für die Aufrechterhaltung der erforderlichen Reinraumstandards und die Gewährleistung der Sicherheit und Effektivität der dort durchgeführten Prozesse.
Klima- und Lüftungszentralen (HVAC) für Reinräume müssen außerhalb der Reinräume installiert, leicht zugänglich für technisches Personal, vor unbefugtem Zugriff geschützt sein und folgende Anforderungen erfüllen:
– Alle Komponenten der Klima- und Lüftungszentralen müssen den Normen EN 13093 und EN 1886 entsprechen.
– Die Anlagen müssen einen konstanten, einseitigen Luftstrom durch das gesamte Lüftungssystem sicherstellen.
– Jede Zentrale muss eine eigene Produktspezifikation haben.
– Alle Innenflächen müssen glatt, frei von scharfen Kanten sein und so gestaltet werden, dass sie die Bildung von Mikroorganismen verhindern.
– Alle Innenflächen und Komponenten (Wärmetauscher, Ventilatoren) müssen leicht zugänglich für Reinigung und Desinfektion sein.
– Halboffene Profile oder Verbindungen, in denen sich Schmutz ansammeln kann und die schwer zu reinigen sind, sollten vermieden werden; Schrauben und andere ähnliche Konstruktionselemente sollten nicht aus den Innenwänden des Gehäuses herausragen.
– Materialien, die mit der konditionierten Luft in Kontakt kommen, müssen korrosionsbeständig sein und dürfen keine Gefahr der Emission von festen Partikeln oder schädlichen chemischen Substanzen darstellen.
– Kondensatwannen müssen korrosionsbeständig sein (z.B. Edelstahl 1.4301) und einen kontinuierlichen und vollständigen Abfluss des Kondensats aus der Anlage gewährleisten; der Abfluss aus jeder Kondensatwanne muss einen eigenen Siphon haben.
– Die Kondensatableitung muss aus Rohren mit einem Durchmesser von mindestens 40 mm bestehen.
– Alle faserigen und porösen Materialien, mit Ausnahme der austauschbaren Elemente wie Filtereinsätze, sollten durch ein geeignetes, glattes Material geschützt sein, das gegen wiederholte Reinigung und Abrieb beständig ist.
– Die Zentralen sollten mit Inspektionsfenstern und Innenbeleuchtung ausgestattet sein, mindestens in der Sektion der Ventilatoren, Filter und Befeuchter; die Größe der Inspektionsöffnung sollte eine einfache visuelle Kontrolle des Inneren der Zentrale ermöglichen und einen Durchmesser von mindestens 150 mm haben.
– Als Dichtungsmittel sollten nur in Reinräumen zugelassene Materialien verwendet werden.
– Die Filter der ersten und zweiten Stufe sollten so montiert sein, dass sie von der schmutzigen Seite aus gewechselt werden können, sodass der Luftstrom durch die Zentrale eine ordnungsgemäße Abdichtung des Filters gewährleistet.
– Absperrklappen für Ein- und Auslassöffnungen der Zuluft und Abluft sollten die Dichtigkeitsanforderungen der Klasse 2 (nach EN 1751) erfüllen.
– Die Gehäusedichtigkeit der Zentralen sollte mindestens der Klasse L2(R) nach EN 1886 entsprechen.
– Die mechanische Festigkeit des Gehäuses, die seiner Beständigkeit gegen Verformungen unter dem Einfluss des statischen Luftdrucks entspricht, sollte mindestens der Klasse D2 nach EN 1886 entsprechen.
– Die Wärmeisolierung der Zentralen sollte einen Wärmeverlust nicht größer als für die Klasse T3 nach EN 1886 definiert zulassen, und Wärmebrücken sollten nicht größer als für die Klasse TB4 (TB3 für im Freien installierte Zentralen) nach EN 1886 definiert sein.
– Der zulässige Filterleckwert ist gemäß EN 1886 als 0,5% des Nenndurchflusses definiert.
– Für im Freien installierte Zentralen sollten fabrikmäßig montierte Vordächer über jeder Sektion der Zentrale vorhanden sein, eine angemessene Wärmeisolierung bieten, zusätzlich an den Außenverbindungen abgedichtet sein. Antriebe von Absperrklappen sollten im Gerät eingebaut oder vor äußeren Einflüssen geschützt sein. Versorgungsleitungen für Medien zur Zentrale sowie die Kondensatableitungen im Außenbereich sollten vor dem Einfrieren geschützt werden. Zusätzlich müssen Klima- und Lüftungszentralen, die für Installationen bestimmt sind, die Reinräume der Klasse ISO 5 und höher bedienen, folgende Anforderungen erfüllen: Die Produktspezifikation der Zentrale für Räume der Klasse ISO 5 sollte detaillierte Betriebsparameter der darin verwendeten Ventilatoren enthalten. Das Wärmerückgewinnungssystem für Räume der Klasse ISO 5 muss einen Kontakt zwischen den Zuluft- und Abluftströmen ausschließen. Diese umfassenden Anforderungen stellen sicher, dass die Klima- und Lüftungszentralen nicht nur die Luft effizient konditionieren, sondern auch den strengen hygienischen Standards von Reinräumen gerecht werden. Durch die Vermeidung von Kontaminationsquellen, die Gewährleistung einfacher Wartung und Reinigung sowie durch die Nutzung korrosionsbeständiger und leicht zu reinigender Materialien wird das Risiko einer Kreuzkontamination minimiert. Die sorgfältige Planung und Konstruktion der HVAC-Systeme spielen eine entscheidende Rolle bei der Aufrechterhaltung der Reinheit und Sicherheit in kritischen Umgebungen wie Reinräumen, indem sie eine kontrollierte und saubere Arbeitsumgebung schaffen.
Die Gestaltung von HEPA-Filtern für Reinräume muss sicherstellen, dass in der Nähe der Luftfilter die Lufttemperatur über dem Taupunkt liegt, auch während der Stillstandzeiten des Systems. Der Rahmen und die Filterkassetten müssen so konstruiert sein, dass sie kein Wachstum von Mikroorganismen zulassen, eine einfache und sichere Montage ermöglichen und die Dichtigkeit des eingebauten Filters gewährleisten. Direkt nach der Herstellung dürfen die Filter keine Materialfragmente enthalten, die während des Betriebs des Systems freigesetzt werden könnten. Die Filtermaterialien dürfen nicht mit biociden Substanzen imprägniert werden. Die Gehäuse der Filter der ersten und zweiten Stufe sollten aus feuchtigkeitsbeständigen Materialien bestehen, die gegen Verformungen während der Montage und Nutzung beständig sind. Bei der Lieferung sollten die Filter mindestens einer vorläufigen Inspektion unterzogen werden, um Schäden oder Verunreinigungen sowie den Zustand der darauf montierten Dichtungen zu prüfen. Auf dem Filtermaterial sollten keine Verunreinigungen oder Schäden sichtbar sein. Die Filter sollten in sicheren Verpackungen geliefert werden, die das Filtermaterial vor Beschädigungen und die Dichtungen vor Verformungen schützen.
Jede Filtersektion in der Klima- und Lüftungszentrale muss mit einem Druckschalter oder einem Druckwandler ausgestattet sein, um die Verschmutzung des Filters zu überwachen. Es wird empfohlen, dass alle hochwirksamen Filter (oder Filtergruppen an Installationsorten mit identischer hydraulischer und Nutzungseigenschaft), die direkt in den Luftauslässen platziert sind, mit einem Druckschalter oder Druckwandler ausgestattet werden. Diese Geräte müssen mit einem dedizierten Steuerungs- und Automatisierungssystem zusammenarbeiten, das die Lüftungs-, Abluft- und Rezirkulationsinstallationen steuert. Für Anlagen, die Räume der Klasse ISO 8 und höher bedienen, ist zusätzlich eine lokale Ablesung der Druckschaltereinstellung oder des Druckwandlers erforderlich, neben der Anwendung übergeordneter Steuerungssysteme oder des Druckwandlers im BMS-System. Das technische Personal sollte das Datum jedes Filterwechsels dokumentieren, einschließlich Typ und Größe des Filters.
Der Betrieb von Räumen der Klasse ISO 8 und höher mit beschädigten oder undicht montierten HEPA-Filtern kann das Risiko von Infektionen erhöhen und eine direkte Bedrohung für die dort durchgeführten Produktionsprozesse darstellen.
Montage und Austausch der Filter der ersten und zweiten Stufe:
Der Filter der ersten und zweiten Stufe muss ausgetauscht werden, wenn der Luftdruckabfall gleich oder größer als der vom Hersteller empfohlene Maximalwert ist. Es muss eine dichte Verbindung zwischen dem Filterrahmen und dem Gehäuse der Zentrale sichergestellt werden. Zum Abdichten wird die Verwendung von undurchsichtigen Dichtungsmaterialien oder vorgefertigten Dichtungen aus geschlossenzelligem Material empfohlen, die für Installationen mit erhöhten hygienischen Anforderungen zugelassen sind. Der erste Filterwechsel in der Klima- und Lüftungszentrale sollte nach dem ersten Start der Anlage und nach Durchführung der Abnahmemessungen erfolgen. Der Filterwechsel sollte von der schmutzigen Seite her erfolgen.
Montage und Austausch der HEPA-Filter:
HEPA-Filter sollten zusammen mit einem Qualitätszertifikat geliefert werden. Es wird empfohlen, die Filter bis zu ihrer Montage in sicheren Verpackungen aufzubewahren. Es muss unbedingt sichergestellt werden, dass es zu keinen Leckagen an den HEPA-Filtern kommt. Mögliche Leckagearten umfassen: Leckagen am Filter selbst, Leckagen an der Verbindung zwischen dem Filterrahmen und dem konstruktiven Element des Luftauslasses, Leckagen zwischen dem Filterrahmen und dem Filtermaterial, Leckagen zwischen dem Filterrahmen und dem Lüftungskanal. Es muss eine dichte Verbindung zwischen dem Filterrahmen und dem Gehäuse des Luftauslasses gewährleistet werden. Zum Abdichten wird die Verwendung von vorgefertigten Dichtungen aus geschlossenzelligem Material empfohlen, die feuchtigkeits- und schimmelresistent sind und für den Einsatz in Reinräumen vorgesehen sind. In besonderen Fällen ist die Verwendung von undurchsichtigen Dichtungsmaterialien zulässig, sofern sie für die Verwendung in Reinräumen zugelassen und geeignet sind. Der Austausch des HEPA-Filters kann von der Seite des Reinraums aus erfolgen.
Um die Betriebsbereitschaft von Räumen der Klasse ISO 8 und höher nach jedem Austausch der HEPA-Filter zu bestätigen, sollten folgende Tests durchgeführt werden (entsprechend der Methodik gemäß DIN 14644-3):
– Durchführung eines Tests zur Staubreinheit der Luft (Raumvalidierung),
– Überprüfung der Dichtigkeit und Integrität der Hochleistungsfilter (Bewertung der Gleichmäßigkeit des Filtermaterials),
– Messung der Luftdruckkaskade zwischen den Räumen,
– Messung des Luftdruckabfalls am Hochleistungsfilter.
Für Räume der Klasse ISO 8 wird nach jedem Austausch der HEPA-Filter zusätzlich eine Messung der mikrobiologischen Luftreinheit empfohlen. Ein negatives Testergebnis kann (muss aber nicht) auf Unregelmäßigkeiten im Betrieb der Lüftungsanlage hinweisen. Nach der Installation der Hochleistungsfilter in den Luftauslässen der Räume der Klasse ISO 8, 7, 6, 5 sollte ein Test zur Überprüfung der Dichtigkeit und Integrität der Hochleistungsfilter durchgeführt werden, um eventuelle Beschädigungen während der Montage und die korrekte Montage zu bewerten. Die empfohlene Betriebsdauer eines HEPA-Filters beträgt 2 Jahre, kann jedoch auf bis zu 4 Jahre verlängert werden, vorausgesetzt, dass jährlich (nach Ablauf der erwähnten 2 Jahre) folgende Tests und Messungen durchgeführt werden (entsprechend der in EN DIN 14644-3 beschriebenen Methodik):
– Überprüfung der Dichtigkeit und Integrität der Hochleistungsfilter (Bewertung der Gleichmäßigkeit des Filtermaterials),
– Messung der Luftdruckkaskade zwischen den Räumen,
– Messung des Luftdruckabfalls am Filter.
Diese regelmäßigen Überprüfungen und der ordnungsgemäße Austausch von Filtern sind entscheidend, um die kontinuierliche Wirksamkeit der Luftreinigung in Reinräumen zu gewährleisten und um sicherzustellen, dass die Produktionsprozesse in diesen Räumen nicht durch Verunreinigungen gefährdet werden.
Zu- und Abluftventilatoren spielen eine entscheidende Rolle in der Gestaltung von Lüftungssystemen für Reinräume. Sie tragen wesentlich zur Aufrechterhaltung der erforderlichen Luftreinheit und zum Druckniveau bei, das für die Klassifizierung von Reinräumen nach ISO 8 und höher erforderlich ist. Die sorgfältige Auswahl und Platzierung dieser Ventilatoren gewährleisten eine kontinuierliche und effiziente Filtration sowie einen angemessenen Luftaustausch, der entscheidend ist, um die Integrität des Reinraums zu bewahren.
Die Platzierung der Zuluftventilatoren zwischen dem ersten und zweiten Filterstadium und der Abluftventilatoren hinter dem Filterabschnitt im Abluftteil der Klimazentrale gewährleistet einen einheitlichen und kontrollierten Luftstrom durch den Reinraum. Dies ist besonders wichtig, um ein konstantes Überdruckniveau zu erreichen und einen stabilen laminaren Luftstrom während des gesamten Betriebs des Filtersystems aufrechtzuerhalten, von den anfänglichen Widerstandswerten über die zunehmende Filterverschmutzung bis hin zu einem Zustand, der eine Gefahr für den Verlust des Überdrucks darstellt.
Für die Berechnung des verfügbaren Drucks wird empfohlen, den maximal zulässigen Druckabfall über den Filtern der ersten und zweiten Stufe, den der Hersteller angibt, sowie für den dritten Filterstadium den Anfangswiderstand zuzüglich mindestens 200% (für den angenommenen Luftstrom) anzunehmen. Diese Empfehlung sollte ebenfalls für Räume der Klasse ISO 9 berücksichtigt werden.
Der Planer sollte in der Entwurfsphase die Widerstände der Anlage berechnen, die Ventilatoren (ihre Kapazität und den verfügbaren Druck) auswählen und die Charakteristik der Anlage auf die Charakteristik des ausgewählten Ventilators abbilden. Dabei sollten die Betriebspunkte des Zuluftventilators in vier Phasen gekennzeichnet werden:
– Anfangsphase: bei den anfänglichen Durchflusswiderständen der Filter der ersten, zweiten und dritten Stufe,
– Nennphase: bei den Widerständen der Filter der ersten und zweiten Stufe, die zwischen dem Anfangswert und dem zulässigen Enddruckabfall liegen, und bei den Widerständen der dritten Filterstufe, die einem 100%igen Druckanstieg im Vergleich zu den Anfangswiderständen entsprechen,
– Endphase: bei den angenommenen maximalen Widerständen der Filter der ersten und zweiten Stufe und den Widerständen der dritten Filterstufe, die einem 200%igen Druckanstieg im Vergleich zu den Anfangswiderständen entsprechen (bei maximaler Betriebsfrequenz des Ventilators und vollständiger Öffnung der Durchflussregler),
– Modus mit reduziertem Durchfluss (sog. Nachtmodus – wenn der Reinraum betriebsbereit ist und keine Produktionsprozesse stattfinden) bei den Widerständen der Filter der ersten und zweiten Stufe, die zwischen dem Anfangswert und dem Enddruckabfall liegen, und den Widerständen der dritten Filterstufe, die einem 100%igen Druckanstieg im Vergleich zu den Anfangswiderständen entsprechen.
Obwohl diese Empfehlung nicht verpflichtend ist, bestätigt sie die guten Planungspraktiken bei der Herausforderung, ein Lüftungssystem für Reinräume zu entwerfen. Die Nichtbeachtung dieser Empfehlung kann zu Ansprüchen des Investors und/oder Nutzers führen, insbesondere wenn dies zu einer überdurchschnittlichen Zunahme der Filterwechselhäufigkeit, zu erhöhten Betriebskosten und zum Nichterreichen der erwarteten Mikroklimaparameter in den Reinräumen führt.
Bei der Auswahl des Ventilators sollte der Planer die gewählte Dichtheitsklasse der Kanäle berücksichtigen und einen Leistungsüberschuss des Ventilators für eventuelle Montagefehler während der Ausführungsphase einplanen.
Die Gestaltung von Lüftungskanälen für Reinräume sollte immer die kürzestmögliche Leitungsführung berücksichtigen. Dies ist besonders wichtig für Anlagen, die Reinräume der Klasse ISO 8, ISO 7 und ISO 5 bedienen.
Materialien und Oberflächen
Lüftungskanäle in allen Bereichen der Luftverteilung sollten aus Materialien gefertigt sein, die:
– keine schädlichen Substanzen, Fasern oder Gerüche an die zugeführte Luft oder an die Räume abgeben,
– kein Nährboden für Mikroorganismen sind oder deren Wachstum fördern,
– keine Ansammlung von Verunreinigungen begünstigen.
Für die Herstellung von Lüftungskanälen wird der Einsatz von verzinktem Stahlblech empfohlen, gemäß den Normen EN 1505 für rechteckige Querschnitte und EN 1506 für runde Querschnitte. Der Einsatz von flexiblen Kanälen (z.B. Flex-Typ) ist für die Anbindung von Zu- und Abluftgeräten in Reinräumen der Klasse ISO 6 und ISO 5 nicht zulässig. In allen Hauptkanälen, an ihren Abzweigungen sowie in der Nähe von kanalintegrierten Temperatur- und Feuchtigkeitssensoren sollten Messöffnungen vorgesehen werden, die für Leistungsmessungen und Kalibrierungen der Sensoren vorgesehen sind. Messöffnungen sollten mit weichen, dichten Verschlussstopfen gesichert sein.
Dichtheit der Kanäle
Lüftungskanäle müssen die Dichtheits- und Festigkeitsanforderungen gemäß den Normen EN 1507 für rechteckige Querschnitte und EN 12237 für runde Querschnitte erfüllen. Für Anlagen mit HEPA-Filtern wird empfohlen, das Kanalnetz unter Berücksichtigung der Dichtheitsklasse C gemäß den Normen EN 1507 und EN 12237 zu entwerfen, wobei ein Testüberdruck von 1000 Pa angenommen wird. In besonderen, begründeten Fällen kann die Dichtheitsklasse der Kanäle auf Klasse B gemäß EN 1507 und EN 12237 reduziert werden. Für Anlagen ohne HEPA-Filter wird empfohlen, das Kanalnetz unter Berücksichtigung der Dichtheitsklasse B zu entwerfen. Die Dichtheitsklasse der Kanäle sollte im Entwurf des Lüftungs- und Klimasystems eindeutig festgelegt werden. Fehlt eine solche Spezifikation, sollte standardmäßig für Anlagen mit HEPA-Filtern die Dichtheitsklasse C und für Anlagen ohne HEPA-Filter die Klasse B angenommen werden.
Die für die Dichtheitstests ausgewählten Kanalabschnitte sollten vertraglich zwischen dem Auftragnehmer und dem Investor festgelegt werden. Fehlen entsprechende Vereinbarungen, sollten willkürlich vom Investor ausgewählte Abschnitte, die mindestens 50% der Oberfläche der Zuluftkanäle mit Hochleistungsfiltern und mindestens 30% der Oberfläche der Zuluftkanäle ohne HEPA-Filter abdecken, getestet werden. Bei festgestellten Undichtigkeiten in den Testabschnitten sollte eine Überprüfung des gesamten Kanalnetzes durchgeführt werden.
Bei Umluftsystemen sollten die Dichtheitstests gemäß den für Zuluftanlagen festgelegten Prinzipien durchgeführt werden, wobei die Umluftanlage als separate Anlage behandelt und mindestens 30% der Oberfläche der Lüftungskanäle getestet werden sollte. Die Dichtheitsklasse der Anlage sollte durch Dichtheitstests bestätigt werden. Die Durchführung der Dichtheitstests der Lüftungsanlage sollte kommissioniert werden. Die Dichtheit der Kanäle sollte durch ein entsprechendes Protokoll bestätigt werden, das von allen Mitgliedern der Kommission unterzeichnet und der Ausführungsdokumentation beigefügt wird. Sollte die erforderliche Dichtheitsklasse der Lüftungskanäle nicht erreicht werden, müssen Nachbesserungen an der Anlage vorgenommen und die Dichtheitstests erneut durchgeführt werden, um die Einhaltung der spezifizierten Anforderungen sicherzustellen.
Es ist wesentlich, dass die Ergebnisse dieser Tests und alle Maßnahmen, die zur Behebung von Undichtigkeiten ergriffen wurden, sorgfältig dokumentiert werden. Diese Dokumentation dient nicht nur als Nachweis der Konformität mit den festgelegten Anforderungen, sondern auch als wichtige Informationsquelle für zukünftige Wartungs- und Instandhaltungsarbeiten. Die genaue Kenntnis der Zustände der Lüftungskanäle kann wesentlich zur effizienten Planung von Reinigungs- und Wartungsarbeiten beitragen und hilft dabei, potenzielle Probleme frühzeitig zu erkennen und zu beheben.
Zusätzlich zu den Dichtheitstests sollte besonderes Augenmerk auf die regelmäßige Inspektion und Wartung der Lüftungskanäle gelegt werden, um sicherzustellen, dass sie frei von Verunreinigungen sind und die Luftqualität in den Reinräumen nicht beeinträchtigen. Insbesondere in hochsensiblen Bereichen wie ISO 5 oder ISO 7 Reinräumen kann die Ansammlung von Staub oder anderen Partikeln in den Lüftungskanälen die Wirksamkeit der Luftfiltration beeinträchtigen und das Risiko einer Kontamination erhöhen.
Die Auswahl der Materialien für die Lüftungskanäle, ihre Konstruktion und die Sorgfalt bei der Installation sind somit entscheidend für die langfristige Aufrechterhaltung der Reinraumstandards. Eine gründliche Planung und Ausführung, zusammen mit einem kontinuierlichen Überwachungs- und Wartungsprogramm, sind der Schlüssel zur Gewährleistung einer zuverlässigen und effizienten Lüftungsleistung in Reinräumen.