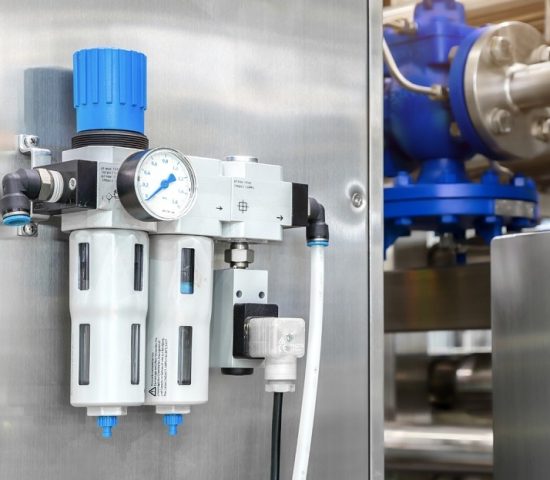
DRUCKLUFTKLASSEN
ISO 8573-1
Wir sind ein Labor, das Reinheitsklassenprüfungen von Druckluft gemäß ISO 8573-1:2010 durchführt. Wir untersuchen Druckluft in Bezug auf folgende Parameter:
- Partikelgehalt (ISO 8573-4),
- Wassergehalt / Drucktaupunkt (ISO 8573-3),
- Öl-Aerosol-Gehalt (ISO 8573-2),
- Gehalt an Bakterien, Hefen und Schimmelpilzen (ISO 8573-7).
Die Messungen führen wir an folgenden Tagen durch: Donnerstag-Freitag (in ganz Deutschland)
Die Zeit, die für die Messungen an einem Messpunkt benötigt wird: 40-60 Minuten
Anfragen und Bestellungen: labor@qualifizierung-validierung.de
ISO 8573-1:2010 ist eine weithin anerkannte Norm zur Klassifizierung von Druckluft aufgrund des Gehalts an drei Verunreinigungen: Partikel, Wasser und Öl. Probenahmemethoden und die Messungen selbst werden in den nachfolgenden Abschnitten der ISO-Norm 8573 (-2, -3, -4) ausführlich beschrieben. Ihre Anwendung ist obligatorisch, wenn die erzielten Messergebnisse mit den in der ISO 8573-1 beschriebenen Reinheitsklassen für Druckluft verglichen werden sollen. In einigen Branchen wird die Druckluft auch in Bezug auf mikrobiologische Verunreinigungen geprüft, wobei diese Prüfungen nicht die Grundlage für die Klassifizierung der Druckluftreinheit nach ISO 8573-1 bilden, sondern ergänzen sie nur.
Probenahmestellen zur Druckluftklassifizierung (ISO 8573-1)
Reinheitsprüfungen der Druckluft werden in der Regel für solche Teile der Anlage durchgeführt, in denen die Druckluft:
– direkt mit dem Produkt/Material in Berührung kommt (Lebensmittel, Kosmetika, Arzneimittel, Medizinprodukte [eng. medical devices]),
– mit kontaminationsempfindlichen Geräten (Laborgeräte, optische Systeme, Laser) verbunden ist,
– in die Umwelt freigesetzt wird und zur Steigerung der Partikelzahl im Reinraum [eng. cleanroom] beiträgt.
Die Klassifizierung der Druckluftreinheit erfolgt üblicherweise an Messstellen, die sich in den letzten Abschnitten des Druckluftverteilungssystems befinden. Manchmal werden zusätzliche Proben im Kompressorraum entnommen, jedoch immer nach der Druckluftaufbereitungsanlage (nach den Filtern). Durch die Prüfung der Druckluft an 3-4 Messstellen kann in der Regel bereits eine zuverlässige Beurteilung der Druckluftreinheit vorgenommen werden. Zur Prüfung von Druckluft nach ISO 8573-1 ist der Anschluss an ein Drucksystem erforderlich. Es ist nicht möglich, die Reinheit des in die Umgebung abgegebenen Gases zu überprüfen (siehe unten erforderliche Anschlussarten auf der Anlagenseite).
Druckluftklassen: Gehalt an Partikeln
Die Messung der Partikelanzahl erfolgt mit einem tragbaren Laserpartikelzähler, der Partikel bis zu einer Größe von 0,1 µm gleichzeitig in vier Größenbereichen messen kann: 0,1 – 0,5 µm, 0,5 – 1,0 µm, 1,0 – 5,0 µm und >5,0 µm. Damit ist es unter anderem möglich, die Reinheitsklasse der Druckluft nach den Anforderungen der ISO 8573-1 zu bestimmen sowie die Messergebnisse mit den Anforderungen von GMP, ISO 14644-1 oder SEMI 49.8 in Beziehung zu setzen. Die ISO 8573-4:2019 beschreibt die Messmethodik im Detail – die Ausrüstung für die Probenahme, die Parameter für die eigentliche Messung.
Die ISO 8573-1:2010 definiert verschiedene Reinheitsklassen für Druckluft basierend auf der maximalen Anzahl von Partikeln pro Kubikmeter Luft in drei Größenbereichen:
ISO 8573-1:2010 Klasse 1: Die strengsten Anforderungen mit maximal 20.000 Partikeln (0,1-0,5 µm), 400 Partikeln (0,5-1,0 µm) und 10 Partikeln (1,0-5,0 µm) pro m³.
ISO 8573-1:2010 Klasse 2: Erlaubt bis zu 400.000 Partikel (0,1-0,5 µm), 6.000 Partikel (0,5-1,0 µm) und 100 Partikel (1,0-5,0 µm) pro m³.
ISO 8573-1:2010 Klasse 3: Definiert nur Grenzen für größere Partikel mit maximal 90.000 Partikeln (0,5-1,0 µm) und 1.000 Partikeln (1,0-5,0 µm) pro m³.
ISO 8573-1:2010 Klasse 4: Setzt eine Obergrenze von 10.000 Partikeln für die Größe 1,0-5,0 µm fest.
ISO 8573-1:2010 Klasse 5: Erlaubt bis zu 100.000 Partikel in der Größe 1,0-5,0 µm.
ISO 8573-1:2010 Klasse X: Bezeichnet Druckluft, die die Grenzwerte der Klasse 5 überschreitet und somit eine kundenspezifische Vereinbarung erfordert.
Druckluftklassen: Wassergehalt (Drucktaupunkt)
Der Drucktaupunkt (°C) informiert über den Feuchtigkeitsgehalt der Druckluft und wird aus der relativen Luftfeuchtigkeit, der Temperatur und dem Betriebsdruck an der Druckluftentnahmestelle bestimmt. Die Messung des Drucktaupunktes erfolgt mit einem tragbaren Gerät, das an die Druckanlage angeschlossen wird (2-8 bar). Je niedriger der Drucktaupunkt Wert ist, desto weniger Wasser enthält die Druckluft und desto niedriger ist die Druckluftklassennummer.
ISO 8573-1 definiert Akzeptanzkriterien für die Feuchtigkeit einzelner Druckluftklassen auf der Basis des Parameters Drucktaupunkt:
ISO 8573-1:2010 Klasse 1: Der strengste Standard mit einem Drucktaupunkt von ≤ -70°C.
ISO 8573-1:2010 Klasse 2: Erfordert einen Drucktaupunkt von ≤ -40°C.
ISO 8573-1:2010 Klasse 3: Setzt einen Drucktaupunkt von ≤ -20°C fest.
ISO 8573-1:2010 Klasse 4: Verlangt einen Drucktaupunkt von ≤ +3°C.
ISO 8573-1:2010 Klasse 5: Erlaubt einen Drucktaupunkt von ≤ +7°C.
ISO 8573-1:2010 Klasse 6: Definiert einen Drucktaupunkt von ≤ +10°C.
Druckluftklassen: Gehalt an Ölaerosolen
Die Bestimmung des Ölgehalts der Druckluft ist aus analytischer Sicht ein recht komplexes Problem. Die ISO 8573-1 besagt, dass der Gesamtölgehalt der Druckluft aus Öl in flüssiger Form, Öl in Aerosolform und Öldampf zusammengesetzt ist. Um die sogenannte Reinheitsklasse der Druckluft in Bezug auf den Ölgehalt zu bestimmen, sollte der Gesamtölgehalt, der sich aus der Summe der aufgeführten Ölfraktionen ergibt, berücksichtigt werden. Da das Öl in Aerosolform den größten Teil des Ölgehalts in Druckluftfiltern (grob, fein, extrafein/Kohle) ausmacht, ist es üblich, den Aerosolgehalt des Öls bei der Reinheitsüberwachung der Druckluft zu messen.
In unserem Unternehmen verwenden wir ein Probenahmesystem nach ISO-Methode 8573-2 Punkt B1 – das Ölaerosol wird auf einen Glasfaserfilter gesaugt und anschließend im Labor mittels FTIR-Technik untersucht. Die niedrige Ölbestimmungsgrenze dieser Methode ermöglicht die Beurteilung der Druckluftreinheit auch dann, wenn die Druckluftreinheitsklasse 1 nach ISO 8573-1 zu erwarten ist.
Ölgehalt-Anforderungen für Druckluft-Reinheitsklassen nach ISO 8573-1:2010:
ISO 8573-1:2010 Klasse 1: Die strengste Anforderung mit einem maximalen Ölgehalt von ≤ 0,01 mg/m³.
ISO 8573-1:2010 Klasse 2: Erlaubt einen Ölgehalt von ≤ 0,1 mg/m³.
ISO 8573-1:2010 Klasse 3: Setzt eine Obergrenze von ≤ 1 mg/m³ fest.
ISO 8573-1:2010 Klasse 4: Definiert einen maximal zulässigen Ölgehalt von ≤ 5 mg/m³.
ISO 8573-1:2010 Klasse X: Bezeichnet Druckluft mit einem Ölgehalt von > 5 mg/m³. In diesem Fall ist eine kundenspezifische Vereinbarung erforderlich, da der Ölgehalt die Grenzwerte der vordefinierten Klassen überschreitet.
Druckluftklassifizierung – Akzeptanzkriterien
Die ISO 8573 Normenreihe dient lediglich der Festlegung von Reinheitsklassen für Druckluft und enthält keine Grenzwerte (Akzeptanzkriterien) für bestimmte Branchen, die Druckluft verwenden. In der ISO 8573 Normenreihe befinden sich auch keine Grenzwerte für bestimmte Anwendungen oder Prozessbedingungen innerhalb einer Branche. Grundlegende Richtlinien in dieser Hinsicht wurden von FDA, VDMA, BCAS und BRC veröffentlicht. In den meisten Fällen (Lebensmittel, Kosmetik, Pharmazie, Laserschneiden, Elektronikfertigung, Lackierereien, Pulverbeschichtung) werden Reinheitsklassen der Druckluft (bezogen auf den Partikelgehalt) von 1 bis 4 nach ISO 8573-1 erwartet, bei kritischen Anwendungen die Klasse 1 oder 2. In vielen Fällen wird die Druckluft jedoch für typische technische Anwendungen eingesetzt – sie dient zur Steuerung von Ventilen, Stellantrieben und Greifern. In solchen Anwendungen sollten Verunreinigungen aus der Druckluft entfernt werden, um die pneumatischen Komponenten vor Korrosion und übermäßigem Verschleiß zu schützen. Die Klasse 3 oder 4 nach ISO 8573-1 ist hier in der Regel ausreichend.
ISO 8573-1: Grenzwerte
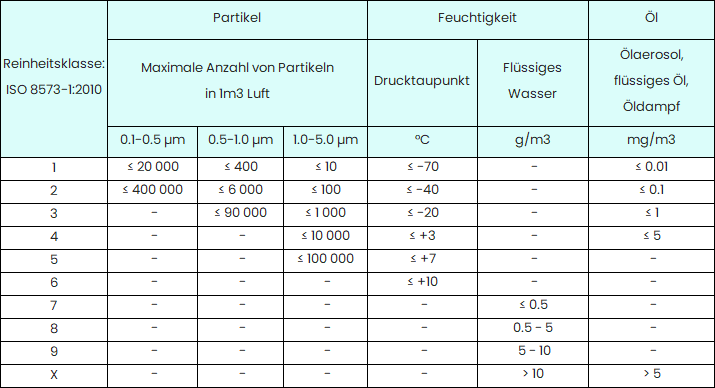
GEPRÜFTE PARAMETER
PARTIKEL
Messmethode: ISO 8573-4:2019
Messbereich: Messung von Partikeln im Bereich 0,1 - 0,5 µm (Klassen 1-7 nach ISO 8573-1)
Messausrüstung: Laser-Partikelzähler
WASSER
Messmethode: ISO 8573-3:2010
Messbereich: –70 … +30°C td
Messunsicherheit: ±2°C
Messausrüstung: Drucktaupunktmessgerät
ÖL-AEROSOL
Messmethode: ISO 8573-2:2007
Messbereich: 0,003 – 2mg/1m3
Messunsicherheit: ±10%
Messausrüstung: Filtrationskit, FTIR
MIKROBIOLOGIE
Messmethode: ISO 8573-7:2003
Geprüfte Parameter: Gehalt an Bakterien, Hefen, Schimmelpilzen in 1 m3 Luft
Messausrüstung: Druckluftprüfgerät, Anzucht der Kolonien in Petrischalen
TECHNISCHE ANFORDERUNEN
ÜBERPRÜFEN SIE, BEVOR SIE EINE BESTELLUNG AUFGEBEN
KUNDENSEITIGE ANSCHLÜSSE
Schnellkupplung DN 7.2
Gewindekupplung 1/2' oder 3/8' (Innengewinde)
Leitung 6, 8, 10, 12 oder 16mm (Außendurchmesser)
ANLAGEDRUCK
Maximal 7,3 bar
UMGEBUNGSTEMPERATUR
Minimum 10°C
LAGE DER MESSSTELLE
1 Gereinigte Druckluft
Die Partikelzahl kann nur in Gas gemessen werden, das auf den Filtern gereinigt wurde. Es ist nicht möglich, vor den Filtern zu messen.
2. Leicht zugänglicher Raum
Die Messgeräte sind stoßempfindlich und wiegen mehr als 20 kg, weshalb sie z. B. nicht auf einer Leiter, auf Tanks usw. getragen werden dürfen.
ZEIT DER PROBENAHME
Die Durchführung der Testreihe an einer Messstelle dauert etwa 45-60 Minuten.
BERICHTERSTATTUNG
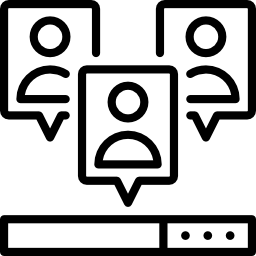
AUF DEUTSCH
UND ENGLISCH
Standardmäßig erstellen wir den Bericht in einer zweisprachigen Version: Deutsch-Englisch.
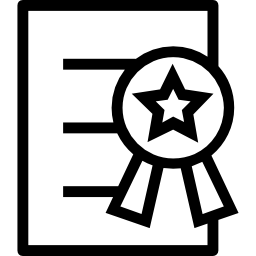
IM EINKLANG MIT DEN
GMP-GRUNDSÄTZEN
Der Bericht enthält u. a. die Angaben zu den verwendeten Geräten und der an den Prüfungen beteiligten Personen.
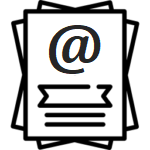
ELEKTRONISCHE
ÜBERMITTLUNG
Der Bericht wird in elektronischer Form
(PDF-Dokument) übermittelt.
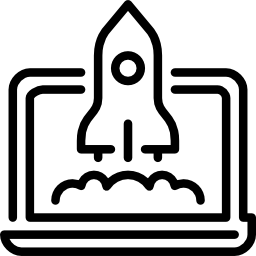
IN DER REGEL INNERHALB
VON 14-21 TAGEN FERTIG
In der Regel wird der Bericht innerhalb von 14 Tagen
(maximal 21 Tagen) nach der Messung übermittelt.
DIESE KUNDEN HABEN UNS BEREITS VERTRAUT
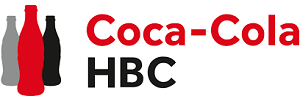
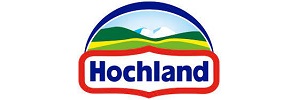
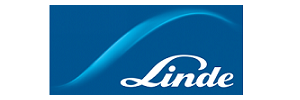
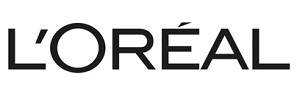
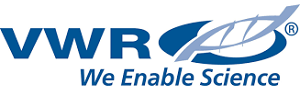
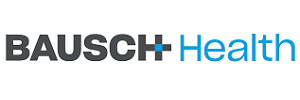
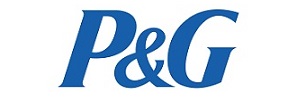
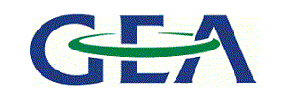
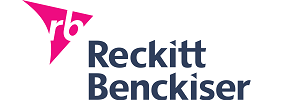
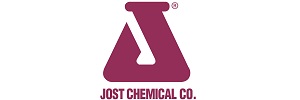
PREISLISTE
Möchten Sie schnell die Kosten für die Durchführung von Messungen abschätzen?
In der Preisliste finden Sie:
– Informationen über die von uns durchgeführten Messungen
– Preise der Untersuchungen
EIN GENAUES ANGEBOT ANFORDERN
Druckluftqualitätsklassen nach ISO 8573-1 für verschiedene industrielle Anwendungen
Druckluft spielt eine Schlüsselrolle in vielen industriellen Anwendungen, daher ist es wichtig sicherzustellen, dass sie die erforderlichen Reinheitsstandards erfüllt. Im folgenden Artikel betrachten wir verschiedene Druckluftklassen und ihre Bedeutung für spezifische industrielle Anwendungen.
ISO 8573-1: Druckluft Reinheitsklassen und ihre Anwendungen
Mischluft: Diese Anwendung erfordert eine Druckluft Qualitätsklasse 3-5-1. Das bedeutet, dass sie Partikel bis zu 5 μm enthalten darf, auf -7°C Drucktaupunkt gekühlt sein muss und bis zu 1,0 mg/m³ Öl enthalten darf.
Lackierluft: Die Reinheitsklasse Druckluft ist hier 2-4-1, was Partikel bis 1 μm, Kühlung auf -40°C Drucktaupunkt und einen Ölgehalt bis 1,0 mg/m³ bedeutet.
Schwere pneumatische Motoren: Für diese Anwendung ist die Druckluftklasse 4-5-3 geeignet, mit Partikeln bis 5 μm, Kühlung auf -20°C Drucktaupunkt und einem Ölgehalt bis 15 mg/m³.
Spritzpistolen, Lackieranwendungen: Die Druckluft Qualitätsklasse 2-4-1 ist ideal, mit Partikeln bis 1 μm, Kühlung auf -40°C Drucktaupunkt und einem Ölgehalt bis 1,0 mg/m³.
Verpackungsmaschinen: Für diese Maschinen ist die Reinheitsklasse Druckluft 1-4-1 geeignet, mit Partikeln bis 1 μm, Kühlung auf -40°C Drucktaupunkt und einem Ölgehalt bis 1,0 mg/m³.
Werkstattluft, allgemein: Hier wird die Druckluftklasse 3-6-5 gefordert, mit Partikeln bis 15 μm, Kühlung auf -20°C Drucktaupunkt und einem Ölgehalt bis 25 mg/m³.
Baugewerbe: Klasse 4 mit einem Partikelgehalt von 5 μm, einem Drucktaupunkt von +3°C und einem Ölgehalt von 5,0 mg/m³.
Transport von Holzmaterialien: Klasse 3 hat einen Partikelgehalt von 5 μm, einen Drucktaupunkt von +7°C und einen Ölgehalt von 1,0 mg/m³.
Verpackung von Lebensmitteln und Getränken: Klasse 1 zeichnet sich durch einen Partikelgehalt von 0,1 μm, einen Drucktaupunkt von -70°C und einen Ölgehalt von 0,01 mg/m³ aus.
Viele weitere Anwendungen haben ihre eigenen Spezifikationen bezüglich der Druckluft Reinheitsklassen.
Fallbeispiel: Prüfung von Druckluftklassen nach ISO 8573-1
ISO 8573-1 Messergebnisse (reale Fälle; verschiedene Druckluftsysteme):
Anforderungen für Druckluft der Reinheitsklasse 1:1:1 gemäß ISO 8573-1
Hier ist eine detaillierte Beschreibung der Anforderungen, Erreichungsmethoden und Anwendungsbereiche für Druckluft der Reinheitsklasse 1:1:1 gemäß ISO 8573-1:
Anforderungen für Druckluft der Reinheitsklasse 1:1:1 gemäß ISO 8573-1
Eine Druckluft der Reinheitsklasse 1:1:1 muss folgende Kriterien erfüllen:
1. Partikel (1): Maximal 20.000 Partikel pro m³ für Partikelgrößen von 0,1-0,5 µm, maximal 400 Partikel pro m³ für 0,5-1 µm und maximal 10 Partikel pro m³ für 1-5 µm.
2. Feuchtigkeit (1): Der Drucktaupunkt muss bei ≤ -70°C liegen.
3. Öl (1): Der Gesamtölgehalt (flüssig, Aerosol und Dampf) darf 0,01 mg/m³ nicht überschreiten.
Erreichung der Reinheitsklasse 1:1:1
Um diese höchste Reinheitsklasse zu erreichen, sind mehrere Aufbereitungsstufen erforderlich:
1. Hocheffiziente Kompressoren, vorzugsweise ölfrei.
2. Mehrstufige Filtration:
– Vorfilter zur Entfernung grober Partikel
– Feinfilter für kleinere Partikel
– Aktivkohlefilter zur Ölentfernung
3. Kältetrockner gefolgt von einem Adsorptionstrockner für extrem niedrige Drucktaupunkte.
4. Sterilfilter als letzte Stufe zur Entfernung feinster Partikel.
5. Regelmäßige Wartung und Überwachung des Systems.
Anwendungsbereiche für Druckluft der Reinheitsklasse 1:1:1
Diese extrem reine Druckluft wird in sensiblen Industriezweigen benötigt, wie zum Beispiel:
1. Pharmazeutische Industrie: Für die Herstellung von Medikamenten und Impfstoffen.
2. Halbleiterindustrie: Bei der Produktion von Mikrochips und elektronischen Bauteilen.
3. Optische Industrie: Für die Herstellung von Präzisionslinsen und -spiegeln.
4. Lebensmittel- und Getränkeindustrie: Bei besonders sensiblen Verpackungsprozessen.
5. Medizintechnik: Für die Produktion von Implantaten und sterilen medizinischen Geräten.
6. Luft- und Raumfahrtindustrie: Bei der Fertigung hochsensibler Komponenten.
7. Forschungslabore: Für Experimente, die eine extrem saubere Umgebung erfordern.
In diesen Bereichen kann selbst die geringste Verunreinigung zu schwerwiegenden Qualitätsproblemen oder Gesundheitsrisiken führen, weshalb die höchste Reinheitsklasse 1:1:1 unerlässlich ist.
Anforderungen für Druckluft der Reinheitsklasse 2:1:1 gemäß ISO 8573-1
Gerne, hier ist eine detaillierte Beschreibung der Druckluft-Reinheitsklasse 2:1:1 gemäß ISO 8573-1:
Anforderungen für Druckluft der Reinheitsklasse 2:1:1 gemäß ISO 8573-1
Eine Druckluft der Reinheitsklasse 2:1:1 muss folgende Kriterien erfüllen:
1. Partikel (2): Maximal 400.000 Partikel pro m³ für Partikelgrößen von 0,1-0,5 µm, maximal 6.000 Partikel pro m³ für 0,5-1 µm und maximal 100 Partikel pro m³ für 1-5 µm.
2. Feuchtigkeit (1): Der Drucktaupunkt muss bei ≤ -70°C liegen.
3. Öl (1): Der Gesamtölgehalt (flüssig, Aerosol und Dampf) darf 0,01 mg/m³ nicht überschreiten.
Erreichung der Reinheitsklasse 2:1:1
Um diese sehr hohe Reinheitsklasse zu erreichen, sind folgende Maßnahmen erforderlich:
1. Einsatz von hochwertigen, vorzugsweise ölfreien Kompressoren.
2. Mehrstufige Filtration:
– Feinfilter zur Entfernung von Partikeln
– Submikrofilter für kleinste Partikel
– Aktivkohlefilter zur Ölentfernung
3. Adsorptionstrockner für sehr niedrige Drucktaupunkte.
4. Regelmäßige Wartung und Überwachung des Systems.
Anwendungsbereiche für Druckluft der Reinheitsklasse 2:1:1
Diese sehr reine Druckluft wird in verschiedenen anspruchsvollen Industriezweigen benötigt, wie zum Beispiel:
1. Lebensmittelindustrie: Für direkte Produktkontakte und kritische Verpackungsprozesse.
2. Pharmaindustrie: Für weniger kritische Prozesse als Klasse 1:1:1, aber immer noch mit hohen Reinheitsanforderungen.
3. Chemische Industrie: Für sensible Produktionsprozesse.
4. Elektronikindustrie: Für die Herstellung von empfindlichen elektronischen Bauteilen.
5. Automobilindustrie: Für Lackierprozesse und die Herstellung von Präzisionsteilen.
6. Medizintechnik: Für die Produktion von medizinischen Geräten, die nicht direkt in den Körper eingeführt werden.
7. Textilindustrie: Für hochwertige Textilproduktionsprozesse.
Unterschied zur Klasse 1:1:1
Der Hauptunterschied zur Klasse 1:1:1 liegt in den Anforderungen an den Partikelgehalt. Während die Feuchtigkeits- und Ölgehaltsanforderungen identisch sind, erlaubt die Klasse 2:1:1 eine höhere Anzahl von Partikeln. Dies macht die Erreichung dieser Klasse etwas weniger aufwendig, bietet aber immer noch ein sehr hohes Maß an Reinheit, das für viele kritische Anwendungen ausreichend ist.
Die Wahl zwischen Klasse 1:1:1 und 2:1:1 hängt von den spezifischen Anforderungen des jeweiligen Produktionsprozesses ab und sollte sorgfältig unter Berücksichtigung der Kosten-Nutzen-Relation getroffen werden.
Anforderungen für Druckluft der Reinheitsklasse 1:4:1 gemäß ISO 8573-1
Gerne, hier ist eine detaillierte Beschreibung der Druckluft-Reinheitsklasse 1:4:1 gemäß ISO 8573-1:
Anforderungen für Druckluft der Reinheitsklasse 1:4:1 gemäß ISO 8573-1
Eine Druckluft der Reinheitsklasse 1:4:1 muss folgende Kriterien erfüllen:
1. Partikel (1): Maximal 20.000 Partikel pro m³ für Partikelgrößen von 0,1-0,5 µm, maximal 400 Partikel pro m³ für 0,5-1 µm und maximal 10 Partikel pro m³ für 1-5 µm.
2. Feuchtigkeit (4): Der Drucktaupunkt muss bei ≤ +3°C liegen.
3. Öl (1): Der Gesamtölgehalt (flüssig, Aerosol und Dampf) darf 0,01 mg/m³ nicht überschreiten.
Erreichung der Reinheitsklasse 1:4:1
Um diese Reinheitsklasse zu erreichen, sind folgende Maßnahmen erforderlich:
1. Einsatz von hochwertigen Kompressoren, vorzugsweise ölfrei.
2. Mehrstufige Filtration:
– Hochleistungsfeinfilter zur Entfernung von Partikeln
– Submikrofilter für kleinste Partikel
– Aktivkohlefilter zur Ölentfernung
3. Kältetrockner für die Erreichung des geforderten Drucktaupunkts.
4. Regelmäßige Wartung und Überwachung des Systems.
Anwendungsbereiche für Druckluft der Reinheitsklasse 1:4:1
Diese Reinheitsklasse wird in verschiedenen Industriezweigen eingesetzt, wie zum Beispiel:
1. Verpackungsindustrie: Für Verpackungsmaschinen in der Lebensmittel- und Getränkeindustrie.
2. Pharmaindustrie: Für bestimmte Produktionsprozesse, die eine hohe Partikel- und Ölfreiheit, aber keine extrem trockene Luft benötigen.
3. Elektronikindustrie: Für die Herstellung von elektronischen Komponenten, die nicht feuchtigkeitsempfindlich sind.
4. Automobilindustrie: Für Lackierprozesse und Montagelinien.
5. Textilindustrie: Für Webmaschinen und Färbeprozesse.
6. Druckindustrie: Für den Betrieb von Druckmaschinen.
7. Kunststoffindustrie: Für Spritzguss- und Extrusionsprozesse.
Besonderheiten der Klasse 1:4:1
Die Klasse 1:4:1 bietet eine interessante Kombination aus sehr hoher Partikel- und Ölreinheit bei moderaten Anforderungen an die Luftfeuchtigkeit. Dies macht sie besonders geeignet für Anwendungen, bei denen:
– Eine sehr geringe Partikelbelastung kritisch ist
– Ölfreiheit unbedingt erforderlich ist
– Eine gewisse Restfeuchtigkeit toleriert werden kann oder sogar erwünscht ist
Der relativ hohe Drucktaupunkt von +3°C ermöglicht den Einsatz von Kältetrocknern anstelle der teureren Adsorptionstrockner, was die Betriebskosten senkt. Gleichzeitig wird durch die hohen Anforderungen an Partikel- und Ölgehalt eine sehr saubere Druckluft gewährleistet.
Diese Klasse stellt einen guten Kompromiss zwischen hoher Reinheit und wirtschaftlichem Betrieb dar und ist daher in vielen industriellen Anwendungen weit verbreitet.
Anforderungen für Druckluft der Reinheitsklasse 4:4:1 gemäß ISO 8573-1
Gerne, hier ist eine detaillierte Beschreibung der Druckluft-Reinheitsklasse 4:4:1 gemäß ISO 8573-1:
Anforderungen für Druckluft der Reinheitsklasse 4:4:1 gemäß ISO 8573-1
Eine Druckluft der Reinheitsklasse 4:4:1 muss folgende Kriterien erfüllen:
1. Partikel (4): Maximal 10.000 Partikel pro m³ für Partikelgrößen von 1-5 µm. Für Partikel < 1 µm gibt es keine Begrenzung.
2. Feuchtigkeit (4): Der Drucktaupunkt muss bei ≤ +3°C liegen.
3. Öl (1): Der Gesamtölgehalt (flüssig, Aerosol und Dampf) darf 0,01 mg/m³ nicht überschreiten.
Erreichung der Reinheitsklasse 4:4:1
Um diese Reinheitsklasse zu erreichen, sind folgende Maßnahmen erforderlich:
1. Einsatz von Standardkompressoren mit nachgeschalteter Aufbereitung.
2. Filtration:
– Standardfilter zur Entfernung größerer Partikel
– Feinfilter für kleinere Partikel
– Aktivkohlefilter zur Ölentfernung
3. Kältetrockner für die Erreichung des geforderten Drucktaupunkts.
4. Regelmäßige Wartung des Systems.
Anwendungsbereiche für Druckluft der Reinheitsklasse 4:4:1
Diese Reinheitsklasse findet Anwendung in verschiedenen Industriezweigen, wie zum Beispiel:
1. Allgemeine Fertigungsindustrie: Für pneumatische Werkzeuge und Maschinen.
2. Automobilindustrie: Für nicht-kritische Montageprozesse und Werkstattanwendungen.
3. Bauindustrie: Für pneumatische Werkzeuge auf Baustellen.
4. Holzverarbeitungsindustrie: Für Pneumatikzylinder und Werkzeuge.
5. Metallindustrie: Für Schweißroboter und Schneidwerkzeuge.
6. Kunststoffindustrie: Für bestimmte Extrusionsprozesse.
7. Textilindustrie: Für Webstühle und andere Textilmaschinen.
Besonderheiten der Klasse 4:4:1
Die Klasse 4:4:1 bietet eine interessante Kombination aus moderaten Anforderungen an Partikel- und Feuchtigkeitsgehalt bei gleichzeitig sehr hoher Ölreinheit. Dies macht sie besonders geeignet für Anwendungen, bei denen:
– Eine gewisse Partikelbelastung toleriert werden kann
– Ein Drucktaupunkt von +3°C ausreichend ist
– Ölfreiheit unbedingt erforderlich ist
Die moderaten Anforderungen an Partikel- und Feuchtigkeitsgehalt ermöglichen einen kostengünstigen Betrieb der Druckluftanlage. Der Einsatz von Kältetrocknern ist ausreichend, was die Betriebskosten im Vergleich zu Adsorptionstrocknern senkt.
Die sehr strenge Anforderung an den Ölgehalt (Klasse 1) stellt sicher, dass die Druckluft praktisch ölfrei ist. Dies ist besonders wichtig in Anwendungen, wo selbst geringe Ölmengen zu Problemen führen können, wie bei bestimmten Oberflächenbehandlungen oder in der Lebensmittelindustrie.
Diese Klasse stellt einen guten Kompromiss zwischen ausreichender Reinheit für viele industrielle Anwendungen und wirtschaftlichem Betrieb dar. Sie ist besonders geeignet für Unternehmen, die eine ölfreie Druckluft benötigen, aber keine extrem hohen Anforderungen an Partikelreinheit und Trockenheit haben.
Richtlinien zur Überprüfung der Druckluftklassen nach ISO 8573-1:2010
Die regelmäßige Kontrolle der Druckluftqualitätsklassen gemäß ISO 8573-1:2010 ist entscheidend für die optimale Leistung und Sicherheit pneumatischer Systeme. Folgende Prüfintervalle werden für die Überwachung der Druckluft Reinheitsklassen empfohlen:
- Inbetriebnahme:
- Im ersten Monat nach der Installation: Drei Prüfungen der Druckluftklasse an verschiedenen Tagen durchführen.
- Zweck: Konsistenz und Zuverlässigkeit der Ergebnisse sicherstellen und die Einhaltung aller erforderlichen Reinheitsklassen für Druckluft überprüfen.
- Regelmäßige Kontrollen der Druckluft Qualitätsklasse:
- In den ersten drei Betriebsjahren: Jährliche Überprüfung der Druckluftklassen.
- Begründung: Ermöglicht die Überwachung von Veränderungen in den Druckluftqualitätsklassen und frühzeitige Erkennung potenzieller Probleme, die zu Geräteschäden oder Leistungseinbußen führen könnten.
- Langfristige Überwachung der Reinheitsklassen Druckluft:
- Nach drei Jahren Betrieb: Bei konstant guten Ergebnissen in den Druckluft Reinheitsklassen kann das Prüfintervall auf zwei Jahre verlängert werden.
- Voraussetzung: Sorgfältige Analyse der historischen Daten der Druckluftklassen und des aktuellen Systemzustands.
- Hinweis: Die Verlängerung des Intervalls darf die Qualität der Druckluftklassen nicht beeinträchtigen.
Wichtige Hinweise für die Implementierung der Druckluft Qualitätsklasse-Prüfungen:
- Dokumentieren Sie alle Prüfungen der Druckluftklassen sorgfältig, um Trends und Veränderungen über Zeit zu erkennen.
- Schulen Sie das zuständige Personal in den Prüfverfahren für Druckluft Reinheitsklassen und der Interpretation der Ergebnisse.
- Erstellen Sie klare Handlungsanweisungen für den Fall, dass Abweichungen von den Soll-Druckluftklassen festgestellt werden.
- Überprüfen Sie regelmäßig, ob die gewählten Prüfintervalle für Ihre spezifischen Druckluftqualitätsklassen und Umgebungsbedingungen angemessen sind.
Durch die Einhaltung dieser Richtlinien stellen Sie sicher, dass Ihre Druckluftanlage stets den hohen Standards der Druckluftklassen nach ISO 8573-1:2010 entspricht. Dies trägt zur Effizienz und Zuverlässigkeit Ihrer Produktionsprozesse bei, indem die erforderlichen Reinheitsklassen Druckluft kontinuierlich gewährleistet werden.
Checkliste: Klassifikation von Druckluft nach ISO 8573-1
1. Grundlegende Kenntnisse
-
Sind die Referenzbedingungen für Gasvolumina bekannt? (20 °C, 100 kPa oder 1 bar, relativer Wasserdampfdruck 0)
-
Sind die drei Hauptkontaminanten in Druckluft gemäß ISO 8573 bekannt?
-
Ist die Gruppierung der Reinheitsklassen für Druckluft verstanden?
2. Partikel
-
Sind die Partikelreinheitsklassen gemäß ISO 8573-1 bekannt?
-
Sind die Messmethoden für Partikel (ISO 8573-4 und ISO 8573-8) vertraut?
-
Ist bekannt, dass Klassifikationen 1 bis 5 nicht anwendbar sind, wenn Partikel > 5 μm vorliegen?
3. Feuchtigkeit
-
Sind die Feuchtigkeits- und Flüssigwasser-Reinheitsklassen gemäß ISO 8573-1 verstanden?
-
Sind die Messmethoden für Feuchtigkeit (ISO 8573-3 und ISO 8573-9) bekannt?
4. Öl
-
Sind die Ölreinheitsklassen gemäß ISO 8573-1 bekannt?
-
Sind die Messmethoden für flüssiges Öl und Ölaerosole (ISO 8573-2) vertraut?
-
Ist die Bedeutung der Klassen 3, 4 und X bezüglich des Öldampfgehalts verstanden?
-
Ist bekannt, dass die Messung von Öldampf optional ist und nach ISO 8573-5 erfolgen sollte?
5. Andere Kontaminanten
-
Ist bekannt, dass für gasförmige und mikrobiologische Kontaminanten keine Reinheitsklassen festgelegt sind?
-
Sind die Darstellungsweise und Messnormen für gasförmige (ISO 8573-6) und mikrobiologische Kontaminanten (ISO 8573-7) vertraut?
6. Kennzeichnung und Angabe der Reinheitsklassen
-
Ist das Prinzip der Kennzeichnung der Reinheitsklasse am Messpunkt verstanden?
-
Kann die Bezeichnung korrekt angegeben werden, wenn eine Klasse nicht spezifiziert ist?
-
Ist die Verwendung des Bindestrichs für nicht spezifizierte Reinheitsklassen bekannt?
-
Kann die Kontamination korrekt bezeichnet werden, wenn sie in die Klasse X fällt?
7. Systemverständnis
-
Ist bekannt, dass die Luftreinheitsklassifikation den gesamten Druckluftsystemzustand betrifft?
-
Ist die Bedeutung der richtigen Schmiermittel-/Kühlmittelspezifikation verstanden?
-
Ist der Einfluss der Temperaturregelung auf den Zustand von Flüssigkeiten im System bekannt?
-
Sind die empfohlenen Wartungsintervalle bekannt und werden sie eingehalten?
8. Spezielle Anwendungen
-
Ist bekannt, dass ISO 8573-1 möglicherweise nicht für alle speziellen Anwendungen geeignet ist?
-
Sind Beispiele für Anwendungen mit besonderen Anforderungen (z.B. Atemluft, medizinische Luft) bekannt?
-
Ist bekannt, wann auf andere Informationsquellen (z.B. Pharmakopöen, Reinraumstandards) zurückgegriffen werden sollte?
9. Verständnis der Kontaminanten
-
Ist bekannt, dass Kontaminanten in fester, flüssiger oder gasförmiger Form existieren können?
-
Ist die Interaktion zwischen verschiedenen Kontaminanten verstanden?
-
Sind die verschiedenen Quellen und Größenordnungen von festen Kontaminanten bekannt?
-
Ist die Bedeutung der Partikelklassen 6 und 7 und deren Filtereffizienz verstanden?
-
Sind die Hauptquellen und Auswirkungen von flüssigen Kontaminanten bekannt?
-
Ist die Abhängigkeit der Konzentration gasförmiger Kontaminanten von Temperatur und Druck verstanden?
Problemlösung: Unzureichende Druckluftqualität trotz scheinbar guter Filter
Sehr geehrter Instandhaltungstechniker,
Sie stehen vor dem Problem, dass trotz scheinbar hochwertiger Filter in Ihrer Druckluftanlage die Messungen der Partikelanzahl eine Druckluftklasse unterhalb der Erwartungen zeigen. Die Druckluft Reinheitsklasse entspricht nicht den Anforderungen nach ISO 8573-1. Hier finden Sie eine detaillierte Anleitung zur schrittweisen Problemlösung:
Schritt 1: Überprüfung der Messergebnisse und Druckluftklasse
- Wiederholen Sie die Messungen an verschiedenen Stellen des Systems, um die Druckluftklasse nach ISO 8573-1 zu verifizieren.
- Vergleichen Sie die Ergebnisse mit früheren Messungen der Druckluft Reinheitsklasse, falls vorhanden.
Schritt 2: Inspektion der Filteranlage in Bezug auf Druckluftklassen
- Überprüfen Sie alle Filter auf ihre Eignung für die angestrebte Druckluftklasse.
- Kontrollieren Sie die Dichtungen und Anschlüsse auf Lecks, die die Druckluft Reinheitsklasse beeinträchtigen könnten.
- Stellen Sie sicher, dass die Filter korrekt installiert sind und die Flussrichtung für die gewünschte Druckluftqualitätsklasse stimmt.
- Überprüfen Sie die Differenzdruckanzeigen der Filter in Bezug auf die Druckluftklassen nach ISO 8573-1.
Schritt 3: Wartung der Filter für optimale Druckluftqualitätsklassen
- Reinigen oder ersetzen Sie die Filtereinsätze gemäß Herstellerangaben und den Anforderungen der Druckluftklassen.
- Achten Sie auf die richtige Reihenfolge bei mehrstufigen Filtersystemen zur Erreichung der gewünschten Druckluft Reinheitsklasse.
- Dokumentieren Sie den Austausch und die verwendeten Filtertypen in Bezug auf die Druckluftklassen ISO 8573.
Schritt 4: Überprüfung des Kompressors und dessen Einfluss auf die Druckluftqualitätsklasse
- Inspizieren Sie den Lufteinlass des Kompressors auf Verschmutzungen, die die Druckluftklasse beeinträchtigen könnten.
- Überprüfen Sie den Ölabscheider auf Funktionsfähigkeit und seinen Einfluss auf die Druckluft Reinheitsklasse.
- Kontrollieren Sie die Kühleinrichtung auf Verschmutzungen oder Fehlfunktionen, die die Druckluftqualitätsklasse beeinflussen könnten.
Schritt 5: Inspektion des Rohrleitungssystems in Bezug auf Druckluftklassen
- Suchen Sie nach Korrosion oder Ablagerungen in den Rohren, die die Druckluft Reinheitsklasse verschlechtern könnten.
- Überprüfen Sie alle Verbindungsstellen auf Dichtigkeit, um die angestrebte Druckluftklasse zu gewährleisten.
- Kontrollieren Sie die Kondensatableiter auf korrekte Funktion für die Einhaltung der Druckluftqualitätsklassen.
Schritt 6: Analyse der Umgebungsbedingungen und deren Einfluss auf die Druckluftklassen
- Untersuchen Sie die Luftqualität im Bereich des Kompressoreinlasses in Bezug auf die Druckluftklassen ISO 8573.
- Überprüfen Sie die Raumtemperatur und Luftfeuchtigkeit im Kompressorraum und deren Auswirkungen auf die Druckluft Reinheitsklasse.
- Achten Sie auf mögliche externe Verschmutzungsquellen in der Nähe der Anlage, die die Druckluftqualitätsklasse beeinträchtigen könnten.
Schritt 7: Überprüfung der Systemauslegung für die gewünschte Druckluftklasse
- Vergleichen Sie die tatsächliche Luftmenge und den Druck mit der Auslegung für die angestrebte Druckluftklasse nach ISO 8573-1.
- Überprüfen Sie, ob die installierten Filter für die aktuelle Anwendung und die erforderliche Druckluft Reinheitsklasse geeignet sind.
- Stellen Sie sicher, dass die Filterkapazität nicht überschritten wird, um die gewünschte Druckluftqualitätsklasse zu erhalten.
Schritt 8: Dokumentation und erneute Messung der Druckluftklassen
- Dokumentieren Sie alle durchgeführten Maßnahmen detailliert in Bezug auf die Druckluftklassen ISO 8573.
- Führen Sie nach jeder größeren Änderung eine erneute Messung der Druckluft Reinheitsklasse durch.
- Vergleichen Sie die neuen Messergebnisse mit den Anforderungen der Druckluftqualitätsklassen und vorherigen Werten.
Schritt 9: Konsultation von Experten für Druckluftklassen
- Wenn das Problem mit der Druckluftklasse weiterhin besteht, ziehen Sie den Hersteller der Filteranlage hinzu.
- Erwägen Sie die Beauftragung eines spezialisierten Dienstleisters für Druckluftqualitätsklassen.
- Diskutieren Sie mögliche Systemverbesserungen oder Aufrüstungen zur Erreichung der gewünschten Druckluft Reinheitsklasse.
Schritt 10: Präventive Maßnahmen zur Sicherung der Druckluftklassen
- Erstellen Sie einen detaillierten Wartungsplan für die gesamte Druckluftanlage unter Berücksichtigung der Druckluftklassen nach ISO 8573-1.
- Schulen Sie das Personal in Bezug auf die Bedeutung der Druckluftqualitätsklassen und Reinheitsklassen der Druckluft.
- Implementieren Sie ein regelmäßiges Monitoring-System für die Luftqualität und Druckluftklassen.
Durch systematisches Vorgehen gemäß dieser Schritte sollten Sie in der Lage sein, die Ursache für die unzureichende Druckluftqualitätsklasse zu identifizieren und zu beheben. Dokumentieren Sie jeden Schritt sorgfältig, um zukünftige Problemlösungen zu erleichtern und die Effizienz Ihrer Anlage in Bezug auf die Druckluftklassen ISO 8573 kontinuierlich zu verbessern.
Druckluftfilter
Die Auswahl geeigneter Filter für Druckluftanlagen ist entscheidend, um die gewünschte Druckluftqualität gemäß ISO 8573-1 zu erreichen. Diese Norm definiert verschiedene Druckluftklassen, auch bekannt als Druckluft Reinheitsklassen oder Druckluftqualitätsklassen, die für unterschiedliche industrielle Anwendungen relevant sind.
Für die Erreichung der Druckluft Qualitätsklasse 1 nach ISO 8573-1, der höchsten Reinheitsklasse für Druckluft, ist ein mehrstufiges Filtersystem erforderlich:
- Vorfilter: Grobpartikelfilter zur Entfernung größerer Verunreinigungen
- Feinfilter: Entfernung von Partikeln bis zu 0,1 μm
- Aktivkohlefilter: Adsorption von Öldämpfen und Gerüchen
- Mikrofilter: Entfernung feinster Partikel bis zu 0,01 μm
- Sterilfilter: Für keimfreie Druckluft in sensiblen Anwendungen
Bei der Druckluftklasse 2 gemäß ISO 8573-1 kann auf den Sterilfilter verzichtet werden, sofern keine absolut keimfreie Luft erforderlich ist. Die Kombination aus Vor-, Fein-, Aktivkohle- und Mikrofilter ist hier in der Regel ausreichend, um die Anforderungen der Druckluft Reinheitsklassen zu erfüllen.
Für die Druckluftklasse 3 nach den Druckluft Klassen der ISO 8573-1 genügt oft ein dreistufiges System:
- Vorfilter
- Feinfilter
- Aktivkohlefilter oder Mikrofilter (je nach spezifischen Anforderungen)
Bei der Auswahl der Filter für die verschiedenen Druckluftqualitätsklassen ist es wichtig, nicht nur die Partikelgröße, sondern auch den Ölgehalt und den Drucktaupunkt zu berücksichtigen. Die ISO 8573-1 definiert für jede Druckluftklasse spezifische Grenzwerte für diese Parameter.
Es ist zu beachten, dass die Effizienz der Filter von regelmäßiger Wartung und dem rechtzeitigen Austausch der Filterelemente abhängt. Nur so kann die gewünschte Druckluft Qualitätsklasse dauerhaft sichergestellt werden.
Für die optimale Auslegung eines Filtersystems entsprechend der gewünschten Druckluftklasse empfiehlt es sich, mit Spezialisten für Drucklufttechnik zusammenzuarbeiten. Diese können basierend auf den spezifischen Anforderungen und Bedingungen der Anlage die passende Filterkombination für die angestrebten Druckluft Reinheitsklassen empfehlen.
Einführung in die Druckluftqualität
Die Norm ISO 8573-1:2010 ist ein fundamentales Dokument für die Klassifizierung und Kontrolle der Druckluftqualität in industriellen Anwendungen. Sie definiert präzise Qualitätsklassen für die drei Hauptverunreinigungen in Druckluftsystemen: feste Partikel, Wasser und Öl. Diese Norm ist von entscheidender Bedeutung für Ingenieure, Techniker und Manager, die für die Planung, Installation und Wartung von Druckluftsystemen verantwortlich sind.
Die Bedeutung der Druckluftqualität lässt sich anhand verschiedener industrieller Prozesse veranschaulichen. Betrachten wir beispielsweise die Halbleiterproduktion: Hier kann selbst die kleinste Verunreinigung katastrophale Folgen haben. Ein einzelnes Ölpartikel von wenigen Mikrometern Größe kann die Funktionalität eines gesamten Mikrochips beeinträchtigen. In der Lebensmittelindustrie wiederum können mikrobiologische Kontaminationen, die durch unzureichend gereinigte Druckluft eingebracht werden, zu Produktverunreinigungen und im schlimmsten Fall zu Gesundheitsrisiken für Verbraucher führen.
Grundlegende Konzepte der Druckluftreinigung
Um die in der Norm definierten Qualitätsklassen zu erreichen, ist ein tiefgreifendes Verständnis der Reinigungsprozesse erforderlich. Die Reinigung von Druckluft basiert auf verschiedenen physikalischen und chemischen Prinzipien:
- Partikelabscheidung: Die Entfernung fester Partikel erfolgt hauptsächlich durch mechanische Filtration. Dabei kommen verschiedene Mechanismen zum Einsatz: a) Direktes Abfangen: Partikel, die größer als die Porenöffnungen des Filters sind, werden direkt zurückgehalten. b) Trägheitsabscheidung: Größere Partikel folgen aufgrund ihrer Trägheit nicht den Stromlinien der Luft und prallen auf die Filterfasern. c) Diffusion: Sehr kleine Partikel (< 0,1 μm) bewegen sich aufgrund der Brownschen Bewegung zufällig und kollidieren mit den Filterfasern. Die Effizienz eines Filters kann durch die folgende Gleichung beschrieben werden: E = 1 – exp(-4αηL / (πdf)) Wobei: E: Filtereffizienz α: Packungsdichte des Filtermediums η: Einzelfasereffizienz L: Filterdicke df: Faserdurchmesser
- Wasserentfernung: Die Entfeuchtung der Druckluft basiert auf verschiedenen Prinzipien: a) Kühlung: Durch Abkühlung der Luft wird der Taupunkt gesenkt. Die Menge des kondensierten Wassers kann mit der Clausius-Clapeyron-Gleichung berechnet werden: ln(P2/P1) = (ΔHvap/R) * (1/T1 – 1/T2) Wobei: P1, P2: Dampfdrücke bei Temperaturen T1 und T2 ΔHvap: Verdampfungsenthalpie von Wasser R: Gaskonstante b) Adsorption: Verwendung von Trocknungsmitteln wie Silicagel oder Molekularsieben. Die Adsorptionskapazität kann durch die Freundlich-Isotherme beschrieben werden: x/m = kc^(1/n) Wobei: x/m: adsorbierte Menge pro Einheit Adsorbens c: Gleichgewichtskonzentration des Adsorptivs k, n: empirische Konstanten
- Ölentfernung: Die Entfernung von Öl erfordert oft einen mehrstufigen Prozess: a) Mechanische Abscheidung: Für größere Öltröpfchen, ähnlich der Partikelabscheidung. b) Koaleszenz: Kleine Öltröpfchen werden zu größeren vereint, die leichter abgeschieden werden können. c) Adsorption: Zur Entfernung von Öldämpfen, oft mit Aktivkohle. Die Adsorptionskapazität kann durch die Langmuir-Isotherme beschrieben werden: q = qm * (Kc) / (1 + Kc) Wobei: q: adsorbierte Menge pro Einheit Adsorbens qm: maximale Adsorptionskapazität K: Langmuir-Konstante c: Gleichgewichtskonzentration des Adsorptivs
Qualitätsklassen und ihre praktische Anwendung
Qualitätsklassen für feste Partikel
Die Norm definiert Qualitätsklassen für feste Partikel basierend auf der maximalen Anzahl von Partikeln pro Kubikmeter Luft in verschiedenen Größenbereichen. Diese Klassifizierung ist von entscheidender Bedeutung für viele industrielle Anwendungen, bei denen selbst kleinste Partikel Probleme verursachen können.
Betrachten wir die Klassen im Detail:
Klasse 1: Diese höchste Klasse erlaubt maximal:
- 20.000 Partikel pro m³ für Partikel von 0,1-0,5 μm
- 400 Partikel pro m³ für Partikel von 0,5-1 μm
- 10 Partikel pro m³ für Partikel von 1-5 μm
Um die Herausforderung dieser Anforderung zu verdeutlichen, stellen wir uns ein Volumen von einem Kubikmeter vor. Wenn wir dieses Volumen gleichmäßig in Würfel mit einer Kantenlänge von 1 mm aufteilen würden, hätten wir eine Milliarde solcher Würfel. Die Klasse 1 erlaubt in diesem gesamten Volumen nur 10 Partikel, die größer als 1 μm sind. Dies entspricht praktisch der Reinheit eines Operationssaals.
Praktisches Beispiel: In der Halbleiterproduktion ist eine solch hohe Reinheit oft erforderlich. Ein einzelnes Partikel von 1 μm könnte mehrere Transistoren auf einem modernen Mikrochip bedecken und so dessen Funktion beeinträchtigen.
Berechnung der erforderlichen Filtereffizienz: Nehmen wir an, die Umgebungsluft enthält 1.000.000 Partikel pro m³ im Bereich von 0,1-0,5 μm. Um Klasse 1 zu erreichen, muss der Filter eine Effizienz von:
E = (1.000.000 – 20.000) / 1.000.000 * 100% = 98%
Dies erfordert hocheffiziente HEPA-Filter (High Efficiency Particulate Air).
Klasse 2 bis 5: Diese Klassen erlauben progressiv mehr Partikel. Zum Beispiel erlaubt Klasse 3:
- Keine Begrenzung für Partikel von 0,1-0,5 μm
- 90.000 Partikel pro m³ für Partikel von 0,5-1 μm
- 1.000 Partikel pro m³ für Partikel von 1-5 μm
Praktisches Beispiel: In der Lebensmittelverpackungsindustrie könnte Klasse 3 ausreichend sein. Hier ist die Kontrolle größerer Partikel wichtiger, da diese eher sichtbar sind und das Erscheinungsbild des Produkts beeinträchtigen könnten.
Klassen 6 und 7: Diese Klassen werden durch Massenkonzentration definiert.
- Klasse 6: ≤ 5 mg/m³
- Klasse 7: 5 < Konzentration ≤ 10 mg/m³
Diese Klassen sind typisch für allgemeine industrielle Anwendungen, wie pneumatische Werkzeuge oder Spritzlackieranlagen.
Berechnung der Partikelmassenkonzentration: Nehmen wir an, wir haben 1.000.000 sphärische Partikel pro m³ mit einem Durchmesser von 1 μm und einer Dichte von 2,5 g/cm³ (typisch für Mineralstaub).
Volumen eines Partikels: V = (4/3) * π * (0,5 * 10^-6 m)³ = 5,24 * 10^-19 m³ Masse eines Partikels: m = 5,24 * 10^-19 m³ * 2,5 * 10^6 g/m³ = 1,31 * 10^-12 g Gesamtmasse pro m³: 1,31 * 10^-12 g * 1.000.000 = 1,31 mg/m³
Diese Konzentration würde noch in Klasse 6 fallen.
Qualitätsklassen für Feuchtigkeit
Die Feuchtigkeit in Druckluft wird entweder durch den Drucktaupunkt (für Klassen 1-6) oder den Wassergehalt (für Klassen 7-9) definiert. Die Kontrolle der Feuchtigkeit ist entscheidend, um Korrosion, Bakterienwachstum und Störungen in pneumatischen Systemen zu verhindern.
Klasse 1: Drucktaupunkt ≤ -70°C Dies ist die strengste Klasse und erfordert spezielle Trocknungstechniken wie Tiefkühlung oder hocheffiziente Adsorptionstrockner.
Praktisches Beispiel: In der Raumfahrtindustrie, wo extreme Temperaturschwankungen auftreten können, ist ein sehr niedriger Taupunkt erforderlich, um jegliche Eisbildung in pneumatischen Systemen zu verhindern.
Berechnung des Wassergehalts: Bei -70°C und 1 bar beträgt der Sättigungsdampfdruck von Wasser etwa 0,0026 Pa. Wassergehalt = (0,0026 Pa / (1 * 10^5 Pa)) * 10^6 = 0,026 ppm (v/v)
Dies entspricht etwa 0,000021 g Wasser pro m³ Luft – eine extrem geringe Menge.
Klassen 2-6: Diese decken Drucktaupunkte von -40°C bis +10°C ab.
Praktisches Beispiel für Klasse 4 (Drucktaupunkt ≤ +3°C): In vielen allgemeinen industriellen Anwendungen, wie der Verwendung von Druckluft für Pneumatikzylinder, ist Klasse 4 ausreichend. Sie verhindert Kondensation bei normalen Umgebungstemperaturen.
Berechnung der Wasserentfernung: Angenommen, wir haben Lufteintritt bei 20°C, 100% relativer Feuchtigkeit und 7 bar Druck. Der Wassergehalt beträgt etwa 23 g/m³. Um Klasse 4 zu erreichen, muss der Wassergehalt auf etwa 6 g/m³ reduziert werden.
Zu entfernende Wassermenge = 23 g/m³ – 6 g/m³ = 17 g/m³
Für einen Luftstrom von 100 m³/h bedeutet dies eine Wasserentfernung von 1,7 kg/h.
Klassen 7-9: Diese werden durch flüssigen Wassergehalt definiert.
- Klasse 7: ≤ 0,5 g/m³
- Klasse 8: 0,5 < Wassergehalt ≤ 5 g/m³
- Klasse 9: 5 < Wassergehalt ≤ 10 g/m³
Diese Klassen sind typisch für Anwendungen, bei denen eine gewisse Feuchtigkeit tolerierbar oder sogar erwünscht ist, wie bei einigen Sprühprozessen.
Qualitätsklassen für Öl
Die Ölklassen beziehen sich auf den Gesamtölgehalt, einschließlich flüssigem Öl, Öl-Aerosolen und Öldämpfen. Die Kontrolle des Ölgehalts ist entscheidend, um Produktkontaminationen, Verstopfungen von Filtern und Ventilen sowie Umweltprobleme zu vermeiden.
Klasse 1: ≤ 0,01 mg/m³ Dies ist die strengste Klasse und erfordert mehrere Reinigungsstufen.
Praktisches Beispiel: In der Pharmaindustrie, wo jegliche Ölkontamination die Produktqualität beeinträchtigen könnte, ist Klasse 1 oft erforderlich.
Berechnung der erforderlichen Reinigungseffizienz: Angenommen, der Ölgehalt nach der Kompression beträgt 5 mg/m³. Um Klasse 1 zu erreichen, muss die Reinigungseffizienz sein:
E = (5 – 0,01) / 5 * 100% = 99,8%
Dies erfordert typischerweise eine mehrstufige Filtration:
- Ölabscheider: Entfernt grobe Öltröpfchen, Effizienz etwa 99%
- Feinfilter: Entfernt feinere Öltröpfchen, Effizienz 99,99%
- Aktivkohlefilter: Entfernt Öldämpfe, Effizienz 99,9999%
Gesamteffizienz: 1 – (1-0,99) * (1-0,9999) * (1-0,999999) = 99,999999%
Klassen 2-4: Diese erlauben progressiv höhere Ölgehalte.
- Klasse 2: ≤ 0,1 mg/m³
- Klasse 3: ≤ 1 mg/m³
- Klasse 4: ≤ 5 mg/m³
Praktisches Beispiel für Klasse 3: In der allgemeinen Fertigungsindustrie, wo Druckluft für pneumatische Werkzeuge verwendet wird, ist Klasse 3 oft ausreichend. Eine geringe Menge Öl kann sogar vorteilhaft sein, da sie zur Schmierung der Werkzeuge beiträgt.
Berechnung der Ölkonzentration in der Luft: Angenommen, ein Kompressor mit einer Förderleistung von 10 m³/min verbraucht 0,1 ml Öl pro Stunde.
Ölvolumen pro m³ Luft = (0,1 ml/h) / (10 m³/min * 60 min/h) = 0,000167 ml/m³ Bei einer Öldichte von 0,9 g/ml ergibt dies eine Massenkonzentration von: 0,000167 ml/m³ * 0,9 g/ml = 0,15 mg/m³
Dies würde Klasse 3 entsprechen.
Die Anwendung dieser Qualitätsklassen in der Praxis erfordert ein tiefes Verständnis der Reinigungstechnologien und der spezifischen Anforderungen der jeweiligen Industrie. In vielen Fällen ist eine Kombination verschiedener Reinigungstechniken erforderlich, um die gewünschte Luftqualität zu erreichen und aufrechtzuerhalten.
Anwendung der Norm in verschiedenen Industriezweigen
Die Norm ISO 8573-1:2010 findet in einer Vielzahl von Industriezweigen Anwendung, wobei die Anforderungen je nach Branche und spezifischem Prozess variieren können. Betrachten wir einige Beispiele:
Elektronikindustrie
In der Elektronikindustrie, insbesondere bei der Herstellung von Halbleitern, sind extrem hohe Reinheitsgrade erforderlich.
Beispiel: Fertigung von Mikrochips
- Erforderliche Klasse: 1:2:1
- Begründung:
- Partikel: Klasse 1, um Kurzschlüsse und Defekte auf den Mikrochips zu vermeiden
- Feuchtigkeit: Klasse 2, um Oxidation und elektrostatische Entladungen zu verhindern
- Öl: Klasse 1, um Verunreinigungen der empfindlichen Oberflächen zu vermeiden
Berechnung der Reinraumfläche: Angenommen, wir benötigen 1000 m³/h Druckluft der Klasse 1:2:1. Um diese Luftmenge zu reinigen, benötigen wir eine Filterfläche von etwa:
A = Q / v
Wobei: A: Filterfläche in m² Q: Luftdurchsatz in m³/s v: Filtergeschwindigkeit (typischerweise 0,03 m/s für HEPA-Filter)
A = (1000 / 3600) / 0,03 ≈ 9,26 m²
Dies verdeutlicht den erheblichen Aufwand für die Luftreinigung in dieser Industrie.
Lebensmittel- und Getränkeindustrie
In der Lebensmittelindustrie ist die Vermeidung von mikrobiologischen Kontaminationen von höchster Bedeutung.
Beispiel: Abfüllanlage für Milchprodukte
- Erforderliche Klasse: 2:2:1 [0 KBE/m³]
- Begründung:
- Partikel: Klasse 2, um sichtbare Verunreinigungen zu vermeiden
- Feuchtigkeit: Klasse 2, um Bakterienwachstum zu verhindern
- Öl: Klasse 1, um jegliche Produktkontamination zu vermeiden
- Zusätzlich: 0 KBE/m³ (Koloniebildende Einheiten), um mikrobiologische Sicherheit zu gewährleisten
Berechnung der Sterilisationseffizienz: Angenommen, die Umgebungsluft enthält 1000 KBE/m³. Die erforderliche Sterilisationseffizienz beträgt:
E = (1000 – 0) / 1000 * 100% = 100%
Dies erfordert in der Praxis oft eine Kombination aus HEPA-Filtration und UV-Sterilisation.
Pharmazeutische Industrie
In der Pharmaindustrie sind sowohl Reinheit als auch die Abwesenheit bestimmter Kontaminanten kritisch.
Beispiel: Herstellung von Injektionslösungen
- Erforderliche Klasse: 1:2:1 [CO2 < 500 ppm] [0 KBE/m³]
- Begründung:
- Partikel: Klasse 1, um Verunreinigungen in den Injektionslösungen zu vermeiden
- Feuchtigkeit: Klasse 2, um chemische Stabilität zu gewährleisten
- Öl: Klasse 1, um jegliche Kontamination zu vermeiden
- CO2 < 500 ppm, um pH-Wert-Schwankungen zu minimieren
- 0 KBE/m³, um Sterilität zu gewährleisten
Berechnung der CO2-Entfernung: Angenommen, die Umgebungsluft enthält 1000 ppm CO2. Die erforderliche Entfernungseffizienz beträgt:
E = (1000 – 500) / 1000 * 100% = 50%
Dies kann durch den Einsatz von CO2-Adsorbern erreicht werden, z.B. mit Aktivkohle oder speziellen molekularen Sieben.
Messmethoden und ihre Bedeutung
Die genaue Messung der Luftqualität ist entscheidend für die Einhaltung der Norm. Die ISO 8573-Serie umfasst spezifische Teile, die sich mit Messmethoden befassen:
Partikelmessung (ISO 8573-4)
Methode: Lichtstreuung oder Kondensationskernzähler Prinzip: Partikel streuen Licht oder dienen als Kondensationskerne, was detektiert und gezählt wird.
Beispielberechnung: Angenommen, ein Lichtstreuungszähler misst in 1 Liter Luft:
- 50 Partikel von 0,1-0,5 μm
- 10 Partikel von 0,5-1,0 μm
- 2 Partikel von 1,0-5,0 μm
Umrechnung auf 1 m³:
- 50.000 Partikel von 0,1-0,5 μm
- 10.000 Partikel von 0,5-1,0 μm
- 2.000 Partikel von 1,0-5,0 μm
Dies würde Klasse 3 entsprechen.
Feuchtigkeitsmessung (ISO 8573-3)
Methoden:
- Taupunktspiegel
- Kapazitive Sensoren
Beispiel für Taupunktspiegelmessung: Prinzip: Die Oberfläche wird gekühlt, bis sich Kondensat bildet. Die Temperatur, bei der dies geschieht, ist der Taupunkt.
Berechnung des Wassergehalts aus dem Taupunkt: Angenommen, der gemessene Drucktaupunkt beträgt -40°C bei 7 bar.
- Sättigungsdampfdruck bei -40°C: etwa 12,8 Pa
- Partialdruck des Wasserdampfs: 12,8 Pa * (7 + 1) = 102,4 Pa
- Wassergehalt: (102,4 / (7 * 10^5)) * 1000 = 0,146 g/m³
Dies entspricht Klasse 2 für Feuchtigkeit.
Ölmessung (ISO 8573-2 und ISO 8573-5)
Methoden:
- Für Öl-Aerosole: Infrarotspektroskopie oder Gaschromatographie
- Für Öldämpfe: Flammenionisationsdetektor (FID)
Beispielberechnung für FID-Messung: Angenommen, der FID misst eine Kohlenwasserstoffkonzentration von 0,05 mg/m³ (als Methanäquivalent).
Umrechnung in Ölkonzentration: Typisches Verhältnis von Öl zu Methanäquivalent: 1,5 Ölkonzentration = 0,05 mg/m³ * 1,5 = 0,075 mg/m³
Dies würde Klasse 2 für Öl entsprechen.
Spezielle Überlegungen und Herausforderungen
Mikrobiologische Kontamination
Obwohl die Norm keine spezifischen Klassen für mikrobiologische Kontamination definiert, ist dies in vielen Industrien von großer Bedeutung.
Methode: Kultivierung auf Nährmedien oder PCR (Polymerase-Kettenreaktion)
Beispiel: In einer Lebensmittelverpackungsanlage wird eine Luftprobe von 1000 Litern entnommen und auf einem Nährboden kultiviert. Nach 48 Stunden werden 5 Kolonien gezählt.
Berechnung der KBE/m³: KBE/m³ = (5 Kolonien / 1000 Liter) * 1000 = 5 KBE/m³
Dies würde in vielen Lebensmittelanwendungen als akzeptabel gelten, obwohl für besonders empfindliche Produkte strengere Grenzwerte gelten können.
Korrosion in Druckluftsystemen
Die Korrosion in Druckluftsystemen ist ein komplexes Problem, das von mehreren Faktoren abhängt, einschließlich Feuchtigkeit, Säuren und Salzen.
Beispielberechnung der Korrosionsrate: Angenommen, wir haben ein Stahlrohr mit einer Wandstärke von 5 mm und messen eine Wanddickenabnahme von 0,1 mm pro Jahr.
Korrosionsrate = 0,1 mm/Jahr Lebensdauer bis zur kritischen Wandstärke (angenommen 2 mm): (5 mm – 2 mm) / 0,1 mm/Jahr = 30 Jahre
Dies verdeutlicht die Bedeutung der Luftqualität für die Langlebigkeit des Systems.
Energieeffizienz und Luftqualität
Die Erreichung hoher Luftqualität erfordert oft einen erhöhten Energieaufwand. Es ist wichtig, ein Gleichgewicht zwischen Qualität und Effizienz zu finden.
Beispielberechnung: Angenommen, ein System benötigt 100 kW zur Erzeugung von 1000 m³/h Druckluft der Klasse 3:4:3. Um Klasse 1:2:1 zu erreichen, steigt der Energiebedarf auf 130 kW.
Energiekosten pro Jahr (bei 8760 Betriebsstunden und 0,15 €/kWh):
- Klasse 3:4:3: 100 kW * 8760 h * 0,15 €/kWh = 131.400 €
- Klasse 1:2:1: 130 kW * 8760 h * 0,15 €/kWh = 170.820 €
Differenz: 39.420 € pro Jahr
Diese erhöhten Kosten müssen gegen die Vorteile der höheren Luftqualität abgewogen werden.
Die praktische Anwendung der Norm ISO 8573-1:2010 erfordert ein tiefes Verständnis nicht nur der Norm selbst, sondern auch der spezifischen Anforderungen der jeweiligen Industrie und der komplexen Wechselwirkungen zwischen verschiedenen Faktoren wie Luftqualität, Energieeffizienz und Systemlebensdauer. Eine sorgfältige Analyse und kontinuierliche Überwachung sind entscheidend, um optimale Ergebnisse zu erzielen und die Einhaltung der Norm zu gewährleisten.