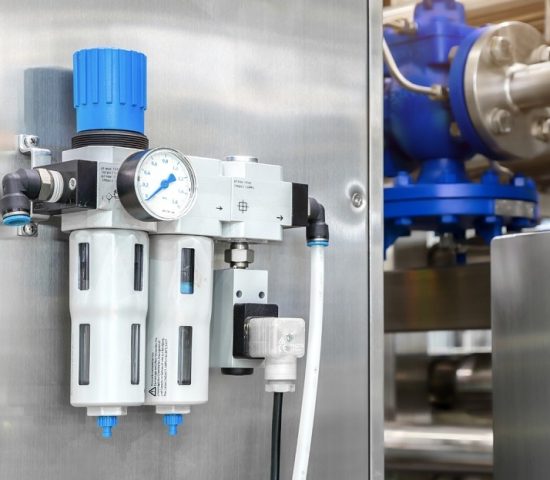
LEBENSMITTELPRODUKTION: DRUCKLUFTQUALITÄT
[ISO 8573-1]
Wir prüfen die Qualität der Druckluft in der Lebensmittelindustrie auf folgende Parameter:
- Partikelgehalt,
- Wassergehalt / Drucktaupunkt,
- Öl-Aerosol-Gehalt,
- Bakterien-, Hefe- und Schimmelpilzgehalt.
Die Messungen führen wir an folgenden Tagen durch: Donnerstag-Freitag (in ganz Deutschland)
Die Zeit, die für die Messungen an einem Messpunkt benötigt wird: 40-60 Minuten
Anfragen und Bestellungen: info@qualifizierung-validierung.de
ISO 8573-1 ist eine weithin anerkannte Norm zur Beurteilung der Qualität von Druckluft aufgrund des Gehalts an drei Verunreinigungen: Partikel, Wasser und Öl. In der Lebensmittelproduktion wird die Qualität der Druckluft häufig auf mikrobielle Kontamination geprüft, wobei diese Prüfungen nicht die Grundlage für die Klassifizierung der Druckluftreinheit nach ISO 8573-1 bilden, sondern ergänzen sie nur.
Die Prüfung der Druckluftreinheit erfolgt in der Regel an Messstellen, die sich in den letzten Abschnitten des Druckluftverteilungssystems befinden. In der Lebensmittelproduktion lohnt es sich, die Qualität der Druckluft für die Teile des Systems zu überprüfen, in denen die Druckluft in direkten Kontakt mit dem Lebensmittel oder der Verpackung kommt. Durch die Prüfung der Druckluftqualität an 3-4 Messstellen kann in der Regel bereits eine zuverlässige Beurteilung der Druckluftqualität vorgenommen werden.
Das Lebensmittelrecht besagt im Allgemeinen, dass komprimierte Gase (einschließlich Druckluft), die in der Lebensmittelproduktion verwendet werden, nicht zu einer „Kontamination des Lebensmittelprodukts“ führen dürfen. Ein großer Teil der derzeit in der Lebensmittelbranche tätigen Unternehmen hat ein freiwilliges Qualitäts- und Sicherheitsmanagementsystem wie IFS Food, BRC Food oder FSSC 22000 implementiert – diese Systeme erfordern von den Lebensmittelherstellern eine Überwachung der Qualität komprimierter Gase.
In der aktuellen Version 8 des IFS Food Standards heißt es unter Punkt „4.9.10 Druckluft und Gase“: „4.9.10.1 Die Qualität von Druckluft, die in direkten Kontakt mit Lebensmitteln oder Lebensmittelkontaktmaterialien kommt, muss risikobasiert überwacht werden. Druckluft darf keine Kontaminationsrisiken darstellen. 4.9.10.2 Gase, die in direkten Kontakt mit Lebensmitteln oder Lebensmittelkontaktmaterialien kommen, müssen Sicherheit und Qualität für den beabsichtigten Gebrauch nachweisen.“
Der BRC Food Standard verweist seinerseits auf einen der gemeinsam von BRC und BCAS entwickelten Leitfäden: „Food Grade Compressed Air – A code of practice“. Dieser Leitfaden gibt folgende Grenzwerte für Partikelgehalte an:
Druckluft für direkten oder gelegentlichen Kontakt mit Lebensmitteln:
– Partikel der Größe 0,1 – 0,5µm: 100.000 Partikel,
– Partikel der Größe 0,5 – 1,0µm: 1.000 Partikel,
– Partikel der Größe 1,0 – 5,0µm: 10 Partikel.
Die oben angegebenen Grenzwerte entsprachen zum Zeitpunkt der Veröffentlichung des Leitfadens dem Grenzwert der Klasse 2 für Druckluft gemäß ISO 8573-1:2001. Seit 2010 akzeptiert die Norm ISO 8573-1 höhere Partikelgrenzwerte für die einzelnen Klassen (sie hat die Qualitätsanforderungen für die Reinheitsklassen gesenkt), aber die Anforderungen wurden von der BRC-Organisation nicht gesenkt.
Einige Lebensmittelhersteller wenden noch strengere Akzeptanzkriterien bei Druckluftmessungen an:
Druckluft in direktem Kontakt mit nicht-trockenen Lebensmittelprodukten (z.B. Getränke, Fleisch, Gemüse usw.):
– Feststoffpartikel: Klasse 1; Wasser: Klasse 4; Öl: Klasse 1 (gemäß ISO 8573-1:2010)
Druckluft in direktem Kontakt mit trockenen Lebensmittelprodukten:
– Feststoffpartikel: Klasse 1; Wasser: Klasse 2; Öl: Klasse 1 (gemäß ISO 8573-1:2010)
Druckluft in Lebensmittelverpackungsmaschinen: – Feststoffpartikel: Klasse 1; Wasser: Klasse 4; Öl: Klasse 1 (gemäß ISO 8573-1:2010)
Bei mikrobiologischen Untersuchungen gibt es unterschiedliche Ansätze. Einige Lebensmittelhersteller erwarten, dass Bakterien, Hefen und Schimmelpilze in den untersuchten Druckluftproben nicht nachweisbar sind. Andere Lebensmittelhersteller legen interne Warngrenzwerte von 10-50 KBE / 1m³ Druckluftprobe und Alarmgrenzwerte von 100 KBE / 1m³ Druckluftprobe fest.
Leider ist es auch wahr, dass einige Lebensmittelhersteller überhaupt keine Druckluftmessungen durchführen und den Einfluss ihrer Reinheit auf die hergestellten Produkte nicht bewerten.
ISO 8573-1: Grenzwerte
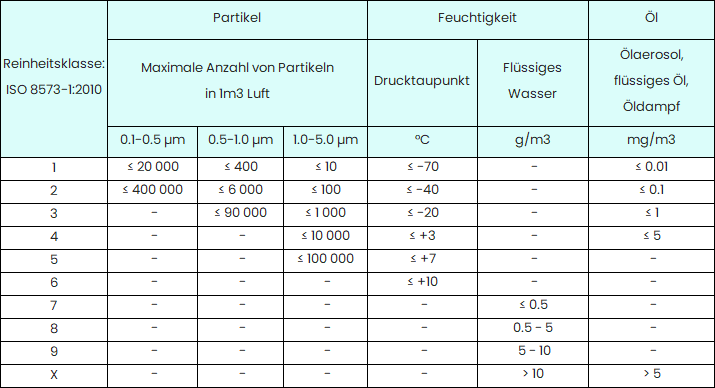
GEPRÜFTE PARAMETER
PARTIKEL
Messmethode: ISO 8573-4:2019
Messbereich: Messung von Partikeln im Bereich 0,1 - 0,5 µm (Klassen 1-7 nach ISO 8573-1)
Messausrüstung: Laser-Partikelzähler
WASSER
Messmethode: ISO 8573-3:2010
Messbereich: –70 … +30°C td
Messunsicherheit: ±2°C
Messausrüstung: Drucktaupunktmessgerät
ÖL-AEROSOL
Messmethode: ISO 8573-2:2007
Messbereich: 0,003 – 2mg/1m3
Messunsicherheit: ±10%
Messausrüstung: Filtrationskit, FTIR
MIKROBIOLOGIE
Messmethode: ISO 8573-7:2003
Geprüfte Parameter: Gehalt an Bakterien, Hefen, Schimmelpilzen in 1 m3 Luft
Messausrüstung: Druckluftprüfgerät, Anzucht der Kolonien in Petrischalen
TECHNISCHE ANFORDERUNEN
ÜBERPRÜFEN SIE, BEVOR SIE EINE BESTELLUNG AUFGEBEN
KUNDENSEITIGE ANSCHLÜSSE
Schnellkupplung DN 7.2
Gewindekupplung 1/2' oder 3/8' (Innengewinde)
Leitung 6, 8, 10, 12 oder 16mm (Außendurchmesser)
ANLAGEDRUCK
Maximal 7,3 bar
UMGEBUNGSTEMPERATUR
Minimum 10°C
LAGE DER MESSSTELLE
1 Gereinigte Druckluft
Die Partikelzahl kann nur in Gas gemessen werden, das auf den Filtern gereinigt wurde. Es ist nicht möglich, vor den Filtern zu messen.
2. Leicht zugänglicher Raum
Die Messgeräte sind stoßempfindlich und wiegen mehr als 20 kg, weshalb sie z. B. nicht auf einer Leiter, auf Tanks usw. getragen werden dürfen.
ZEIT DER PROBENAHME
Die Durchführung der Testreihe an einer Messstelle dauert etwa 45-60 Minuten.
BERICHTERSTATTUNG
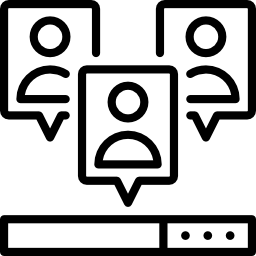
AUF DEUTSCH
UND ENGLISCH
Standardmäßig erstellen wir den Bericht in einer zweisprachigen Version: Deutsch-Englisch.
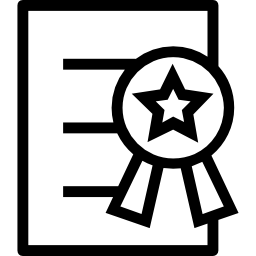
IM EINKLANG MIT DEN
GMP-GRUNDSÄTZEN
Der Bericht enthält u. a. die Angaben zu den verwendeten Geräten und der an den Prüfungen beteiligten Personen.
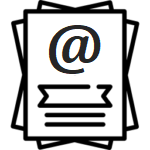
ELEKTRONISCHE
ÜBERMITTLUNG
Der Bericht wird in elektronischer Form
(PDF-Dokument) übermittelt.
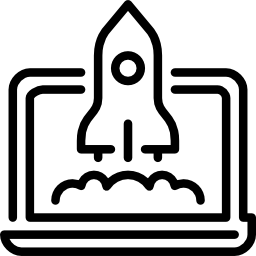
IN DER REGEL INNERHALB
VON 14-21 TAGEN FERTIG
In der Regel wird der Bericht innerhalb von 14 Tagen
(maximal 21 Tagen) nach der Messung übermittelt.
DIESE KUNDEN HABEN UNS BEREITS VERTRAUT
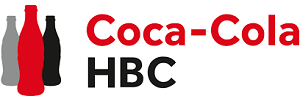
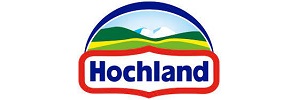
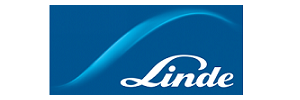
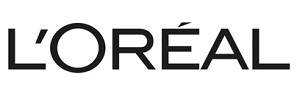
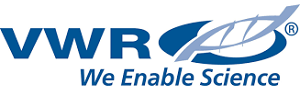
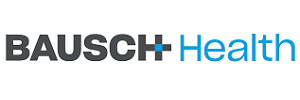
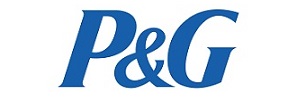
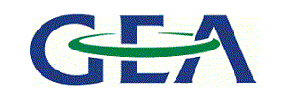
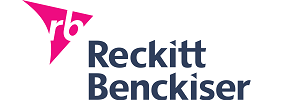
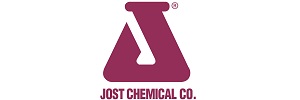
PREISLISTE
Möchten Sie schnell die Kosten für die Durchführung von Messungen abschätzen?
In der Preisliste finden Sie:
– Informationen über die von uns durchgeführten Messungen
– Preise der Untersuchungen
EIN GENAUES ANGEBOT ANFORDERN
Druckluft als Prozessluft in der Lebensmittelproduktion
In der modernen Lebensmittelindustrie spielt die Druckluftqualität eine entscheidende Rolle für die Lebensmittelsicherheit. Druckluft, die als Prozessluft verwendet wird (z.B. zum Ausblasen von Formen oder für den direkten Kontakt mit Lebensmitteln), erfordert eine wesentlich höhere Reinheitsklasse als Druckluft, die nur zur Steuerung von Ventilen, Zylindern oder Greifern eingesetzt wird.
Die Verwendung von hochqualitativer Druckluft in der Lebensmittelproduktion ist unerlässlich, um die strengen Anforderungen der Lebensmittelsicherheit zu erfüllen. Die ISO 8573-1 Norm für Lebensmittel legt die Qualitätsstandards fest, die in der Branche eingehalten werden müssen. Diese Norm definiert verschiedene Klassen der Druckluftqualität, wobei für den direkten Kontakt mit Lebensmitteln die höchsten Reinheitsklassen erforderlich sind.
Aufgrund der hohen Anforderungen an die Druckluftqualität in der Lebensmittelindustrie beschränkt sich der Einsatz von Prozessluft in der Regel auf spezifische Bereiche. Es wird empfohlen, eine dezentrale Druckluftaufbereitung so nah wie möglich an den Verbrauchsstellen einzurichten. Diese Strategie ermöglicht es, die Menge an Druckluft mit hohen Reinheitsklassen zu begrenzen, was zu erheblichen Energieeinsparungen führt.
Die Nähe der Druckluftaufbereitung zu den Zielgeräten minimiert das Risiko einer erneuten Verunreinigung der hochreinen Druckluft in den Leitungen, beispielsweise durch Rostpartikel. Dies ist besonders wichtig in der Lebensmittelproduktion, wo selbst kleinste Verunreinigungen schwerwiegende Folgen haben können.
Um die optimale Druckluftqualität für Lebensmittel zu gewährleisten, sollten regelmäßige Überprüfungen und Wartungen der Druckluftsysteme durchgeführt werden. Dies umfasst die Kontrolle von Filtern, Trocknern und Leitungen, um sicherzustellen, dass die Druckluft den hohen Standards der Lebensmittelindustrie entspricht.
Zusammenfassend lässt sich sagen, dass die sorgfältige Kontrolle und Verwaltung der Druckluftqualität in der Lebensmittelindustrie von entscheidender Bedeutung ist. Durch die Einhaltung strenger Standards und den Einsatz modernster Technologien können Unternehmen die Lebensmittelsicherheit gewährleisten und gleichzeitig ihre Produktionsprozesse optimieren.
Druckluft im direkten Kontakt mit nicht-trockenen Lebensmitteln
In der modernen Lebensmittelproduktion spielt Druckluft eine entscheidende Rolle, insbesondere wenn sie in direkten Kontakt mit nicht-trockenen Lebensmitteln kommt. Dies betrifft eine breite Palette von Produkten wie Getränke, Fleisch, Gemüse und ähnliche Erzeugnisse. Die Lebensmittelsicherheit steht hierbei an oberster Stelle, und die Qualität der verwendeten Druckluft ist von entscheidender Bedeutung.
Die Druckluft in der Lebensmittelindustrie wird für verschiedene Zwecke eingesetzt, darunter:
Transport von Zutaten und Fertigprodukten
Mischvorgänge in der Produktion
Verpackungsprozesse
Reinigung von Behältern und Anlagen
Bei all diesen Anwendungen kommt die Druckluft in direkten Kontakt mit den Lebensmitteln. Daher ist es unerlässlich, dass die Druckluftqualität in der Lebensmittelindustrie strengen Standards entspricht.
Um die Lebensmittelsicherheit zu gewährleisten, müssen Unternehmen die Druckluftqualität gemäß der Norm ISO 8573-1 für Lebensmittel sicherstellen. Diese internationale Norm definiert die Reinheitsklassen für Druckluft und ist besonders relevant für die Lebensmittelproduktion. Für nicht-trockene Lebensmittel gelten folgende Qualitätsklassen nach ISO 8573-1:2010:
Feststoffpartikel: Klasse 1
Wasser: Klasse 4
Öl: Klasse 1
Um die erforderliche Luftreinheitsklasse zu erreichen, wird ein mehrstufiges Filtersystem eingesetzt. Der Prozess beginnt mit der zentralen Druckluftvorbereitung, gefolgt von einer Reihe zunehmend feinerer Filter. Zunächst wird die Luft durch einen 5 μm Filter gereinigt, dann durch einen 1 μm Filter und schließlich durch einen hochpräzisen 0,01 μm Filter. Die letzte Stufe bildet ein Aktivkohlefilter, der restliche gasförmige Verunreinigungen und Gerüche entfernt. Am Eingang des Systems beträgt das Kompressionsverhältnis -:4:4, am Ausgang 1:4:1, was auf eine erhebliche Verbesserung der Luftqualität hinweist. Dieser mehrstufige Filtrationsprozess gewährleistet, dass die in der Lebensmittelproduktion verwendete Druckluft die höchsten Reinheitsstandards erfüllt, die von den Lebensmittelsicherheitsnormen gefordert werden. Diese sorgfältige Aufbereitung der Druckluft ist entscheidend für die Sicherstellung der Lebensmittelqualität und -sicherheit in der gesamten Produktionskette.
Diese strengen Anforderungen an die Druckluftqualität für Lebensmittel sind notwendig, um Kontaminationen zu vermeiden und die Produktsicherheit zu gewährleisten. Qualitätssicherungsexperten in der Lebensmittelindustrie müssen daher besonderes Augenmerk auf die Überwachung und Aufrechterhaltung dieser Standards legen.
Um die geforderte Druckluftqualität in der Lebensmittelindustrie zu erreichen und aufrechtzuerhalten, sind folgende Maßnahmen erforderlich:
Regelmäßige Wartung und Überprüfung der Druckluftsysteme
Einsatz geeigneter Filtrationssysteme
Kontinuierliche Überwachung der Druckluftqualität
Schulung des Personals hinsichtlich der Bedeutung von Druckluftqualität für die Lebensmittelsicherheit
Druckluft in direktem Kontakt mit trockenen Lebensmitteln: Ein kritischer Aspekt der Lebensmittelsicherheit
Druckluft wird nicht nur für den Transport und das Mischen von Zutaten eingesetzt, sondern kommt auch direkt mit Lebensmitteln in Berührung. Besonders bei der Herstellung trockener Lebensmittel ist die Druckluftqualität von höchster Bedeutung für die Lebensmittelsicherheit.
Die Druckluft in der Lebensmittelindustrie unterliegt strengen Qualitätsanforderungen, die in der Norm ISO 8573-1 festgelegt sind. Diese Norm definiert die Reinheitsklassen für Druckluft und ist besonders relevant für die Lebensmittelproduktion. Bei trockenen Lebensmitteln gelten verschärfte Anforderungen an die Luftfeuchtigkeit, da jede Form von Feuchtigkeit die Produktqualität beeinträchtigen kann.
Für Fachleute im Bereich der Instandhaltung ist es unerlässlich, die spezifischen Anforderungen an die Druckluftqualität in der Lebensmittelindustrie zu kennen und umzusetzen. Basierend auf der ISO 8573-1 Norm für Lebensmittel wird für den direkten Kontakt mit trockenen Lebensmitteln folgende Klassifizierung empfohlen:
Feststoffpartikel: Klasse 1
Wasser: Klasse 2
Öl: Klasse 1
Das Bild zeigt eine Filterkaskade zur Aufbereitung von Druckluft gemäß der Klasse 1:2:1 nach ISO 8573-1, die für die Lebensmittelindustrie relevant ist. Der Prozess beginnt mit der zentralen Drucklufterzeugung (-4:4) und durchläuft dann mehrere Filterstufen: Zunächst einen 5 µm Filter, gefolgt von einem Adsorptionstrockner zur Feuchtigkeitsreduzierung. Anschließend passiert die Luft einen 1 µm Filter und einen 0,01 µm Filter für eine feinere Partikelentfernung. Den Abschluss bildet ein Aktivkohlefilter, der speziell Öldämpfe und Gerüche entfernt. Diese Filterkaskade gewährleistet, dass die Druckluft am Ende den strengen Anforderungen der Klasse 1:2:1 entspricht, was für den direkten Kontakt mit Lebensmitteln unerlässlich ist.
Diese strenge Klassifizierung gewährleistet, dass die Druckluft frei von schädlichen Verunreinigungen ist, die die Qualität und Sicherheit der Lebensmittel gefährden könnten.
Um diese hohen Standards der Druckluftqualität in der Lebensmittelindustrie zu erreichen und aufrechtzuerhalten, sind regelmäßige Wartungen und Überprüfungen der Druckluftsysteme unerlässlich. Instandhaltungsspezialisten sollten besonderes Augenmerk auf die Filtration, Trocknung und Aufbereitung der Druckluft legen, um sicherzustellen, dass sie den strengen Anforderungen der Lebensmittelproduktion entspricht.
Die Einhaltung dieser Richtlinien für Druckluft in der Lebensmittelindustrie ist nicht nur eine Frage der Produktqualität, sondern auch der gesetzlichen Compliance und des Verbraucherschutzes. Durch die Sicherstellung einer hohen Druckluftqualität in der Lebensmittelproduktion tragen Instandhaltungsspezialisten wesentlich zur Gewährleistung der Lebensmittelsicherheit und zum Schutz der öffentlichen Gesundheit bei.
Lebensmittelproduktion - Druckluft in Verpackungsanlagen
Die Lebensmittelsicherheit hängt maßgeblich von der Qualität der verwendeten Druckluft ab, da diese in direkten Kontakt mit Verpackungsmaterialien kommt, die anschließend mit Lebensmitteln befüllt werden. Dadurch wird das Verpackungsmaterial de facto Teil der Lebensmittelverarbeitungszone.
Für die Druckluft in der Lebensmittelproduktion gelten strenge Qualitätsanforderungen gemäß der Norm ISO 8573-1:2010. Diese Norm definiert die Druckluftqualität für die Lebensmittelindustrie wie folgt:
- Festpartikel: Klasse 1
- Wasser: Klasse 4
- Öl: Klasse 1
Pneumatischer Transport in der Lebensmittelindustrie: Effiziente Förderung von Schüttgütern
Der pneumatische Transport spielt in der Lebensmittelindustrie eine entscheidende Rolle bei der effizienten und hygienischen Beförderung von pulverförmigen und körnigen Materialien wie Mehl, Zucker oder Gewürzen. Die Druckluft in der Lebensmittelindustrie ist dabei der Schlüssel zur Bewegung dieser Schüttgüter durch geschlossene Rohrsysteme.
Grundlagen des pneumatischen Transports
Das Prinzip des pneumatischen Transports basiert auf der Nutzung von Druckunterschieden. Schüttgüter werden in einem Luftstrom suspendiert und durch Rohrleitungen befördert. Dabei unterscheidet man zwischen Saug-, Druck- und Saugdruckförderung, wobei die Wahl des Systems von Faktoren wie Förderdistanz, Materialeigenschaften und Durchsatzmengen abhängt.
Aufbau eines pneumatischen Fördersystems
Ein typisches System für den pneumatischen Transport in der Lebensmittel Produktion mit Druckluft besteht aus folgenden Hauptkomponenten:
- Drucklufterzeugung (Kompressor)
- Luftaufbereitung (Filter, Trockner)
- Materialeinspeisung (z.B. Zellenradschleuse)
- Förderleitung
- Abscheider (z.B. Zyklon oder Filteranlage)
- Steuerung und Regelung
Anforderungen an die Druckluftqualität
Die Druckluftqualität in der Lebensmittelindustrie ist von höchster Bedeutung für die Produktsicherheit und Anlageneffizienz. Gemäß der Norm ISO 8573-1 für Lebensmittel muss die Druckluft frei von Verunreinigungen wie Öl, Wasser und Partikeln sein. Für die meisten Anwendungen in der Lebensmittelindustrie wird mindestens Klasse 1.4.1 gefordert, was bedeutet:
- Partikel: Klasse 1 (≤ 0,1 μm, max. 0,1 mg/m³)
- Wasser: Klasse 4 (Drucktaupunkt ≤ +3°C)
- Öl: Klasse 1 (max. 0,01 mg/m³)
Physikalische Grundlagen und Berechnungen
Die Förderung von Schüttgütern basiert auf dem Prinzip der Fluidisierung. Die Luftgeschwindigkeit muss dabei hoch genug sein, um die Partikel in Suspension zu halten. Die minimale Fluidisierungsgeschwindigkeit (v_mf) kann mit der Ergun-Gleichung berechnet werden:
v_mf = (μ / (ρ_f * d_p)) * [150 * (1 – ε) / ε³] * [(μ / (ρ_f * d_p))² + 0,0408]^0,5 – 150 * (1 – ε) / ε³ * (μ / (ρ_f * d_p))
Dabei ist:
- μ: dynamische Viskosität der Luft
- ρ_f: Dichte der Luft
- d_p: Partikeldurchmesser
- ε: Porosität des Schüttguts
Für die Dimensionierung der Förderleitung ist die Berechnung des Druckverlusts entscheidend. Dieser setzt sich aus dem Reibungsverlust in der Rohrleitung und dem geodätischen Höhenunterschied zusammen.
Lebensmittelsicherheit und Druckluft
Die Lebensmittelsicherheit bei der Verwendung von Druckluft ist ein kritischer Aspekt. Kontaminationen durch Mikroorganismen, Öl oder Partikel müssen unbedingt vermieden werden. Daher ist eine regelmäßige Wartung und Überwachung der Druckluftaufbereitung unerlässlich.
Moderne Systeme zur Überwachung der Druckluftqualität in der Lebensmittelindustrie ermöglichen eine kontinuierliche Messung relevanter Parameter wie Restölgehalt, Feuchtigkeit und Partikelbelastung. Dies gewährleistet eine konstant hohe Produktqualität und minimiert das Risiko von Verunreinigungen.
Energieeffizienz und Nachhaltigkeit
Die Erzeugung von Druckluft ist energieintensiv. Typischerweise werden nur etwa 10-15% der aufgewendeten elektrischen Energie in nutzbare pneumatische Energie umgewandelt. Daher sind Maßnahmen zur Steigerung der Energieeffizienz von großer Bedeutung:
- Optimierung der Kompressorregelung
- Nutzung der Abwärme der Kompressoren
- Regelmäßige Leckageortung und -beseitigung
- Einsatz von Frequenzumrichtern zur bedarfsgerechten Drucklufterzeugung
Durch diese Maßnahmen können Energieeinsparungen von bis zu 30% realisiert werden.
Fazit
Der pneumatische Transport in der Lebensmittelindustrie erfordert ein tiefes Verständnis der physikalischen Grundlagen sowie der spezifischen Anforderungen an die Druckluftqualität für Lebensmittel. Durch die richtige Auslegung und kontinuierliche Überwachung der Systeme kann eine effiziente, hygienische und sichere Förderung von Schüttgütern gewährleistet werden. Die Beachtung der Norm ISO 8573-1 für Lebensmittel und die Implementierung moderner Überwachungssysteme sind dabei unerlässlich, um höchste Standards in der Lebensmittelproduktion zu erfüllen.
Pneumatischer Transport von Kaffee- und Teekörnern: Technische Herausforderungen und Lösungen
Der pneumatische Transport von Kaffee- und Teekörnern stellt besondere Anforderungen an die Fördertechnik. Anders als bei pulverförmigen Substanzen müssen hier größere, unregelmäßig geformte Partikel schonend bewegt werden, ohne dass ihre Qualität beeinträchtigt wird.
Spezifische Eigenschaften von Kaffee- und Teekörnern
Kaffeebohnen und Teekörner weisen einige charakteristische Eigenschaften auf, die beim pneumatischen Transport berücksichtigt werden müssen:
- Größe: Kaffeebohnen sind typischerweise 8-18 mm lang, während Teekörner je nach Sorte zwischen 0,5-2 mm variieren.
- Dichte: Geröstete Kaffeebohnen haben eine Schüttdichte von ca. 350-450 kg/m³, Teekörner etwa 200-300 kg/m³.
- Feuchtigkeitsempfindlichkeit: Beide Produkte reagieren empfindlich auf Feuchtigkeit, was die Anforderungen an die Druckluftqualität erhöht.
- Aromaschutz: Die flüchtigen Aromastoffe müssen während des Transports erhalten bleiben.
Anlagenkonzept für den schonenden Transport
Ein pneumatisches Fördersystem für Kaffee- und Teekörner umfasst folgende Hauptkomponenten:
- Niederdruckverdichter (max. 0,5 bar Überdruck)
- Luftaufbereitung mit Feinfilter und Adsorptionstrockner
- Produkteinspeisung über eine spezielle Zellenradschleuse
- Förderleitung aus elektropoliertem Edelstahl
- Sanfter Produktabscheider (z.B. Zyklonabscheider mit reduzierter Einströmgeschwindigkeit)
- Staubfilter zur Reinigung der Abluft
- Frequenzumrichtergesteuerte Gebläse für variable Fördergeschwindigkeiten
Strömungsmechanische Betrachtungen
Die Förderung von Kaffee- und Teekörnern erfolgt im sogenannten Dünnstromverfahren. Dabei ist die Berechnung der minimalen Fluggeschwindigkeit v_min entscheidend:
v_min = k * √(2 * g * d * (ρ_s – ρ_f) / (ρ_f * c_w))
Wobei:
- k: Sicherheitsfaktor (typisch 1,2-1,5)
- g: Erdbeschleunigung (9,81 m/s²)
- d: Partikeldurchmesser
- ρ_s: Partikeldichte
- ρ_f: Luftdichte
- c_w: Widerstandsbeiwert
Für Kaffeebohnen ergibt sich bei einem mittleren Durchmesser von 10 mm und einer Dichte von 400 kg/m³ eine minimale Fluggeschwindigkeit von etwa 8-10 m/s. Für Teekörner mit 1 mm Durchmesser und 250 kg/m³ Dichte liegt sie bei ca. 3-4 m/s.
Druckluftanforderungen und -aufbereitung
Die Druckluftqualität spielt eine kritische Rolle für den Erhalt der Produktqualität. Folgende Anforderungen müssen erfüllt werden:
- Partikelfreiheit: Klasse 1 nach ISO 8573-1 (max. 0,1 μm und 0,1 mg/m³)
- Feuchte: Klasse 2 (Drucktaupunkt -40°C) zur Vermeidung von Kondensation
- Ölfrei: Klasse 0 (weniger als 0,003 mg/m³)
Die Luftaufbereitung erfolgt über eine mehrstufige Filtration:
- Zyklonabscheider für grobe Partikel
- Koaleszenzfilter zur Öl- und Feinstpartikelabscheidung
- Adsorptionstrockner zur Feuchtigkeitsreduzierung
- Aktivkohlefilter zur Entfernung von Gerüchen und Dämpfen
Energieeffizienz und Wärmerückgewinnung
Die Kompression der Förderluft erzeugt erhebliche Wärmemengen. Bei einem typischen Fördersystem mit 75 kW Antriebsleistung entstehen etwa 54 kW Abwärme. Diese kann durch Wärmetauscher zurückgewonnen und für Prozesse wie die Röstung oder Trocknung genutzt werden, was die Gesamteffizienz der Anlage erheblich steigert.
Reinigung und Wartung
Regelmäßige Reinigung und Wartung sind essentiell für den hygienischen Betrieb:
- CIP-fähige Ausführung (Cleaning In Place) der Förderleitungen
- Automatische Reinigungszyklen mit Heißluft (typisch 120°C für 20 Minuten)
- Regelmäßiger Austausch von Filterelementen (typisch alle 3-6 Monate)
- Vierteljährliche Inspektion der Zellenradschleusen auf Verschleiß
Prozessüberwachung und Qualitätssicherung
Moderne Systeme nutzen verschiedene Sensoren zur Echtzeitüberwachung:
- Laser-Partikelzähler zur kontinuierlichen Luftqualitätskontrolle
- Kapazitive Feuchtesensoren in der Förderleitung
- Differenzdrucksensoren zur Überwachung des Filterzustands
- Thermografische Kameras zur Detektion von Lagerschäden an rotierenden Teilen
Die Daten werden in einem zentralen Leitsystem erfasst und ermöglichen eine prädiktive Wartung sowie die lückenlose Dokumentation der Produktqualität.
Fazit
Der pneumatische Transport von Kaffee- und Teekörnern erfordert ein sorgfältig abgestimmtes System, das die spezifischen Eigenschaften dieser Produkte berücksichtigt. Durch die Kombination von präziser strömungsmechanischer Auslegung, hochwertiger Druckluftaufbereitung und intelligenter Prozessüberwachung lässt sich ein schonender und effizienter Materialtransport realisieren, der höchsten Qualitätsansprüchen genügt.
Pneumatischer Transport granulierter Lebensmittelprodukte: Technische Aspekte und Anforderungen
Der pneumatische Transport von granulierten Lebensmittelprodukten stellt aufgrund der spezifischen Eigenschaften dieser Materialien besondere Anforderungen an die Fördertechnik. Zu den typischen Produkten gehören Zucker, Salz, Getreide, Nüsse oder auch Tierfutter. Diese Anlagen müssen nicht nur effizient arbeiten, sondern auch höchste Hygienestandards erfüllen.
Eigenschaften granulierter Lebensmittel
Granulierte Lebensmittel weisen folgende charakteristische Merkmale auf:
- Partikelgröße: Typischerweise zwischen 0,8 und 5 mm
- Schüttdichte: Variiert stark, z.B. Zucker ca. 800 kg/m³, Haferflocken ca. 400 kg/m³
- Abrasivität: Kann je nach Produkt erheblich sein (z.B. Salz, Zucker)
- Feuchtigkeitsempfindlichkeit: Viele Produkte neigen zur Agglomeration bei Feuchtigkeitsaufnahme
- Bruchempfindlichkeit: Einige Produkte (z.B. Cerealien) dürfen nicht beschädigt werden
Systemaufbau für den Granulattransport
Ein typisches pneumatisches Fördersystem für Lebensmittelgranulate besteht aus:
- Drucklufterzeugung: Schraubenkompressor mit Frequenzumrichter
- Luftaufbereitung: Mehrstufige Filtration und Trocknung
- Produkteinspeisung: Hygienische Zellenradschleuse oder Injektorsystem
- Förderleitung: Edelstahlrohre mit großen Biegeradien (min. 10x Rohrdurchmesser)
- Weichen und Verteilsysteme: Pneumatisch betätigte Klappenweichen
- Produktabscheidung: Zyklonabscheider oder Filterabscheider
- Staubfilter: Zur Reinigung der Abluft (HEPA-Filter)
- Steuerungssystem: SPS mit Visualisierung und Rezeptverwaltung
Strömungstechnische Betrachtungen
Die Förderung granulierter Produkte erfolgt meist im Dichtstromverfahren, um Produktbeschädigungen zu minimieren. Die Froude-Zahl Fr ist hierbei ein wichtiger Parameter:
Fr = v² / (g * D)
Wobei:
- v: Fördergeschwindigkeit [m/s]
- g: Erdbeschleunigung (9,81 m/s²)
- D: Rohrdurchmesser [m]
Für einen stabilen Dichtstromtransport sollte Fr zwischen 3 und 15 liegen. Bei einem typischen Rohrdurchmesser von 100 mm ergibt sich eine optimale Fördergeschwindigkeit von 5-12 m/s.
Druckluftanforderungen und -aufbereitung
Die Druckluftqualität ist entscheidend für die Produktsicherheit. Folgende Anforderungen müssen erfüllt werden:
- Partikelfreiheit: Klasse 1 nach ISO 8573-1 (max. 0,1 μm und 0,1 mg/m³)
- Feuchte: Klasse 2 (Drucktaupunkt -40°C)
- Ölfrei: Klasse 0 (weniger als 0,003 mg/m³)
Die Luftaufbereitung umfasst:
- Ansaugfilter (F7 nach EN 779)
- Ölfreier Schraubenkompressor
- Nachkühler mit Zyklonabscheider
- Kältetrockner (für Vorkühlung)
- Adsorptionstrockner (für Feinttrocknung)
- Staubfilter (H13 nach EN 1822)
Energieeffizienz und Wärmerückgewinnung
Die Kompression erzeugt erhebliche Wärmemengen. Bei einem 90 kW Kompressor fallen etwa 72 kW als Abwärme an. Diese kann genutzt werden für:
- Raumheizung (direkt über Luftkühlung)
- Prozesswärme (über Wasser-Wärmetauscher)
- Vorwärmung von Reinigungswasser
Durch effiziente Wärmerückgewinnung lassen sich bis zu 80% der Energiekosten für die Drucklufterzeugung einsparen.
Hygiene und Reinigung
Höchste Hygienestandards sind unerlässlich:
- Alle produktberührenden Teile aus Edelstahl 1.4404 (AISI 316L)
- Oberflächenrauigkeit Ra < 0,8 μm für leichte Reinigung
- CIP-fähige Ausführung (Cleaning In Place)
- Automatische Reinigungszyklen mit Heißluft (130°C für 30 Minuten)
- Sterilfilter (HEPA H14) für die Trocknungsluft nach der Reinigung
Prozessüberwachung und Qualitätssicherung
Moderne Systeme nutzen fortschrittliche Sensorik:
- Massenfluss-Messung mittels Coriolis-Sensoren
- Inline-Feuchtemessung durch NIR-Spektroskopie
- Elektrostatische Partikeldetektoren zur Fremdkörpererkennung
- Echtzeitüberwachung der Druckluftqualität (Partikler, Feuchte, Ölgehalt)
Die Daten werden in einem MES (Manufacturing Execution System) erfasst und ermöglichen eine lückenlose Rückverfolgbarkeit.
Spezielle Herausforderungen bei Lebensmittelgranulaten
- Produktschonender Transport: Verwendung von Langbogenkrümmern (R/D > 10) und Prallplatten aus PTFE
- Vermeidung von Entmischung: Einsatz von Mischern vor der Abfüllung
- Statische Aufladung: Verwendung von leitfähigen Kunststoffrohren oder Erdungssystemen
- Explosionsschutz: ATEX-konforme Ausführung für staubexplosionsgefährdete Bereiche (z.B. bei Zucker oder Mehl)
Fazit
Der pneumatische Transport von granulierten Lebensmitteln erfordert ein tiefes Verständnis der Produkteigenschaften und der strömungsmechanischen Grundlagen. Durch die Kombination moderner Fördertechnik mit hochwertigem Hygienedesign und intelligenter Prozessüberwachung lassen sich Systeme realisieren, die höchsten Qualitäts- und Effizienzanforderungen gerecht werden. Die kontinuierliche Optimierung dieser Systeme bleibt eine Herausforderung für Ingenieure in der Lebensmittelindustrie, um den steigenden Anforderungen an Produktqualität, Energieeffizienz und Nachhaltigkeit gerecht zu werden.
Sprühtrocknung in der Milchpulverproduktion: Atomisierung und Druckluftanforderungen
Die Sprühtrocknung ist ein komplexer thermischer Prozess, der in der Lebensmittelindustrie, insbesondere bei der Herstellung von Milchpulver, weitverbreitet ist. Die Atomisierung der Flüssigkeit spielt dabei eine Schlüsselrolle für die Effizienz des Verfahrens und die Qualität des Endprodukts.
Grundlagen der Sprühtrocknung
Bei der Sprühtrocknung wird eine Flüssigkeit (in diesem Fall Milch) in feine Tröpfchen zerstäubt und in einen heißen Luftstrom eingebracht. Durch die große Oberfläche der Tröpfchen verdampft das Wasser sehr schnell, und es entstehen feine Pulverpartikel.
Atomisierung der Milch
Die Atomisierung ist der kritische erste Schritt des Prozesses. Zwei Hauptmethoden kommen zum Einsatz:
- Rotationszerstäuber
- Druckdüsen (pneumatische oder hydraulische Zerstäubung)
Rotationszerstäuber
- Funktionsprinzip: Zentrifugalkraft
- Drehzahl: 10.000 – 30.000 U/min
- Tröpfchengröße: 20 – 180 μm
- Vorteil: Gleichmäßige Tröpfchenverteilung
Pneumatische Zweistoffdüsen
- Funktionsprinzip: Hochgeschwindigkeits-Luftstrom zerreißt Flüssigkeitsfilm
- Luftgeschwindigkeit: 300 – 500 m/s
- Tröpfchengröße: 10 – 100 μm
- Vorteil: Feinere Zerstäubung möglich
Systemaufbau einer Sprühtrocknungsanlage
- Vorkonzentrierungsstufe (Eindampfer)
- Homogenisator
- Zerstäubungseinheit (Rotationszerstäuber oder Düsen)
- Trocknungskammer (typischerweise 15-30 m hoch)
- Heißlufterzeugung (Gasbefeuerung oder Dampferhitzer)
- Zyklonabscheider für Grobpartikel
- Feinstaubfilter (Schlauchfilter oder Elektrofilter)
- Kühlstufe
- Abpackanlage
Druckluftanforderungen für die Atomisierung
Die Druckluftversorgung ist kritisch für die Funktion pneumatischer Düsen und die Steuerung des gesamten Prozesses.
Technische Spezifikationen:
- Druck: 4 – 7 bar (abhängig vom Düsendesign)
- Volumenstrom: 50 – 200 m³/h pro Düse
- Temperatur: 20 – 30°C (kontrolliert durch Nachkühler)
- Luftqualität nach ISO 8573-1:
- Partikel: Klasse 1 (max. 0,1 μm und 0,1 mg/m³)
- Feuchte: Klasse 2 (Drucktaupunkt -40°C)
- Öl: Klasse 0 (weniger als 0,003 mg/m³)
Drucklufterzeugung und -aufbereitung:
- Ölfreier Schraubenkompressor (z.B. Atlas Copco ZR 250, 250 kW)
- Nachkühler mit Zyklonabscheider
- Adsorptionstrockner im Wechselbetrieb
- Mehrschicht-Aktivkohlefilter zur Öldampfentfernung
- Sterilfilter (HEPA H14) als letzte Stufe
Strömungsmechanische Betrachtungen
Die Weber-Zahl (We) ist ein wichtiger Parameter für die Zerstäubung:
We = (ρ_l * v² * d) / σ
Wobei:
- ρ_l: Dichte der Flüssigkeit [kg/m³]
- v: Relativgeschwindigkeit zwischen Flüssigkeit und Gas [m/s]
- d: Charakteristischer Durchmesser [m]
- σ: Oberflächenspannung [N/m]
Für eine effektive Zerstäubung sollte We > 13 sein. Bei Milch (σ ≈ 0,05 N/m) und einem Düsendurchmesser von 1 mm ergibt sich eine notwendige Relativgeschwindigkeit von etwa 100 m/s.
Energieeffizienz und Wärmerückgewinnung
Die Sprühtrocknung ist ein energieintensiver Prozess. Typische Energieverbräuche:
- Thermisch: 3000 – 4000 kJ/kg verdampftes Wasser
- Elektrisch: 150 – 300 kJ/kg Pulver
Maßnahmen zur Effizienzsteigerung:
- Mehrstufige Eindampfung vor der Sprühtrocknung
- Wärmerückgewinnung aus der Abluft (60-80°C) für die Vorwärmung der Zuluft
- Nutzung der Kompressorabwärme zur Vorwärmung des Produkts
- Einsatz von Frequenzumrichtern für Gebläse und Kompressoren
Prozessüberwachung und Qualitätssicherung
Kritische Kontrollpunkte:
- Eingangsviskosität der Milch (typisch 10-50 mPa*s)
- Zerstäubungsdruck und -temperatur
- Eingangs- und Ausgangstemperatur der Trocknungsluft
- Restfeuchte des Pulvers (Ziel: 2-4%)
- Partikelgrößenverteilung (typisch d50 = 50-250 μm)
Inline-Messungen:
- Laser-Diffraktometrie zur Tröpfchengrößenanalyse
- NIR-Spektroskopie zur Feuchtigkeitsbestimmung
- Bildanalyse zur Partikelmorphologie-Kontrolle
Herausforderungen und Optimierungspotenziale
- Vermeidung von Pulverablagerungen (Wandbeläge)
- Lösung: Optimierte Strömungsführung, intermittierende Wandreinigung
- Minimierung der thermischen Belastung
- Ansatz: Mehrstufige Trocknung mit angepassten Temperaturniveaus
- Steigerung der Ausbeute
- Maßnahme: Feinabscheider mit Rückführung des Feinstaubs
- Flexibilität bei Produktwechseln
- Konzept: Modulare Düsensysteme und anpassbare Prozessparameter
- Energieeffizienz
- Innovation: Integration von Wärmepumpen zur Abwärmenutzung
Fazit
Die Sprühtrocknung von Milch zu Milchpulver ist ein hochkomplexer Prozess, bei dem die präzise Kontrolle der Atomisierung und der Luftqualität entscheidend für Produktqualität und Effizienz ist. Die Anforderungen an die Drucklufttechnik sind besonders hoch, da sie direkt mit dem Produkt in Kontakt kommt. Fortschrittliche Überwachungssysteme und innovative Ansätze zur Energierückgewinnung tragen dazu bei, die Effizienz zu steigern und gleichzeitig höchste Qualitätsstandards zu gewährleisten. Die kontinuierliche Optimierung dieses Prozesses bleibt eine zentrale Aufgabe für Verfahrenstechniker und Anlagenbetreiber in der Milchindustrie.
Druckluftanwendungen bei der Beschichtung von Süßwaren: Technische Anforderungen und Anlagenkonzepte
Die Beschichtung von Süßwaren erfordert präzise kontrollierte Prozesse, bei denen Druckluft eine zentrale Rolle spielt. Von der Zerstäubung von Beschichtungsmaterialien bis hin zur Prozesssteuerung ist die Qualität und Verfügbarkeit von Druckluft entscheidend für die Produktqualität und Effizienz der Anlage.
Hauptanwendungen von Druckluft in der Süßwarenbeschichtung
- Sprühbeschichtung (Atomisierung)
- Produkttransport und -handhabung
- Reinigung und Trocknung
- Prozesssteuerung und Automatisierung
Druckluftanforderungen für Sprühbeschichtungen
Technische Spezifikationen:
- Druck: 2-6 bar (abhängig vom Düsentyp und Beschichtungsmaterial)
- Volumenstrom: 50-200 Nl/min pro Düse
- Luftqualität nach ISO 8573-1:
- Partikel: Klasse 1 (max. 0,1 μm und 0,1 mg/m³)
- Feuchte: Klasse 2 (Drucktaupunkt -40°C)
- Öl: Klasse 0 (weniger als 0,003 mg/m³)
Düsensysteme:
- Zweistoffdüsen für feine Zerstäubung
- Luftdruck: 2-4 bar
- Materialdruck: 1-2 bar
- Ultraschallzerstäuber für besonders feine Tröpfchen
- Frequenz: 20-100 kHz
- Luftunterstützung: 0,5-1 bar
Drucklufterzeugung und -aufbereitung
Kompressorsystem:
- Ölfreier Schraubenkompressor (z.B. Atlas Copco ZR 90 VSD+, 90 kW)
- Frequenzumrichtersteuerung für energieeffiziente Lastanpassung
- Wärmerückgewinnung zur Nutzung der Kompressorabwärme (ca. 72 kW bei 90 kW Antriebsleistung)
Luftaufbereitung:
- Nachkühler mit Zyklonabscheider
- Adsorptionstrockner im Wechselbetrieb (z.B. Atlas Copco BD 100+)
- Mehrstufige Filtration:
- Vorfilter (1 μm)
- Feinfilter (0,01 μm)
- Aktivkohlefilter zur Geruchsentfernung
- Sterilfilter (HEPA H14) als letzte Stufe vor Produktkontakt
Druckluftverteilung
- Hauptleitungen: Edelstahl 1.4404 (AISI 316L), Durchmesser DN50-DN80
- Ringleitung zur gleichmäßigen Druckverteilung
- Abzweige mit Kugelhähnen und Schnellkupplungen für Flexibilität
- Druckminderer an den Verbrauchsstellen zur präzisen Druckregelung
Energieeffizienz und Nachhaltigkeit
- Wärmerückgewinnung aus der Kompressorabwärme:
- Nutzung für Raumheizung oder Prozesswärme (z.B. Vorwärmung von Beschichtungsmaterialien)
- Potenzielle Energieeinsparung: 70-80% der elektrischen Eingangsleistung
- Leckagemanagement:
- Regelmäßige Ultraschall-Leckageortung
- Ziel: Leckagerate < 5% des Gesamtverbrauchs
- Druckluft-Energiemonitoring:
- Echtzeitüberwachung des spezifischen Energieverbrauchs (typisch: 0,1-0,2 kWh/m³)
- KPI-basierte Optimierung
Prozesssteuerung und Automatisierung
- Pneumatische Ventile für präzise Dosierung von Beschichtungsmaterialien
- Reaktionszeit: < 20 ms
- Wiederholgenauigkeit: ± 1%
- Pneumatische Zylinder für Produkthandhabung
- Druckbereich: 4-6 bar
- Positioniergenauigkeit: ± 0,1 mm
- Luftmengenmessung zur Prozessüberwachung
- Thermische Massendurchflussmesser (z.B. Endress+Hauser t-mass F/I)
- Messbereich: 0,5-3000 Nm³/h
Reinigung und Hygiene
- CIP-Systeme mit Druckluftunterstützung:
- Luftdruck für Reinigungsdüsen: 2-3 bar
- Luftunterstütztes Ausblasen von Restfeuchtigkeit
- Sterilisation von Druckluftleitungen:
- Periodische Heißluftsterilisation (130°C, 30 Minuten)
- Ozonbehandlung der Druckluft (0,1-0,2 ppm)
Qualitätssicherung der Druckluft
- Kontinuierliche Überwachung:
- Online-Partikelmessung (Laserspektrometer)
- Taupunktmessung (kapazitiver Sensor)
- Ölgehaltmessung (Photoionisationsdetektor)
- Regelmäßige Probennahme und Laboranalyse:
- Mikrobiologische Untersuchung (max. 100 KBE/m³)
- Partikelanalyse nach ISO 8573-4
Herausforderungen und Lösungsansätze
- Problem: Schwankende Druckluftqualität Lösung: Implementierung eines mehrstufigen Aufbereitungssystems mit Redundanz
- Problem: Hoher Energieverbrauch Lösung: Einsatz von VSD-Kompressoren und bedarfsgerechte Drucklufterzeugung
- Problem: Kontaminationsrisiko Lösung: Verwendung von Sterilfiltern und regelmäßige Integritätstests
- Problem: Ungleichmäßige Beschichtung durch Druckschwankungen Lösung: Installation von Druckausgleichsbehältern und präzisen Druckreglern
Innovative Ansätze
- Elektrostatisch unterstützte Luftzerstäubung:
- Erhöhte Auftrageffizienz durch geladene Tröpfchen
- Reduzierter Overspray um bis zu 30%
- Pulsierendes Luftsystem für verbesserte Schichtbildung:
- Frequenz: 10-50 Hz
- Verbesserte Penetration bei porösen Substraten
- IoT-basierte Druckluftüberwachung:
- Echtzeitanalyse von Verbrauch und Qualität
- Prädiktive Wartung basierend auf Maschinenlernalgorithmen
Fazit
Die Druckluftinstallation spielt eine zentrale Rolle bei der Beschichtung von Süßwaren. Sie beeinflusst direkt die Qualität des Endprodukts, die Effizienz des Prozesses und die Betriebskosten der Anlage. Eine sorgfältige Planung, regelmäßige Wartung und kontinuierliche Optimierung der Druckluftanlage sind entscheidend für den Erfolg in der Süßwarenproduktion. Die Integration innovativer Technologien und die Berücksichtigung strenger Hygieneanforderungen stellen hohe Anforderungen an Ingenieure und Technologen, bieten aber auch Chancen für signifikante Verbesserungen in Qualität und Effizienz.
Druckluftanwendungen beim Sprühen flüssiger Zusätze in der Lebensmittelindustrie
Die Applikation flüssiger Zusätze wie Glasuren oder Öle auf Lebensmittelprodukte erfordert präzise und hygienische Sprühtechniken. Druckluft spielt hierbei eine entscheidende Rolle für die Zerstäubung und gleichmäßige Verteilung dieser Zusätze.
Druckluftgestützte Sprühsysteme
1. Zweistoffdüsen
Funktionsprinzip:
- Druckluft und Flüssigkeit werden separat zugeführt und erst am Düsenaustritt gemischt
- Feine Zerstäubung durch hohe Relativgeschwindigkeit zwischen Luft und Flüssigkeit
Technische Daten:
- Luftdruck: 1-6 bar (abhängig von Viskosität und gewünschter Tröpfchengröße)
- Luftverbrauch: 50-500 Nl/min pro Düse
- Tröpfchengröße: 10-100 μm
2. Ultraschall-Zerstäuber mit Luftunterstützung
Funktionsprinzip:
- Primärzerstäubung durch Ultraschallschwingungen (20-100 kHz)
- Sekundärzerstäubung und Formung des Sprühkegels durch Druckluft
Technische Daten:
- Luftdruck: 0,5-2 bar
- Luftverbrauch: 20-100 Nl/min pro Zerstäuber
- Tröpfchengröße: 10-50 μm
3. Rotationszerstäuber mit Luftunterstützung
Funktionsprinzip:
- Zentrifugalkraft einer rotierenden Scheibe für Primärzerstäubung
- Druckluft für Feinzerstäubung und Richtungskontrolle
Technische Daten:
- Luftdruck: 0,5-3 bar
- Luftverbrauch: 100-1000 Nl/min pro Zerstäuber
- Rotationsgeschwindigkeit: 10.000-50.000 U/min
Druckluftanforderungen und -aufbereitung
Luftqualität:
- ISO 8573-1 Klasse 1.2.1 oder besser
- Partikel: Klasse 1 (max. 0,1 μm und 0,1 mg/m³)
- Feuchte: Klasse 2 (Drucktaupunkt -40°C)
- Öl: Klasse 1 (max. 0,01 mg/m³)
Aufbereitungssystem:
- Ölfreier Schraubenkompressor (z.B. Atlas Copco ZR 75 VSD+, 75 kW)
- Nachkühler mit Zyklonabscheider
- Adsorptionstrockner (z.B. Atlas Copco CD 100+)
- Mehrstufige Filtration:
- Vorfilter (1 μm)
- Feinfilter (0,01 μm)
- Aktivkohlefilter
- Sterilfilter (HEPA H14) als finale Stufe
Prozesssteuerung und Automatisierung
Druckluftgesteuerte Komponenten:
- Pneumatische Ventile für präzise Dosierung
- Reaktionszeit: < 10 ms
- Wiederholgenauigkeit: ± 0,5%
- Luftmotoren für Rührwerke in Vorratsbehältern
- Drehzahlbereich: 100-10.000 U/min
- Leistung: 0,1-5 kW
- Pneumatische Zylinder für Düsenpositionierung
- Positioniergenauigkeit: ± 0,05 mm
Überwachungssysteme:
- Massendurchflussmesser für Luft und Flüssigkeit
- Messbereich Luft: 0,1-1000 Nl/min
- Genauigkeit: ± 0,5% vom Messwert
- Drucksensoren zur Überwachung des Zerstäubungsdrucks
- Messbereich: 0-10 bar
- Genauigkeit: ± 0,1% vom Endwert
Energieeffizienz und Nachhaltigkeit
Energiesparmaßnahmen:
- Verwendung von VSD-Kompressoren für bedarfsgerechte Lufterzeugung
- Energieeinsparung: bis zu 35% gegenüber Festdrehzahlkompressoren
- Wärmerückgewinnung aus der Kompressorabwärme
- Nutzungspotenzial: bis zu 94% der elektrischen Eingangsleistung
- Präzise Druckregelung zur Vermeidung von Überdruck
- Druckreduktion um 1 bar spart ca. 7% Energie
Ressourceneffizienz:
- Closed-Loop-Sprühsysteme zur Rückgewinnung von Overspray
- Materialeinsparung: bis zu 30%
- Luftrezirkulation nach Feinfilterung
- Reduzierung des Frischluftbedarfs um bis zu 50%
Hygieneaspekte und Reinigung
CIP-Systeme (Cleaning In Place):
- Druckluftunterstützte Reinigungsdüsen
- Luftdruck: 2-4 bar
- Verbesserte Reinigungswirkung durch Kavitation
- Luftspülung nach Nassreinigung
- Luftdruck: 6-8 bar
- Dauer: 2-5 Minuten
Sterilisation:
- Heißluftsterilisation der Leitungen
- Temperatur: 130-150°C
- Dauer: 30-60 Minuten
- Ozonbehandlung der Druckluft
- Ozonkonzentration: 0,1-0,2 ppm
- Kontaktzeit: 1-2 Sekunden
Innovative Ansätze
1. Elektrostatisch unterstützte Luftzerstäubung:
- Elektrische Aufladung der Tröpfchen: 60-80 kV
- Verbesserung der Auftrageffizienz um 20-30%
2. Pulsierende Luftströmung:
- Frequenz: 10-100 Hz
- Verbesserung der Schichtgleichmäßigkeit um bis zu 15%
3. Adaptive Sprühsysteme:
- Echtzeit-Anpassung von Luftdruck und -menge basierend auf Produktgeometrie
- Reduzierung des Oversprays um bis zu 40%
Herausforderungen und Lösungsansätze
- Problem: Verstopfung feiner Düsen Lösung: Implementierung von Ultraschallreinigungssystemen in den Düsen
- Problem: Ungleichmäßige Beschichtung bei komplexen Produktformen Lösung: Einsatz von 3D-Scanning und robotergeführten Sprühsystemen
- Problem: Produktkontamination durch Druckluft Lösung: Mehrstufige Filtration und regelmäßige mikrobiologische Kontrollen
- Problem: Hoher Energieverbrauch Lösung: Bedarfsgerechte Drucklufterzeugung und Nutzung von Niederdrucksystemen wo möglich
Fazit
Die Anwendung von Druckluft beim Sprühen flüssiger Zusätze in der Lebensmittelindustrie erfordert ein tiefes Verständnis der Zerstäubungstechnologien, Hygieneanforderungen und Energieeffizienz. Durch den Einsatz moderner Druckluftsysteme und innovativer Sprühtechniken können Produktqualität, Prozesseffizienz und Ressourcennutzung signifikant verbessert werden. Die kontinuierliche Weiterentwicklung dieser Technologien, insbesondere im Hinblick auf Präzision und Nachhaltigkeit, wird auch in Zukunft eine zentrale Herausforderung für Ingenieure und Lebensmitteltechnologen darstellen.
Druckluftanwendung beim Ausblasen von Verpackungen vor dem Befüllen
Das Ausblasen von Verpackungen mit Druckluft vor dem Befüllen ist ein kritischer Prozessschritt in der Lebensmittel-, Getränke- und Pharmaindustrie. Diese Maßnahme gewährleistet die Reinheit der Verpackungen und trägt maßgeblich zur Produktqualität und -sicherheit bei.
Grundlagen des Ausblasens von Verpackungen
Zweck:
- Entfernung von Staub, Partikeln und möglichen Kontaminanten
- Reduzierung der mikrobiellen Belastung
- Vorbereitung für aseptische Abfüllprozesse
Typische Verpackungsarten:
- PET-Flaschen
- Glasflaschen
- Dosen
- Kartonverpackungen (Tetra Pak)
- Kunststoffbecher
Druckluftanforderungen und technische Spezifikationen
Luftqualität:
Nach ISO 8573-1:2010 für lebensmittelkonforme Anwendungen:
- Partikel: Klasse 1 (≤ 0,1 μm, max. 0,1 mg/m³)
- Feuchtigkeit: Klasse 2 (Drucktaupunkt ≤ -40°C)
- Öl: Klasse 0 (< 0,003 mg/m³)
Druck und Volumenstrom:
- Betriebsdruck: 4-7 bar (anpassbar je nach Verpackungstyp)
- Volumenstrom: 20-100 Nl/min pro Düse (abhängig von Verpackungsgröße und Taktzeit)
Düsenkonfiguration:
- Mehrdüsensysteme für gleichmäßige Abdeckung
- Ionisierungsdüsen zur Neutralisierung statischer Aufladung
Drucklufterzeugung und -aufbereitung
Kompressorsystem:
- Ölfreier Schraubenkompressor (z.B. Atlas Copco ZR 110, 110 kW)
- Frequenzumrichtersteuerung für energieeffiziente Lastanpassung
- Wärmerückgewinnung (bis zu 94% der elektrischen Eingangsleistung nutzbar)
Luftaufbereitung:
- Nachkühler mit Zyklonabscheider
- Adsorptionstrockner (z.B. Atlas Copco BD 100+)
- Mehrstufige Filtration:
- Vorfilter (1 μm)
- Feinfilter (0,01 μm)
- Aktivkohlefilter
- Sterilfilter (HEPA H14) als finale Stufe
Druckluftverteilung:
- Hauptleitungen: Edelstahl 1.4404 (AISI 316L), Durchmesser DN50-DN80
- Ringleitungssystem für gleichmäßige Druckverteilung
- Druckminderer an Verbrauchsstellen für präzise Druckregelung
Prozessintegration und Steuerung
Synchronisation mit Abfüllanlage:
- Taktgenaue Steuerung der Ausblasimpulse
- Typische Taktzeiten: 0,1-0,5 Sekunden pro Verpackung
Sensorik und Überwachung:
- Drucksensoren zur Überwachung des Betriebsdrucks
- Durchflussmesser zur Kontrolle des Luftverbrauchs
- Partikelzähler zur kontinuierlichen Luftqualitätsüberwachung
Automatisierung:
- SPS-gesteuerte Ventilinseln für präzise Luftimpulse
- Reaktionszeit der Ventile: < 10 ms
Energieeffizienz und Nachhaltigkeit
Energiesparmaßnahmen:
- Bedarfsgerechte Drucklufterzeugung durch VSD-Kompressoren
- Optimierung der Ausblaszeit und des Druckniveaus
- Einsatz von Hocheffizienz-Düsen (z.B. Venturi-Düsen)
Luftverbrauchsoptimierung:
- Typischer Verbrauch: 0,2-0,5 Nl pro Verpackung
- Potenzielle Einsparung durch optimierte Düsen: 20-30%
Wärmerückgewinnung:
- Nutzung der Kompressorabwärme für Prozesswasser oder Raumheizung
- Rückgewinnungspotenzial: bis zu 80 kW bei einem 110 kW Kompressor
Qualitätssicherung und Hygiene
Mikrobiologische Kontrolle:
- Regelmäßige Luftkeimsammlung und Analyse
- Grenzwert: < 1 KBE/m³ für aseptische Abfüllungen
Inline-Qualitätsüberwachung:
- Kontinuierliche Taupunktmessung
- Online-Ölgehaltmessung (Photoionisationsdetektor)
- Partikelmessung mittels Laserspektrometer
Reinigung und Wartung:
- CIP-fähige Ausführung der Druckluftleitungen
- Periodische Heißluftsterilisation (130°C, 30 Minuten)
- Regelmäßiger Austausch von Filterelemente (typisch alle 3-6 Monate)
Herausforderungen und Lösungsansätze
- Problem: Kontaminationsrisiko durch Druckluft Lösung: Mehrstufige Luftaufbereitung und regelmäßige Qualitätskontrollen
- Problem: Hoher Energieverbrauch Lösung: Einsatz effizienter Düsen und bedarfsgerechte Drucklufterzeugung
- Problem: Ungleichmäßiges Ausblasen bei hohen Taktraten Lösung: Optimierte Düsengeometrie und präzise Ventilsteuerung
- Problem: Statische Aufladung der Verpackungen Lösung: Integration von Ionisierungsdüsen in das Ausblassystem
Innovative Ansätze und Zukunftstrends
- UV-C Behandlung der Druckluft zur Keimreduktion
- Wellenlänge: 254 nm
- Bestrahlungsdosis: 25-30 mJ/cm²
- Pulsierendes Luftströmungssystem
- Frequenz: 50-100 Hz
- Verbesserte Reinigungswirkung bei reduziertem Luftverbrauch
- KI-gestützte Prozessoptimierung
- Echtzeitanpassung von Druck und Volumenstrom basierend auf Produktionsparametern
- Prädiktive Wartung der Druckluftanlage
- Integration von Luftqualitätssensoren in jede Ausblaseinheit
- Echtzeit-Überwachung jeder einzelnen Verpackung
- Sofortige Aussortierung bei Qualitätsabweichungen
Wirtschaftliche Betrachtung
- Investitionskosten für ein Ausblassystem: 50.000 – 200.000 € (abhängig von Größe und Komplexität)
- Betriebskosten: 0,01 – 0,03 € pro 1000 ausgeblasene Verpackungen
- Amortisationszeit durch verhinderte Produktkontaminationen: typischerweise 1-2 Jahre
Fazit
Das Ausblasen von Verpackungen mit Druckluft ist ein kritischer Prozessschritt, der maßgeblich zur Produktqualität und -sicherheit beiträgt. Die Anforderungen an die Druckluftqualität und -versorgung sind hoch und erfordern ein durchdachtes Anlagenkonzept sowie ständige Überwachung. Durch den Einsatz moderner Technologien und innovativer Ansätze lässt sich der Prozess kontinuierlich optimieren, sowohl im Hinblick auf die Effizienz als auch auf die Qualität. Die Herausforderung für Ingenieure und Technologen besteht darin, ein System zu entwickeln und zu betreiben, das höchste Hygieneanforderungen erfüllt und gleichzeitig energie- und kosteneffizient arbeitet.
Oberflächentrocknung mit Druckluft in der Getränkeindustrie: Technische Aspekte und Anlagenkonzepte
Die effiziente Trocknung von Dosen und Flaschen nach dem Reinigungsprozess ist ein kritischer Schritt in der Getränkeproduktion. Druckluft spielt dabei eine zentrale Rolle, da sie eine schnelle, effektive und hygienische Methode zur Entfernung von Restwasser bietet.
Grundlagen der Drucklufttrocknung
Physikalische Prinzipien:
- Bernoulli-Effekt: Erzeugung von Unterdruck durch schnell strömende Luft
- Venturi-Effekt: Beschleunigung der Luftströmung durch Querschnittsverengung
Vorteile der Drucklufttrocknung:
- Kontaktlose Trocknung
- Hohe Effizienz bei geringem Energieeinsatz
- Schnelle Prozessgeschwindigkeiten (bis zu 120.000 Behälter/Stunde)
- Flexibilität bei verschiedenen Behälterformen
Druckluftanforderungen für die Oberflächentrocknung
Technische Spezifikationen:
- Druck: 4-7 bar (abhängig vom Düsendesign und Anwendung)
- Volumenstrom: 50-200 Nl/min pro Düse
- Luftqualität nach ISO 8573-1:
- Partikel: Klasse 1 (max. 0,1 μm und 0,1 mg/m³)
- Feuchte: Klasse 2 (Drucktaupunkt -40°C)
- Öl: Klasse 0 (weniger als 0,003 mg/m³)
Düsensysteme:
- Luftmesser (Air Knives):
- Länge: 50-2000 mm
- Luftaustrittsgeschwindigkeit: 200-300 m/s
- Energieeffizienz: ca. 70% im Vergleich zu Einzeldüsen
- Wirbelstromdüsen:
- Durchmesser: 10-50 mm
- Luftverstärkungsfaktor: 25:1 bis 40:1
- Geräuschpegel: 70-80 dBA
Drucklufterzeugung und -aufbereitung
Kompressorsystem:
- Ölfreier Schraubenkompressor (z.B. Atlas Copco ZR 110 VSD+, 110 kW)
- Frequenzumrichtersteuerung für bedarfsgerechte Luftproduktion
- Wärmerückgewinnung (Potenzial: bis zu 94% der elektrischen Eingangsleistung)
Luftaufbereitung:
- Nachkühler mit Zyklonabscheider
- Adsorptionstrockner im Wechselbetrieb (z.B. Atlas Copco BD 150+)
- Mehrstufige Filtration:
- Vorfilter (1 μm)
- Feinfilter (0,01 μm)
- Aktivkohlefilter zur Geruchsentfernung
- Sterilfilter (HEPA H14) als letzte Stufe vor Produktkontakt
Anlagenkonzept für die Oberflächentrocknung
Hauptkomponenten:
- Drucklufterzeugung und -aufbereitung
- Druckluftverteilungssystem
- Trocknungsstation mit Luftmessern oder Wirbelstromdüsen
- Fördersystem für Dosen/Flaschen (typisch: 1-2 m/s)
- Steuerungssystem mit SPS
Prozessablauf:
- Vorreinigung mit Wasserdüsen
- Erste Trocknungsstufe mit Hochdruck-Luftmessern (6-7 bar)
- Zweite Trocknungsstufe mit Niederdruck-Luftmessern (4-5 bar)
- Optionale dritte Stufe für kritische Bereiche (z.B. Dosenränder)
Energieeffizienz und Optimierung
Energiesparmaßnahmen:
- Einsatz von VSD-Kompressoren (Energieeinsparung: bis zu 35%)
- Optimierung des Systemdrucks (1 bar Drucksenkung ≈ 7% Energieeinsparung)
- Wärmerückgewinnung aus Kompressorabwärme
- Verwendung von hocheffizienten Motoren (IE4-Klasse)
Luftverbrauchsoptimierung:
- Präzise Düsenausrichtung (Luftverbrauchsreduktion bis zu 30%)
- Einsatz von Luftsparventilen (automatische Abschaltung bei Lücken)
- Sequenzielle Aktivierung von Trocknungszonen
Prozessüberwachung und Qualitätssicherung
Messtechnik:
- Inline-Feuchtigkeitssensoren (kapazitiv oder optisch)
- Hochgeschwindigkeitskameras zur Oberflächeninspektion
- Drucktaupunktmessung in der Druckluftleitung
Qualitätskontrolle:
- Stichprobenartige Gewichtskontrolle zur Restfeuchtigkeitsbestimmung
- Mikrobiologisches Monitoring der Druckluft (max. 100 KBE/m³)
- Regelmäßige Überprüfung der Filterintegrität
Herausforderungen und Lösungsansätze
- Problem: Ungleichmäßige Trocknung bei hohen Geschwindigkeiten Lösung: Mehrstufiges Trocknungskonzept mit optimierter Düsengeometrie
- Problem: Hoher Energieverbrauch Lösung: Implementierung eines Energiemanagementsystems nach ISO 50001
- Problem: Kontaminationsrisiko durch Druckluft Lösung: Einsatz von Sterilfiltern und regelmäßige Luftqualitätsüberwachung
- Problem: Lärmentwicklung Lösung: Verwendung von Schalldämpfern und lärmarmen Düsen (Reduktion um 10-15 dBA möglich)
Innovative Ansätze
- Pulsierendes Luftsystem:
- Frequenz: 10-50 Hz
- Verbesserung der Trocknungseffizienz um bis zu 20%
- Elektrostatisch unterstützte Trocknung:
- Erzeugung eines elektrischen Felds zur Wasserabstoßung
- Reduzierung des Luftverbrauchs um bis zu 40%
- KI-basierte Prozessoptimierung:
- Echtzeitanpassung der Trocknungsparameter basierend auf Produkttyp und Umgebungsbedingungen
- Potenzielle Effizienzsteigerung von 10-15%
Wirtschaftliche Betrachtungen
- Investitionskosten:
- Druckluftsystem: 100.000 – 500.000 € (abhängig von Größe und Komplexität)
- Trocknungsstation: 50.000 – 200.000 € pro Linie
- Betriebskosten:
- Energiekosten: 0,01 – 0,02 € pro 1000 Behälter
- Wartungskosten: ca. 5-7% der Investitionskosten pro Jahr
- Amortisationszeit:
- Typisch 2-4 Jahre bei Neuanlagen
- 1-2 Jahre bei Nachrüstung ineffizienter Systeme
Fazit
Die Oberflächentrocknung mit Druckluft ist ein komplexer Prozess, der sorgfältige Planung und kontinuierliche Optimierung erfordert. Durch den Einsatz moderner Technologien und innovativer Ansätze lassen sich signifikante Verbesserungen in Bezug auf Effizienz, Qualität und Nachhaltigkeit erzielen. Die Herausforderungen liegen in der Balance zwischen hoher Trocknungsleistung, Energieeffizienz und der Einhaltung strenger Hygienestandards. Für Ingenieure und Technologen in der Getränkeindustrie bleibt die Optimierung der Oberflächentrocknung ein wichtiges Feld für Innovation und kontinuierliche Verbesserung.
Druckluftanwendung beim Mischen von Schüttgütern in der Lebensmittelindustrie
Das Mischen von Schüttgütern mithilfe von Druckluft ist eine effiziente und schonende Methode, die in der Lebensmittelindustrie häufig Anwendung findet. Diese Technik nutzt die Energie der komprimierten Luft, um eine homogene Vermischung verschiedener pulverförmiger oder granularer Materialien zu erreichen.
Grundprinzip der druckluftgestützten Mischung
Bei diesem Verfahren wird Druckluft in einen Behälter mit Schüttgütern eingeblasen. Die einströmende Luft erzeugt Turbulenzen und Verwirbelungen, die das Material in Bewegung setzen und durchmischen. Die Effizienz dieses Prozesses hängt maßgeblich von der Qualität und den Eigenschaften der verwendeten Druckluft ab.
Druckluftanforderungen für effizientes Mischen
Technische Spezifikationen:
- Druck: 2-6 bar (abhängig von Produkteigenschaften und Behältergröße)
- Volumenstrom: 0,1-1 m³/min pro m³ Behältervolumen
- Luftqualität nach ISO 8573-1:
- Partikel: Klasse 1 (max. 0,1 μm und 0,1 mg/m³)
- Feuchte: Klasse 2 (Drucktaupunkt -40°C)
- Öl: Klasse 0 (weniger als 0,003 mg/m³)
Drucklufterzeugung und -aufbereitung:
- Ölfreier Schraubenkompressor (z.B. Atlas Copco ZR 110, 110 kW)
- Frequenzumrichtersteuerung für bedarfsgerechte Luftlieferung
- Mehrstufige Luftaufbereitung:
- Nachkühler mit Zyklonabscheider
- Adsorptionstrockner (z.B. Atlas Copco BD 100+)
- Feinfilter (0,01 μm)
- Aktivkohlefilter zur Geruchsneutralisierung
- Sterilfilter (HEPA H14) als finale Stufe
Mischsysteme und Drucklufteinbringung
1. Wirbelschichtmischer
- Funktionsprinzip: Fluidisierung des Schüttguts durch Druckluft von unten
- Luftverteilung: Poröser Boden oder Düsenplatten
- Luftdruck: 0,2-0,5 bar über dem Fluidisierungspunkt
- Luftmenge: 0,1-0,3 m³/min pro m² Bodenfläche
2. Pneumatischer Mischer mit Luftlanzen
- Funktionsprinzip: Einblasen von Druckluft durch Lanzen im Mischbehälter
- Lanzenkonfiguration: 3-6 Lanzen pro m³ Behältervolumen
- Luftdruck an den Lanzen: 2-4 bar
- Pulsierende Luftzufuhr: Frequenz 1-10 Hz für verbesserte Mischwirkung
3. Strahlschichtmischer
- Funktionsprinzip: Kombination aus Wirbelschicht und gerichteten Luftstrahlen
- Lufteintrag: Zentrale Düse und Randdüsen
- Druckbereich: 1-3 bar für Zentraldüse, 0,5-1 bar für Randdüsen
- Luftmengenverteilung: 60% Zentraldüse, 40% Randdüsen
Prozesssteuerung und Optimierung
- Druckregelung:
- Proportionalventile zur präzisen Druckeinstellung
- Reaktionszeit: < 100 ms
- Genauigkeit: ±0,1 bar
- Durchflussmessung:
- Thermische Massendurchflussmesser (z.B. Endress+Hauser t-mass F/I)
- Messbereich: 0,5-1000 Nm³/h
- Genauigkeit: ±1% vom Messwert
- Feuchtigkeitsüberwachung:
- Taupunktsensoren in der Druckluftleitung
- Messbereich: -60°C bis +20°C Taupunkt
- Genauigkeit: ±2°C Taupunkt
- Partikelmonitoring:
- Online-Partikelzähler zur kontinuierlichen Luftqualitätsüberwachung
- Messbereich: 0,1-5,0 μm
- Empfindlichkeit: 1 Partikel pro Liter
Energieeffizienz und Nachhaltigkeit
- Wärmerückgewinnung aus der Kompressorabwärme:
- Nutzung für Raumheizung oder Prozesswärme
- Potenzielle Energieeinsparung: bis zu 75% der elektrischen Eingangsleistung
- Bedarfsgerechte Drucklufterzeugung:
- Frequenzumrichtergesteuerte Kompressoren
- Lastanpassung im Bereich 20-100%
- Energieeinsparung gegenüber konventionellen Systemen: 20-35%
- Druckluft-Energiemonitoring:
- Echtzeitüberwachung des spezifischen Energieverbrauchs
- Typischer Zielwert: 0,1-0,15 kWh/m³ erzeugter Druckluft
Herausforderungen und Lösungsansätze
- Problem: Ungleichmäßige Luftverteilung Lösung: CFD-Simulation zur Optimierung der Düsenanordnung und Luftströme
- Problem: Produktanhaftungen an Mischerwänden Lösung: Intermittierende Luftstöße mit höherem Druck (4-6 bar) zur Wandreinigung
- Problem: Staubentwicklung Lösung: Unterdruck im Mischbehälter und Staubabsaugung mit Filtereinheit
- Problem: Entmischung bei unterschiedlichen Partikelgrößen Lösung: Anpassung der Luftmenge und -geschwindigkeit an die Fluidisierungspunkte der Komponenten
Innovative Ansätze
- Pulsierende Druckluftzufuhr:
- Frequenzbereich: 1-50 Hz
- Verbesserung der Mischwirkung um bis zu 30%
- Reduzierung der Mischzeit um 20-40%
- Elektrostatische Unterstützung:
- Aufladung der Partikel zur Verbesserung der Dispergierung
- Reduzierung der benötigten Luftmenge um 10-20%
- Ultraschall-unterstützte Fluidisierung:
- Frequenzbereich: 20-40 kHz
- Verbesserung der Fließeigenschaften kohäsiver Pulver
- Reduzierung der erforderlichen Luftmenge um bis zu 25%
Qualitätssicherung und Hygiene
- Inline-Probennahme:
- Pneumatische Probennehmer mit Druckluftspülung
- Repräsentative Probennahme aus verschiedenen Behälterzonen
- CIP-Reinigung:
- Druckluftunterstützte Reinigungsdüsen
- Luftdruck für Reinigungsdüsen: 2-3 bar
- Ausblasen von Restfeuchtigkeit mit steriler Druckluft
- Sterilisation der Druckluftleitungen:
- Periodische Heißluftsterilisation (130°C, 30 Minuten)
- Alternativ: Ozonbehandlung der Druckluft (0,1-0,2 ppm)
Fazit
Die Anwendung von Druckluft beim Mischen von Schüttgütern in der Lebensmittelindustrie bietet zahlreiche Vorteile hinsichtlich Effizienz, Produktqualität und Flexibilität. Die präzise Steuerung der Druckluftparameter, kombiniert mit innovativen Technologien, ermöglicht eine optimale Anpassung an verschiedene Produktanforderungen. Die Herausforderungen liegen in der Gewährleistung einer konstant hohen Druckluftqualität, der Optimierung des Energieverbrauchs und der Einhaltung strenger Hygienestandards. Durch den Einsatz moderner Steuerungs- und Überwachungssysteme können diese Herausforderungen effektiv bewältigt werden, was zu einer verbesserten Produktqualität und Prozesseffizienz führt.
Aerierung von Schokolade: Druckluftqualität und Anlagenaufbau
Die Aerierung von Schokolade ist ein entscheidender Prozess in der Süßwarenindustrie, der die Textur und den Geschmack des Endprodukts maßgeblich beeinflusst. Die Qualität der verwendeten Druckluft und der Aufbau der Druckluftanlage spielen hierbei eine zentrale Rolle für die Produktqualität und die Effizienz des Verfahrens.
Grundlagen der Schokoladenaerierung
Bei der Aerierung wird Luft in die flüssige Schokoladenmasse eingebracht, um eine poröse Struktur zu erzeugen. Dies resultiert in einer leichteren Textur und kann den Geschmack intensivieren. Typische Produkte sind Luftschokolade oder Schokoriegel mit luftiger Füllung.
Anforderungen an die Druckluftqualität
Die Druckluftqualität ist von höchster Bedeutung, da die Luft direkt mit dem Lebensmittel in Kontakt kommt. Die Anforderungen übersteigen sogar die strengen Normen der ISO 8573-1:2010 für die Lebensmittelindustrie.
Spezifikationen:
- Partikel:
- Klasse 1 oder besser
- Maximal 0,1 μm und 0,1 mg/m³
- Verwendung von HEPA-Filtern (H13 oder H14)
- Feuchtigkeit:
- Klasse 2 oder besser
- Drucktaupunkt mindestens -40°C
- Verhindert Kondensation und mikrobielles Wachstum
- Ölgehalt:
- Klasse 0
- Absolut ölfrei (< 0,003 mg/m³)
- Vermeidung jeglicher Geschmacksbeeinträchtigung
- Mikrobiologische Reinheit:
- Keimzahl < 1 KBE/m³
- Einsatz von Sterilfiltern unmittelbar vor dem Prozess
- Geruch:
- Absolut geruchsneutral
- Aktivkohlefilter zur Entfernung von Geruchsstoffen
Aufbau der Druckluftanlage für Schokoladenaerierung
Eine typische Anlage zur Erzeugung von Druckluft für die Schokoladenaerierung besteht aus folgenden Komponenten:
- Luftansaugung:
- HEPA-Filter für Ansaugluft (F9 nach EN 779)
- Wettergeschützte Ansaugung, mind. 3m über Bodenniveau
- Kompressor:
- Ölfrei verdichtender Schraubenkompressor (z.B. Atlas Copco ZR 75, 75 kW)
- Wassereinspritzung zur Kühlung statt Öl
- Frequenzumrichter für energieeffiziente Regelung
- Nachkühler:
- Edelstahl-Wärmetauscher
- Kühlung auf 3°C über Umgebungstemperatur
- Druckluftbehälter:
- Volumen: ca. 2000 Liter
- Innen beschichtet zur Vermeidung von Korrosion
- Aufbereitung: a) Kältetrockner:
- Drucktaupunkt +3°C b) Adsorptionstrockner:
- Drucktaupunkt -40°C
- Wärmeloser Regenerationsprozess c) Filterkaskade:
- Vorfilter (1 μm)
- Feinfilter (0,01 μm)
- Aktivkohleadsorber
- Staubfilter (1 μm) d) Sterilfilter:
- HEPA H14 (99,995% Abscheidung bei 0,1 μm)
- Membranfilter direkt vor Prozesseinbindung
- Leitungssystem:
- Edelstahlrohre (1.4571) mit Orbital-Schweißnähten
- Hygienische Kugelhähne und Ventile
- Monitoring:
- Kontinuierliche Überwachung von Druck, Temperatur, Feuchtigkeit
- Partikelzähler zur Kontrolle der Luftreinheit
- Durchflussmessung mit Massenstrommesser
Prozessintegration und Steuerung
Die Einbringung der Druckluft in die Schokoladenmasse erfolgt über spezielle Düsensysteme:
- Düsendesign:
- Mehrkanal-Düsen für feine Luftverteilung
- Materialpaarung zur Vermeidung von Abrieb
- Druckregelung:
- Präzise Regelventile (Genauigkeit ±0,1 bar)
- Druckbereich: typisch 2-6 bar, produktabhängig
- Durchflussregelung:
- Massendurchflussregler für reproduzierbare Luftmengen
- Typischer Bereich: 5-50 Nl/min pro Düse
- Temperaturkontrolle:
- Erwärmung der Druckluft auf Produkttemperatur (ca. 30-40°C)
- Verwendung von ATEX-zertifizierten Lufterhitzern
Energieeffizienz und Nachhaltigkeit
Energiesparmaßnahmen bei der Drucklufterzeugung für die Schokoladenaerierung:
- Wärmerückgewinnung:
- Nutzung der Kompressorabwärme zur Vortemperierung der Schokolade
- Potenzial: bis zu 75% der elektrischen Antriebsenergie
- Druckoptimierung:
- Minimierung des Systemdrucks (jede Reduktion um 1 bar spart ca. 6-8% Energie)
- Leckagemanagement:
- Regelmäßige Ultraschall-Leckageortung
- Ziel: Leckagerate < 5% des Gesamtverbrauchs
- Bedarfsgerechte Erzeugung:
- Kaskadenschaltung mehrerer Kompressoren
- Nutzung der Frequenzregelung für Grundlastkompressor
Qualitätssicherung und Hygiene
Maßnahmen zur Sicherstellung der Druckluftqualität:
- Regelmäßige Probenahme:
- Monatliche mikrobiologische Untersuchung
- Vierteljährliche Analyse auf Öl- und Partikelgehalt
- Wartungsintervalle:
- Sterilfilter: Wechsel alle 3 Monate
- Aktivkohlefilter: Austausch halbjährlich
- Kompressorwartung: Nach Herstellervorgaben, mindestens jährlich
- Reinigungskonzept:
- CIP-fähige Ausführung der produktnahen Komponenten
- Jährliche Grundreinigung des gesamten Systems
- Dokumentation:
- Lückenlose Aufzeichnung aller Qualitätsparameter
- Integration in das HACCP-Konzept des Betriebs
Herausforderungen und Zukunftsperspektiven
- Energieeffizienz:
- Entwicklung noch effizienterer Kompressortechnologien
- Integration von KI zur prädiktiven Wartung und Optimierung
- Produktinnovation:
- Feinere Kontrolle der Luftblasengrößen für neue Texturen
- Kombination von Aerierung mit Aromatisierung
- Nachhaltigkeit:
- Untersuchung alternativer Gase (z.B. Stickstoff aus Luftzerlegung)
- Entwicklung von Niederdrucksystemen zur Energieeinsparung
Fazit
Die Aerierung von Schokolade stellt höchste Anforderungen an die Qualität der Druckluft und den Aufbau der Druckluftanlage. Durch die Kombination modernster Filtertechnologien, präziser Steuerungssysteme und strenger Hygienekonzepte lässt sich eine Luftqualität erreichen, die den sensiblen Anforderungen der Schokoladenproduktion gerecht wird. Die kontinuierliche Optimierung des Systems hinsichtlich Energieeffizienz und Produktqualität bleibt eine zentrale Aufgabe für Ingenieure und Qualitätsmanager in der Süßwarenindustrie.