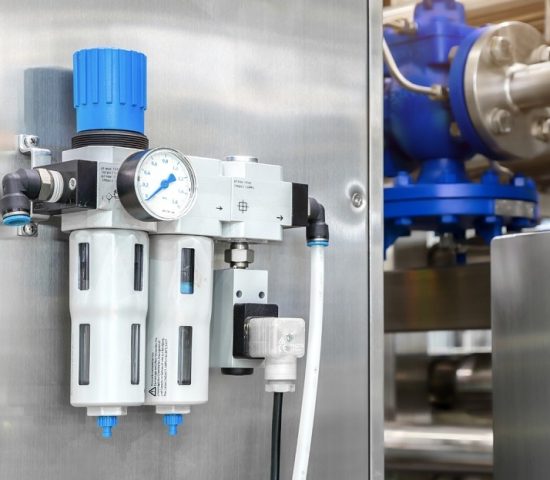
REINHEIT DER DRUCKLUFT
Wir prüfen die Reinheit der Druckluft auf folgende Parameter::
- Partikelgehalt,
- Wassergehalt / Drucktaupunkt,
- Öl-Aerosol-Gehalt,
- Bakterien-, Hefe- und Schimmelpilzgehalt.
Die Messungen führen wir an folgenden Tagen durch: Donnerstag-Freitag (in ganz Deutschland)
Die Zeit, die für die Messungen an einem Messpunkt benötigt wird: 40-60 Minuten
Anfragen und Bestellungen: labor@qualifizierung-validierung.de
ISO 8573-1 ist eine weithin anerkannte Norm zur Beurteilung der Reinheit der Druckluft aufgrund des Gehalts an drei Verunreinigungen: Partikel, Wasser und Öl. Probenahmemethoden und die Messungen selbst werden in den nachfolgenden Abschnitten der ISO-Norm 8573 (-2, -3, -4) ausführlich beschrieben. Ihre Anwendung ist obligatorisch, wenn die erzielten Messergebnisse mit den in der ISO 8573-1 beschriebenen Reinheitsklassen für Druckluft verglichen werden sollen. In einigen Branchen wird die Druckluftreinheit auch auf mikrobiologische Verunreinigungen geprüft, wobei diese Prüfungen nicht die Grundlage für die Klassifizierung der Reinheit Druckluft nach ISO 8573-1 bilden, sondern sie nur ergänzen.
Prüfungen der Druckluftreinheit werden in der Regel für solche Teile der Anlage durchgeführt, in denen die Druckluft: – direkt mit dem Produkt/Material in Berührung kommt (Lebensmittel, Kosmetika, Arzneimittel, Medizinprodukte [eng. medical devices]), – mit kontaminationsempfindlichen Geräten (Laborgeräte, optische Systeme, Laser) verbunden ist, – in die Umwelt freigesetzt wird und zur Steigerung der Partikelzahl im Reinraum [eng. cleanroom] beiträgt.
Die Klassifizierung der Reinheit Druckluft erfolgt üblicherweise an Messstellen, die sich in den letzten Abschnitten des Druckluftverteilungssystems befinden. Manchmal werden zusätzliche Proben im Kompressorraum entnommen, jedoch immer nach der Druckluftaufbereitungsanlage (nach den Filtern). Durch die Prüfung der Druckluftreinheit an 3-4 Messstellen kann in der Regel bereits eine zuverlässige Beurteilung der Reinheit der Druckluft vorgenommen werden. Zur Prüfung von Druckluft nach ISO 8573-1 ist der Anschluss an ein Drucksystem erforderlich. Es ist nicht möglich, die Reinheit Druckluft des in die Umgebung abgegebenen Gases zu überprüfen (siehe unten erforderliche Anschlussarten auf der Anlagenseite).
In der Regel beginnt die Testphase neuer Druckluftinstallationen mit intensiven Untersuchungen im ersten Monat der Nutzung. Hierbei werden üblicherweise drei Tests zu verschiedenen Tagen durchgeführt, um eine anfängliche Bestandsaufnahme der Druckluftreinheit sicherzustellen und eventuelle Unregelmäßigkeiten frühzeitig zu identifizieren. Nach dieser ersten intensiven Testphase schließt sich eine jährliche Überprüfung über die nächsten drei Jahre an. Diese jährlichen Tests dienen dazu, die Konstanz der Reinheit der Druckluft zu überwachen und sicherzustellen, dass die Installation weiterhin den in der ISO 8573-1 festgelegten Reinheitsklassen entspricht. Falls nach drei Jahren Nutzung die bisherigen Testergebnisse stets innerhalb der akzeptierten Kriterien lagen, kann das Prüfintervall auf eine zweijährige Basis ausgedehnt werden.
ISO 8573-1: Grenzwerte
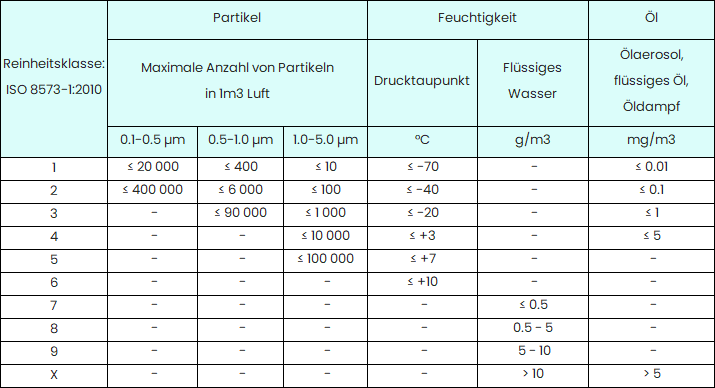
GEPRÜFTE PARAMETER
PARTIKEL
Messmethode: ISO 8573-4:2019
Messbereich: Messung von Partikeln im Bereich 0,1 - 0,5 µm (Klassen 1-7 nach ISO 8573-1)
Messausrüstung: Laser-Partikelzähler
WASSER
Messmethode: ISO 8573-3:2010
Messbereich: –70 … +30°C td
Messunsicherheit: ±2°C
Messausrüstung: Drucktaupunktmessgerät
ÖL-AEROSOL
Messmethode: ISO 8573-2:2007
Messbereich: 0,003 – 2mg/1m3
Messunsicherheit: ±10%
Messausrüstung: Filtrationskit, FTIR
MIKROBIOLOGIE
Messmethode: ISO 8573-7:2003
Geprüfte Parameter: Gehalt an Bakterien, Hefen, Schimmelpilzen in 1 m3 Luft
Messausrüstung: Druckluftprüfgerät, Anzucht der Kolonien in Petrischalen
TECHNISCHE ANFORDERUNEN
ÜBERPRÜFEN SIE, BEVOR SIE EINE BESTELLUNG AUFGEBEN
KUNDENSEITIGE ANSCHLÜSSE
Schnellkupplung DN 7.2
Gewindekupplung 1/2' oder 3/8' (Innengewinde)
Leitung 6, 8, 10, 12 oder 16mm (Außendurchmesser)
ANLAGEDRUCK
Maximal 7,3 bar
UMGEBUNGSTEMPERATUR
Minimum 10°C
LAGE DER MESSSTELLE
1 Gereinigte Druckluft
Die Partikelzahl kann nur in Gas gemessen werden, das auf den Filtern gereinigt wurde. Es ist nicht möglich, vor den Filtern zu messen.
2. Leicht zugänglicher Raum
Die Messgeräte sind stoßempfindlich und wiegen mehr als 20 kg, weshalb sie z. B. nicht auf einer Leiter, auf Tanks usw. getragen werden dürfen.
ZEIT DER PROBENAHME
Die Durchführung der Testreihe an einer Messstelle dauert etwa 45-60 Minuten.
BERICHTERSTATTUNG
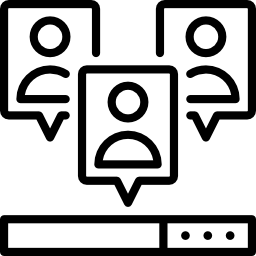
AUF DEUTSCH
UND ENGLISCH
Standardmäßig erstellen wir den Bericht in einer zweisprachigen Version: Deutsch-Englisch.
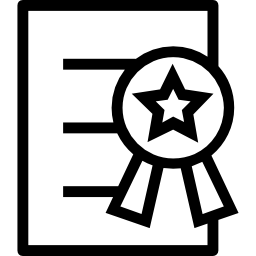
IM EINKLANG MIT DEN
GMP-GRUNDSÄTZEN
Der Bericht enthält u. a. die Angaben zu den verwendeten Geräten und der an den Prüfungen beteiligten Personen.
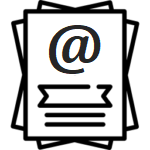
ELEKTRONISCHE
ÜBERMITTLUNG
Der Bericht wird in elektronischer Form
(PDF-Dokument) übermittelt.
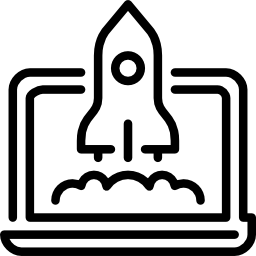
IN DER REGEL INNERHALB
VON 14-21 TAGEN FERTIG
In der Regel wird der Bericht innerhalb von 14 Tagen
(maximal 21 Tagen) nach der Messung übermittelt.
DIESE KUNDEN HABEN UNS BEREITS VERTRAUT
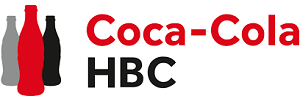
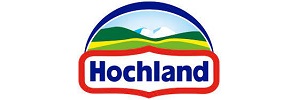
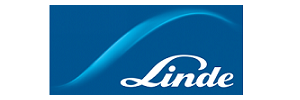
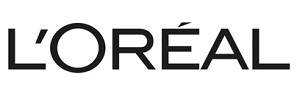
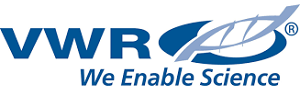
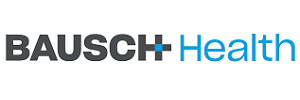
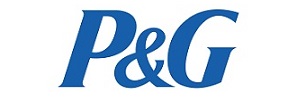
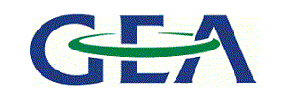
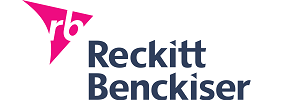
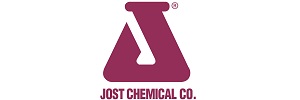
PREISLISTE
Möchten Sie schnell die Kosten für die Durchführung von Messungen abschätzen?
In der Preisliste finden Sie:
– Informationen über die von uns durchgeführten Messungen
– Preise der Untersuchungen
EIN GENAUES ANGEBOT ANFORDERN
Leitfaden zur Reinheit der Druckluft - Teil 1
Die Reinheit der Druckluft ist ein entscheidendes Element in vielen industriellen Prozessen, insbesondere in der Lebensmittelproduktion und in sensiblen Fertigungsumgebungen. Dieser Leitfaden soll Qualitätsmanagern, Investitionsleitern, Instandhaltungsmanagern und Auditoren für Lebensmittelsicherheitsmanagementsysteme ein tiefgreifendes Verständnis für die Bedeutung, die Anforderungen und die Methoden zur Sicherstellung der Druckluftreinheit vermitteln.
Bedeutung der Druckluftreinheit
Druckluft findet in der Industrie vielfältige Anwendungen, von der Steuerung pneumatischer Systeme bis hin zum direkten Kontakt mit Produkten. In der Lebensmittelindustrie kann sie beispielsweise zur Verpackung, zum Transport von Rohstoffen oder zur Reinigung von Anlagen eingesetzt werden. Die Reinheit der Druckluft ist daher von höchster Bedeutung, da Verunreinigungen zu Produktkontaminationen, Qualitätsminderungen oder sogar Gesundheitsrisiken für Verbraucher führen können.
Quellen von Verunreinigungen
Um die Reinheit der Druckluft effektiv zu gewährleisten, ist es wichtig, die potenziellen Verunreinigungsquellen zu verstehen. Diese können in verschiedene Kategorien eingeteilt werden:
Umgebungsluft: Die Ansaugluft des Kompressors enthält bereits Verunreinigungen wie Staub, Mikroorganismen und Feuchtigkeit.
Kompressor: Während des Kompressionsvorgangs können Öl, Abrieb und andere Partikel in die Druckluft gelangen.
Druckluftsystem: Rohrleitungen, Ventile und andere Komponenten können Rost, Ablagerungen oder Mikroorganismen beherbergen.
Nachgeschaltete Komponenten: Filter, Trockner und andere Aufbereitungseinheiten können bei unsachgemäßer Wartung selbst zu Kontaminationsquellen werden.
Arten von Verunreinigungen
Die Verunreinigungen in Druckluft lassen sich in drei Hauptkategorien unterteilen:
Feste Partikel: Hierzu gehören Staub, Abrieb, Fasern und andere mikroskopisch kleine Festkörper.
Wasser: In Form von Flüssigkeit oder Dampf kann Wasser zu Korrosion, Bakterienwachstum und Produktschäden führen.
Öl: Sowohl in flüssiger als auch in Dampfform kann Öl aus dem Kompressor oder anderen Quellen stammen und Produkte kontaminieren.
Leitfaden zur Reinheit der Druckluft - Teil 2
Anforderungen und Normen für Druckluftreinheit
Die Anforderungen an die Reinheit der Druckluft variieren je nach Anwendungsbereich und Industrie. In der Lebensmittelindustrie und anderen sensiblen Produktionsbereichen gelten besonders strenge Vorschriften. Es ist wichtig, dass Qualitätsmanager, Investitionsleiter und Instandhaltungsmanager mit den relevanten Normen und Richtlinien vertraut sind.
ISO 8573-1: Die Grundlage der Druckluftreinheitsklassifizierung
Die internationale Norm ISO 8573-1 bildet die Grundlage für die Klassifizierung der Druckluftreinheit. Sie definiert Reinheitsklassen für die drei Hauptverunreinigungen: feste Partikel, Wasser und Öl. Die Norm verwendet ein System von Klassen von 0 bis 6, wobei 0 die höchste Reinheit darstellt.
Für feste Partikel berücksichtigt die Norm sowohl die Anzahl als auch die Größe der Partikel. Bei Wasser wird der Drucktaupunkt oder der Wassergehalt gemessen. Für Öl wird der Gesamtölgehalt, einschließlich Aerosole und Dampf, berücksichtigt.
Ein Beispiel für eine Druckluftqualität nach ISO 8573-1 könnte [1:2:1] sein, was bedeutet:
Klasse 1 für feste Partikel
Klasse 2 für Wasser
Klasse 1 für Öl
Branchenspezifische Anforderungen
In der Lebensmittelindustrie gelten oft strengere Anforderungen, die über die ISO 8573-1 hinausgehen. Beispielsweise fordern viele Lebensmittelsicherheitsstandards wie IFS Food, BRC Food oder FSSC 22000 eine regelmäßige Überprüfung und Dokumentation der Druckluftqualität.
Die Europäische Hygienic Engineering & Design Group (EHEDG) hat Richtlinien für die Verwendung von Druckluft in Kontakt mit Lebensmitteln herausgegeben. Diese empfehlen in der Regel mindestens die Klasse [1:2:1] nach ISO 8573-1, wobei in einigen Fällen sogar höhere Reinheitsgrade erforderlich sein können.
Pharmazeutische und medizinische Anwendungen
Für pharmazeutische und medizinische Anwendungen gelten noch strengere Anforderungen. Hier kommen oft die Richtlinien der Europäischen Arzneimittelagentur (EMA) oder der US Food and Drug Administration (FDA) zum Tragen. In diesen Bereichen kann eine Klassifizierung von [1:1:1] oder sogar [0:0:0] nach ISO 8573-1 erforderlich sein.
Energieeffizienz und Umweltaspekte
Neben den Reinheitsanforderungen spielen auch Aspekte der Energieeffizienz und Umweltfreundlichkeit eine zunehmend wichtige Rolle. Die Europäische Union hat mit der Ökodesign-Richtlinie (2009/125/EG) Anforderungen an die Energieeffizienz von Druckluftsystemen festgelegt. Qualitäts- und Instandhaltungsmanager sollten diese Aspekte bei der Planung und dem Betrieb von Druckluftsystemen berücksichtigen.
Dokumentation und Nachweisführung
Für Auditoren von Lebensmittelsicherheitsmanagementsystemen ist die korrekte Dokumentation der Druckluftqualität von entscheidender Bedeutung. Unternehmen müssen nachweisen können, dass sie:
Die Druckluftqualität regelmäßig überwachen und dokumentieren.
Geeignete Maßnahmen zur Aufrechterhaltung der erforderlichen Reinheitsklasse implementiert haben.
Ein Risikomanagement-System für potenzielle Kontaminationen durch Druckluft etabliert haben.
Schulungen für relevantes Personal durchführen, um das Bewusstsein für die Bedeutung der Druckluftreinheit zu schärfen.
Leitfaden zur Reinheit der Druckluft - Teil 3
Technische Lösungen und Methoden zur Sicherstellung der Druckluftreinheit
Um die erforderliche Reinheit der Druckluft zu erreichen und aufrechtzuerhalten, ist ein ganzheitlicher Ansatz erforderlich, der die gesamte Druckluftkette von der Erzeugung bis zum Verbrauch berücksichtigt. In diesem Abschnitt werden wir die wichtigsten technischen Lösungen und Methoden erörtern.
Kompressoren und Drucklufterzeugung
Die Wahl des richtigen Kompressors ist der erste Schritt zur Sicherstellung einer hohen Druckluftqualität. Ölfreie Kompressoren sind in vielen Fällen die bevorzugte Wahl, insbesondere in der Lebensmittel- und Pharmaindustrie. Sie eliminieren von vornherein die Gefahr einer Ölkontamination. Allerdings können auch öl-geschmierte Kompressoren in Kombination mit entsprechenden Filtersystemen eine ausreichende Luftqualität liefern.
Moderne Schraubenkompressoren mit variabler Drehzahlregelung bieten nicht nur eine hohe Energieeffizienz, sondern auch eine gleichmäßigere Luftversorgung, was sich positiv auf die Luftqualität auswirken kann. Bei der Auswahl des Kompressors sollten Faktoren wie Kapazität, Effizienz und Wartungsfreundlichkeit berücksichtigt werden.
Luftaufbereitung
Nach der Kompression durchläuft die Druckluft in der Regel mehrere Aufbereitungsstufen:
Nachkühler: Direkt nach dem Kompressor kühlt ein Nachkühler die verdichtete Luft ab. Dies führt zur Kondensation eines Großteils der Feuchtigkeit, die dann abgeschieden werden kann.
Drucklufttrockner: Zur weiteren Reduzierung der Feuchtigkeit kommen verschiedene Arten von Trocknern zum Einsatz:
Kältetrockner sind energieeffizient und erreichen Drucktaupunkte von etwa +3°C.
Adsorptionstrockner können sehr niedrige Drucktaupunkte bis zu -70°C erreichen, benötigen aber mehr Energie.
Membrantrockner sind kompakt und wartungsarm, eignen sich aber eher für kleinere Luftmengen.
Filtersysteme: Ein mehrstufiges Filtersystem ist entscheidend für die Entfernung von Partikeln, Öl und anderen Verunreinigungen:
Vorfilter entfernen gröbere Partikel und schützen nachfolgende Komponenten.
Feinfilter können Partikel bis zu 0,01 µm zurückhalten.
Aktivkohlefilter entfernen Öldämpfe und Gerüche.
Sterilfilter kommen zum Einsatz, wenn höchste Reinheit erforderlich ist, z.B. in der Pharmazie.
Rohrleitungssystem
Das Rohrleitungssystem spielt eine oft unterschätzte Rolle bei der Aufrechterhaltung der Luftqualität:
Materialauswahl: Edelstahl oder Aluminium sind korrosionsbeständig und reduzieren die Gefahr von Verunreinigungen.
Ringförmige Anordnung: Ein Ringleitungssystem ermöglicht eine gleichmäßige Druckverteilung und reduziert Druckverluste.
Gefälle und Kondensatableiter: Ein leichtes Gefälle in Fließrichtung und strategisch platzierte Kondensatableiter helfen, Feuchtigkeit effektiv abzuführen.
Überwachung und Kontrolle
Ein kontinuierliches Monitoring der Druckluftqualität ist unerlässlich:
Online-Messgeräte: Sensoren zur kontinuierlichen Überwachung von Partikeln, Feuchtigkeit und Ölgehalt ermöglichen eine Echtzeitkontrolle der Luftqualität.
Regelmäßige Probenahmen und Laboranalysen: Diese ergänzen die Online-Überwachung und bieten eine detailliertere Analyse.
Dokumentation: Alle Messergebnisse sollten sorgfältig dokumentiert werden, um Trends zu erkennen und für Audits vorbereitet zu sein.
Wartung und Instandhaltung
Ein gut geplantes Wartungsprogramm ist entscheidend für die langfristige Aufrechterhaltung der Druckluftqualität:
Regelmäßiger Filterwechsel: Basierend auf Herstellerempfehlungen und tatsächlichem Verschmutzungsgrad.
Inspektion und Reinigung: Regelmäßige Überprüfung des gesamten Systems auf Lecks, Korrosion oder andere Probleme.
Kalibrierung von Messinstrumenten: Sicherstellung der Genauigkeit aller Überwachungsgeräte.
Schulung des Personals: Regelmäßige Schulungen für Bediener und Wartungspersonal zur Sensibilisierung für die Bedeutung der Druckluftreinheit.
Leitfaden zur Reinheit der Druckluft - Teil 4
Implementierung eines ganzheitlichen Managementsystems für die Druckluftreinheit
Die Sicherstellung der Druckluftreinheit erfordert mehr als nur technische Lösungen. Ein ganzheitliches Managementsystem ist notwendig, um alle Aspekte der Druckluftqualität effektiv zu steuern und kontinuierlich zu verbessern. In diesem Abschnitt werden wir die Schlüsselelemente eines solchen Systems betrachten.
Risikobewertung und HACCP
Die Anwendung von Prinzipien des Hazard Analysis and Critical Control Points (HACCP) Systems auf die Druckluftversorgung ist ein effektiver Ansatz zur Identifizierung und Kontrolle potenzieller Risiken:
Gefahrenanalyse: Identifizierung aller potenziellen physikalischen, chemischen und biologischen Gefahren im Druckluftsystem.
Kritische Kontrollpunkte (CCPs): Bestimmung der Punkte im System, an denen Kontrollen angewendet werden müssen, um Gefahren zu verhindern oder zu minimieren. Dies können beispielsweise Filterstationen oder Messstellen sein.
Kritische Grenzwerte: Festlegung von Grenzwerten für jeden CCP, wie zum Beispiel maximale Partikelkonzentrationen oder Drucktaupunkte.
Überwachungsverfahren: Etablierung von Verfahren zur regelmäßigen Überwachung der CCPs.
Korrekturmaßnahmen: Definition von Maßnahmen, die ergriffen werden müssen, wenn die Überwachung anzeigt, dass ein CCP nicht unter Kontrolle ist.
Verifizierungsverfahren: Regelmäßige Überprüfung des Systems zur Sicherstellung seiner Wirksamkeit.
Dokumentation: Führung von Aufzeichnungen über alle Aspekte des Systems.
Integration in bestehende Managementsysteme
Die Verwaltung der Druckluftreinheit sollte in bestehende Qualitäts-, Sicherheits- und Umweltmanagementsysteme integriert werden:
Qualitätsmanagement (z.B. ISO 9001): Integration von Druckluftqualitätszielen und -prozessen in das allgemeine Qualitätsmanagementsystem.
Lebensmittelsicherheit (z.B. FSSC 22000, IFS Food, BRC Food): Einbeziehung der Druckluft als potenzielles Kontaminationsrisiko in die Gefahrenanalyse und Festlegung entsprechender Kontrollmaßnahmen.
Umweltmanagement (z.B. ISO 14001): Berücksichtigung der Energieeffizienz und des Ressourcenverbrauchs des Druckluftsystems.
Arbeitsschutz (z.B. ISO 45001): Einbeziehung von Sicherheitsaspekten bei der Handhabung und Wartung von Druckluftsystemen.
Kontinuierliche Verbesserung
Ein effektives Managementsystem für Druckluftreinheit sollte einen Prozess der kontinuierlichen Verbesserung beinhalten:
Regelmäßige Leistungsüberprüfungen: Analyse von Trends in der Druckluftqualität, Energieverbrauch und Systemeffizienz.
Benchmarking: Vergleich der eigenen Leistung mit Branchenstandards und Best Practices.
Innovationsmanagement: Kontinuierliche Beobachtung neuer Technologien und Methoden zur Verbesserung der Druckluftqualität und -effizienz.
Schulung und Bewusstseinsbildung: Regelmäßige Schulungen für Mitarbeiter zur Aktualisierung ihres Wissens und zur Förderung einer Kultur der Qualität.
Feedback-Mechanismen: Etablierung von Systemen, die es Mitarbeitern ermöglichen, Verbesserungsvorschläge einzubringen.
Vorbereitung auf Audits
Für Auditoren von Lebensmittelsicherheitsmanagementsystemen und Qualitätsmanager ist eine gute Vorbereitung auf Audits unerlässlich:
Dokumentation: Sicherstellung, dass alle relevanten Dokumente aktuell und leicht zugänglich sind. Dies umfasst Risikobewertungen, Überwachungsprotokolle, Wartungsaufzeichnungen und Schulungsnachweise.
Kennzahlen und Leistungsindikatoren: Vorbereitung von Berichten, die die Einhaltung der Druckluftqualitätsstandards über einen längeren Zeitraum demonstrieren.
Prozessverständnis: Sicherstellung, dass alle beteiligten Mitarbeiter den Prozess der Drucklufterzeugung und -aufbereitung sowie die kritischen Kontrollpunkte verstehen und erklären können.
Korrekturmaßnahmen: Nachweis, dass bei Abweichungen angemessene Korrekturmaßnahmen ergriffen und deren Wirksamkeit überprüft wurde.
Kontinuierliche Verbesserung: Vorbereitung von Beispielen, die zeigen, wie das Unternehmen kontinuierlich an der Verbesserung der Druckluftqualität arbeitet.
Schlussfolgerung
Die Implementierung eines ganzheitlichen Managementsystems für die Druckluftreinheit ist ein komplexer, aber notwendiger Prozess. Es erfordert die Integration technischer Lösungen mit robusten Managementpraktiken, kontinuierlicher Überwachung und einer Kultur der ständigen Verbesserung. Durch die Anwendung der in diesem Leitfaden beschriebenen Prinzipien und Methoden können Unternehmen nicht nur die erforderlichen Reinheitsstandards für Druckluft erreichen und aufrechterhalten, sondern auch ihre Gesamteffizienz steigern und sich auf zukünftige Herausforderungen vorbereiten.
Für Qualitätsmanager, Investitionsleiter, Instandhaltungsmanager und Auditoren bietet dieser ganzheitliche Ansatz einen Rahmen für die effektive Verwaltung der Druckluftqualität, der sowohl den aktuellen regulatorischen Anforderungen entspricht als auch flexibel genug ist, um sich an zukünftige Entwicklungen anzupassen.