Trockner spielen eine entscheidende Rolle in Druckluftsystemen, indem sie Feuchtigkeit aus der komprimierten Luft entfernen. Eine Fehlfunktion des Trockners kann zu erheblichen Problemen führen, die die Effizienz, Zuverlässigkeit und Qualität des gesamten Druckluftsystems beeinträchtigen. In diesem Artikel untersuchen wir die Ursachen, Auswirkungen und Lösungen für Fehlfunktionen des Trockners in industriellen Druckluftsystemen.
Grundlagen der Drucklufttrocknung
Zunächst ist es wichtig, die Funktion und Bedeutung von Trocknern in Druckluftsystemen zu verstehen. Trockner dienen dazu, den Taupunkt der Druckluft zu senken und somit Kondensation in den Leitungen und an den Verbrauchsstellen zu verhindern. Es gibt verschiedene Arten von Trocknern:
- Kältetrockner: Kühlen die Druckluft unter den Taupunkt ab, um Feuchtigkeit zu kondensieren und abzuscheiden.
- Adsorptionstrockner: Verwenden ein hygroskopisches Material (z.B. Silicagel), um Feuchtigkeit zu binden.
- Membrantrockner: Nutzen selektiv permeable Membranen zur Feuchtigkeitsabscheidung.
- Wärmeregenerierte Adsorptionstrockner: Kombinieren Adsorption mit Wärme zur Regeneration des Trocknungsmittels.
Die Effizienz eines Trockners wird typischerweise durch den erreichten Drucktaupunkt gemessen. Nach ISO 8573-1 werden verschiedene Klassen der Druckluftqualität definiert, wobei Klasse 1 einen Drucktaupunkt von -70°C oder niedriger erfordert.
Ursachen und Szenarien für Fehlfunktionen des Trockners
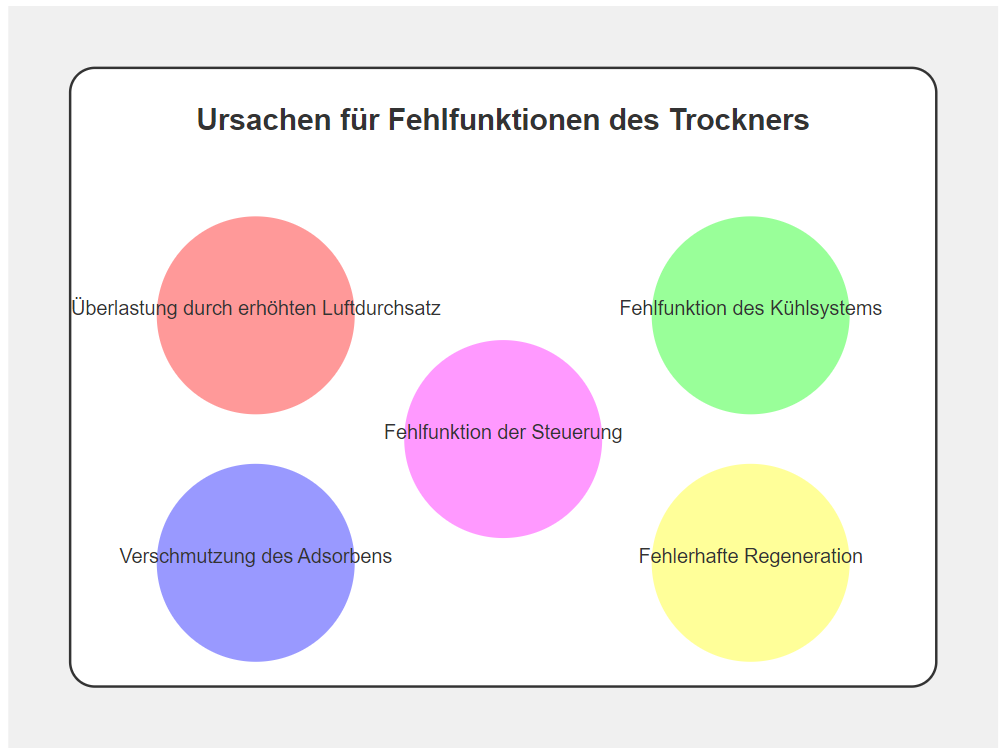
1. Überlastung durch erhöhten Luftdurchsatz
Eine häufige Ursache für Trocknerprobleme ist eine Überlastung durch einen unerwartet hohen Luftdurchsatz.
Fallbeispiel: Ein Automobilzulieferer in Bayern erweiterte seine Produktion, ohne den vorhandenen Kältetrockner anzupassen. Der Luftdurchsatz überstieg die Nennkapazität des Trockners um 30%. Als Folge stieg der Drucktaupunkt von den spezifizierten -20°C auf +5°C, was zu Kondensationsproblemen in den Produktionsanlagen führte. Der Energieverbrauch des Trockners erhöhte sich um 25%, ohne die erforderliche Trocknungsleistung zu erreichen.
2. Fehlfunktion des Kühlsystems bei Kältetrocknern
Bei Kältetrocknern kann eine Störung im Kühlkreislauf zu einer unzureichenden Trocknung führen.
Fallbeispiel: In einem chemischen Werk in Sachsen-Anhalt wurde ein allmählicher Anstieg des Drucktaupunkts beobachtet. Eine Untersuchung ergab, dass das Kältemittel im Trockner aufgrund einer Leckage um 40% reduziert war. Dies führte zu einer unzureichenden Kühlung und einem Anstieg des Drucktaupunkts von -25°C auf -5°C. Die resultierende Feuchtigkeit in der Druckluft verursachte Korrosionsprobleme in den Rohrleitungen und Störungen in empfindlichen Prozesssteuerungen.
3. Verschmutzung des Adsorbens bei Adsorptionstrocknern
Bei Adsorptionstrocknern kann eine Verschmutzung des Trocknungsmittels die Effizienz erheblich beeinträchtigen.
Fallbeispiel: Ein Pharmaunternehmen in Hessen bemerkte einen stetigen Anstieg des Energieverbrauchs seines Adsorptionstrockners bei gleichzeitiger Verschlechterung des Drucktaupunkts. Eine Analyse zeigte, dass Ölaerosole aus dem Kompressor das Adsorbens kontaminiert hatten, was dessen Aufnahmefähigkeit für Feuchtigkeit um 60% reduzierte. Der Drucktaupunkt stieg von -40°C auf -10°C, was die Reinraumqualität gefährdete.
4. Fehlerhafte Regeneration bei wärmeregenierten Adsorptionstrocknern
Eine unzureichende Regeneration des Adsorbens kann zu einer verminderten Trocknungsleistung führen.
Fallbeispiel: Ein Lebensmittelhersteller in Niedersachsen stellte fest, dass der Drucktaupunkt seines wärmeregenierten Adsorptionstrockners von -70°C auf -20°C angestiegen war. Eine Untersuchung ergab, dass das Heizelement für die Regeneration defekt war und nur 50% der erforderlichen Leistung erbrachte. Dies führte zu einer unvollständigen Regeneration des Adsorbens und einer verminderten Trocknungsleistung.
5. Fehlfunktion der Steuerung
Probleme mit der Trocknersteuerung können zu ineffizientem Betrieb und unzureichender Trocknung führen.
Fallbeispiel: In einem Werk für Elektronikkomponenten in Thüringen wurde eine starke Schwankung des Drucktaupunkts festgestellt. Die Ursache war ein defekter Taupunktsensor, der falsche Werte an die Trocknersteuerung lieferte. Dies führte zu einer fehlerhaften Zyklussteuerung des Adsorptionstrockners, bei der die Umschaltung zwischen den Adsorptionsbehältern nicht optimal erfolgte. Der durchschnittliche Drucktaupunkt verschlechterte sich von -40°C auf -15°C, was zu Qualitätsproblemen in der Produktion führte.
Auswirkungen von Trockner-Fehlfunktionen
Die Auswirkungen einer Fehlfunktion des Trockners sind vielfältig und können erhebliche betriebliche und wirtschaftliche Konsequenzen haben:
- Erhöhte Feuchtigkeit in der Druckluft: Dies kann zu Korrosion, Eisbildung und Störungen in pneumatischen Systemen führen.
- Qualitätsprobleme: In sensiblen Anwendungen wie der Lebensmittel- oder Pharmaindustrie kann erhöhte Feuchtigkeit zu Kontaminationen führen.
- Erhöhter Energieverbrauch: Ein ineffizient arbeitender Trockner verbraucht mehr Energie, ohne die gewünschte Trocknungsleistung zu erbringen.
- Verkürzung der Lebensdauer von Komponenten: Feuchtigkeit in der Druckluft kann zu vorzeitigem Verschleiß von Ventilen, Werkzeugen und anderen Druckluftverbrauchern führen.
- Produktionsausfälle: Im Extremfall können Probleme mit dem Trockner zu Systemausfällen oder Qualitätsproblemen führen, die Produktionsunterbrechungen nach sich ziehen.
Lösungsansätze und Präventivmaßnahmen
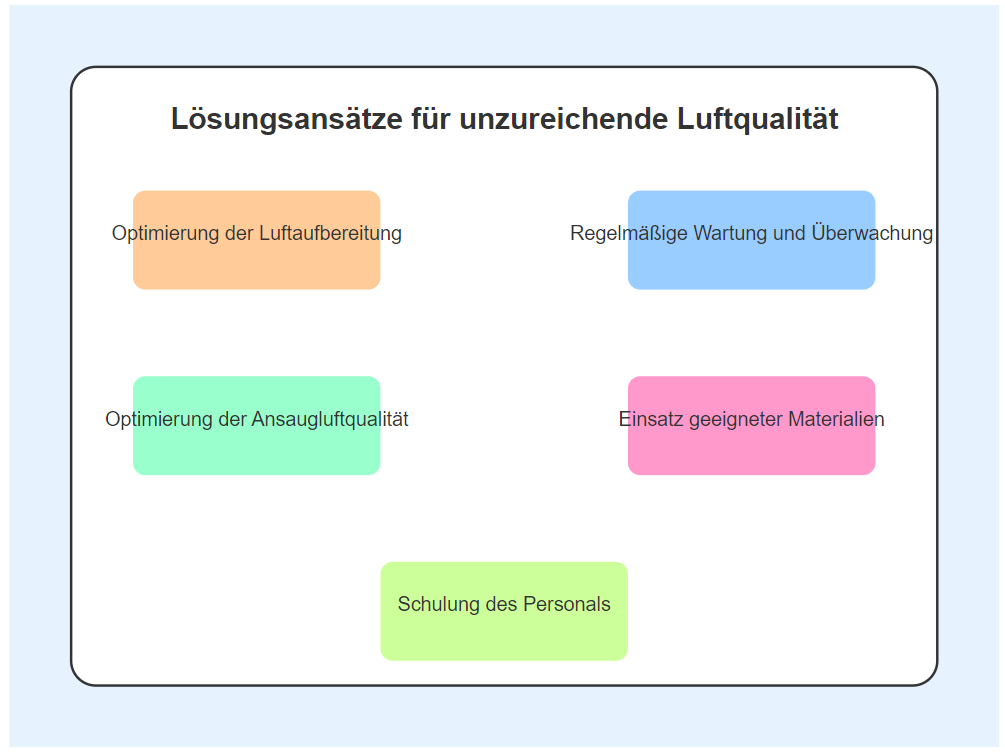
Die Vermeidung und Behebung von Problemen mit Trocknern erfordert einen systematischen Ansatz:
1. Regelmäßige Wartung und Inspektion
Ein strukturiertes Wartungsprogramm ist entscheidend, um Probleme frühzeitig zu erkennen und zu beheben.
Fallbeispiel: Ein Automobilhersteller in Baden-Württemberg implementierte ein präventives Wartungsprogramm für seine Drucklufttrockner, das auf kontinuierlicher Überwachung des Drucktaupunkts und regelmäßigen Inspektionen basiert. Durch frühzeitige Erkennung von Problemen konnte die ungeplante Ausfallzeit des Trocknungssystems um 80% reduziert werden. Zudem wurde der durchschnittliche Energieverbrauch des Trocknungssystems um 12% gesenkt.
2. Implementierung eines Überwachungssystems
Moderne Überwachungssysteme können den Zustand des Trockners kontinuierlich überwachen und frühzeitig auf Probleme hinweisen.
Fallbeispiel: Ein Chemieunternehmen in Nordrhein-Westfalen installierte ein online Überwachungssystem für seine Drucklufttrockner, das kontinuierlich Drucktaupunkt, Energieverbrauch und andere kritische Parameter misst. Das System alarmiert das Wartungspersonal automatisch, wenn vordefinierte Grenzwerte überschritten werden. In den ersten 12 Monaten nach der Installation konnte die Anzahl der ungeplanten Trocknerausfälle um 70% reduziert werden, während gleichzeitig die Energieeffizienz um 15% verbessert wurde.
3. Richtige Dimensionierung und Redundanz
Eine sorgfältige Auslegung des Trocknungssystems und die Bereitstellung von Redundanzen können die Zuverlässigkeit erheblich verbessern.
Fallbeispiel: Ein mittelständisches Unternehmen der Metallindustrie in Sachsen optimierte sein Drucklufttrocknungssystem durch die Installation eines redundanten Trockners. Statt eines großen Trockners wurden zwei kleinere Einheiten installiert, die im Normalfall abwechselnd betrieben werden. Dies ermöglicht nicht nur eine kontinuierliche Trocknung auch während Wartungsarbeiten, sondern verbesserte auch die Energieeffizienz um 20% durch optimale Lastanpassung.
4. Schulung des Personals
Gut geschultes Personal kann einen wesentlichen Beitrag zur frühzeitigen Erkennung und Behebung von Trocknerproblemen leisten.
Fallbeispiel: Ein Pharmaunternehmen in Bayern führte ein umfassendes Schulungsprogramm für alle Mitarbeiter durch, die mit dem Druckluftsystem in Berührung kamen. Als Ergebnis stieg die Zahl der frühzeitig gemeldeten potenziellen Trocknerprobleme um 200%. Dies ermöglichte präventive Maßnahmen, die die ungeplanten Trocknerausfälle um 60% reduzierten.
5. Einsatz energieeffizienter Technologien
Moderne, energieeffiziente Trocknertechnologien können nicht nur den Energieverbrauch senken, sondern auch die Zuverlässigkeit erhöhen.
Fallbeispiel: Ein Lebensmittelhersteller in Rheinland-Pfalz ersetzte seinen alten Kältetrockner durch einen modernen Trockner mit Frequenzumrichter und integrierter Wärmerückgewinnung. Dies führte zu einer Reduzierung des Energieverbrauchs um 35% bei gleichzeitiger Verbesserung der Trocknungsleistung. Der Drucktaupunkt konnte konstant bei -40°C gehalten werden, was die Produktqualität verbesserte und die Wartungsintervalle verlängerte.
Zukunftsperspektiven und innovative Ansätze
Die Verbesserung der Trocknertechnologie in Druckluftsystemen ist ein Bereich kontinuierlicher Innovation:
- Hybride Trocknungssysteme: Kombination verschiedener Trocknungstechnologien für optimale Effizienz. Fallbeispiel: Ein Start-up aus München entwickelte ein hybrides Trocknungssystem, das Kältetrocknung mit Membrantechnologie kombiniert. In einem Pilotprojekt bei einem Automobilzulieferer konnte das System einen konstanten Drucktaupunkt von -40°C bei 30% geringerem Energieverbrauch im Vergleich zu herkömmlichen Systemen erreichen.
- KI-gestützte Trocknersteuerung: Einsatz künstlicher Intelligenz zur optimalen Steuerung des Trocknungsprozesses. Fallbeispiel: Ein Hersteller von Druckluftsystemen aus Baden-Württemberg entwickelte eine KI-basierte Steuerung für Adsorptionstrockner. Das System lernt kontinuierlich aus den Betriebsdaten und passt die Regenerationszyklen und Energiezufuhr optimal an. In einem Feldtest bei einem großen Chemieunternehmen konnte der Energieverbrauch um 25% gesenkt werden, bei gleichzeitiger Verbesserung der Trocknungsstabilität.
- Neue Adsorbentien: Entwicklung hocheffizienter Materialien für Adsorptionstrockner. Fallbeispiel: Ein Forschungsteam der TU Dresden entwickelte ein neuartiges, nanostrukturiertes Adsorbens auf Zeolithbasis. In Laborversuchen zeigte das Material eine um 40% höhere Wasseraufnahmekapazität bei gleichzeitig schnellerer Regeneration im Vergleich zu herkömmlichen Adsorbentien.
- Integrierte Wärmerückgewinnung: Nutzung der Abwärme des Trocknungsprozesses für andere industrielle Prozesse. Fallbeispiel: Ein mittelständisches Unternehmen der Kunststoffverarbeitung in Thüringen implementierte ein System zur Wärmerückgewinnung aus dem Kältetrockner. Die zurückgewonnene Wärme wird zur Vorwärmung von Prozesswasser genutzt, was den Gesamtenergieverbrauch des Unternehmens um 5% reduzierte.
- Molekulare Siebe: Einsatz hochselektiver Materialien zur gezielten Feuchtigkeitsabsorption. Fallbeispiel: Ein japanisches Unternehmen entwickelte ein molekulares Sieb auf Basis von Metal-Organic Frameworks (MOFs) für den Einsatz in Adsorptionstrocknern. In einem Pilotprojekt bei einem deutschen Halbleiterhersteller konnte das Material einen konstanten Drucktaupunkt von -80°C bei 20% geringerem Energieverbrauch im Vergleich zu herkömmlichen Silicagel-basierten Systemen erreichen.
- Solarunterstützte Regeneration: Nutzung von Solarenergie zur Regeneration von Adsorptionstrocknern. Fallbeispiel: Ein Unternehmen in Spanien entwickelte ein solarthermisches System zur Unterstützung der Regeneration von Adsorptionstrocknern. In einem Feldtest bei einem Lebensmittelhersteller in Süddeutschland konnte der Energiebedarf für die Regeneration in den Sommermonaten um bis zu 70% reduziert werden.
- Phasenwechselmaterialien (PCM) in Kältetrocknern: Einsatz von PCM zur Stabilisierung der Kühlleistung. Fallbeispiel: Ein Forschungsteam der RWTH Aachen entwickelte einen Kältetrockner mit integrierten Phasenwechselmaterialien. Das System konnte Lastschwankungen besser ausgleichen und erreichte eine um 15% höhere Energieeffizienz bei gleichzeitig stabilerer Trocknungsleistung.
- Fazit und Ausblick
- Die effiziente und zuverlässige Trocknung von Druckluft bleibt eine zentrale Herausforderung und gleichzeitig eine große Chance für Unternehmen, ihre Energieeffizienz zu verbessern, Betriebskosten zu senken und die Qualität ihrer Prozesse zu steigern. Die in diesem Artikel vorgestellten Fallbeispiele zeigen, dass sowohl bewährte Methoden als auch innovative Ansätze signifikante Verbesserungen ermöglichen können.
Die detaillierte Beschreibung der verschiedenen Trocknertypen und ihrer spezifischen Problemstellungen ist sehr informativ. Als Energiemanager in einem Automobilzulieferunternehmen möchte ich den Aspekt der Energieeffizienz noch stärker betonen. Wir haben festgestellt, dass eine optimale Abstimmung zwischen Kompressor und Trockner erhebliche Energieeinsparungen ermöglicht. In unserem Fall führte die Installation eines Wärmetauschers zwischen Kompressor und Trockner zu einer Reduzierung des Energiebedarfs für die Trocknung um 20%. Es wäre interessant gewesen, im Artikel noch mehr über solche systemübergreifenden Optimierungsansätze zu erfahren.
Der Artikel betont zu Recht die Bedeutung der richtigen Dimensionierung und Redundanz von Trocknersystemen. Als Berater für Industrieanlagen möchte ich die Wichtigkeit einer ganzheitlichen Systembetrachtung unterstreichen. In vielen Projekten haben wir festgestellt, dass eine Optimierung des gesamten Druckluftsystems, einschließlich Leitungsführung und Druckmanagement, oft größere Effizienzsteigerungen ermöglicht als die alleinige Fokussierung auf den Trockner. Ein interessanter Trend, den wir beobachten, ist die zunehmende Modularisierung von Druckluftsystemen, die eine flexiblere Anpassung an schwankende Bedarfssituationen ermöglicht. Dies kann insbesondere bei saisonalen Produktionsschwankungen zu erheblichen Effizienzsteigerungen führen.
Die Ausführungen zu den innovativen Ansätzen wie KI-gestützte Trocknersteuerung und neue Adsorbentien sind faszinierend. Als Forscher im Bereich der Materialwissenschaften sehe ich großes Potenzial in der Entwicklung von maßgeschneiderten Adsorbentien. Ein vielversprechender Ansatz, der meiner Meinung nach Erwähnung verdient, ist die Entwicklung von Composite-Adsorbentien, die sowohl Wasser als auch Ölaerosole effizient entfernen können. Wir arbeiten derzeit an einem Material, das die Eigenschaften von Zeolithen und Aktivkohle kombiniert und in ersten Labortests eine um 30% höhere Gesamteffizient als herkömmliche Adsorbentien zeigt.
Die vorgestellten Fallbeispiele sind sehr praxisnah und aufschlussreich. Als Wartungsingenieur in einem Chemieunternehmen kann ich die Wichtigkeit der präventiven Wartung bestätigen. Ein Aspekt, den ich gerne ergänzen möchte, ist die Bedeutung der Datenanalyse für die vorausschauende Wartung. Wir haben ein System implementiert, das historische Wartungsdaten mit aktuellen Betriebsparametern kombiniert, um potenzielle Ausfälle vorherzusagen. Dies hat uns ermöglicht, die Verfügbarkeit unserer Trocknersysteme um 15% zu erhöhen und gleichzeitig die Wartungskosten zu reduzieren.
Der Artikel bietet einen umfassenden Überblick über die Problematik von Trockner-Fehlfunktionen in Druckluftsystemen. Als Ingenieur in der Lebensmittelindustrie möchte ich die Bedeutung der Trocknungsleistung für die Produktqualität und -sicherheit hervorheben. In unserem Unternehmen haben wir zusätzlich zu den im Artikel genannten Maßnahmen ein System zur kontinuierlichen Überwachung der mikrobiologischen Luftqualität implementiert. Dies ermöglicht uns, auch indirekte Auswirkungen von Trockner-Fehlfunktionen frühzeitig zu erkennen. Ein interessanter Ansatz, den wir derzeit evaluieren, ist die Integration von UV-C-Entkeimung in unsere Trocknersysteme, um eine zusätzliche Barriere gegen mikrobiologische Kontaminationen zu schaffen.