Filter und Abscheider spielen eine entscheidende Rolle in Druckluftsystemen, indem sie Verunreinigungen wie Staub, Öl und Feuchtigkeit aus der Druckluft entfernen. Wenn diese Komponenten verstopfen, kann dies zu erheblichen Problemen führen, die die Effizienz, Zuverlässigkeit und Qualität des gesamten Druckluftsystems beeinträchtigen. In diesem Artikel untersuchen wir die Ursachen, Auswirkungen und Lösungen für verstopfte Filter und Abscheider in industriellen Druckluftsystemen.
Grundlagen der Filtration und Abscheidung in Druckluftsystemen
Zunächst ist es wichtig, die Funktion und Bedeutung von Filtern und Abscheidern in Druckluftsystemen zu verstehen. Diese Komponenten dienen dazu, verschiedene Arten von Verunreinigungen aus der Druckluft zu entfernen:
- Partikelfilter: Entfernen feste Partikel wie Staub, Rost und andere Schwebstoffe.
- Koaleszenzfilter: Separieren feine Öltröpfchen und Aerosole aus der Druckluft.
- Adsorptionsfilter (z.B. Aktivkohlefilter): Entfernen Öldämpfe und Gerüche.
- Wasserabscheider: Trennen kondensiertes Wasser aus der Druckluft.
Die Effizienz dieser Komponenten wird typischerweise in Mikrometern (µm) für Partikelfilter und in mg/m³ für Ölabscheidung gemessen. Die ISO 8573-1 definiert verschiedene Klassen der Druckluftqualität, wobei Klasse 1 die höchsten Anforderungen stellt.
Ursachen und Szenarien für verstopfte Filter und Abscheider
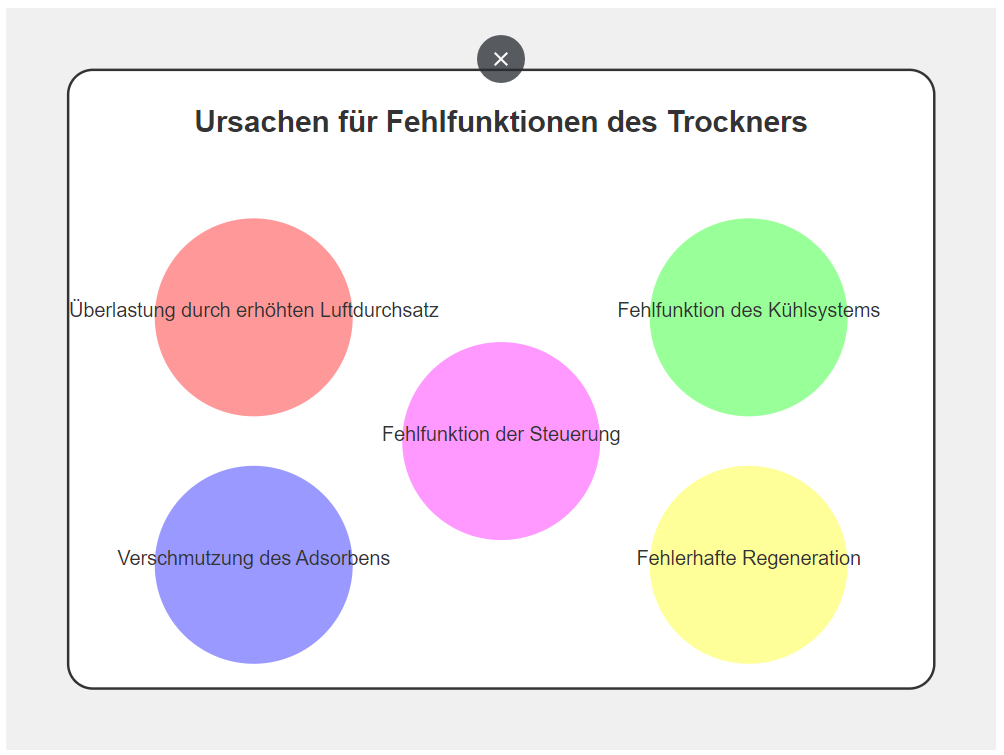
1. Überlastung durch erhöhte Verunreinigungen
Eine der häufigsten Ursachen für verstopfte Filter ist eine unerwartet hohe Belastung durch Verunreinigungen.
Fallbeispiel: Ein Automobilzulieferer in Sachsen bemerkte einen rapiden Anstieg des Druckverlusts über seine Filtereinheiten. Eine Untersuchung ergab, dass aufgrund von Bauarbeiten in der Nähe der Luftansaugung des Kompressors die Staubbelastung in der Ansaugluft um das Zehnfache gestiegen war. Die Filter, die für normale Bedingungen ausgelegt waren, verstopften innerhalb weniger Tage, was zu einem Anstieg des Energieverbrauchs um 12% führte.
2. Unzureichende Wartungsintervalle
Zu lange Wartungsintervalle können zu einer Überlastung der Filter führen.
Fallbeispiel: Ein mittelständisches Unternehmen der Lebensmittelindustrie in Bayern hatte die Wartungsintervalle seiner Druckluftfilter aus Kostengründen von 3 auf 6 Monate verlängert. Als Folge davon stieg der Druckverlust über die Filter kontinuierlich an, was zu einem erhöhten Energieverbrauch der Kompressoren um 8% führte. Zudem wurde eine Verschlechterung der Druckluftqualität festgestellt, die beinahe zu Kontaminationen in der Produktion geführt hätte.
3. Fehlerhafte Dimensionierung
Eine falsche Dimensionierung der Filter und Abscheider kann zu vorzeitiger Verstopfung führen.
Fallbeispiel: Ein Pharmaunternehmen in Hessen installierte im Rahmen einer Produktionserweiterung neue Druckluftverbraucher, ohne die Filterkapazität anzupassen. Als Folge davon überstieg der Luftdurchsatz die Nennkapazität der vorhandenen Filter um 30%. Dies führte zu einer schnellen Verstopfung der Filter, einem Anstieg des Druckverlusts und einer Verschlechterung der Luftqualität. Der SEC (Specific Energy Consumption) des Druckluftsystems stieg von 6,2 kW/(m³/min) auf 7,1 kW/(m³/min).
4. Ungeeignete Filtertypen
Die Wahl eines ungeeigneten Filtertyps kann zu ineffizienter Filtration und schneller Verstopfung führen.
Fallbeispiel: Ein Hersteller von Elektronikkomponenten in Thüringen verwendete Standardpartikelfilter in einer Umgebung mit hoher Luftfeuchtigkeit. Die Filter verstopften schnell durch die Kombination von Feuchtigkeit und feinen Partikeln. Der Austausch gegen spezielle Koaleszenzfilter mit integriertem Wasserabscheider verlängerte die Standzeit der Filter um das Dreifache und verbesserte die Luftqualität erheblich.
5. Temperaturschwankungen und Kondensation
Starke Temperaturschwankungen können zu Kondensation und damit zu Problemen in Filtern und Abscheidern führen.
Fallbeispiel: Ein Chemieunternehmen in Nordrhein-Westfalen bemerkte saisonale Schwankungen in der Effizienz seiner Druckluftaufbereitung. Im Winter, wenn die Temperatur in den nicht isolierten Teilen des Rohrleitungssystems stark abfiel, kam es zu verstärkter Kondensation in den Filtern. Dies führte zu einer erhöhten Belastung der Koaleszenzfilter und einer Verkürzung ihrer Standzeit um 40%.
Auswirkungen verstopfter Filter und Abscheider
Die Auswirkungen verstopfter Filter und Abscheider sind vielfältig und können erhebliche betriebliche und wirtschaftliche Konsequenzen haben:
- Erhöhter Energieverbrauch: Verstopfte Filter erhöhen den Druckverlust im System, was die Kompressoren zwingt, mit höherem Druck zu arbeiten.
- Verminderte Luftqualität: Überlastete Filter können Verunreinigungen nicht mehr effektiv zurückhalten, was zu einer Verschlechterung der Druckluftqualität führt.
- Erhöhte Wartungskosten: Häufigere Filterwechsel und potenzielle Schäden an nachgelagerten Komponenten führen zu höheren Wartungskosten.
- Produktionsausfälle: Im Extremfall können verstopfte Filter zu Systemausfällen oder Qualitätsproblemen in der Produktion führen.
- Verkürzung der Lebensdauer von Komponenten: Verunreinigte Druckluft kann zu erhöhtem Verschleiß an Ventilen, Werkzeugen und anderen Druckluftverbrauchern führen.
Lösungsansätze und Präventivmaßnahmen
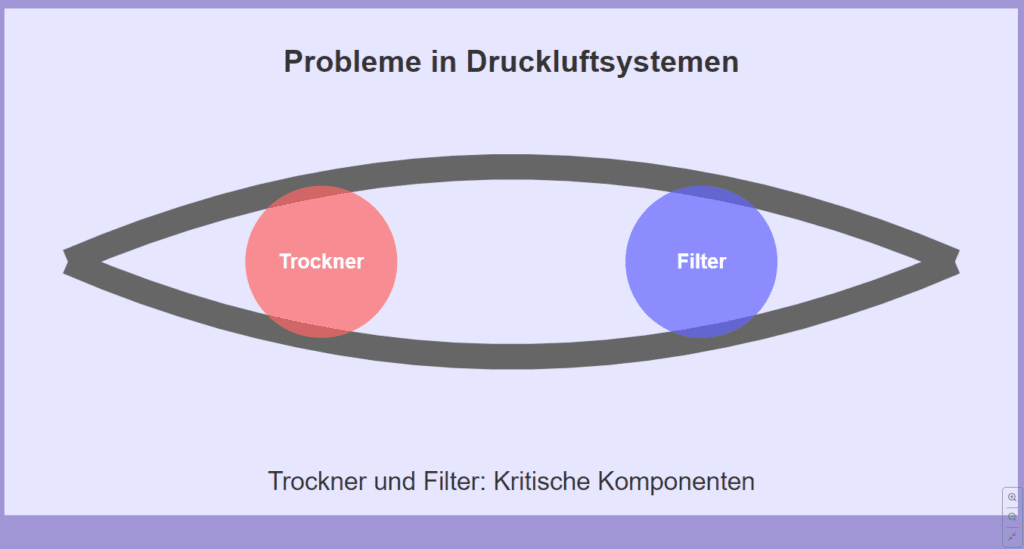
Die Vermeidung und Behebung von Problemen mit verstopften Filtern und Abscheidern erfordert einen systematischen Ansatz:
1. Implementierung eines präventiven Wartungsprogramms
Ein strukturiertes Wartungsprogramm ist entscheidend, um Probleme frühzeitig zu erkennen und zu beheben.
Fallbeispiel: Ein großer Automobilhersteller in Baden-Württemberg implementierte ein präventives Wartungsprogramm für seine Druckluftaufbereitung, das auf kontinuierlicher Überwachung des Differenzdrucks über die Filter basiert. Durch den rechtzeitigen Austausch der Filter konnte der durchschnittliche Energieverbrauch des Druckluftsystems um 7% gesenkt werden. Zudem wurden ungeplante Stillstandzeiten aufgrund von Filterproblemen um 90% reduziert.
2. Einsatz moderner Filtertechnologien
Moderne Filtertechnologien können die Effizienz und Standzeit erheblich verbessern.
Fallbeispiel: Ein Lebensmittelhersteller in Niedersachsen ersetzte seine herkömmlichen Partikelfilter durch neue Nanofilter mit größerer Filterfläche und verbesserter Strömungsdynamik. Dies führte zu einer Verdoppelung der Filterstandzeit und einer Reduzierung des Druckverlusts um 40%, was zu einer jährlichen Energieeinsparung von 45.000 kWh führte.
3. Optimierung der Systemauslegung
Eine sorgfältige Auslegung des gesamten Druckluftsystems kann die Belastung der Filter reduzieren.
Fallbeispiel: Ein mittelständisches Unternehmen der Metallindustrie in Sachsen-Anhalt optimierte sein Druckluftnetz durch die Installation eines Ringleitungssystems und die Verlegung der Hauptfilterstation näher an die Kompressoren. Dies führte zu einer gleichmäßigeren Belastung der Filter und einer Reduzierung des Gesamtdruckverlusts im System um 0,5 bar. Der SEC des Systems verbesserte sich von 6,8 kW/(m³/min) auf 6,2 kW/(m³/min).
4. Schulung und Sensibilisierung des Personals
Gut geschultes Personal kann einen wesentlichen Beitrag zur Vermeidung von Filterproblemen leisten.
Fallbeispiel: Ein Pharmaunternehmen in Bayern führte ein umfassendes Schulungsprogramm für alle Mitarbeiter durch, die mit dem Druckluftsystem in Berührung kamen. Als Ergebnis stieg die Zahl der frühzeitig gemeldeten potenziellen Filterprobleme um 150%. Dies ermöglichte präventive Maßnahmen, die die ungeplanten Filterwechsel um 60% reduzierten.
5. Einsatz von Überwachungssystemen
Moderne Überwachungssysteme können den Zustand von Filtern und Abscheidern kontinuierlich überwachen.
Fallbeispiel: Ein Chemieunternehmen in Rheinland-Pfalz installierte ein online Überwachungssystem für seine Druckluftfilter, das kontinuierlich Differenzdruck, Durchfluss und Restölgehalt misst. Das System alarmiert das Wartungspersonal automatisch, wenn vordefinierte Grenzwerte überschritten werden. In den ersten 12 Monaten nach der Installation konnte die Anzahl der ungeplanten Filterwechsel um 75% reduziert werden, während gleichzeitig die durchschnittliche Luftqualität verbessert wurde.
Zukunftsperspektiven und innovative Ansätze
Die Verbesserung der Filtration und Abscheidung in Druckluftsystemen ist ein Bereich kontinuierlicher Innovation:
- Selbstreinigende Filter: Entwicklung von Filtern mit integrierten Reinigungsmechanismen, die ihre Standzeit erheblich verlängern. Fallbeispiel: Ein Start-up aus München entwickelte einen selbstreinigenden Partikelfilter, der durch periodische Rückspülung mit Druckluft seine Effizienz aufrechterhält. In einem Pilotprojekt bei einem Automobilzulieferer konnte die Standzeit der Filter um das Fünffache verlängert werden.
- Intelligente Filter mit IoT-Anbindung: Filter, die ihren Zustand selbst überwachen und Daten in Echtzeit übermitteln. Fallbeispiel: Ein Hersteller von Filtersystemen aus Baden-Württemberg entwickelte einen „smarten“ Filter mit integrierten Sensoren und IoT-Anbindung. In einem Feldtest bei einem großen Chemieunternehmen konnte durch die präzise Vorhersage des optimalen Wechselzeitpunkts der Energieverbrauch um 5% und die Filterkosten um 20% gesenkt werden.
- Nanotechnologie in der Filtration: Einsatz von Nanomaterialien für hocheffiziente Filtration bei geringerem Druckverlust. Fallbeispiel: Ein Forschungsprojekt an der TU Dresden entwickelte einen Nanofilter auf Basis von Graphenoxid. In Laborversuchen zeigte der Filter eine um 30% höhere Abscheideleistung bei gleichzeitig 20% geringerem Druckverlust im Vergleich zu herkömmlichen Filtern.
- Membrantechnologie: Fortschritte in der Membrantechnologie könnten zu effizienteren und langlebigeren Filtern führen. Fallbeispiel: Ein niederländisches Unternehmen entwickelte eine neuartige Polymermembran für Druckluftfilter, die eine hohe Abscheideleistung mit geringem Druckverlust kombiniert. In einem Pilotprojekt bei einem deutschen Pharmaunternehmen konnte der Energieverbrauch des Druckluftsystems um 8% gesenkt werden.
- Biologische Filtration: Einsatz von Mikroorganismen zur Entfernung spezifischer Verunreinigungen aus der Druckluft. Fallbeispiel: Ein Forschungsteam der Universität Hohenheim entwickelte einen biobasierten Filter, der spezifische organische Verbindungen aus der Druckluft entfernt. In ersten Tests in einer Brauerei zeigte der Filter eine hohe Effizienz bei der Entfernung von geruchsbildenden Substanzen, ohne den Druckverlust zu erhöhen.
Fazit und Ausblick
Die effiziente Filtration und Abscheidung in Druckluftsystemen bleibt eine zentrale Herausforderung und gleichzeitig eine große Chance für Unternehmen, ihre Energieeffizienz zu verbessern, Betriebskosten zu senken und die Qualität ihrer Prozesse zu steigern. Die in diesem Artikel vorgestellten Fallbeispiele zeigen, dass sowohl bewährte Methoden als auch innovative Ansätze signifikante Verbesserungen ermöglichen können.
Entscheidend für den Erfolg ist ein ganzheitlicher Ansatz, der nicht nur die Filter und Abscheider selbst, sondern das gesamte Druckluftsystem einschließlich Kompressoren, Aufbereitung und Verteilung berücksichtigt. Die richtige Dimensionierung, regelmäßige Wartung und Überwachung, der Einsatz moderner Filtertechnologien sowie die Schulung des Personals sind Schlüsselelemente einer erfolgreichen Strategie zur Optimierung der Filtration und Abscheidung.
Die wirtschaftlichen und ökologischen Vorteile einer effektiven Filtration sind beträchtlich. In den vorgestellten Fallbeispielen konnten Energieeinsparungen von 5% bis 12% realisiert werden, was sich direkt in reduzierten Betriebskosten und verminderten CO2-Emissionen niederschlägt. Zudem führt eine verbesserte Luftqualität zu geringerem Verschleiß an nachgelagerten Komponenten und kann die Produktqualität in sensiblen Anwendungen erheblich steigern.
Blickt man in die Zukunft, so versprechen Entwicklungen in Bereichen wie Nanotechnologie, intelligente Sensorik und biologische Filtration weitere Verbesserungen. Die Integration dieser Technologien in bestehende und neue Druckluftsysteme wird es ermöglichen, die Effizienz weiter zu steigern und gleichzeitig die Zuverlässigkeit und Flexibilität der Systeme zu erhöhen.
Besonders vielversprechend erscheinen Ansätze, die verschiedene Technologien intelligent kombinieren. So könnte beispielsweise ein selbstreinigender Filter mit integrierter IoT-Anbindung und KI-gestützter Vorhersage des optimalen Wartungszeitpunkts zu einer deutlichen Steigerung der Systemeffizienz führen.
Die Herausforderung für Unternehmen wird darin bestehen, mit den technologischen Entwicklungen Schritt zu halten und die für ihre spezifische Situation am besten geeigneten Lösungen zu identifizieren und umzusetzen. Dies erfordert nicht nur Investitionen in Technologie, sondern auch in Wissen und Kompetenzen. Kontinuierliche Fortbildung des technischen Personals, der Austausch von Best Practices und die enge Zusammenarbeit mit Technologieanbietern und Forschungseinrichtungen werden dabei entscheidende Erfolgsfaktoren sein.
Gleichzeitig wird die Bedeutung eines ganzheitlichen Energiemanagements zunehmen. Die Optimierung der Filtration und Abscheidung sollte nicht isoliert betrachtet werden, sondern als Teil einer übergreifenden Strategie zur Verbesserung der Energieeffizienz und Nachhaltigkeit des gesamten Unternehmens. In diesem Kontext können Maßnahmen zur Verbesserung der Filtration mit anderen Energieeffizienzmaßnahmen kombiniert werden, um maximale Synergien zu erzielen.
Die detaillierte Beschreibung der verschiedenen Filtertypen und ihrer spezifischen Problemstellungen ist sehr informativ. Als Qualitätsmanager in einem Pharmaunternehmen möchte ich den Aspekt der Luftqualitätsüberwachung noch stärker betonen. Wir haben festgestellt, dass eine kontinuierliche Messung der Partikel- und Ölkonzentration in der Druckluft nicht nur zur Filterüberwachung, sondern auch zur Prozessoptimierung beitragen kann. In unserem Fall führte die Installation von Online-Luftqualitätssensoren zu einer Verbesserung der Produktqualität und einer Reduzierung von Ausschuss um 5%. Es wäre interessant gewesen, im Artikel noch mehr über solche erweiterten Anwendungen der Luftqualitätsüberwachung zu erfahren.
Der Artikel betont zu Recht die Bedeutung eines ganzheitlichen Ansatzes zur Optimierung von Druckluftsystemen. Als Berater für Industrieanlagen möchte ich die Wichtigkeit der Integration von Filtrations- und Abscheidersystemen in das Gesamtkonzept der Anlageneffizienz unterstreichen. In vielen Projekten haben wir festgestellt, dass eine optimierte Filtration nicht nur die Druckluftqualität verbessert, sondern auch zur Steigerung der Anlagenverfügbarkeit und Produktivität beiträgt. Ein interessanter Trend, den wir beobachten, ist die zunehmende Vernetzung von Filtrationssystemen mit übergeordneten Produktionsmanagementsystemen. Dies ermöglicht eine bessere Abstimmung der Wartungsintervalle auf die Produktionsplanung und trägt zur Minimierung von Stillstandzeiten bei. Es wäre spannend gewesen, im Artikel noch mehr über solche integrierten Ansätze zu lesen, die Filtration und Produktionssteuerung verbinden.
Die Ausführungen zu den innovativen Ansätzen wie selbstreinigende Filter und IoT-Anbindung sind faszinierend. Als Forscher im Bereich der Materialtechnologie sehe ich großes Potenzial in der Entwicklung von multifunktionalen Filtermaterialien. Ein vielversprechender Ansatz, der meiner Meinung nach Erwähnung verdient, ist die Entwicklung von Filtern mit katalytischen Eigenschaften. Wir arbeiten derzeit an einem Material, das nicht nur Partikel und Öl abscheidet, sondern auch schädliche Gase katalytisch umwandelt. In ersten Labortests zeigt dieses Material vielversprechende Ergebnisse für die Verbesserung der Luftqualität in industriellen Umgebungen.
Die vorgestellten Fallbeispiele sind sehr praxisnah und aufschlussreich. Als Energiemanager in einem Chemieunternehmen kann ich die Wichtigkeit der Energieeffizienz bei der Filtration bestätigen. Ein Aspekt, den ich gerne ergänzen möchte, ist die Bedeutung der Druckluftaufbereitung für die Gesamtenergieeffizienz. Wir haben durch die Optimierung unserer Filteranlagen und die Installation eines Wärmerückgewinnungssystems an den Kompressoren nicht nur den Energieverbrauch für die Drucklufterzeugung um 15% gesenkt, sondern auch die Abwärme für Prozesswärme nutzbar gemacht. Dies zeigt, wie Filtrationsprobleme oft Chancen für ganzheitliche Effizienzverbesserungen bieten können.
Der Artikel bietet einen umfassenden Überblick über die Problematik verstopfter Filter und Abscheider in Druckluftsystemen. Als Ingenieur in der Automobilindustrie möchte ich die Bedeutung der Filterüberwachung für die Gesamteffizienz des Produktionsprozesses hervorheben. In unserem Werk haben wir zusätzlich zu den im Artikel genannten Maßnahmen ein System zur Echtzeitüberwachung des Druckluftverbrauchs implementiert. Dies ermöglicht uns, auch indirekte Auswirkungen von Filterproblemen, wie erhöhten Luftverbrauch durch Leckagen oder ineffiziente Prozesse, frühzeitig zu erkennen. Ein interessanter Ansatz, den wir derzeit evaluieren, ist die Integration von prädiktiven Wartungsalgorithmen, die Filterwechsel basierend auf historischen Daten und aktuellen Betriebsbedingungen vorhersagen.