Die Effizienz von Kompressoren ist von entscheidender Bedeutung für die Leistungsfähigkeit und Wirtschaftlichkeit von Druckluftsystemen. Ineffiziente Kompressorfunktion kann zu erhöhtem Energieverbrauch, verminderter Luftqualität und erhöhten Betriebskosten führen. In diesem Artikel werden wir die Ursachen, Auswirkungen und Lösungen für ineffiziente Kompressorfunktion eingehend untersuchen.
Grundlagen der Kompressoreffizienz
Zunächst ist es wichtig, die Grundlagen der Kompressoreffizienz zu verstehen. Die Effizienz eines Kompressors wird typischerweise durch das Verhältnis von Nutzenergieabgabe zu Energieaufnahme gemessen. In der Praxis wird dies oft als spezifischer Energieverbrauch (SEC – Specific Energy Consumption) ausgedrückt, gemessen in kW pro m³/min produzierter Druckluft.
Ein effizienter Kompressor sollte:
- Die erforderliche Luftmenge mit minimalem Energieeinsatz produzieren.
- Eine stabile Druckluftversorgung gewährleisten.
- Eine hohe Verfügbarkeit und Zuverlässigkeit aufweisen.
- Minimal zur Kontamination der Druckluft beitragen.
Ursachen und Szenarien für ineffiziente Kompressorfunktion
1. Falsche Dimensionierung
Eine häufige Ursache für ineffiziente Kompressorfunktion ist die falsche Dimensionierung des Kompressors in Bezug auf den tatsächlichen Luftbedarf.
Fallbeispiel: Ein mittelständisches Unternehmen der Metallverarbeitung in Bayern hatte einen 75 kW Schraubenkompressor installiert, der ursprünglich für eine geplante Produktionserweiterung ausgelegt war. Die Erweiterung wurde jedoch nicht realisiert, sodass der Kompressor nun die meiste Zeit im Teillastbetrieb lief. Dies führte zu häufigen Start-Stopp-Zyklen und einem ineffizienten Betrieb mit einem SEC von 8,5 kW/(m³/min), verglichen mit einem Branchendurchschnitt von 6,5 kW/(m³/min).
2. Verschleiß und mangelnde Wartung
Verschleiß und unzureichende Wartung können die Effizienz von Kompressoren erheblich beeinträchtigen.
Fallbeispiel: In einem Chemiewerk in Sachsen-Anhalt wurde festgestellt, dass der Energieverbrauch eines 10 Jahre alten Turbokompressors stetig anstieg. Eine Analyse ergab, dass die Verdichterschaufeln durch Ablagerungen und Korrosion beschädigt waren. Der SEC war von ursprünglich 5,8 kW/(m³/min) auf 7,2 kW/(m³/min) gestiegen. Nach einer gründlichen Reinigung und Reparatur konnte der SEC auf 6,1 kW/(m³/min) gesenkt werden.
3. Ungeeignete Regelung
Die Art der Kompressorregelung hat einen erheblichen Einfluss auf die Effizienz, insbesondere bei schwankendem Luftbedarf.
Fallbeispiel: Ein Automobilzulieferer in Baden-Württemberg betrieb drei 90 kW Kompressoren mit einfacher Last-Leerlauf-Regelung. Bei geringem Luftbedarf liefen die Kompressoren häufig im energieintensiven Leerlauf. Der durchschnittliche SEC lag bei 7,8 kW/(m³/min). Nach der Installation einer übergeordneten Verbundsteuerung mit Frequenzumrichter für einen der Kompressoren konnte der SEC auf 6,3 kW/(m³/min) gesenkt werden.
4. Hohe Ansaugtemperatur
Die Temperatur der Ansaugluft hat einen direkten Einfluss auf die Kompressoreffizienz.
Fallbeispiel: In einer Brauerei in Nordrhein-Westfalen war der Kompressorraum unzureichend belüftet, was zu Ansaugtemperaturen von bis zu 40°C führte. Dies resultierte in einem erhöhten SEC von 7,5 kW/(m³/min). Nach Installation eines verbesserten Belüftungssystems, das die Ansaugtemperatur auf 25°C reduzierte, sank der SEC auf 6,8 kW/(m³/min).
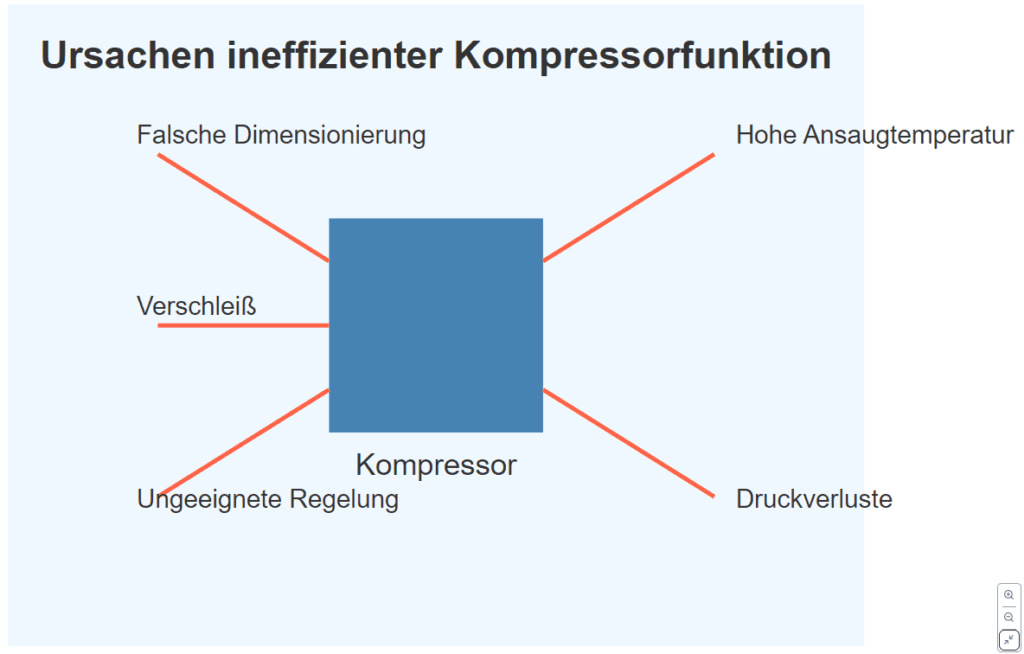
5. Druckverluste im Ansaugsystem
Verstopfte Ansaugfilter oder ungeeignete Ansaugleitungen können die Kompressoreffizienz beeinträchtigen.
Fallbeispiel: Ein Pharmaunternehmen in Hessen bemerkte einen allmählichen Anstieg des Energieverbrauchs seiner Kompressoren. Eine Untersuchung ergab, dass die Ansaugfilter stark verschmutzt waren, was zu einem Druckverlust von 50 mbar führte. Nach dem Austausch der Filter sank der SEC von 7,2 kW/(m³/min) auf 6,7 kW/(m³/min).
Auswirkungen ineffizienter Kompressorfunktion
Die Auswirkungen ineffizienter Kompressorfunktion sind vielfältig und können erhebliche wirtschaftliche und betriebliche Konsequenzen haben:
- Erhöhter Energieverbrauch: Ineffiziente Kompressoren verbrauchen mehr Energie pro produzierter Luftmenge, was zu höheren Betriebskosten führt.
- Verminderte Luftqualität: Ineffiziente Kompressoren können mehr Verunreinigungen in die Druckluft einbringen, was zu Qualitätsproblemen in nachgelagerten Prozessen führen kann.
- Erhöhter Verschleiß: Kompressoren, die nicht optimal arbeiten, unterliegen oft einem erhöhten Verschleiß, was zu häufigeren Ausfällen und höheren Wartungskosten führt.
- Instabile Druckluftversorgung: Ineffiziente Kompressoren können Schwierigkeiten haben, einen stabilen Druck aufrechtzuerhalten, was zu Problemen in Produktionsprozessen führen kann.
- Erhöhte CO2-Emissionen: Der erhöhte Energieverbrauch ineffizienter Kompressoren trägt direkt zu erhöhten CO2-Emissionen bei.
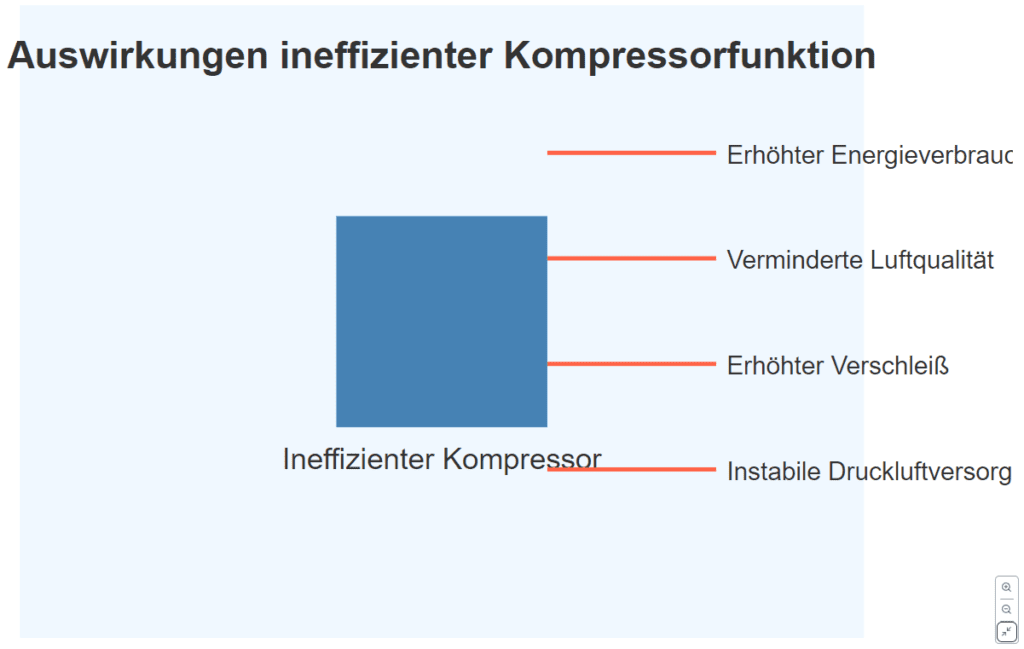
Lösungsansätze und Präventivmaßnahmen
Die Verbesserung der Kompressoreffizienz erfordert einen ganzheitlichen Ansatz:
1. Bedarfsanalyse und richtige Dimensionierung
Eine genaue Analyse des Druckluftbedarfs ist entscheidend für die Auswahl und Dimensionierung von Kompressoren.
Fallbeispiel: Ein Lebensmittelhersteller in Niedersachsen führte eine detaillierte Druckluftbedarfsanalyse durch. Basierend auf den Ergebnissen wurde das bestehende System mit drei 75 kW Kompressoren durch ein System mit einem 90 kW Grundlastkompressor, einem 45 kW Mittelastkompressor und einem 22 kW Spitzenlastkompressor ersetzt. Dies führte zu einer Reduktion des durchschnittlichen SEC von 7,3 kW/(m³/min) auf 6,1 kW/(m³/min) und einer jährlichen Energieeinsparung von 280.000 kWh.
2. Implementierung moderner Regelungssysteme
Moderne Regelungssysteme können die Kompressoreffizienz erheblich verbessern, insbesondere bei schwankendem Luftbedarf.
Fallbeispiel: Ein Automobilhersteller in Sachsen rüstete seine Kompressorstation mit einem intelligenten Steuerungssystem aus, das die Lastverteilung zwischen den Kompressoren optimiert und einen der Kompressoren mit einem Frequenzumrichter ausstattet. Dies ermöglichte eine präzise Anpassung der Drucklufterzeugung an den tatsächlichen Bedarf. Der durchschnittliche SEC konnte dadurch von 7,0 kW/(m³/min) auf 5,8 kW/(m³/min) gesenkt werden, was einer jährlichen Energieeinsparung von über 500.000 kWh entspricht.
3. Regelmäßige Wartung und Überwachung
Ein strukturiertes Wartungsprogramm ist essentiell für die Aufrechterhaltung der Kompressoreffizienz.
Fallbeispiel: Ein mittelständisches Unternehmen der Kunststoffverarbeitung in Thüringen implementierte ein präventives Wartungsprogramm mit kontinuierlicher Effizienzüberwachung für seine Kompressoren. Durch regelmäßige Reinigung, Austausch von Verschleißteilen und Optimierung der Einstellungen konnte der durchschnittliche SEC von 7,5 kW/(m³/min) auf 6,5 kW/(m³/min) gesenkt werden.
4. Optimierung der Ansaugbedingungen
Die Verbesserung der Ansaugbedingungen kann die Kompressoreffizienz signifikant steigern.
Fallbeispiel: Ein Chemieunternehmen in Rheinland-Pfalz optimierte die Belüftung seines Kompressorraums und verlegte die Ansaugöffnung nach außen. Dadurch konnte die durchschnittliche Ansaugtemperatur von 35°C auf 20°C gesenkt werden. Dies führte zu einer Reduktion des SEC von 7,8 kW/(m³/min) auf 7,0 kW/(m³/min).
5. Wärmerückgewinnung
Die Nutzung der Abwärme von Kompressoren kann die Gesamteffizienz des Systems erheblich verbessern.
Fallbeispiel: Ein Maschinenbauunternehmen in Bayern installierte ein Wärmerückgewinnungssystem an seinen Kompressoren. Die zurückgewonnene Wärme wird zur Heizung der Produktionshallen und zur Warmwasserbereitung genutzt. Obwohl der SEC der Kompressoren unverändert blieb, konnte durch die Wärmerückgewinnung der Gesamtenergieverbrauch des Unternehmens um 8% gesenkt werden.
Zukunftsperspektiven und innovative Ansätze
Die Verbesserung der Kompressoreffizienz ist ein Bereich kontinuierlicher Innovation:
- KI-gestützte Kompressorsteuerung: Künstliche Intelligenz und maschinelles Lernen können zur Optimierung der Kompressorsteuerung eingesetzt werden. Fallbeispiel: Ein Forschungsprojekt an der TU Dresden entwickelte ein KI-basiertes Steuerungssystem für Kompressorstationen. In ersten Feldversuchen bei einem Automobilzulieferer konnte das System den SEC um durchschnittlich 12% senken, indem es Luftbedarfsmuster vorhersagte und die Kompressorkonfiguration proaktiv anpasste.
- Hocheffiziente Motoren und Antriebe: Fortschritte in der Motorentechnologie versprechen weitere Effizienzsteigerungen. Fallbeispiel: Ein Kompressorhersteller aus Baden-Württemberg entwickelte einen neuen Schraubenkompressor mit einem hocheffizienten Permanentmagnet-Synchronmotor. In Feldtests konnte der neue Kompressor einen SEC von 5,2 kW/(m³/min) erreichen, was eine Verbesserung von 20% gegenüber herkömmlichen Modellen darstellt.
- Innovative Verdichtertechnologien: Neue Ansätze in der Verdichtertechnologie könnten zu signifikanten Effizienzsteigerungen führen. Fallbeispiel: Ein Start-up aus München entwickelte einen neuartigen Spiralverdichter, der in Laborversuchen einen SEC von 4,8 kW/(m³/min) erreichte. Das Unternehmen plant, die Technologie in Zusammenarbeit mit einem etablierten Kompressorhersteller zur Marktreife zu bringen.
- Integrierte Systemoptimierung: Ganzheitliche Ansätze, die Kompressoren, Aufbereitung und Verteilung als Gesamtsystem betrachten, versprechen weitere Effizienzgewinne. Fallbeispiel: Ein Konsortium aus Industrie und Forschung in Nordrhein-Westfalen entwickelte ein integriertes Optimierungssystem, das Kompressoren, Trockner, Filter und Verteilungsnetz als Gesamtsystem betrachtet. In einem Pilotprojekt bei einem großen Chemieunternehmen konnte der Gesamtenergieverbrauch des Druckluftsystems um 18% gesenkt werden.
- Hybride Druckluftsysteme: Die Kombination von Kompressoren mit Druckluftspeichern und innovativen Speichertechnologien könnte neue Möglichkeiten zur Effizienzsteigerung eröffnen. Fallbeispiel: Ein Energietechnikunternehmen aus Sachsen entwickelte ein hybrides Druckluftsystem, das Kompressoren mit einem adiabaten Druckluftspeicher kombiniert. In einem Testbetrieb bei einem mittelständischen Unternehmen konnte das System Lastspitzen abfangen und den durchschnittlichen SEC um 15% senken.
Fazit und Ausblick
Die Verbesserung der Kompressoreffizienz bleibt eine zentrale Herausforderung und Chance für Unternehmen, die Druckluftsysteme betreiben. Die in diesem Artikel vorgestellten Fallbeispiele zeigen, dass sowohl bewährte Methoden als auch innovative Ansätze signifikante Verbesserungen ermöglichen können.
Entscheidend für den Erfolg ist ein ganzheitlicher Ansatz, der nicht nur die Kompressoren selbst, sondern das gesamte Druckluftsystem einschließlich Aufbereitung, Verteilung und Verbrauch berücksichtigt. Die richtige Dimensionierung, effiziente Regelungsstrategien, regelmäßige Wartung und Überwachung sowie die Optimierung der Betriebsbedingungen sind Schlüsselelemente einer erfolgreichen Strategie zur Effizienzsteigerung.
Die wirtschaftlichen und ökologischen Vorteile einer verbesserten Kompressoreffizienz sind beträchtlich. In den vorgestellten Fallbeispielen konnten Energieeinsparungen von 10% bis 20% realisiert werden, was sich direkt in reduzierten Betriebskosten und verminderten CO2-Emissionen niederschlägt. Angesichts steigender Energiepreise und zunehmender regulatorischer Anforderungen im Bereich des Klimaschutzes wird die Effizienz von Kompressoren in Zukunft noch stärker in den Fokus rücken.
Blickt man in die Zukunft, so versprechen Entwicklungen in Bereichen wie künstliche Intelligenz, innovative Verdichtertechnologien und integrierte Systemoptimierung weitere Verbesserungen. Die Integration dieser Technologien in bestehende und neue Druckluftsysteme wird es ermöglichen, die Effizienz weiter zu steigern und gleichzeitig die Zuverlässigkeit und Flexibilität der Systeme zu erhöhen.
Besonders vielversprechend erscheinen Ansätze, die verschiedene Technologien intelligent kombinieren. So könnte beispielsweise ein KI-gesteuertes System, das hocheffiziente Kompressoren mit innovativen Speichertechnologien und einer ganzheitlichen Netzwerkoptimierung verbindet, zu Effizienzsteigerungen führen, die weit über das hinausgehen, was heute als Standard gilt.
Die Herausforderung für Unternehmen wird darin bestehen, mit den technologischen Entwicklungen Schritt zu halten und die für ihre spezifische Situation am besten geeigneten Lösungen zu identifizieren und umzusetzen. Dies erfordert nicht nur Investitionen in Technologie, sondern auch in Wissen und Kompetenzen. Kontinuierliche Fortbildung des technischen Personals, der Austausch von Best Practices und die enge Zusammenarbeit mit Technologieanbietern und Forschungseinrichtungen werden dabei entscheidende Erfolgsfaktoren sein.
Gleichzeitig wird die Bedeutung eines ganzheitlichen Energiemanagements zunehmen. Die Optimierung der Kompressoreffizienz sollte nicht isoliert betrachtet werden, sondern als Teil einer übergreifenden Strategie zur Verbesserung der Energieeffizienz und Nachhaltigkeit des gesamten Unternehmens. In diesem Kontext können Maßnahmen wie die Wärmerückgewinnung aus Kompressoren oder die Integration von Druckluftsystemen in intelligente Energiemanagementsysteme zusätzliche Synergien und Einsparungspotenziale erschließen.
Ein weiterer Trend, der sich abzeichnet, ist die zunehmende Vernetzung und Digitalisierung von Druckluftsystemen im Rahmen von Industrie 4.0-Konzepten. Die Möglichkeit, Betriebsdaten in Echtzeit zu erfassen, zu analysieren und darauf zu reagieren, wird zu einer neuen Ära der Effizienzoptimierung führen. Predictive Maintenance, automatische Anpassung an sich ändernde Produktionsbedingungen und die Optimierung des Gesamtsystems in Echtzeit werden zum Standard werden.
Die Ausführungen zu den zukünftigen Entwicklungen und innovativen Ansätzen sind faszinierend. Als Forscher im Bereich der künstlichen Intelligenz sehe ich großes Potenzial in der KI-gestützten Optimierung von Druckluftsystemen. Ein Aspekt, der meiner Meinung nach noch mehr Beachtung verdient, ist die Möglichkeit, Druckluftsysteme in das übergeordnete Energiemanagement von Produktionsanlagen zu integrieren. KI-Systeme könnten beispielsweise Produktionsplanungen mit der Steuerung von Kompressoren verknüpfen, um Lastspitzen zu vermeiden und die Effizienz weiter zu steigern.
Der Artikel hebt zu Recht die Bedeutung der regelmäßigen Wartung und Überwachung hervor. Als Techniker in einem Chemieunternehmen möchte ich ergänzen, dass wir sehr gute Erfahrungen mit der Implementierung eines kontinuierlichen Monitoring-Systems gemacht haben. Wir haben Sensoren an allen kritischen Punkten des Druckluftsystems installiert, die Daten in Echtzeit an ein zentrales System übermitteln. Dies ermöglicht uns nicht nur eine schnelle Reaktion auf Probleme, sondern auch eine datenbasierte Optimierung des Gesamtsystems. Die Investition hat sich durch reduzierte Ausfallzeiten und verbesserte Effizienz schnell amortisiert.
Die vorgestellten Fallbeispiele sind sehr aufschlussreich und praxisnah. Als Ingenieur in der Automobilindustrie kann ich die Bedeutung der richtigen Dimensionierung und Regelung von Kompressorsystemen bestätigen. Ein Aspekt, den ich gerne noch ergänzen würde, ist die Wichtigkeit der Schulung und Sensibilisierung der Mitarbeiter. In unserem Werk haben wir festgestellt, dass gut informierte Mitarbeiter oft wertvolle Hinweise zur Verbesserung der Effizienz geben können, da sie täglich mit den Anlagen arbeiten. Ein strukturiertes Vorschlagswesen für Energieeffizienzmaßnahmen hat bei uns zu einigen innovativen Lösungen geführt.
Der Artikel bietet einen umfassenden Überblick über die Herausforderungen und Lösungsansätze zur Verbesserung der Kompressoreffizienz. Als Energiemanager in einem mittelständischen Unternehmen finde ich besonders den Aspekt der ganzheitlichen Systembetrachtung interessant. In unserer Firma haben wir kürzlich begonnen, nicht nur die Kompressoren selbst, sondern auch das gesamte Druckluftnetz zu optimieren. Eine Maßnahme, die wir ergänzend umgesetzt haben, ist die Installation von Durchflussmessgeräten an strategischen Punkten im Netz. Dies ermöglicht uns, Leckagen schneller zu identifizieren und den Verbrauch einzelner Produktionsbereiche genauer zu analysieren.
Als Nachhaltigkeitsbeauftragter finde ich den Aspekt der CO2-Reduktion durch verbesserte Kompressoreffizienz besonders wichtig. Der Artikel erwähnt dies kurz, aber ich denke, dieser Punkt verdient mehr Aufmerksamkeit. In unserem Unternehmen haben wir die Effizienzsteigerung unseres Druckluftsystems in unsere Nachhaltigkeitsstrategie integriert. Wir berichten jährlich über die erzielten Energieeinsparungen und die damit verbundene CO2-Reduktion. Dies hat nicht nur intern zu einer höheren Akzeptanz für Investitionen in diesem Bereich geführt, sondern wird auch von unseren Kunden und Investoren sehr positiv wahrgenommen. Es wäre interessant gewesen, im Artikel noch mehr über die Quantifizierung und Berichterstattung von CO2-Einsparungen durch Effizienzmaßnahmen bei Druckluftsystemen zu erfahren.