Übermäßiger Druckabfall ist ein weit verbreitetes Problem in industriellen Druckluftsystemen, das erhebliche Auswirkungen auf die Effizienz, Produktivität und Betriebskosten haben kann. In diesem Artikel werden wir die Ursachen, Auswirkungen und Lösungen für dieses komplexe Problem eingehend untersuchen und dabei verschiedene Szenarien aus der industriellen Praxis betrachten.
Grundlagen des Druckabfalls
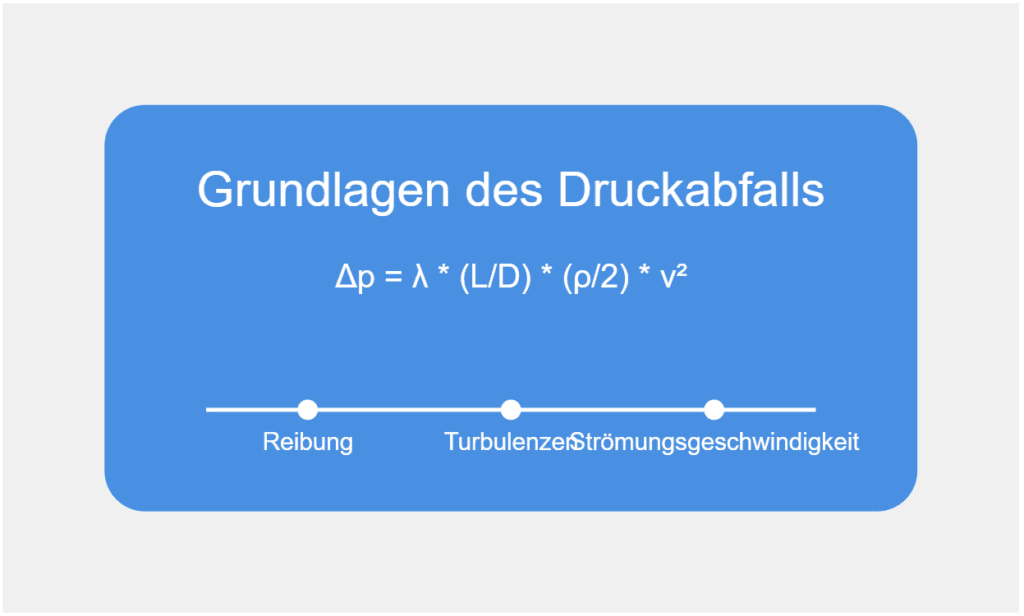
Zunächst ist es wichtig zu verstehen, dass ein gewisser Druckabfall in jedem Druckluftsystem unvermeidbar und sogar notwendig ist. Druckluft ist ein kompressibles Medium, und beim Strömen durch Rohrleitungen, Ventile, Filter und andere Komponenten verliert sie aufgrund von Reibung und Turbulenzen einen Teil ihres Drucks. Ein gut ausgelegtes System sollte einen Gesamtdruckabfall von nicht mehr als 0,1 bar pro 10 Meter Rohrlänge aufweisen.
Der Druckabfall in einem System lässt sich durch die Darcy-Weisbach-Gleichung beschreiben:
Δp = λ * (L/D) * (ρ/2) * v²
Dabei ist: Δp = Druckabfall λ = Rohrreibungszahl L = Rohrlänge D = Rohrdurchmesser ρ = Dichte des Mediums v = Strömungsgeschwindigkeit
Diese Gleichung verdeutlicht, dass der Druckabfall quadratisch mit der Strömungsgeschwindigkeit zunimmt und umgekehrt proportional zum Rohrdurchmesser ist. Dies erklärt, warum Engstellen und hohe Durchflussraten zu erheblichen Druckverlusten führen können.
Ursachen für übermäßigen Druckabfall
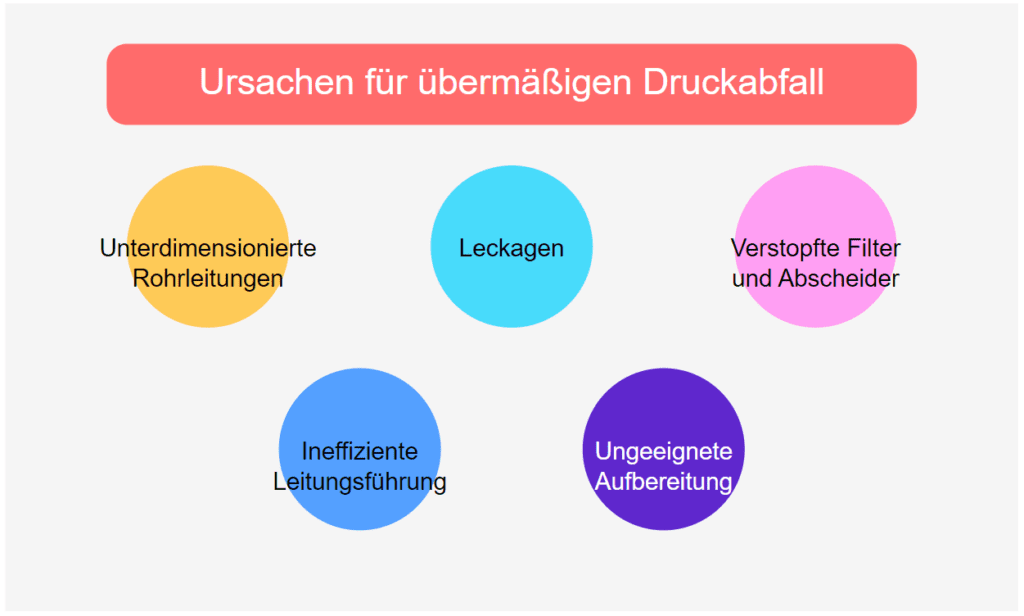
1. Unterdimensionierte Rohrleitungen
Eine der häufigsten Ursachen für übermäßigen Druckabfall sind unterdimensionierte Rohrleitungen. Dies tritt oft in älteren Anlagen auf, die im Laufe der Zeit erweitert wurden, ohne das Leitungssystem entsprechend anzupassen.
Fallbeispiel: Ein mittelständischer Automobilzulieferer in Baden-Württemberg hatte über Jahre hinweg seine Produktion erweitert und neue Maschinen installiert, ohne das Druckluftnetz zu vergrößern. Als Folge davon stieg die Strömungsgeschwindigkeit in den Hauptleitungen auf über 15 m/s, was zu einem Druckabfall von mehr als 1 bar führte. Dies resultierte in Leistungseinbußen bei den Produktionsmaschinen und erhöhtem Energieverbrauch der Kompressoren.
2. Leckagen
Leckagen sind ein weit verbreitetes und oft unterschätztes Problem in Druckluftsystemen. Selbst kleine Lecks können in der Summe zu erheblichen Druckverlusten führen. Nach Schätzungen des Fraunhofer-Instituts für System- und Innovationsforschung gehen in einem typischen industriellen Druckluftsystem 20-30% der erzeugten Druckluft durch Leckagen verloren.
Fallbeispiel: In einem großen Chemiewerk in Nordrhein-Westfalen führte man eine umfassende Leckageortung durch. Dabei wurden über 500 Leckagen identifiziert, die zusammen einen Luftverlust von etwa 1200 Normkubikmetern pro Stunde verursachten. Dies entsprach einem jährlichen Energieverlust von rund 600.000 kWh und Kosten von über 70.000 Euro.
3. Verstopfte Filter und Abscheider
Filter und Abscheider sind essenzielle Komponenten zur Sicherstellung der Druckluftqualität, können aber bei mangelnder Wartung zu erheblichen Druckverlusten führen. Mit zunehmender Verschmutzung steigt der Strömungswiderstand, was zu einem progressiv ansteigenden Druckabfall führt.
Fallbeispiel: Eine Brauerei in Bayern bemerkte einen stetigen Anstieg des Energieverbrauchs ihrer Kompressoren bei gleichbleibendem Luftbedarf. Eine Untersuchung ergab, dass die Coaleszenzfilter vor den Abfüllanlagen stark verschmutzt waren und einen Druckabfall von über 0,5 bar verursachten. Der erhöhte Gegendruck zwang die Kompressoren, mit höherem Druck zu arbeiten, was den Energieverbrauch um etwa 5% erhöhte.
4. Ineffiziente Leitungsführung
Die Art und Weise, wie Rohrleitungen verlegt sind, kann einen erheblichen Einfluss auf den Druckabfall haben. Scharfe Biegungen, plötzliche Querschnittsänderungen und unnötige Verzweigungen können zu Turbulenzen und erhöhten Druckverlusten führen.
Fallbeispiel: In einem Werk für Elektronikartikel in Thüringen stellte man fest, dass der Druck am Ende einer langen Produktionslinie deutlich niedriger war als erwartet. Eine Analyse der Leitungsführung zeigte, dass die Hauptleitung mehrere 90-Grad-Bögen und abrupte Querschnittsänderungen aufwies. Durch den Austausch der scharfen Bögen gegen großzügigere Radien und die Optimierung der Querschnittsübergänge konnte der Druckabfall um 0,4 bar reduziert werden.
5. Ungeeignete Aufbereitung
Eine unzureichende oder falsch dimensionierte Druckluftaufbereitung kann ebenfalls zu erhöhtem Druckabfall führen. Insbesondere Trockner und Öl-Wasser-Separatoren können bei Überlastung oder Fehlfunktion erhebliche Druckverluste verursachen.
Fallbeispiel: Ein Pharmaunternehmen in Hessen bemerkte, dass der Druck in seinem Reinraum-Druckluftsystem stetig abnahm. Eine Untersuchung ergab, dass der installierte Adsorptionstrockner für den tatsächlichen Luftbedarf unterdimensioniert war. Dies führte zu einer Überlastung des Trockners und einem Druckabfall von über 1 bar. Die Installation eines größeren Trockners löste das Problem und verbesserte gleichzeitig die Luftqualität.
Auswirkungen des übermäßigen Druckabfalls
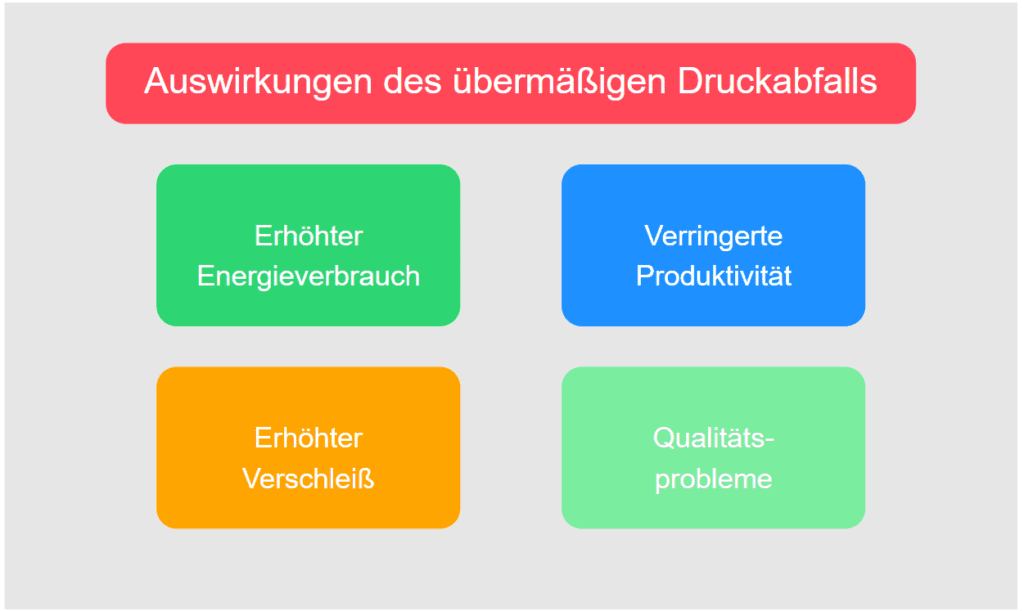
Die Folgen eines übermäßigen Druckabfalls sind vielfältig und können erhebliche wirtschaftliche Auswirkungen haben:
- Erhöhter Energieverbrauch: Um den Druckabfall zu kompensieren, müssen Kompressoren mit höherem Druck arbeiten. Als Faustregel gilt: Eine Erhöhung des Betriebsdrucks um 1 bar führt zu einem Anstieg des Energieverbrauchs um etwa 6-10%.
- Verringerte Produktivität: Niedrigerer Druck an den Verbrauchsstellen kann zu Leistungseinbußen bei pneumatischen Werkzeugen und Maschinen führen. Dies kann sich in längeren Zykluszeiten und verminderter Produktqualität äußern.
- Erhöhter Verschleiß: Kompressoren, die konstant an ihrer Leistungsgrenze arbeiten, um den Druckabfall zu kompensieren, unterliegen einem erhöhten Verschleiß. Dies führt zu häufigeren Wartungen und kürzeren Lebenszyklen der Anlagen.
- Qualitätsprobleme: In Prozessen, die eine präzise Druckluftqualität erfordern, kann ein übermäßiger Druckabfall zu Problemen führen. Beispielsweise kann in Lackieranlagen ein zu niedriger Druck zu einer ungleichmäßigen Farbverteilung führen.
- Erhöhte CO2-Emissionen: Der erhöhte Energieverbrauch aufgrund von Druckverlusten trägt direkt zu einer Erhöhung der CO2-Emissionen bei. In Zeiten zunehmender Klimaschutzbestrebungen und steigender CO2-Preise wird dieser Aspekt immer wichtiger.
Lösungsansätze und Präventivmaßnahmen
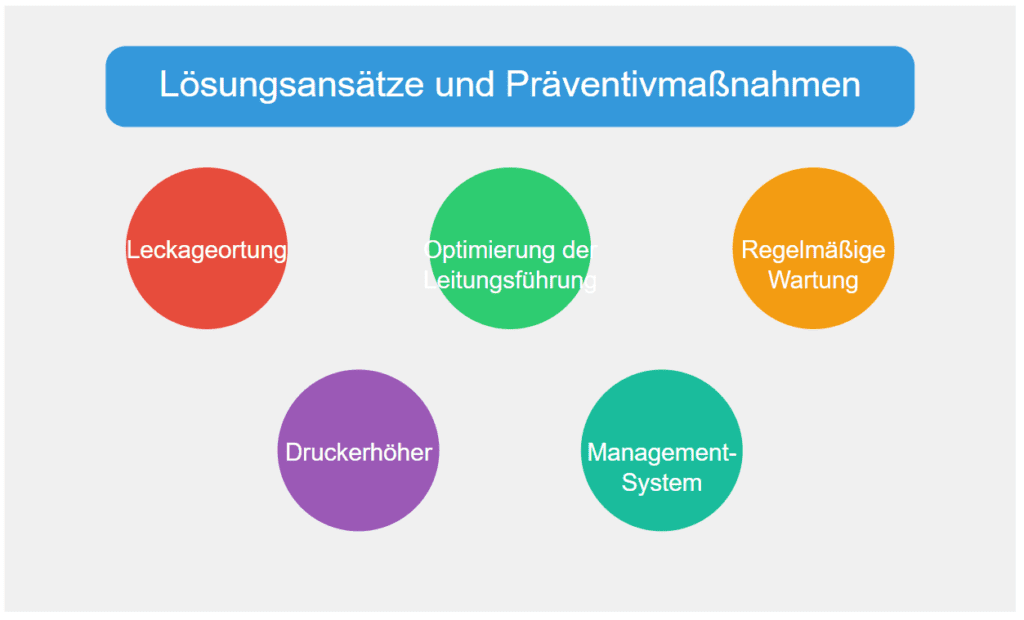
Die Bekämpfung von übermäßigem Druckabfall erfordert einen systematischen Ansatz, der sowohl technische als auch organisatorische Maßnahmen umfasst:
1. Systematische Leckageortung und -beseitigung
Ein regelmäßiges Leckage-Management-Programm ist entscheidend für die Effizienz des Druckluftsystems. Moderne Ultraschall-Leckagedetektoren ermöglichen eine präzise Ortung selbst kleinster Lecks.
Fallbeispiel: Ein großer Automobilhersteller in Niedersachsen implementierte ein vierteljährliches Leckage-Audit-Programm. Innerhalb eines Jahres konnten dadurch Leckagen reduziert und der Energieverbrauch des Druckluftsystems um 15% gesenkt werden. Die Investition in das Programm amortisierte sich innerhalb von sechs Monaten.
2. Optimierung der Leitungsführung
Eine Überprüfung und gegebenenfalls Neugestaltung des Leitungsnetzes kann erhebliche Verbesserungen bringen. Dabei sollten folgende Punkte beachtet werden:
- Verwendung von Bögen mit großem Radius statt scharfer Winkel
- Vermeidung von abrupten Querschnittsänderungen
- Installation von Ringleitungen zur gleichmäßigen Druckverteilung
- Korrekte Dimensionierung der Leitungen basierend auf dem tatsächlichen und zukünftig erwarteten Luftbedarf
Fallbeispiel: Ein Werkzeugmaschinenhersteller in Bayern investierte in eine komplette Neugestaltung seines Druckluftnetzes. Durch die Implementierung eines Ringleitungssystems und die Optimierung der Leitungsführung konnte der Druckabfall um 0,8 bar reduziert werden. Dies führte zu einer Energieeinsparung von 8% und einer Verbesserung der Luftqualität an den Verbrauchsstellen.
3. Regelmäßige Wartung und Austausch von Filtern
Ein strukturiertes Wartungsprogramm für Filter, Abscheider und andere Aufbereitungskomponenten ist essenziell. Die regelmäßige Reinigung oder der Austausch von Filterelementen kann den Druckabfall erheblich reduzieren.
Fallbeispiel: Ein Lebensmittelhersteller in Sachsen-Anhalt führte ein computergestütztes Wartungsmanagementsystem ein, das automatisch an fällige Filterwartungen erinnerte. Im ersten Jahr nach der Einführung konnte der durchschnittliche Druckabfall über die Filter um 0,3 bar reduziert werden, was zu einer Energieeinsparung von etwa 4% führte.
4. Einsatz von Druckerhöhern an kritischen Stellen
In Fällen, wo einzelne Verbraucher einen höheren Druck benötigen als der Rest des Systems, kann der Einsatz lokaler Druckerhöher sinnvoll sein. Dies ermöglicht es, den Systemdruck insgesamt niedriger zu halten und nur dort zu erhöhen, wo es tatsächlich nötig ist.
Fallbeispiel: Ein Hersteller von Präzisionsteilen in Baden-Württemberg hatte eine Produktionslinie, die einen Druck von 8 bar benötigte, während der Rest der Anlage mit 6 bar auskam. Durch die Installation eines Druckerhöhers für diese spezielle Linie konnte der Systemdruck um 2 bar gesenkt werden, was zu einer Energieeinsparung von 12% führte.
5. Implementierung eines Druckluftmanagement-Systems
Ein modernes Druckluftmanagement-System ermöglicht eine kontinuierliche Überwachung und Optimierung des Systems. Solche Systeme können Druckabfälle in Echtzeit erkennen und analysieren, wodurch eine proaktive Wartung ermöglicht wird.
Fallbeispiel: Ein Chemieunternehmen in Rheinland-Pfalz installierte ein umfassendes Druckluftmanagement-System mit Sensoren an kritischen Punkten im gesamten Netzwerk. Das System konnte innerhalb des ersten Betriebsjahres mehrere beginnende Leckagen frühzeitig erkennen und den Wartungsteams melden. Dadurch wurden größere Druckverluste verhindert und die Gesamteffizienz des Systems um 7% verbessert.
6. Schulung und Sensibilisierung des Personals
Ein oft übersehener Aspekt ist die Rolle des Personals. Mitarbeiter, die mit Druckluft arbeiten, sollten geschult werden, um die Bedeutung von Druckverlusten zu verstehen und Anomalien frühzeitig zu erkennen.
Fallbeispiel: Ein mittelständisches Unternehmen der Metallverarbeitung in Thüringen führte ein umfassendes Schulungsprogramm für alle Mitarbeiter durch, die mit Druckluft arbeiteten. Als Ergebnis stieg die Zahl der gemeldeten Leckagen und Unregelmäßigkeiten um 300%. Dies führte zu einer signifikanten Verbesserung der Systemeffizienz und einer Reduzierung des Energieverbrauchs um 10%.
Zukunftsperspektiven und innovative Ansätze
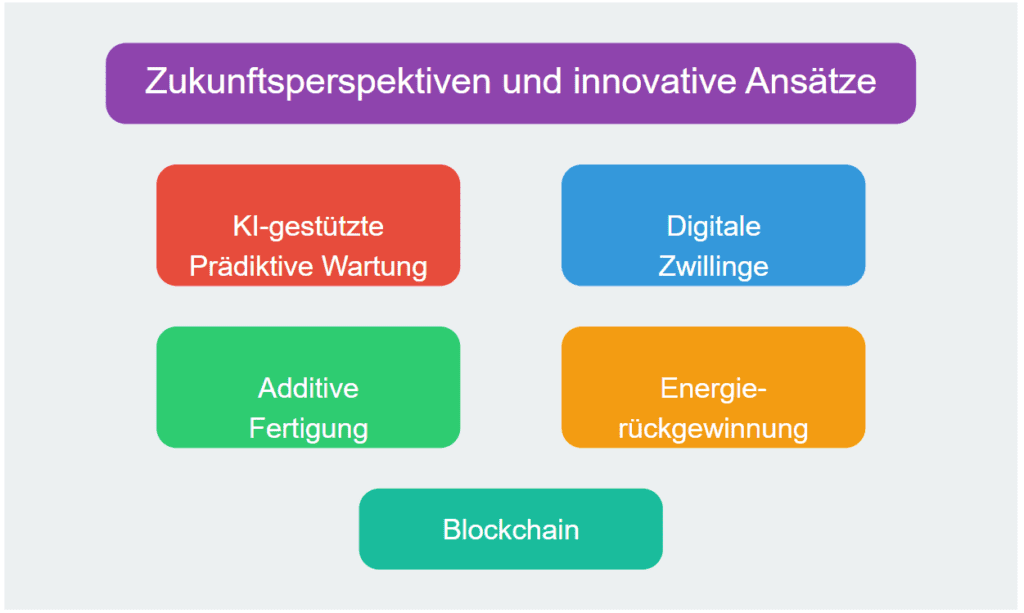
Zukunftsperspektiven und innovative Ansätze
Die Bekämpfung von Druckverlusten in Druckluftsystemen ist ein Bereich, in dem kontinuierlich Innovationen stattfinden. Einige vielversprechende Entwicklungen sind:
- KI-gestützte Prädiktive Wartung: Künstliche Intelligenz und maschinelles Lernen können genutzt werden, um Muster in Druckabfällen zu erkennen und potenzielle Probleme vorherzusagen, bevor sie kritisch werden. Diese Technologie ermöglicht eine proaktive statt einer reaktiven Wartung. Fallbeispiel: Ein großer Automobilhersteller in Bayern implementierte ein KI-basiertes Überwachungssystem für sein Druckluftnetz. Das System konnte innerhalb der ersten sechs Monate seiner Nutzung mehrere sich anbahnende Lecks und Filterverstopfungen vorhersagen, lange bevor sie mit herkömmlichen Methoden erkennbar gewesen wären. Dies führte zu einer Reduzierung ungeplanter Stillstandzeiten um 35% und einer Verbesserung der Gesamteffizienz des Druckluftsystems um 8%.
- Digitale Zwillinge: Die Erstellung digitaler Zwillinge von Druckluftsystemen ermöglicht es, verschiedene Szenarien zu simulieren und die Auswirkungen von Änderungen vorherzusagen, ohne das reale System zu beeinträchtigen. Fallbeispiel: Ein mittelständisches Unternehmen der Verpackungsindustrie in Sachsen nutzte einen digitalen Zwilling seines Druckluftsystems, um die Auswirkungen einer geplanten Produktionserweiterung zu simulieren. Durch die Simulation konnten potenzielle Engpässe im Druckluftnetz identifiziert und präventiv behoben werden, bevor die Erweiterung umgesetzt wurde. Dies ersparte dem Unternehmen kostspielige Nachrüstungen und Produktionsunterbrechungen.
- Additive Fertigung für optimierte Komponenten: 3D-Druck-Technologien ermöglichen die Herstellung von Komponenten mit komplexen inneren Geometrien, die den Druckabfall minimieren können. Fallbeispiel: Ein Hersteller von Pneumatikkomponenten in Baden-Württemberg entwickelte mittels additiver Fertigung neue Ventilblöcke mit optimierten Strömungswegen. Diese neuen Komponenten reduzierten den Druckabfall um 30% im Vergleich zu konventionell gefertigten Ventilen, was zu einer signifikanten Effizienzsteigerung in den Anlagen der Kunden führte.
- Energierückgewinnung aus Druckabfällen: Innovative Technologien zur Umwandlung von Druckenergie in elektrische Energie können helfen, die Verluste durch Druckabfälle teilweise zu kompensieren. Fallbeispiel: Ein Chemieunternehmen in Nordrhein-Westfalen installierte an mehreren Stellen seines Druckluftnetzes, an denen große Druckabfälle unvermeidbar waren, kleine Turbinen zur Energierückgewinnung. Diese Turbinen konnten etwa 15% der durch den Druckabfall verlorenen Energie zurückgewinnen und in das elektrische Netz des Unternehmens einspeisen.
- Selbstheilende Materialien für Rohrleitungen: Fortschritte in der Materialwissenschaft könnten zu Rohrleitungen führen, die kleine Lecks selbstständig abdichten können. Fallbeispiel: Ein Forschungsprojekt an der Technischen Universität München entwickelte ein Polymer-basiertes Rohrmaterial, das bei kleinen Rissen oder Löchern automatisch aufquillt und diese verschließt. In ersten Feldversuchen in einem mittelständischen Produktionsbetrieb konnte die Anzahl der kleinen Lecks um 60% reduziert werden, was zu einer deutlichen Verbesserung der Systemeffizienz führte.
- Blockchain für Druckluftmanagement: Die Blockchain-Technologie könnte genutzt werden, um ein dezentrales, manipulationssicheres System zur Überwachung und Optimierung von Druckluftnetzen zu schaffen. Fallbeispiel: Ein Konsortium von Industrieunternehmen in der Metropolregion Rhein-Neckar startete ein Pilotprojekt zur Implementierung einer Blockchain-basierten Plattform für das Management ihrer Druckluftsysteme. Die Plattform ermöglichte einen sicheren Austausch von Betriebsdaten und Best Practices, was zu einer kollektiven Verbesserung der Effizienz um durchschnittlich 12% führte.
- Hybride Druckluftsysteme: Die Integration von Drucklufterzeugung mit anderen Energiequellen, wie erneuerbaren Energien, kann zu flexibleren und effizienteren Systemen führen. Fallbeispiel: Ein Lebensmittelhersteller in Schleswig-Holstein implementierte ein hybrides System, das die Drucklufterzeugung mit einer Photovoltaikanlage und einem Batteriespeicher koppelte. An sonnigen Tagen konnte die Drucklufterzeugung vollständig mit Solarenergie betrieben werden, was zu einer Reduzierung der CO2-Emissionen um 40% führte.
Fazit und Ausblick
Die Beherrschung von Druckverlusten in industriellen Druckluftsystemen bleibt eine kontinuierliche Herausforderung, bietet aber auch enorme Chancen für Effizienzsteigerungen und Kosteneinsparungen. Die in diesem Artikel vorgestellten Fallbeispiele zeigen, dass sowohl bewährte Methoden als auch innovative Ansätze signifikante Verbesserungen ermöglichen können.
Entscheidend für den Erfolg ist ein ganzheitlicher Ansatz, der technische, organisatorische und personelle Aspekte berücksichtigt. Die Implementierung eines umfassenden Druckluftmanagements, regelmäßige Schulungen des Personals und die Nutzung moderner Technologien zur Überwachung und Optimierung sind Schlüsselelemente einer erfolgreichen Strategie.
Blickt man in die Zukunft, so versprechen Entwicklungen in Bereichen wie künstliche Intelligenz, additive Fertigung und neue Materialien weitere Verbesserungen. Die Integration von Druckluftsystemen in das Konzept der Industrie 4.0 wird es ermöglichen, diese noch enger mit anderen Produktionsprozessen zu verknüpfen und ganzheitlich zu optimieren.
Unternehmen, die proaktiv in die Optimierung ihrer Druckluftsysteme investieren, können nicht nur erhebliche Kosteneinsparungen realisieren, sondern auch ihre Wettbewerbsfähigkeit steigern und einen wichtigen Beitrag zum Klimaschutz leisten. Angesichts steigender Energiepreise und zunehmender regulatorischer Anforderungen im Bereich des Klimaschutzes wird die Effizienz von Druckluftsystemen in Zukunft noch stärker in den Fokus rücken.
Die Herausforderung für Unternehmen wird darin bestehen, mit den technologischen Entwicklungen Schritt zu halten und die für ihre spezifische Situation am besten geeigneten Lösungen zu identifizieren und umzusetzen. Kontinuierliche Fortbildung, der Austausch von Best Practices und die enge Zusammenarbeit mit Technologieanbietern und Forschungseinrichtungen werden dabei entscheidende Erfolgsfaktoren sein.
Letztendlich zeigt die Entwicklung im Bereich der Druckluftoptimierung exemplarisch, wie technologischer Fortschritt und innovative Ansätze dazu beitragen können, industrielle Prozesse nachhaltiger und effizienter zu gestalten – ein Trend, der sich in den kommenden Jahren zweifellos fortsetzen und verstärken wird.
Die vorgestellten Fallbeispiele sind sehr aufschlussreich und praxisnah. Als Energiemanager finde ich besonders den Ansatz der KI-gestützten prädiktiven Wartung interessant. In unserem Betrieb haben wir kürzlich begonnen, Maschinenlernalgorithmen zur Analyse unserer Druckluftdaten einzusetzen. Obwohl wir noch am Anfang stehen, konnten wir bereits einige versteckte Muster in unserem Druckluftverbrauch identifizieren, die uns bei der Optimierung helfen. Es wäre spannend gewesen, im Artikel noch mehr über die Herausforderungen bei der Implementierung solcher Systeme zu erfahren.
Als Nachhaltigkeitsbeauftragter finde ich den Aspekt der CO2-Reduktion durch optimierte Druckluftsysteme besonders wichtig. Der Artikel erwähnt dies kurz, aber ich denke, dieser Punkt verdient mehr Aufmerksamkeit. In unserem Unternehmen haben wir die Optimierung unseres Druckluftsystems in unsere Klimastrategie integriert. Durch die Kombination verschiedener Maßnahmen, einschließlich der im Artikel genannten, konnten wir unseren CO2-Fußabdruck im Bereich Druckluft um 25% reduzieren. Dies zeigt, dass Effizienzsteigerungen in der Drucklufttechnik einen signifikanten Beitrag zum Klimaschutz leisten können. Es wäre interessant gewesen, im Artikel noch mehr über Best Practices zur Integration von Druckluftoptimierung in unternehmensweite Nachhaltigkeitsstrategien zu erfahren.
Die Ausführungen zu den innovativen Ansätzen wie additive Fertigung und selbstheilende Materialien sind faszinierend. Als Forscher im Bereich der Materialwissenschaften sehe ich hier großes Potenzial. Ein weiterer vielversprechender Ansatz, der meiner Meinung nach Erwähnung verdient, ist die Entwicklung von Nano-Beschichtungen für Rohrleitungen. Diese könnten den Reibungswiderstand signifikant reduzieren und somit den Druckabfall minimieren. Erste Laborversuche in unserem Institut zeigen vielversprechende Ergebnisse, wobei die Herausforderung nun in der Skalierung für industrielle Anwendungen liegt.
Der Artikel hebt zu Recht die Bedeutung der Leckageortung und -beseitigung hervor. Als Techniker in einem Chemieunternehmen möchte ich ergänzen, dass wir sehr gute Erfahrungen mit akustischen Kamerasystemen gemacht haben. Diese ermöglichen es uns, Lecks aus sicherer Entfernung zu lokalisieren, was besonders in Bereichen mit gefährlichen Substanzen von Vorteil ist. Zudem haben wir ein Anreizsystem für Mitarbeiter eingeführt, die Lecks melden. Dies hat zu einer deutlichen Steigerung des Bewusstseins für Drucklufteffizenz in der gesamten Belegschaft geführt.
Der Artikel bietet einen umfassenden Überblick über die Problematik des übermäßigen Druckabfalls in Druckluftsystemen. Als Ingenieur in der Fertigungsindustrie kann ich die Relevanz dieses Themas bestätigen. Ein Aspekt, den ich gerne noch hervorheben möchte, ist die Bedeutung der regelmäßigen Schulung des Wartungspersonals. In unserem Unternehmen haben wir festgestellt, dass gut geschulte Techniker nicht nur effizienter bei der Fehlersuche sind, sondern auch proaktiv Verbesserungsvorschläge einbringen. Dies hat zu einer kontinuierlichen Optimierung unseres Druckluftsystems geführt.