Druckluft, die den Anforderungen der ISO 8573-1 entspricht, spielt in der modernen Industrie als vielseitige und zuverlässige Energiequelle eine unersetzliche Rolle. Sie wird oft als die „vierte Utilität“ neben Strom, Wasser und Gas bezeichnet und findet in nahezu allen Industriezweigen Anwendung. Von der Automobilindustrie über die Lebensmittelverarbeitung bis hin zur Pharmazie und Elektronikfertigung – Druckluft ist ein essentieller Bestandteil zahlreicher Produktionsprozesse und Anwendungen. Der Preis der Druckluftproduktion hängt eng von der Qualität der Druckluft ab. Hochwertige Druckluft kostet immer mehr.
Die Bedeutung von Druckluft in der Industrie lässt sich an mehreren Faktoren festmachen:
- Vielseitigkeit: Druckluft kann für eine Vielzahl von Aufgaben eingesetzt werden, darunter Antrieb von Pneumatikzylindern und -motoren, Reinigung, Trocknung, Lackierung, Förderung von Schüttgütern und vieles mehr. Diese Flexibilität macht sie zu einem unverzichtbaren Medium in der Produktion.
- Sicherheit: Im Gegensatz zu elektrischen Systemen ist Druckluft nicht brennbar und erzeugt keine Funken. Dies macht sie besonders geeignet für Anwendungen in explosionsgefährdeten Bereichen oder in der Nähe leicht entzündlicher Materialien.
- Sauberkeit: In Branchen mit hohen Hygieneanforderungen wie der Lebensmittel- oder Pharmaindustrie bietet Druckluft den Vorteil, dass sie bei Leckagen keine Verunreinigungen hinterlässt.
- Präzision und Kontrolle: Pneumatische Systeme ermöglichen eine präzise Steuerung von Kraft und Geschwindigkeit, was sie ideal für Anwendungen macht, die eine genaue Kontrolle erfordern.
- Energiespeicherung: Druckluft kann in Tanks gespeichert und bei Bedarf abgerufen werden, was eine gewisse Pufferung und Flexibilität in der Energieversorgung ermöglicht.
Trotz dieser Vorteile steht die Industrie vor der Herausforderung, dass die Erzeugung von Druckluft mit erheblichen Energiekosten verbunden ist. Tatsächlich ist die Drucklufterzeugung in vielen Unternehmen einer der größten Energieverbraucher. Studien zeigen, dass in manchen Fällen bis zu 30% des gesamten industriellen Stromverbrauchs auf die Drucklufterzeugung entfallen können(Tian et al., 2014). Diese hohen Energiekosten machen eine genaue Kostenanalyse und Effizienzbetrachtung unerlässlich.
Die Notwendigkeit einer detaillierten Kostenanalyse für Druckluft ergibt sich aus mehreren Gründen:
- Energieeffizienz: In Zeiten steigender Energiepreise und wachsenden Umweltbewusstseins ist die Optimierung des Energieverbrauchs ein zentrales Anliegen für Unternehmen. Eine genaue Kenntnis der Druckluftkosten ist der erste Schritt zur Identifizierung von Einsparpotentialen.
- Betriebskostenoptimierung: Druckluft ist oft eine „versteckte“ Kostenstelle, da die tatsächlichen Kosten pro Kubikmeter nicht immer transparent sind. Eine detaillierte Analyse kann helfen, die Gesamtbetriebskosten zu senken und die Wettbewerbsfähigkeit zu verbessern.
- Investitionsentscheidungen: Bei der Anschaffung neuer Kompressoren oder der Modernisierung bestehender Anlagen ist eine genaue Kenntnis der Lebenszykluskosten unerlässlich, um fundierte Entscheidungen treffen zu können.
- Compliance und Nachhaltigkeit: Viele Unternehmen sind zunehmend verpflichtet, ihren Energieverbrauch und CO2-Ausstoß zu reduzieren. Eine genaue Kostenanalyse der Druckluft ist ein wichtiger Baustein in der Gesamtstrategie zur Verbesserung der Energieeffizienz und Nachhaltigkeit.
- Prozessoptimierung: Die Kenntnis der genauen Druckluftkosten ermöglicht es, Produktionsprozesse zu optimieren und alternative Technologien dort einzusetzen, wo sie wirtschaftlicher sind.
Um die tatsächlichen Kosten von Druckluft zu ermitteln, reicht es nicht aus, nur den Stromverbrauch des Kompressors zu betrachten. Eine umfassende Analyse muss verschiedene Faktoren berücksichtigen:
- Energiekosten für die Kompression
- Wartungs- und Instandhaltungskosten
- Kapitalkosten für die Anschaffung der Anlagen
- Kosten für die Aufbereitung der Druckluft (Trocknung, Filterung)
- Verluste durch Leckagen im Druckluftnetz
- Kosten für die Kühlung der Kompressoren
- Personalkosten für Betrieb und Wartung
Darüber hinaus müssen auch indirekte Kosten berücksichtigt werden, wie etwa der Platzbedarf für die Kompressoren oder die Auswirkungen auf andere Prozesse im Unternehmen.
Die Komplexität dieser Kostenstruktur macht deutlich, warum eine detaillierte Analyse so wichtig ist. Nur wenn alle Kostenfaktoren berücksichtigt werden, lässt sich ein realistisches Bild der tatsächlichen Kosten pro Kubikmeter Druckluft zeichnen. Dies ist die Grundlage für jede Optimierungsstrategie und für fundierte Entscheidungen im Bereich der Drucklufttechnik.
In den letzten Jahren hat das Bewusstsein für die Bedeutung der Energieeffizienz in der Industrie stark zugenommen. Dies spiegelt sich auch in verschiedenen nationalen und internationalen Initiativen wider. So hat beispielsweise die Europäische Kommission in ihrer Energieunionsstrategie von 2015 die Verbesserung der Energieeffizienz als eines der Hauptziele definiert(Đukić & Zidar, 2021). Auch Länder wie Serbien und Kroatien haben diese Ziele in ihre nationalen Strategien aufgenommen und setzen verschiedene Investitionsprojekte in diesem Bereich um.
Die Optimierung von Druckluftsystemen bietet hier ein erhebliches Potential zur Verbesserung der Gesamtenergieeffizienz eines Unternehmens. Studien haben gezeigt, dass durch gezielte Maßnahmen Energieeinsparungen von 20-50% in Druckluftsystemen möglich sind. Dies unterstreicht die Notwendigkeit, sich intensiv mit den Kosten und der Effizienz von Druckluft auseinanderzusetzen.
In den folgenden Abschnitten werden wir uns detailliert mit den verschiedenen Aspekten der Druckluftkostenanalyse befassen. Wir werden die Faktoren untersuchen, die die Kosten beeinflussen, Methoden zur Berechnung der Druckluftkosten vorstellen und Strategien zur Kostenoptimierung diskutieren.
Druckluft spielt eine wichtige Rolle in der Lebensmittelproduktion, wird aber oft als „unsichtbarer Energieträger“ übersehen. Die Kosten für 1m3 Druckluft variieren je nach Anlagengröße, Effizienz und Energiepreisen. Durchschnittlich liegen sie zwischen 1,5 und 2,5 Cent pro m3. Allerdings können sie in ineffizienten Systemen bis zu 3,5 Cent pro m3 betragen. Um die Kosten zu senken, sollten Unternehmen regelmäßig ihre Druckluftanlagen warten, Leckagen beheben und energieeffiziente Kompressoren einsetzen.
Eine optimierte Druckluftproduktion kann erhebliche Einsparungen bei der Druckluftproduktion in der Lebensmittelindustrie ermöglichen. In der Lebensmittelproduktion spielt die Reinheit der Druckluft eine entscheidende Rolle für die Qualität und Sicherheit der Produkte. Kontaminierte Druckluft kann Mikroorganismen, Öl oder andere Schadstoffe in die Lebensmittel einbringen und somit die Gesundheit der Verbraucher gefährden. Daher müssen strenge Hygienestandards eingehalten werden, die eine regelmäßige Wartung und Überprüfung der Druckluftsysteme beinhalten. Moderne Filtersysteme und Aufbereitungsanlagen sorgen dafür, dass die verwendete Druckluft frei von Verunreinigungen ist und den hohen Anforderungen der Lebensmittelindustrie entspricht.
Die Kosten für Druckluft werden von verschiedenen Faktoren beeinflusst, wobei die Taupunktmessung eine wichtige Rolle spielt. Der Taupunkt gibt an, bei welcher Temperatur die Feuchtigkeit in der Druckluft kondensiert. Eine präzise Taupunktmessung ermöglicht eine effiziente Steuerung der Lufttrocknung, was den Energieverbrauch und damit die Betriebskosten senkt. Zudem verhindert ein niedriger Taupunkt Korrosion und Probleme durch Kondenswasser in den Leitungen und Maschinen, was wiederum Wartungskosten reduziert. Allerdings erfordert eine zu starke Trocknung mehr Energie, weshalb eine optimale Balance gefunden werden muss, um die Gesamtkosten der Drucklufterzeugung zu minimieren.
Faktoren, die die Kosten von Druckluft beeinflussen
Die Kosten für Druckluft werden von einer Vielzahl von Faktoren beeinflusst, die in ihrer Gesamtheit betrachtet werden müssen, um ein umfassendes Bild der tatsächlichen Kosten pro Kubikmeter Druckluft zu erhalten. Im Folgenden werden die wichtigsten Einflussfaktoren detailliert erläutert.
2.1 Energiekosten
Die Energiekosten stellen in der Regel den größten Anteil an den Gesamtkosten der Drucklufterzeugung dar. Sie setzen sich aus zwei Hauptkomponenten zusammen:
Stromverbrauch der Kompressoren: Der Stromverbrauch der Kompressoren ist der primäre Treiber der Energiekosten. Moderne Druckluftsysteme können bis zu 30% des gesamten industriellen Stromverbrauchs ausmachen. Der tatsächliche Verbrauch hängt von verschiedenen Faktoren ab, wie der Effizienz des Kompressors, der Betriebszeit, dem Druckniveau und dem Lastprofil. Es ist wichtig zu beachten, dass Kompressoren auch im Leerlauf Energie verbrauchen, was die Gesamteffizienz des Systems beeinträchtigen kann.
Intelligente Druckluftsysteme, wie sie von Reisinger et al. (2019) beschrieben werden, können dazu beitragen, den Energieverbrauch zu optimieren. Durch die Implementierung von Datenerfassungs- und Analysesystemen gemäß ISO 20140 können Unternehmen die Energieeffizienz ihrer Druckluftsysteme genau überwachen und verbessern (Reisinger et al., 2019).
Aktuelle Energiepreise und deren Entwicklung: Die Volatilität der Energiepreise hat einen erheblichen Einfluss auf die Gesamtkosten der Drucklufterzeugung. In den letzten Jahren haben viele Länder, einschließlich Deutschland, steigende Energiepreise erlebt. Diese Entwicklung macht es umso wichtiger, den Energieverbrauch von Druckluftsystemen zu optimieren. Langfristige Prognosen für Energiepreise sollten bei der Planung und Bewertung von Investitionen in Druckluftsysteme berücksichtigt werden.
2.2 Anlageneffizienz
Die Effizienz der Druckluftanlage hat einen direkten Einfluss auf die Betriebskosten. Zwei Hauptaspekte sind hier zu betrachten:
Wirkungsgrad der Kompressoren: Der Wirkungsgrad eines Kompressors gibt an, wie effizient er elektrische Energie in Druckluft umwandelt. Moderne Kompressoren können Wirkungsgrade von bis zu 90% erreichen, aber in der Praxis liegt der durchschnittliche Wirkungsgrad oft deutlich darunter. Faktoren wie Alter der Anlage, Wartungszustand und Betriebsbedingungen beeinflussen den Wirkungsgrad. Eine regelmäßige Überprüfung und Optimierung des Kompressorbetriebs kann zu erheblichen Energieeinsparungen führen.
Verluste durch Leckagen im System: Leckagen sind ein oft unterschätzter Kostenfaktor in Druckluftsystemen. Studien zeigen, dass in vielen industriellen Anlagen bis zu 30% der erzeugten Druckluft durch Leckagen verloren gehen. Diese Verluste erhöhen nicht nur den Energieverbrauch, sondern führen auch zu einer Überdimensionierung der Kompressoren, was wiederum die Investitions- und Betriebskosten erhöht. Ein systematisches Leckagemanagement, einschließlich regelmäßiger Inspektionen und Reparaturen, ist entscheidend für die Kostenoptimierung.
2.3 Wartungs- und Instandhaltungskosten
Die Wartung und Instandhaltung von Druckluftsystemen ist ein wesentlicher Kostenfaktor, der oft unterschätzt wird. Regelmäßige Wartung ist jedoch unerlässlich, um die Effizienz und Zuverlässigkeit des Systems zu gewährleisten und ungeplante Ausfälle zu vermeiden.
Zu den Wartungskosten gehören:
- Regelmäßige Inspektionen und Reinigungen
- Austausch von Verschleißteilen wie Filtern und Ölen
- Reparaturen und Ersatz defekter Komponenten
- Kosten für Wartungspersonal oder externe Dienstleister
Moderne Ansätze wie die von Bublitz und Kern (2005) vorgeschlagene Optimierung von Wartungs- und Instandhaltungsprozessen durch Wearable Computing können dazu beitragen, diese Kosten zu reduzieren und die Effizienz der Wartungsarbeiten zu steigern (Bublitz & Kern, 2005). Solche innovativen Technologien ermöglichen eine präzisere Planung und Durchführung von Wartungsarbeiten, was zu einer Verringerung der Ausfallzeiten und einer Verlängerung der Lebensdauer der Anlagen führen kann.
2.4 Investitionskosten für Druckluftsysteme
Die Investitionskosten für ein Druckluftsystem sind ein bedeutender Faktor bei der Gesamtkostenbetrachtung, insbesondere wenn man die Lebenszykluskosten berücksichtigt. Zu den Investitionskosten gehören:
- Anschaffungskosten für Kompressoren und Peripheriegeräte
- Kosten für Rohrleitungen und Verteilungssysteme
- Kosten für Steuerungs- und Überwachungssysteme
- Bauliche Maßnahmen zur Installation der Anlage
Bei der Betrachtung der Investitionskosten ist es wichtig, nicht nur den Anschaffungspreis zu berücksichtigen, sondern auch die langfristigen Auswirkungen auf die Betriebskosten. Ein höherer Investitionsbetrag in effizientere Technologie kann sich durch niedrigere Energiekosten über die Lebensdauer der Anlage amortisieren.
Die Refinanzierung der Investitionskosten, wie von Strobel (2017) diskutiert, ist ein wichtiger Aspekt bei der Planung von Druckluftsystemen (Strobel, 2017). Unternehmen müssen sorgfältig abwägen, wie sie die Investitionen finanzieren und wie sich diese auf ihre Gesamtkostenstruktur auswirken.
Zusammenfassend lässt sich sagen, dass die Kosten von Druckluft von einer Vielzahl von Faktoren beeinflusst werden, die in ihrer Gesamtheit betrachtet werden müssen. Eine ganzheitliche Betrachtung, die Energiekosten, Anlageneffizienz, Wartungskosten und Investitionskosten einbezieht, ist unerlässlich, um die tatsächlichen Kosten pro Kubikmeter Druckluft zu ermitteln und Optimierungspotenziale zu identifizieren. Nur durch ein umfassendes Verständnis dieser Faktoren können Unternehmen effektive Strategien zur Kostenoptimierung und Effizienzsteigerung ihrer Druckluftsysteme entwickeln und umsetzen.
Druckluft ist eine unverzichtbare Energieform in vielen industriellen Prozessen und wird oft als die „vierte Versorgungsleistung“ neben Strom, Wasser und Gas bezeichnet. Trotz ihrer weitverbreiteten Nutzung wird die Effizienz und Kostenstruktur von Druckluftsystemen häufig unterschätzt oder nicht ausreichend analysiert. In der heutigen Zeit, in der Energieeffizienz und Kosteneinsparungen zunehmend in den Fokus rücken, ist es von entscheidender Bedeutung, die tatsächlichen Kosten der Drucklufterzeugung und -nutzung genau zu verstehen und zu quantifizieren.
Die Komplexität der Kostenberechnung für Druckluft ergibt sich aus der Vielzahl von Faktoren, die berücksichtigt werden müssen. Diese reichen von den offensichtlichen Energiekosten für den Betrieb der Kompressoren bis hin zu weniger offensichtlichen Aspekten wie Wartungskosten, Leckageverlusten und der Effizienz des gesamten Druckluftsystems. Eine genaue Kostenanalyse ist nicht nur für die Budgetplanung von Unternehmen wichtig, sondern auch für die Identifizierung von Optimierungspotentialen und die Rechtfertigung von Investitionen in effizientere Technologien.
In diesem Kontext ist es wichtig zu erwähnen, dass die Kosten für Druckluft oft unterschätzt werden. Studien haben gezeigt, dass in vielen Industriebetrieben bis zu 30% des gesamten Stromverbrauchs auf die Drucklufterzeugung entfallen können . Diese Erkenntnis unterstreicht die Notwendigkeit einer detaillierten und präzisen Kostenberechnung, um das volle Einsparpotenzial zu erkennen und zu nutzen.
Berechnung der Druckluftkosten
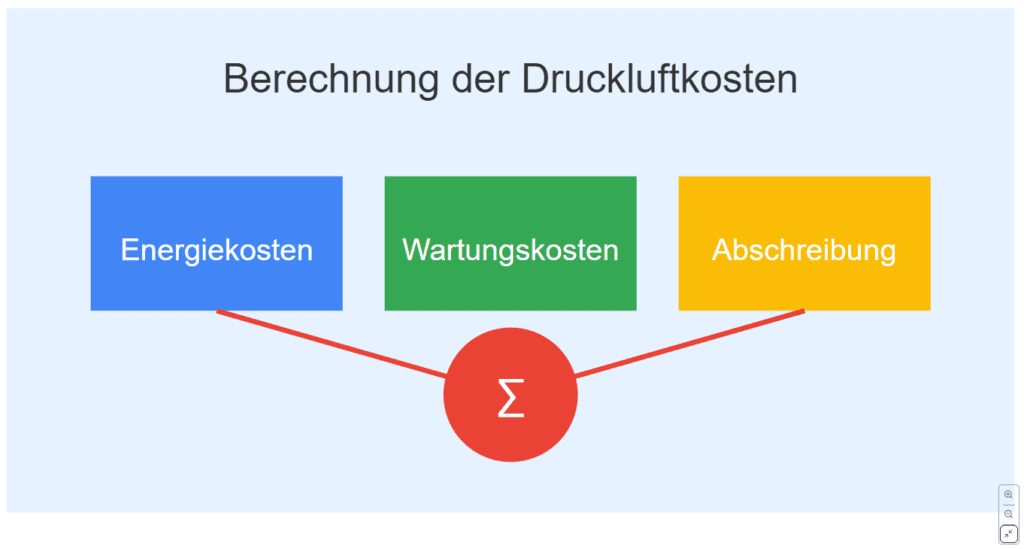
3.1 Grundformel zur Kostenberechnung
Die Berechnung der Druckluftkosten basiert auf einer Grundformel, die verschiedene Kostenfaktoren berücksichtigt. Diese Formel kann wie folgt dargestellt werden:
Gesamtkosten = (Energiekosten + Wartungskosten + Abschreibungskosten) / Druckluftmenge
Dabei ist es wichtig, jeden dieser Faktoren genau zu definieren und zu quantifizieren:
Energiekosten: Dies sind in der Regel die größten Kostentreiber und umfassen den Stromverbrauch der Kompressoren und aller zugehörigen Systeme wie Trockner und Kühler. Die Energiekosten werden berechnet, indem der Stromverbrauch in kWh mit dem aktuellen Strompreis multipliziert wird.
Wartungskosten: Diese beinhalten alle regelmäßigen und unvorhergesehenen Wartungsarbeiten, einschließlich Ersatzteile, Arbeitsstunden und eventuelle Ausfallzeiten. Es ist üblich, die Wartungskosten als Prozentsatz der Investitionskosten oder als festen Betrag pro Betriebsstunde anzusetzen.
Abschreibungskosten: Diese repräsentieren die Investitionskosten für das Druckluftsystem, verteilt über seine erwartete Lebensdauer. Die lineare Abschreibung ist hier eine gängige Methode, bei der die Anschaffungskosten gleichmäßig über die Nutzungsdauer verteilt werden.
Druckluftmenge: Dies ist das Volumen der produzierten Druckluft, typischerweise gemessen in Normkubikmetern (Nm³).
Es ist wichtig zu beachten, dass diese Grundformel je nach spezifischen Anforderungen und Gegebenheiten des Unternehmens angepasst werden kann. Zum Beispiel können zusätzliche Faktoren wie Raumkosten für die Unterbringung der Kompressoren oder Kosten für Kühlwasser hinzugefügt werden, um ein noch genaueres Bild der Gesamtkosten zu erhalten.
3.2 Berücksichtigung von Leckagen und Verlusten
Ein oft unterschätzter, aber signifikanter Faktor bei der Berechnung der Druckluftkosten sind Leckagen und Verluste im System. Diese können die Effizienz des gesamten Druckluftsystems erheblich beeinträchtigen und somit die Kosten pro Kubikmeter Druckluft deutlich erhöhen.
Leckagen: In vielen industriellen Druckluftsystemen gehen bis zu 30% der erzeugten Druckluft durch Leckagen verloren . Um diesen Faktor in die Kostenberechnung einzubeziehen, kann man folgende Formel verwenden:
Effektive Druckluftmenge = Erzeugte Druckluftmenge * (1 – Leckageverlustrate)
Dabei ist die Leckageverlustrate der prozentuale Anteil der Druckluft, der durch Leckagen verloren geht. Diese Rate kann durch regelmäßige Leckageprüfungen und -messungen ermittelt werden.
Druckverluste: Neben Leckagen können auch Druckverluste in Rohrleitungen und Komponenten die Effizienz des Systems beeinträchtigen. Diese Verluste führen dazu, dass mehr Energie aufgewendet werden muss, um den gewünschten Druck am Verbrauchsort zu erreichen. Die Berücksichtigung von Druckverlusten kann durch einen Korrekturfaktor in die Kostenberechnung einfließen:
Korrigierte Energiekosten = Energiekosten * (1 + Druckverlustfaktor)
Der Druckverlustfaktor hängt von der Systemkonfiguration ab und kann durch Messungen oder Berechnungen basierend auf den Rohrleitungslängen und -durchmessern ermittelt werden.
3.3 Beispielrechnung für 1m³ Druckluft
Um die praktische Anwendung der oben genannten Formeln zu veranschaulichen, folgt nun eine Beispielrechnung für die Kosten von 1m³ Druckluft. Für dieses Beispiel nehmen wir folgende Annahmen an:
- Strompreis: 0,20 €/kWh
- Spezifische Leistung des Kompressors: 0,12 kWh/m³
- Wartungskosten: 15% der jährlichen Energiekosten
- Abschreibungskosten: 10% der Investitionskosten pro Jahr
- Investitionskosten: 50.000 € für eine Anlage mit einer Jahresproduktion von 1.000.000 m³
- Leckageverlustrate: 10%
- Druckverlustfaktor: 5%
Schritt 1: Berechnung der Energiekosten pro m³ Energiekosten = Spezifische Leistung * Strompreis Energiekosten = 0,12 kWh/m³ * 0,20 €/kWh = 0,024 €/m³
Schritt 2: Berücksichtigung von Druckverlusten Korrigierte Energiekosten = 0,024 €
Druckluft ist eine unverzichtbare Energieform in vielen industriellen Prozessen und wird oft als die „vierte Versorgungsleistung“ neben Strom, Wasser und Gas bezeichnet. Trotz ihrer weitverbreiteten Nutzung wird die Effizienz und Kostenstruktur von Druckluftsystemen häufig unterschätzt oder nicht ausreichend analysiert. In der heutigen Zeit, in der Energieeffizienz und Kosteneinsparungen zunehmend in den Fokus rücken, ist es von entscheidender Bedeutung, die tatsächlichen Kosten der Drucklufterzeugung und -nutzung genau zu verstehen und zu quantifizieren.
Die Komplexität der Kostenberechnung für Druckluft ergibt sich aus der Vielzahl von Faktoren, die berücksichtigt werden müssen. Diese reichen von den offensichtlichen Energiekosten für den Betrieb der Kompressoren bis hin zu weniger offensichtlichen Aspekten wie Wartungskosten, Leckageverlusten und der Effizienz des gesamten Druckluftsystems. Eine genaue Kostenanalyse ist nicht nur für die Budgetplanung von Unternehmen wichtig, sondern auch für die Identifizierung von Optimierungspotentialen und die Rechtfertigung von Investitionen in effizientere Technologien.
In diesem Kontext ist es wichtig zu erwähnen, dass die Kosten für Druckluft oft unterschätzt werden. Studien haben gezeigt, dass in vielen Industriebetrieben bis zu 30% des gesamten Stromverbrauchs auf die Drucklufterzeugung entfallen können(Dawel & Pehlken, 2023). Diese Erkenntnis unterstreicht die Notwendigkeit einer detaillierten und präzisen Kostenberechnung, um das volle Einsparpotenzial zu erkennen und zu nutzen.
Die jüngsten Entwicklungen in der Industrie 4.0 und die damit verbundenen Fortschritte in der Sensorik und Datenanalyse eröffnen neue Möglichkeiten für ein effizientes Energiemanagement im Bereich der Druckluftsysteme. Insbesondere die Implementierung von Smart Services und automatisierten Überwachungssystemen verspricht eine signifikante Verbesserung in der Erkennung und Quantifizierung von Leckagen, die einen erheblichen Anteil an den Gesamtkosten der Drucklufterzeugung ausmachen können(Brand, 2023).
Energiemonitoring und Leckagenerkennung
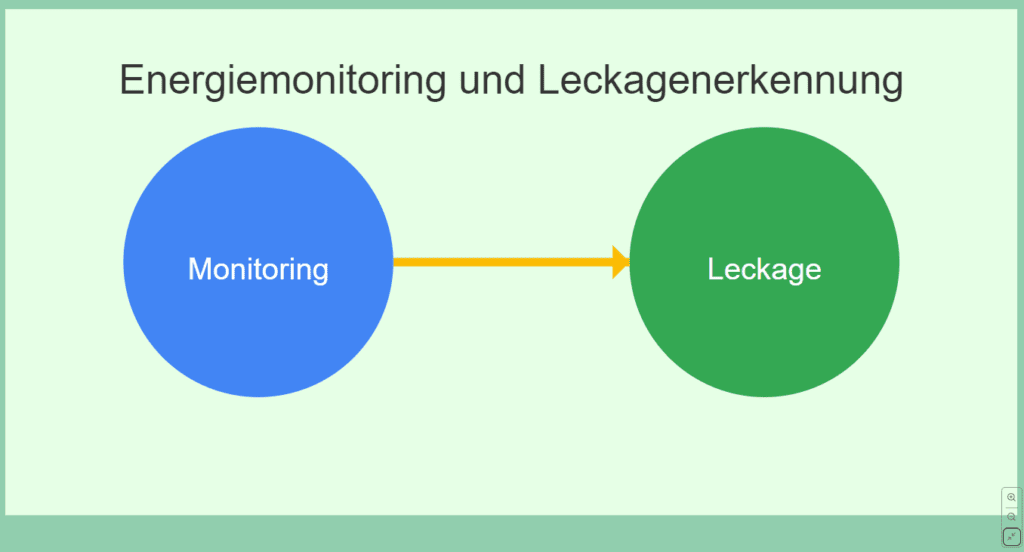
4.1 Bedeutung für die Kostenoptimierung
Das Energiemonitoring und die damit verbundene Leckagenerkennung spielen eine zentrale Rolle in der Kostenoptimierung von Druckluftsystemen. Die Bedeutung dieses Aspekts lässt sich anhand mehrerer Faktoren verdeutlichen:
- Kostenreduktion: Durch die frühzeitige Erkennung und Behebung von Leckagen können erhebliche Energieeinsparungen erzielt werden. Da Leckagen einen kontinuierlichen und oft unsichtbaren Energieverlust darstellen, können sie über die Zeit zu erheblichen Mehrkosten führen. Ein effektives Energiemonitoring ermöglicht es, diese Verluste zu minimieren und somit die Betriebskosten des Druckluftsystems signifikant zu reduzieren(Dawel & Pehlken, 2023).
- Effizienzsteigerung: Ein umfassendes Energiemonitoring liefert wertvolle Daten über den tatsächlichen Energieverbrauch und die Leistungseffizienz des Druckluftsystems. Diese Informationen können genutzt werden, um die Systemeinstellungen zu optimieren, die Auslastung der Kompressoren zu verbessern und unnötige Leerlaufzeiten zu reduzieren. Dadurch wird nicht nur Energie eingespart, sondern auch die Gesamteffizienz des Systems erhöht.
- Präventive Wartung: Durch die kontinuierliche Überwachung des Energieverbrauchs und der Systemleistung können Anomalien frühzeitig erkannt werden. Dies ermöglicht eine präventive Wartung, bei der potenzielle Probleme identifiziert und behoben werden können, bevor sie zu größeren Ausfällen oder Ineffizienzen führen. Dadurch werden nicht nur ungeplante Stillstandzeiten reduziert, sondern auch die Lebensdauer der Anlagen verlängert(Brand, 2023).
- Investitionsentscheidungen: Die durch das Energiemonitoring gewonnenen Daten bilden eine solide Grundlage für fundierte Investitionsentscheidungen. Sie ermöglichen eine genaue Kosten-Nutzen-Analyse für potenzielle Upgrades oder Erneuerungen des Druckluftsystems und helfen bei der Priorisierung von Verbesserungsmaßnahmen.
- Compliance und Nachhaltigkeit: In Zeiten zunehmender regulatorischer Anforderungen an die Energieeffizienz und den CO2-Ausstoß von Industrieanlagen liefert ein umfassendes Energiemonitoring die notwendigen Daten, um Compliance nachzuweisen und Nachhaltigkeitsziele zu erreichen. Dies kann nicht nur zur Kostenoptimierung beitragen, sondern auch das Image des Unternehmens verbessern und möglicherweise Zugang zu Fördermitteln oder Steuervergünstigungen eröffnen(“Pioniere Der Nachhaltigen Druckluft,” 2023).
4.2 Moderne Methoden zur Leckagenerkennung
Die Entwicklung moderner Technologien hat die Möglichkeiten zur Leckagenerkennung in Druckluftsystemen erheblich erweitert. Zwei besonders effektive Ansätze sind automatisierte Systeme und das Energiemonitoring des Druckluftkompressors:
Automatisierte Systeme: Moderne automatisierte Systeme zur Leckagenerkennung nutzen eine Kombination aus fortschrittlicher Sensorik, Datenanalyse und künstlicher Intelligenz, um Leckagen in Echtzeit zu identifizieren und zu lokalisieren. Diese Systeme bieten mehrere Vorteile:
- Kontinuierliche Überwachung: Im Gegensatz zu manuellen Inspektionen, die oft nur in größeren Zeitabständen durchgeführt werden, ermöglichen automatisierte Systeme eine ununterbrochene Überwachung des Druckluftsystems. Dies erhöht die Wahrscheinlichkeit, auch kleine oder intermittierende Leckagen frühzeitig zu erkennen(Dawel & Pehlken, 2023).
- Präzise Lokalisierung: Durch den Einsatz von Ultraschallsensoren oder anderen fortschrittlichen Detektionstechnologien können automatisierte Systeme Leckagen nicht nur erkennen, sondern auch genau lokalisieren. Dies erleichtert die schnelle und gezielte Reparatur.
- Quantifizierung der Verluste: Moderne Systeme sind in der Lage, die Größe der Leckagen zu quantifizieren und den damit verbundenen Energieverlust zu berechnen. Diese Information ist entscheidend für die Priorisierung von Reparaturmaßnahmen und die Berechnung des Return on Investment für Verbesserungsmaßnahmen.
Die Optimierung von Druckluftsystemen bietet ein erhebliches Potenzial zur Kostenreduzierung in industriellen Anlagen. Durch die Implementierung gezielter Maßnahmen können Unternehmen nicht nur ihre Energieeffizienz steigern, sondern auch ihre Betriebskosten signifikant senken. Im Folgenden werden vier Hauptbereiche für Kostenreduzierungsmaßnahmen detailliert erläutert.
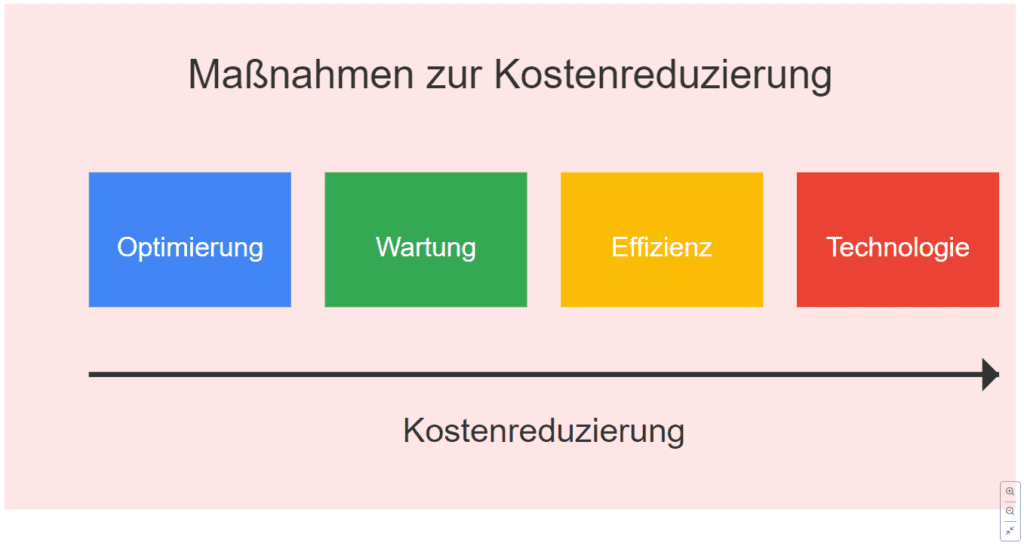
5.1 Optimierung der Kompressorleistung
Die Optimierung der Kompressorleistung ist ein zentraler Ansatzpunkt für Energieeinsparungen in Druckluftsystemen. Folgende Aspekte sollten dabei berücksichtigt werden:
a) Anpassung des Betriebsdrucks: Eine Reduzierung des Systemdrucks kann zu erheblichen Energieeinsparungen führen. Studien zeigen, dass eine Druckreduzierung um 1 bar zu einer Energieeinsparung von etwa 6-10% führen kann (Kaya et al., 2002). Es ist daher ratsam, den tatsächlich benötigten Betriebsdruck für jede Anwendung genau zu ermitteln und den Systemdruck entsprechend anzupassen. Dies kann durch den Einsatz von Druckreglern an den Verbrauchsstellen oder durch eine zentrale Drucksteuerung erreicht werden.
b) Optimierung der Ansauglufttemperatur: Die Ansauglufttemperatur hat einen direkten Einfluss auf die Effizienz des Kompressors. Eine Reduzierung der Ansauglufttemperatur um 3°C kann zu einer Energieeinsparung von etwa 1% führen (Kaya et al., 2002). Es ist daher empfehlenswert, die Kompressoren in kühlen, gut belüfteten Räumen zu installieren oder die Ansaugluft von außen zuzuführen, insbesondere in Regionen mit kühlem Klima.
c) Einsatz von Frequenzumrichtern: Die Verwendung von Frequenzumrichtern ermöglicht eine bedarfsgerechte Anpassung der Kompressorleistung an den tatsächlichen Luftbedarf. Dies ist besonders effektiv bei Anlagen mit stark schwankendem Luftbedarf. Durch die Vermeidung von ineffizienten Teillastbetrieben und häufigen Start-Stopp-Zyklen können Energieeinsparungen von bis zu 30% erzielt werden (Kanoğlu et al., 2008).
d) Kaskadenschaltung und Lastmanagement: Bei Systemen mit mehreren Kompressoren kann eine intelligente Kaskadenschaltung zur Optimierung der Gesamteffizienz beitragen. Hierbei werden die Kompressoren je nach Luftbedarf gestaffelt zugeschaltet, wobei die effizientesten Maschinen bevorzugt betrieben werden. Ein ausgeklügeltes Lastmanagement stellt sicher, dass die Kompressoren im optimalen Betriebsbereich arbeiten und unnötige Leerlaufzeiten vermieden werden.
5.2 Regelmäßige Wartung und Leckagebeseitigung
Die regelmäßige Wartung und insbesondere die konsequente Beseitigung von Leckagen sind entscheidend für die Effizienz und Kostenoptimierung von Druckluftsystemen:
a) Systematische Leckageortung: Leckagen können bis zu 30% des gesamten Druckluftverbrauchs ausmachen (Hernandez-Herrera et al., 2020). Eine systematische Leckageortung sollte daher in regelmäßigen Abständen durchgeführt werden. Moderne Methoden wie Ultraschalldetektoren oder thermografische Kameras ermöglichen eine präzise und effiziente Lokalisierung von Leckagen, auch in schwer zugänglichen Bereichen.
b) Quantifizierung und Priorisierung von Leckagen: Nach der Ortung sollten Leckagen quantifiziert werden, um ihre wirtschaftliche Relevanz zu bestimmen. Dies ermöglicht eine Priorisierung der Reparaturmaßnahmen. Große Leckagen sollten umgehend behoben werden, während kleinere Leckagen im Rahmen der regulären Wartung adressiert werden können.
c) Implementierung eines Leckage-Managementsystems: Ein strukturiertes Leckage-Managementsystem sollte etabliert werden, das regelmäßige Inspektionen, Dokumentation der gefundenen Leckagen, Reparaturmaßnahmen und Nachkontrollen umfasst. Dies gewährleistet eine kontinuierliche Verbesserung der Systemeffizienz.
d) Schulung des Personals: Mitarbeiter sollten geschult werden, um Leckagen frühzeitig zu erkennen und zu melden. Dies fördert ein Bewusstsein für die Bedeutung der Drucklufteffizenz im gesamten Unternehmen.
e) Regelmäßige Wartung von Komponenten: Neben der Leckagebeseitigung ist die regelmäßige Wartung aller Systemkomponenten wie Filter, Trockner und Ventile entscheidend. Verstopfte Filter oder defekte Ventile können zu erhöhtem Druckverlust und damit zu einem höheren Energieverbrauch führen.
5.3 Einsatz energieeffizienter Technologien
Die Integration moderner, energieeffizienter Technologien kann zu signifikanten Kosteneinsparungen führen:
a) Hocheffiziente Motoren: Der Einsatz von IE3- oder IE4-Motoren in Kompressoren kann den Energieverbrauch im Vergleich zu Standardmotoren um 2-8% reduzieren (Kanoğlu et al., 2008). Obwohl die Anschaffungskosten höher sind, amortisieren sich diese Investitionen oft innerhalb weniger Jahre durch die erzielten Energieeinsparungen.
b) Wärmerückgewinnung: Bis zu 94% der elektrischen Energie, die ein Kompressor verbraucht, wird in Wärme umgewandelt (Kaya et al., 2002). Diese Abwärme kann für Heizzwecke oder Prozesswärme genutzt werden, was zu erheblichen Kosteneinsparungen führen kann. Mögliche Anwendungen umfassen die Raumheizung, Warmwasserbereitung oder die Vorwärmung von Prozessluft.
c) Innovative Trocknungstechnologien: Der Einsatz moderner Trocknungstechnologien wie zyklische Adsorptionstrockner oder Membrantrockner kann den Energieverbrauch für die Lufttrocknung erheblich reduzieren. Diese Systeme passen ihre Leistung dem tatsächlichen Bedarf an und vermeiden so unnötige Energieverluste.
d) Intelligente Steuerungssysteme: Moderne Steuerungssysteme ermöglichen eine präzise Anpassung der Druckluftproduktion an den tatsächlichen Bedarf. Sie können mehrere Kompressoren koordinieren, Druckschwankungen ausgleichen und den Gesamtenergieverbrauch optimieren. Einige Systeme bieten auch prädiktive Wartungsfunktionen, die potenzielle Probleme frühzeitig erkennen und so ungeplante Ausfälle vermeiden.
Die wirtschaftliche Betrachtung von Effizienzmaßnahmen in Druckluftsystemen ist ein entscheidender Faktor für Unternehmen, um fundierte Entscheidungen über Investitionen in die Optimierung ihrer Anlagen zu treffen. In diesem Abschnitt werden wir uns eingehend mit der Kosten-Nutzen-Analyse verschiedener Effizienzmaßnahmen sowie den typischen Amortisationszeiten von Investitionen in effiziente Druckluftsysteme befassen.
6.1 Kosten-Nutzen-Analyse von Effizienzmaßnahmen
Die Kosten-Nutzen-Analyse ist ein wesentliches Instrument zur Bewertung der wirtschaftlichen Sinnhaftigkeit von Effizienzmaßnahmen in Druckluftsystemen. Sie ermöglicht es Unternehmen, die potenziellen Einsparungen gegen die erforderlichen Investitionen abzuwägen und somit die rentabelsten Maßnahmen zu identifizieren.
a) Energieeinsparungspotenzial: Das Energieeinsparungspotenzial von Effizienzmaßnahmen in Druckluftsystemen ist beträchtlich. Studien zeigen, dass durch die Implementierung verschiedener Maßnahmen Energieeinsparungen zwischen 20% und 60% erzielt werden können (Hernandez-Herrera et al., 2020). Diese Einsparungen führen direkt zu einer Reduzierung der Betriebskosten und tragen somit zur Verbesserung der Wettbewerbsfähigkeit des Unternehmens bei.
b) Investitionskosten: Die Investitionskosten für Effizienzmaßnahmen können je nach Art und Umfang der Maßnahme stark variieren. Einfache Maßnahmen wie die Optimierung des Betriebsdrucks oder die regelmäßige Wartung und Leckagebeseitigung erfordern oft nur geringe Investitionen, während umfangreichere Maßnahmen wie die Installation neuer, effizienter Kompressoren oder die Implementierung von Wärmerückgewinnungssystemen höhere Anfangsinvestitionen benötigen.
c) Betriebskosteneinsparungen: Die Betriebskosteneinsparungen, die durch Effizienzmaßnahmen erzielt werden, setzen sich aus mehreren Komponenten zusammen:
- Reduzierte Energiekosten: Dies ist oft der größte Einsparungsfaktor, da Druckluftsysteme einen erheblichen Anteil am Gesamtenergieverbrauch eines Unternehmens haben können.
- Verringerte Wartungs- und Reparaturkosten: Effizientere Systeme benötigen oft weniger Wartung und sind weniger anfällig für Ausfälle.
- Verlängerte Lebensdauer der Anlagen: Durch optimierte Betriebsbedingungen kann die Lebensdauer der Komponenten verlängert werden, was langfristig zu Kosteneinsparungen führt.
d) Beispielrechnung: Betrachten wir ein mittelständisches Unternehmen mit einem jährlichen Energieverbrauch von 1.000.000 kWh für das Druckluftsystem und Energiekosten von 0,15 €/kWh. Die jährlichen Energiekosten betragen somit 150.000 €. Eine Effizienzsteigerung von 30% durch verschiedene Maßnahmen würde zu einer jährlichen Einsparung von 45.000 € führen. Bei Investitionskosten von beispielsweise 60.000 € für die Umsetzung der Maßnahmen ergibt sich eine einfache Amortisationszeit von etwa 1,3 Jahren.
e) Nicht-monetäre Vorteile: Neben den direkten finanziellen Einsparungen sollten auch nicht-monetäre Vorteile in die Kosten-Nutzen-Analyse einbezogen werden:
- Verbesserte Produktqualität durch stabilere Druckluftversorgung
- Erhöhte Produktionszuverlässigkeit und reduzierte Ausfallzeiten
- Beitrag zum Umweltschutz durch reduzierte CO2-Emissionen
- Verbessertes Unternehmensimage als umweltbewusstes und effizientes Unternehmen
6.2 Amortisationszeiten von Investitionen in effiziente Systeme
Die Amortisationszeit ist ein wichtiger Indikator für die Wirtschaftlichkeit von Investitionen in Effizienzmaßnahmen. Sie gibt an, nach welcher Zeit sich die Investition durch die erzielten Einsparungen refinanziert hat.
a) Typische Amortisationszeiten: Für Effizienzmaßnahmen in Druckluftsystemen werden in der Literatur häufig Amortisationszeiten von weniger als zwei Jahren genannt (Castellanos et al., 2019; Herrera et al., 2021). Dies macht solche Investitionen besonders attraktiv, da sie relativ schnell zu positiven finanziellen Auswirkungen führen. Die genauen Amortisationszeiten können jedoch je nach spezifischer Maßnahme und Unternehmenssituation variieren:
- Leckagebeseitigung: Oft sehr kurze Amortisationszeiten von wenigen Monaten bis zu einem Jahr, da die Investitionskosten gering sind und die Einsparungen sofort wirksam werden.
- Druckoptimierung: Ebenfalls kurze Amortisationszeiten von meist unter einem Jahr, da auch hier die Investitionskosten gering sind.
- Installation von Frequenzumrichtern: Typischerweise 1-3 Jahre, abhängig von der Größe des Systems und den Betriebsbedingungen.
- Wärmerückgewinnung: Je nach Umfang und Nutzungsmöglichkeiten der Abwärme 1-4 Jahre.
- Austausch alter Kompressoren durch hocheffiziente Modelle: 2-5 Jahre, abhängig von der Größe und Auslastung des Systems.
b) Einflussfaktoren auf die Amortisationszeit: Verschiedene Faktoren beeinflussen die Amortisationszeit von Effizienzmaßnahmen:
- Energiepreise: Höhere Energiepreise führen zu kürzeren Amortisationszeiten, da die Einsparungen größer ausfallen.
- Betriebsstunden: Systeme mit hoher Auslastung und vielen Betriebsstunden amortisieren sich in der Regel schneller.
- Ausgangszustand des Systems: Je ineffizienter das bestehende System, desto größer ist das Einsparpotenzial und desto kürzer die Amortisationszeit.
- Unternehmensgröße und -struktur: Größere Unternehmen können oft von Skaleneffekten profitieren, was zu kürzeren Amortisationszeiten führen kann.
c) Berücksichtigung von Fördermöglichkeiten: Bei der Berechnung der Amortisationszeiten sollten auch mögliche Fördermittel berücksichtigt werden. Viele Länder und Regionen bieten Förderprogramme für Energieeffizienzmaßnahmen an, die die Investitionskosten reduzieren und somit die Amortisationszeiten verkürzen können.
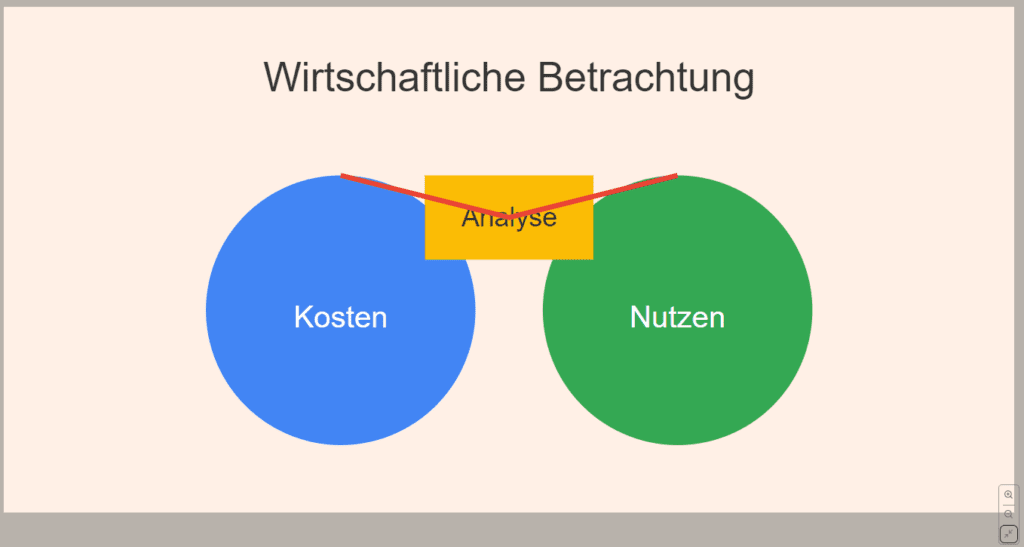
Q: Was kostet 1m³ Druckluft?
A: Die Kosten für 1m³ Druckluft können stark variieren, abhängig von vielen Faktoren wie dem Druck (z.B. 6 bar), den Stromkosten und der Effizienz des Druckluftsystems. Durchschnittlich liegen die Kosten bei etwa 2 bis 4 cent pro m³ Druckluft.
Q: Wie kann ich die Kosten der Druckluft berechnen?
A: Um die Kosten der Druckluft zu berechnen, sollten Sie den Stromverbrauch des Gebläses, die Betriebsstunden pro Jahr und den Strompreis einbeziehen. Eine detaillierte Berechnung enthält auch Faktoren wie Leckagen und die Effizienz der Druckluftanlage.
Q: Welche Faktoren beeinflussen die Kosten der Druckluft?
A: Zu den wichtigsten Faktoren gehören die Effizienz des Druckluftsystems, die Stromkosten, die Höhe des Drucks (z.B. 7 bar), eventuelle Leckagen und die betriebliche Nutzung der Druckluft.
Q: Wie kann ich Energie und Kosten sparen bei der Druckluftproduktion?
A: Sie können Energie und Kosten sparen, indem Sie regelmäßige Leckage-Messungen durchführen, effiziente Gebläse und Kompressoren nutzen und die Betriebsbedingungen optimieren. In vielen Fällen sind auch Investitionen in modernere Druckluftanlagen sinnvoll.
Q: Was sind typische Leckagen in einem Druckluftsystem?
A: Typische Leckagen treten oft bei Verbindungen, Ventilen und Schläuchen auf. Selbst kleine Lecks können über ein Jahr hinweg zu erheblichen Kosten und Energieverlusten führen.
Q: Wie häufig sollten Leckage-Messungen durchgeführt werden?
A: Leckage-Messungen sollten mindestens einmal jährlich durchgeführt werden. In stark genutzten Anlagen könnte eine häufigere Überprüfung sinnvoll sein, um unnötige Kosten zu vermeiden.
Q: Kann ich die Kosten der Druckluft auch ohne professionelle Hilfe reduzieren?
A: Ja, in vielen Fällen können Sie selbst durch regelmäßige Überprüfung auf Leckagen, Optimierung des Drucks und effiziente Nutzung der Druckluft Kosten reduzieren. Es ist jedoch oft hilfreich, spezialisierte Unternehmen wie eine GmbH zu konsultieren, um umfassende Lösungen zu finden.
Q: Welche Rolle spielt der Druck (z.B. 6 bar, 7 bar) bei den Kosten?
A: Der Druck der Druckluft hat einen direkten Einfluss auf die Kosten. Ein höherer Druck erfordert mehr Energie, was zu höheren Stromkosten führt. Daher sollte der Druck so niedrig wie möglich gehalten werden, während die Anforderungen der Anwendungen erfüllt werden.
Q: Wie kann ich weitere Informationen über die Druckluftkosten erhalten?
A: Weitere Informationen finden Sie häufig in Fachartikeln, auf den Webseiten spezialisierter Unternehmen oder durch das Abonnieren von Newsletters. Diese Quellen bieten zudem oft Tipps, wie Sie Kosten und Energie sparen können.
Q: Was kostet 1m3 Druckluft?
A: Der Preis für 1m3 komprimierte Druckluft kann variieren, je nach Faktoren wie Energieverbrauch (kW), Effizienz des Druckluftsystems und mögliche Leckagen. Typischerweise kann es zwischen 0,02 € und 0,05 € pro m3 kosten.
Q: Wie kann ich Leckagen in meinem Druckluftsystem feststellen?
A: Leckagen lassen sich durch eine gründliche Messung und Inspektion des Druckluftsystems feststellen. Es gibt spezialisierte Geräte zur Leckageortung und erfahrene Techniker beraten sie gerne dabei.
Q: Wie hoch sind die jährlichen Kosten für Druckluft?
A: Die jährlichen Kosten für Druckluft können stark variieren und hängen von der Kapazität und Nutzung des Druckluftsystems ab. Im Durchschnitt kann es mehrere Tausend Euro pro Jahr kosten, je nach der Menge der genutzten m3 Druckluft und der Effizienz des Systems.
Q: Kann ich durch regelmäßige Wartung Kosten sparen?
A: Ja, regelmäßige Wartung kann helfen, die Effizienz des Druckluftsystems zu erhalten und Leckagen zu vermeiden, was letztendlich die Kosten senken kann.
Q: Was sind die Vorteile der Nutzung von Druckluft in pneumatischen Systemen?
A: Druckluft in pneumatischen Systemen bietet viele Vorteile wie Sauberkeit, Sicherheit und einfache Mechanismen zur Energieübertragung in verschiedenen Anwendungsbereichen.
Q: Wie kann ich den Energieverbrauch meines Gebläses überwachen?
A: Der Energieverbrauch kann durch die Installation entsprechender Messgeräte überwacht werden, die den kW-Verbrauch aufzeichnen. Diese Daten ermöglichen es, die Effizienz zu analysieren und Optimierungen vorzunehmen.
Q: Ist nasse Druckluft von Nachteil für mein System?
A: Ja, nasse Druckluft kann Korrosion und Verschleiß an Druckluftbehältern und anderen Komponenten verursachen. Es ist wichtig, Trockner und Filter zu verwenden, um solche Probleme zu vermeiden.
Q: Wie kann ich die Kosten für 1m3 Druckluft errechnen?
A: Um die Kosten für 1m3 Druckluft exakt zu errechnen, sollten Sie den Energieverbrauch (kW), die Betriebsstunden und mögliche Leckagen in Ihrem System berücksichtigen. Ein detailliertes Formular kann helfen, die genauen Kosten zu ermitteln.
Q: Wie kann ich mich über Neuigkeiten zum Thema Druckluft informieren?
A: Sie können sich für spezialisierte Newsletter anmelden, die Sie regelmäßig über Neuigkeiten und Tipps zum Thema Druckluft informieren. Sie können diese Newsletter jederzeit über den Abmeldelink kündigen.
Der Artikel hebt zu Recht die Bedeutung der Energiekosten für die Gesamtkosten der Drucklufterzeugung hervor. Als Nachhaltigkeitsbeauftragter in einem Chemieunternehmen möchte ich den Aspekt der CO2-Bilanz ergänzen. Die Optimierung von Druckluftsystemen kann einen erheblichen Beitrag zur Reduzierung der Treibhausgasemissionen eines Unternehmens leisten. In unserem Fall konnten wir durch verschiedene Effizienzmaßnahmen im Druckluftbereich unsere jährlichen CO2-Emissionen um über 500 Tonnen senken. Es wäre interessant gewesen, im Artikel noch mehr über die Verbindung zwischen Druckluftoptimierung und Nachhaltigkeitszielen zu lesen.
Die wirtschaftliche Betrachtung von Effizienzmaßnahmen ist sehr aufschlussreich. Als Controller in einem produzierenden Unternehmen schätze ich besonders die Ausführungen zu den Amortisationszeiten verschiedener Maßnahmen. Ein Aspekt, den ich gerne noch vertiefen würde, ist die Berücksichtigung von Förderprogrammen und steuerlichen Anreizen bei der Investitionsentscheidung. In unserem Unternehmen konnten wir durch die geschickte Nutzung von Fördermitteln die Amortisationszeit für ein umfangreiches Druckluftoptimierungsprojekt von ursprünglich 3 Jahren auf 1,5 Jahre reduzieren. Es wäre hilfreich gewesen, im Artikel noch mehr Informationen über aktuelle Fördermöglichkeiten und deren Einfluss auf die Wirtschaftlichkeitsberechnung zu finden.
Der Artikel bietet einen umfassenden Überblick über die Kostenstruktur von Druckluftsystemen und zeigt deutlich, wie komplex die Berechnung der tatsächlichen Kosten pro Kubikmeter Druckluft ist. Als Energiemanager in einem mittelständischen Unternehmen finde ich besonders den Aspekt der versteckten Kosten durch Leckagen interessant. In unserem Betrieb haben wir kürzlich ein Leckage-Management-Programm implementiert und konnten dadurch unsere Druckluftkosten um etwa 15% senken. Es wäre spannend gewesen, im Artikel noch mehr über Best Practices im Leckage-Management zu erfahren.
Die detaillierte Aufschlüsselung der Kostenfaktoren ist sehr informativ. Als Ingenieur in der Automobilindustrie kann ich bestätigen, wie wichtig es ist, alle diese Aspekte bei der Planung und Optimierung von Druckluftsystemen zu berücksichtigen. Ein Punkt, den ich gerne ergänzen würde, ist die Bedeutung der richtigen Dimensionierung des Gesamtsystems. Wir haben festgestellt, dass eine genaue Analyse des tatsächlichen Druckluftbedarfs und eine entsprechende Anpassung der Kompressorleistung zu erheblichen Kosteneinsparungen führen kann. In unserem Fall konnten wir durch eine Neuauslegung des Systems den Energieverbrauch um 20% reduzieren.
Die Ausführungen zu den innovativen Ansätzen wie KI-gestützte Überwachungssysteme sind faszinierend. Als Forscher im Bereich der industriellen Automatisierung sehe ich großes Potenzial in der Integration von Druckluftsystemen in das Industrial Internet of Things (IIoT). Ein Aspekt, der meiner Meinung nach noch mehr Beachtung verdient, ist die Möglichkeit, durch Echtzeitdatenanalyse und maschinelles Lernen prädiktive Wartungsstrategien zu entwickeln. Dies könnte nicht nur die Effizienz steigern, sondern auch ungeplante Ausfallzeiten minimieren.